Inventory Shrinkage – Causes, Consequences, and Tips
Inventory shrinkage is a common issue in most businesses that deal with physical inventory. The consequences of shrinkage may include financial losses, operational disruptions, and loss of competitiveness. But how does it happen and how to prevent it?
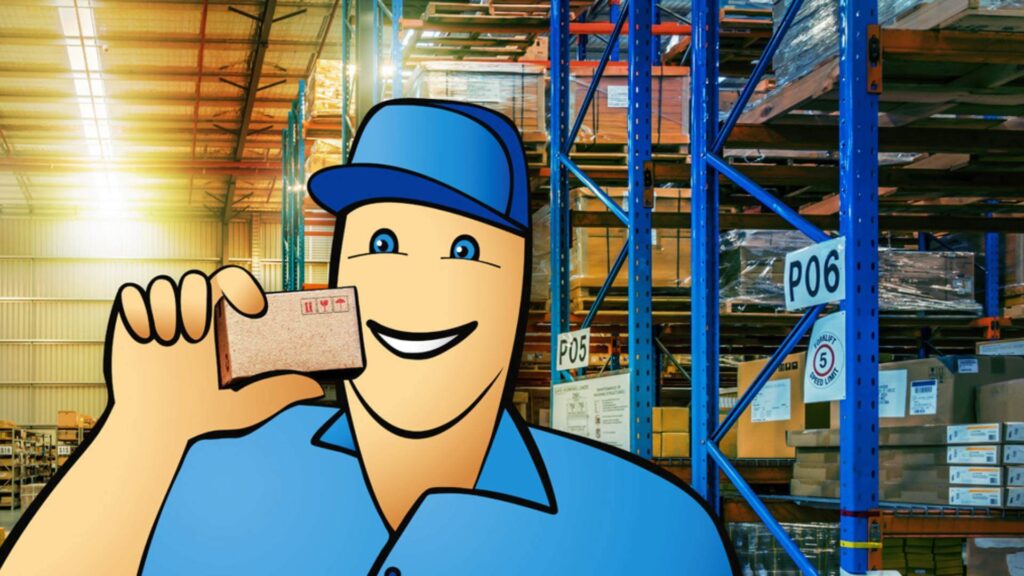
You can also listen to this article:
What is inventory shrinkage?
Inventory shrinkage occurs when the actual quantities in your inventory are smaller than what is recorded in your books or inventory management system. This usually happens due to a combination of factors, including administrative errors, damage, spoilage, theft, and supplier fraud.
According to a Statista report, more than 64% of US retail businesses experienced a yearly shrinkage rate of more than 1% of their total inventory value. And no type of business that deals with physical inventory is immune to shrinkage.
Conducting stocktakes and comparing the results to your inventory records is the most reliable method of discovering inventory loss as this provides concrete evidence of discrepancies.
How to calculate inventory shrinkage?
To calculate the inventory shrinkage value, you can use the following formula:
Shrinkage Value = Inventory Value Record – Physical Inventory Value
Let’s say $80,000 is marked as the company’s inventory value in their accounting records. After an inventory count, the real physical inventory value was calculated to be $78,000. This means the shrinkage value was:
$80,000 – $78,000 = $2,000
Therefore, the company lost $2,000 worth of inventory during the period.
How to calculate the inventory shrinkage rate?
As inventory value can fluctuate, shrinkage value is not the most trustworthy metric for tracking shrinkage over time. To continuously measure shrinkage and use it as a KPI of your inventory management performance, start calculating the inventory shrinkage rate.
Inventory Shrinkage Rate = Shrinkage Value / Inventory Value Record x 100
Let’s continue with the previous example. The recorded inventory value was $80,000 and shrinkage was $2,000. The shrinkage rate, therefore, was:
$2,000 / $80,000 x 100 = 0.025 x 100 = 2.5%
This means that your shrinkage percentage or the inventory value lost through shrinkage was 2.5%. But how could that happen?
Causes of inventory shrinkage
Inventory shrinkage can be caused by many factors that usually work in combination with one another. Here are some of the most common causes of shrinkage:
- Damage. Damage to inventory items can occur during various stages of the supply chain, from handling in the warehouse to transportation. Physical damage often results in a reduction in the actual inventory levels compared to what is recorded in the accounting books.
- Spoilage. Perishable goods or products with expiration dates can suffer from spoilage. When these items go bad before being sold, it leads to a loss of inventory.
- Production errors. Mistakes in the production process may cause scrapped materials or defective products that need to be written off.
- Employee theft. Internal theft by employees is a significant contributor to inventory loss. When employees pilfer inventory items, it results in a direct loss. While the previous causes of shrinkage can be reported, with the items written off, theft is something that can only be discovered through inventory audits and investigations.
- Shoplifting. Shoplifting by external parties is an extremely common cause of shrinkage in retail environments. It occurs when customers steal products from the store.
- Vendor fraud. Vendor fraud occurs when suppliers manipulate orders or invoices, providing fewer items than what was agreed upon or charging higher prices. This leads to a discrepancy between the actual inventory and the recorded amount.
- Inventory miscounting. Errors in counting inventory during physical or cycle counts can lead to inaccuracies in recorded inventory levels. These human errors can result from miscounts, omissions, or double-counting of items.
- Administrative errors. Administrative errors in inventory accounting, such as data entry mistakes, can create discrepancies between actual inventory and recorded amounts. These are often unintentional human errors but can have serious consequences.
Each of these causes of inventory shrinkage represents a potential source of loss for a business. But is monetary loss its only consequence?
Consequences of inventory shrinkage
Inventory shrinkage can lead to a number of consequences. Here are some of the more serious ones:
- Financial loss. One of the most immediate and direct consequences of shrinkage is financial loss. It reduces the value of a company’s assets and directly impacts your bottom line because the cost of the lost inventory is subtracted from revenue without any corresponding benefit from sales.
- Stockouts. Shrinkage can lead to unexpected stockouts, where you run out of products to sell or materials to use in manufacturing.
- Overstocking. To compensate for shrinkage, some businesses may overstock inventory as a buffer, tying up capital that could be used elsewhere.
- Operational disruptions. Frequent stockouts and overstock situations disrupt normal operations, leading to inefficiencies and increased costs in supply chain management, production stoppages due to material shortages, and the inability to fulfill orders on time.
- Damage to reputation. Constant late or incomplete deliveries can lead to customer dissatisfaction and loss of business.
- Increased costs. Maintaining excess inventory as a safeguard against shrinkage-related stockouts increases holding costs while dealing with and analyzing inventory loss often requires additional labor hours.
- Loss of competitiveness. A company that consistently struggles with shrinkage may lose its competitive edge in pricing, availability, and customer service compared to more efficient competitors.
As we can see, inventory shrinkage is a serious issue that needs to be dealt with. Let’s take a look at what you can do to prevent it.
Tips for minimizing inventory shrinkage
Conduct regular inventory audits
Regular inventory audits involve physically counting and verifying the actual amount of inventory on hand against what is recorded in your records. These audits help identify discrepancies and shrinkage issues promptly, enabling you to take corrective actions. Implementing a schedule for these audits, such as monthly or quarterly, ensures that you stay on top of inventory accuracy.
Moreover, using cycle counting methods, where you continuously count a portion of your inventory over time, can provide a more real-time view of inventory levels and reduce the need for massive annual audits. By regularly auditing your inventory, you can uncover issues early, address root causes, and prevent shrinkage from escalating.
Train employees
Training should cover various aspects, including proper inventory handling to prevent damage, understanding production processes to avoid overproduction or errors, accurate data entry to maintain inventory records, and adherence to First Expired, First Out (FEFO) principles for perishable goods. Well-trained staff can drastically reduce human errors that contribute to inventory shrinkage.
Training programs should be ongoing, with regular refreshers, and should also include security awareness to prevent internal theft. Engaging employees in the importance of inventory accuracy and making them aware of how their actions impact the bottom line can be motivating factors in minimizing shrinkage.
Implement security measures
Implementing security measures is vital to prevent both internal and external theft. Internal theft, such as employee theft, can be deterred with security systems like surveillance cameras and access control measures. These not only act as deterrents but also provide evidence in case of suspicious activities.
For e-commerce and point of sale (POS) settings, secure payment processing and order verification processes also contribute to preventing inventory loss.
External theft, such as shoplifting, can be reduced with vigilant staff, proper store layout, and security personnel. It’s essential to regularly review and update security systems to stay ahead of potential threats and maintain a safe environment for your inventory.
Conduct vendor audits
Regular vendor audits are crucial to combat vendor fraud. These audits involve verifying that the products received match the purchase order, both in terms of quantity and quality. They also ensure that the agreed-upon pricing and terms are adhered to. Maintaining strong supplier relationships and transparent communication can help reduce the risk of fraud.
In addition, implementing vendor scorecards and KPIs can help you evaluate supplier performance regularly. If a supplier consistently fails to meet expectations, it may be time to reassess the relationship and explore alternative sources to protect your inventory from vendor-related shrinkage.
Use proper stocktaking procedures
Stocktaking procedures should include guidelines for conducting physical counts, reconciliation processes to address any discrepancies discovered during the count, and steps to handle damaged or spoiled inventory items. Double-checking counts and using barcode scanning systems can further improve accuracy and reduce human errors.
Establishing clear protocols for reporting and addressing discrepancies between physical counts and recorded inventory levels ensures that issues are promptly investigated and resolved. Developing standard operating procedures also plays a crucial role in training new employees and maintaining a consistent approach to inventory management throughout your organization.
Implement inventory management software
Inventory management software offers real-time tracking of inventory levels, automates inventory control tasks, and provides insights into inventory turnover. It streamlines the entire inventory management process, from creating purchase orders and receiving goods to tracking inventory movements and sales.
Barcode scanning capabilities make data entry more efficient and accurate, reducing the risk of errors that contribute to shrinkage. Inventory management software also offers detailed reporting and analytics, helping you identify trends and anomalies that may indicate potential shrinkage issues, allowing for proactive measures to be taken.
Overall, implementing such software increases efficiency, accuracy, and visibility in managing inventory, contributing to shrinkage prevention and minimization efforts.
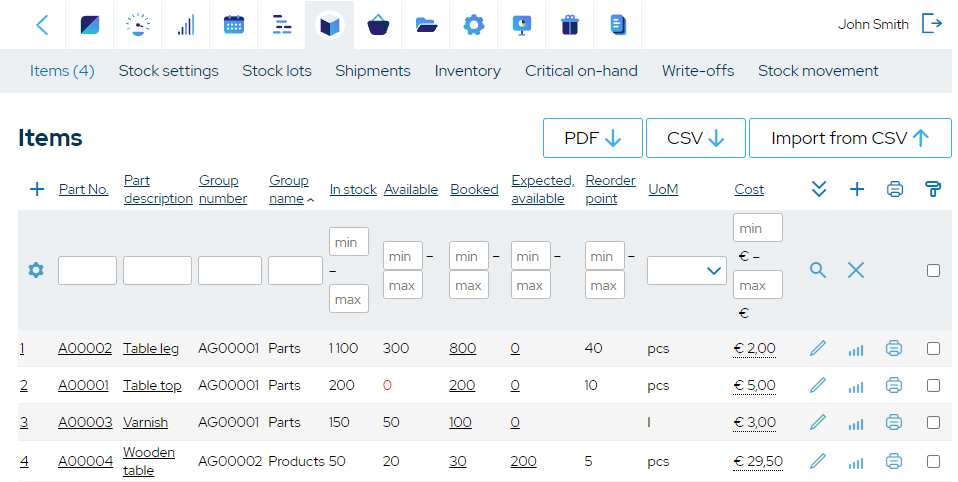
How to report inventory shrinkage in financial statements?
Inventory shrinkage is recorded in financial statements as an expense, typically under the category of Cost of Goods Sold (COGS) or as a separate line item, depending on the accounting method used. Here’s how shrinkage is recorded in financial statements:
- As a component of COGS. Under the accrual accounting method, when shrinkage occurs, it is recognized as a reduction in the value of inventory. This reduction is treated as an expense and is included in the COGS section of the income statement. It directly impacts the calculation of gross profit.
- Separate line item in expenses. In some cases, businesses may choose to report inventory loss as a separate line item in their income statement under operating expenses. This approach provides a clearer breakdown of expenses and allows for easier tracking and analysis of shrinkage over time. The income statement might include a line item like “Inventory Shrinkage Expense” or “Inventory Losses.”
- Specific accounting treatment. Shrinkage may be recorded using specific accounting treatments depending on the circumstances and accounting standards followed by the business. For example, if the loss results from a sudden and unexpected event, it may be treated differently than routine shrinkage. Businesses should adhere to generally accepted accounting principles (GAAP) or other relevant accounting standards in their region when recording inventory shrinkage.
It’s important to note that the method used to record inventory shrinkage in financial statements can vary between businesses and industries. The chosen method should align with accounting standards and accurately reflect the impact of shrinkage on the company’s financial performance. Additionally, maintaining accurate records and documentation of loss incidents is essential for transparency and compliance with accounting regulations.
Key takeaways
- Inventory shrinkage occurs when the actual quantities in your inventory are smaller than what is recorded in your books or inventory management system.
- Inventory shrinkage can result from various factors, including damage, spoilage, production errors, employee theft, shoplifting, vendor fraud, inventory miscounting, and administrative errors.
- Inventory shrinkage can lead to several significant consequences, including financial loss, stockouts, overstocking, operational disruptions, damage to reputation, increased costs, and loss of competitiveness.
- Inventory shrinkage can be prevented or minimized by conducting regular inventory audits, training employees, implementing security measures, conducting vendor audits, using proper stocktaking procedures, and implementing inventory management software.
Frequently asked questions
Inventory shrinkage occurs when the actual quantities in your inventory are smaller than what is recorded in your books or inventory management system.
Common events that could result in inventory shrinkage include damage, spoilage, production errors, employee theft, shoplifting, vendor fraud, inventory miscounting, and administrative errors.
Inventory shrinkage is typically reported as an expense in the financial statements, either within the “Cost of Goods Sold” (COGS) section or as a separate line item under operating expenses, depending on accounting practices.
Inventory shrinkage can be calculated using the formula: Shrinkage Value = Inventory Value Record – Physical Inventory Value. To track shrinkage over time, you can calculate the Inventory Shrinkage Rate using the formula: Inventory Shrinkage Rate = (Shrinkage Value / Inventory Value Record) x 100.
You may also like: Materials Management – Definition, Benefits, Best Practices