Is expensive manufacturing software the right fit for your business?
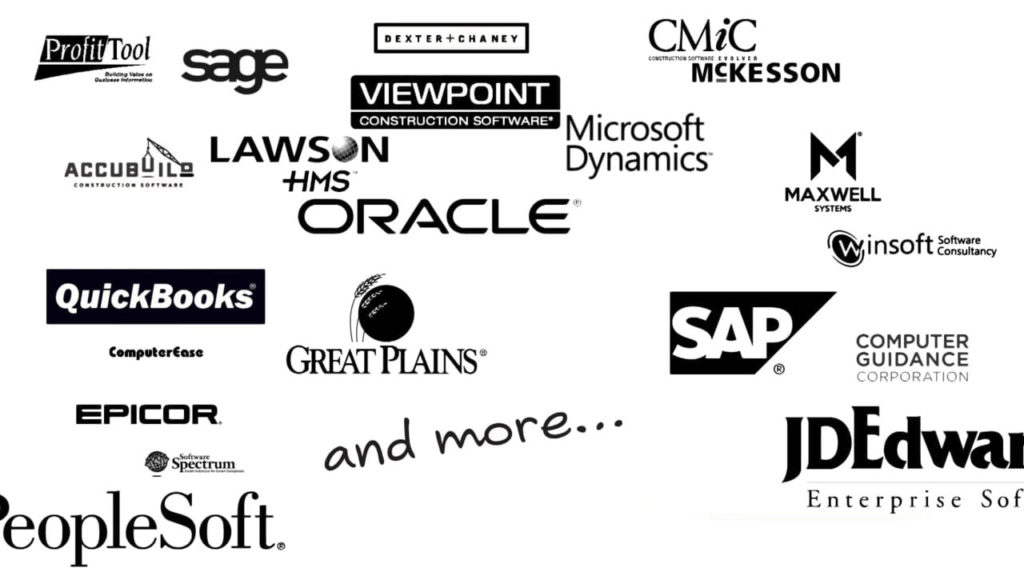
Manufacturing software is expensive, right?
Not necessarily.
There are affordable options out there. In fact, price depends highly on the scale of your operations and the demands of your particular business.
The good news is that there are more than 200 different manufacturing software platforms available today. The bad news is that if you’re a small to medium-sized enterprise (SME), your choices are limited. Most of the 200+ software products are designed for large-scale operations, i.e., those with more than 200 employees.
There are many factors to take into consideration when choosing the right manufacturing software for your business. The last thing you want to do is make a hasty decision that leads to a costly mistake.
This article will help you to identify exactly what you need from a software package, the pros and cons of different types of software, and some advice on picking the ideal solution for you.
What do you want from your manufacturing software?
The answer to this question depends mainly on the size of your business. In general, large companies have very different business needs to smaller ones. Let’s take a brief look at a comparison between the two, before expanding on some of the points.
Large Businesses – Manufacturing Software Priorities | Small to Medium Businesses – Manufacturing Software Priorities |
---|---|
Manage large finance accounts – track purchases, outgoings, income, etc. | Manage small finance accounts – track purchases, outgoings, income, etc. |
Manage high staff numbers: 200+ | Manage small staff numbers: <200 |
Manage supply chain and improve reliability | Manage supply chain and improve reliability |
Plan and manage large amount of materials | Balance materials and inventory |
Control varied and large inventory | Schedule deliveries |
Schedule complex processes | Maintain agile working practices |
Schedule high amount of deliveries | Focus on growth |
Manage big data | Manage small, yet expanding amounts of data |
Invest in hi-tech solutions | Improve customer experience |
As you can see, there is some crossover between the priorities of large and small manufacturing businesses, but there are also some key differences. Apart from the obvious differences in scale, there are one or two aspects that deserve closer inspection.
Agile working practices & managing data for small businesses
In today’s manufacturing industry, the ability to change and adapt quickly is paramount to survival and growth, especially for small businesses. Agility refers to working practices that facilitate flexibility and adaptable workflows. This can range from gaining insights from data to inform decisions, to automated manufacturing processes such as Computer-Assisted Manufacturing (CAM) or additive manufacturing.
Managing data can be a big issue for small businesses, especially if they experience sudden growth and are unprepared.
Managing the supply chain and keeping inventory lean is crucial for small businesses. Without MRP software, keeping inventory low while continuing to fulfill orders can be a very delicate balancing act.
Many small manufacturing firms are finding that the best way to stay agile and integrate workflows is to invest in management software that helps to control materials, inventory, manufacturing processes, labour and finances. But the cost of traditional network-based platforms are often prohibitive.
In recent years, cloud-based Materials Requirement Planning or Manufacturing Resource Planning (MRP) software has made it more affordable for smaller companies. We’ll discuss the benefits of cloud-based systems in a moment.
Managing big data & investing in hi-tech solutions for large businesses
The priorities of a large manufacturing firm are very different from those of a smaller one. For starters, they’re not too concerned with staying agile as they are too big to change anything in a hurry and it isn’t as crucial for their survival or growth.
Their main concerns are managing their large finances, inventory, and keeping their existing customers happy. Secondary concerns are managing big data and investing in technology. Sophisticated LAN-based MRP systems are the order of the day for managing large amounts of data as they require high amounts of processing power.
Big companies are also far more likely to invest in expensive technology such as CAM systems and robotics to speed up production and streamline their operations. Many big companies operate highly complex systems with numerous interactions. Therefore, they are more likely to want hands-on support whenever they need it, and network-based MRP packages often provide a consulting service. When you consider the cost of training for employees to get to grips with the software, it’s easy to see why traditional, network-based MRP packages are expensive compared to cloud-based ones.
Is your company too small for manufacturing software?
This is a question that gets asked quite often. People see the price of traditional locally installed MRP licences and balk. Is it really necessary? Will it benefit our company THAT much?
These are the wrong questions. If you’re a small manufacturing company, what you should be asking is: ‘Is there a less expensive, more agile and less time-consuming alternative that will help us to streamline operations and promote growth?’
The answer is yes.
Cloud-based MRP systems (or Software as a Service (SaaS) systems) are leaner, more agile and still provide a whole host of benefits for small to medium-sized businesses. Rather than paying a huge amount up-front for multiple licenses, cloud MRP systems are usually paid for by subscription. Costs are kept down as there is no need for complex installations on your system, therefore reducing tech support. In addition, training is often provided online as part of the package, and updating the software is taken care of remotely.
And the good news is, just because they are less expensive doesn’t mean they are any less powerful. They may be slightly pared-down in terms of capacity compared to the software big companies use, but smaller firms aren’t worried about that.
Cloud-based MRP software will typically allow you to produce accurate plans and reports, review inventory in real-time, schedule precise and on-time deliveries and manage all of your data centrally. You can integrate your entire workflow – planning, production, stock, sales, team management, supply chains and data analysis.
There are practical advantages as well, such as being able to easily log-in to the system from mobile apps, which improves collaboration and on-site mobility for engineers and managers.
MRP Manufacturing software – the key to success
Staying agile and able to change is the key to success for small manufacturing businesses, whereas maintaining growth is important for bigger companies.
That’s why MRP software is a ‘must-have’ these days. For small businesses, cloud-based MRP software has the edge over it’s more expensive and clunky competitors.