Inventory Planning – A Quick Guide
Inventory represents the very foundation of any manufacturing or distribution operation. Keeping the raw materials, WIP, and finished goods inventories at optimal levels is crucial for short- and long-term business success.
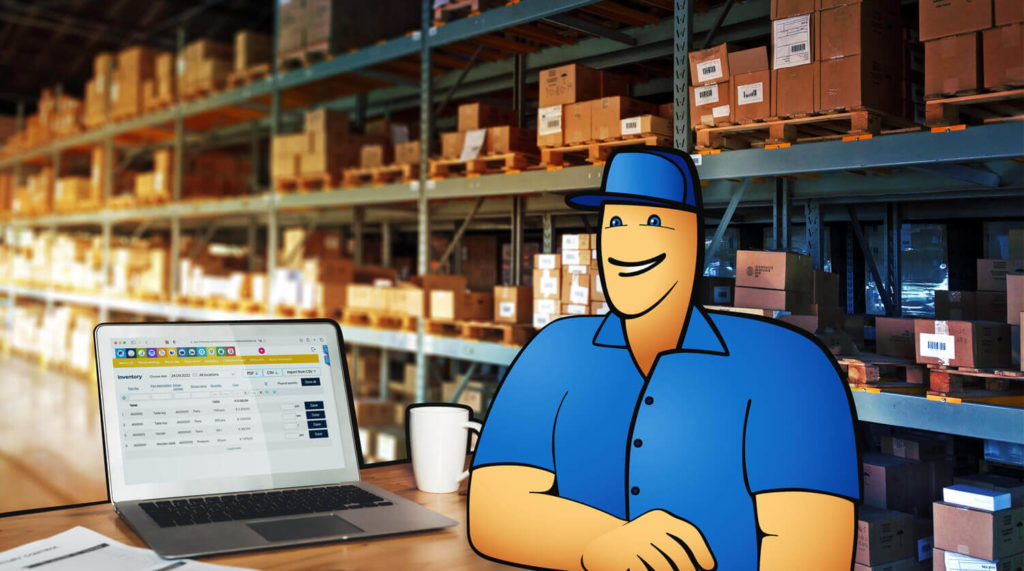
You can also listen to this article:
What is Inventory Planning?
Inventory planning is a set of practices designed to help businesses keep optimal stock levels at any given time. A subset of inventory management, inventory planning is interlinked with both capacity and procurement planning and mostly revolves around aligning procurements and supply chain movements with material demand in order to make sure that inventory is always at healthy levels. This is achieved through the use of various tools and processes such as demand forecasting, restocking methodologies like EOQ, automating reorder points, or adopting inventory management methods like Just-In-Time.
In manufacturing, inventory planning mainly deals with planning ahead and timely restocking of the raw material inventory. This ensures, in turn, that the work-in-process inventory (or WIP) – components that are being processed but are not yet finished – is kept at optimal levels and manufacturing workflows can progress smoothly. The outputs flowing into the finished goods inventory also need to be kept at the right levels as having both too little (stockouts) or too many (overstocking) goods in storage can incur opportunity loss and accrued costs.
Since inventory is directly associated with revenue, inventory planning also affects a company’s cash flow and hence, budgeting considerations. Most modern production and inventory management software solutions have a wide array of inventory planning tools built in.
Why is Inventory Planning important?
Systematic inventory planning is important for a number of reasons, chief among which are optimizing inventory levels and improving cash flow.
Optimizing inventory levels
A manufacturing or distribution company needs to have a steady flow of components and goods moving through it to ensure stable operation. Maintaining optimal inventory levels helps keep warehousing and other overhead costs in check and the shop floor humming at close to ideal capacity. It is also important for more accurate production planning and forecasts. As such, inventory planning attempts to avoid two extremes from occurring – stockouts and overstocking.
Stockouts are situations where the company runs out of raw materials or finished goods that it requires, usually abruptly. These mostly occur due to supply chain disruptions, sudden market fluctuations, or simple human error. The latter is especially common in smaller companies where small planning errors like a misplaced shipping slip or a rushed lead time statement can quickly turn into material deficits and outstanding orders. Stockouts can be dangerous, especially for SMEs, because production may well grind to a standstill, paralyzing the chief means of increasing liquidity. Planning ahead and taking appropriate measures like allocating a healthy amount of safety stock, for example, helps to avoid them.
Improving cashflow
Conversely, overstocking can also be detrimental to a manufacturing operation, especially for cash flow. Overstocking occurs when there is an excess of a type of inventory and is mostly caused by poor inventory management or irregularities in the supply chain. Here again, human error or bad planning is oftentimes the culprit. For example, in an attempt to foresee material deficits arising from inconsistent vendors or planning, 10% of extra raw material stock is ordered “just to be safe”.
Overstocking increases standing inventory overheads, congests warehouse space, and introduces concerns over expiration or security. Potentially even worse, overstocking ties up precious capital that could otherwise be used for re-investing into the company or making strategic purchases.
By keeping the inventory flowing, good inventory planning makes sure that the cash keeps flowing as well. This is, again, especially important for SMEs that usually rely on fast turnover and whose inventories regularly tie up more than 80% of their finances. What’s more, since overhead costs are kept in check by optimized inventory, good planning often translates into an improved bottom line.
Inventory Planning methods
Writ large, inventory management deals with all aspects of stock as it journeys through the company’s supply chain. These include the procurement, storage, utilization, and tracking of raw materials and components, as well as vendor management, stock reordering, and requirements forecasting. In inventory planning, all of these steps need to be taken into account in deliberating optimal stock levels.
For example, if a workstation has a material output that temporarily exceeds available warehouse space, optimal stock levels need to be based on available storage rather than manufacturing capacity to avoid bottlenecks. Traceability and warehouse management are also crucial for inventory planning as it is only possible to plan ahead if you have a good overview of what is in stock and where it is stored. A well-implemented barcode system can go a long way in making sure that stock and its movements are always counted for, for example.
Next, let us take a look at a few methods and processes that may prove most beneficial in ensuring proper inventory planning.
Demand forecasting
Forecasting is a cross-department process geared at making informed predictions about upcoming material demand based on market trends, historical sales data, vendor information, and other metrics. Applying to inventory, it is sometimes used interchangeably with the terms inventory estimation or inventory control. Demand forecasting is one of the main analytical processes that informs production capacities, purchases, and inventory requirements. Therefore, it acts as a crucial baseline for projecting inventory levels.
Most forecasting is conducted before the start of a manufacturing period, with continuous adjustments made throughout the year. At the end of the period, results are coordinated with shareholders, and performance data is consolidated. A number of KPIs, such as inventory turnover rate, tracking signals, fill rate, etc., assist in quantifying forecasts and improving accuracy.
Read more about Demand forecasting
Economic Order Quantity and Reorder Points
Economic Order Quantity (or EOQ) is an inventory management methodology used to calculate the optimal amount of stock to order. EOQ aims to strike a balance between satisfying demand and minimizing excess inventory and its holding and storage costs, making it an ideal inventory planning tool. EOQ is great for optimizing cash flow and keeping raw materials and indeed WIP inventory lot size at an optimal level. It’s one big limitation is that it only functions well if demand as well as holding and storage costs are relatively constant, as is often the case with make-to-stock manufacturers.
EOQ also constitutes one means to determine a company’s reorder point. A reorder point is a preset minimum inventory threshold that triggers stock replenishment. Reorder points are crucial inventory management functions that ensure stock can be replenished before production runs out of raw materials. Reorder points can be calculated using EOQ or as a function of lead time, demand, and safety stock. Most inventory management systems utilize automated reorder point functionality in conjunction with stock tracking.
Read more about Reorder Point
Just-In-Time
Just-In-Time (or JIT) is more of a manufacturing methodology rather than an inventory control mechanism. In JIT the whole manufacturing operation is arranged in a way in which demand is met and purchases are kept aligned with production schedules as precisely as possible. This helps to boost manufacturing efficiency and minimize different types of waste, including those arising from excess inventory.
Borrowing a lot from Lean manufacturing, JIT is most suitable for businesses utilizing a make-to-order or assemble-to-order workflow that have their manufacturing set up in a pull system. JIT may be challenging to set up as it requires rigorous control over the supply chain and steady vendor relationships. Once properly implemented, however, JIT can quickly pay off as it touts exceptional manufacturing efficiency.
Read more about Just-In-Time
4 Inventory Planning best practices
There is no single set of rules that can always ensure the right inventory management practices. An inventory planning method that works for one use case is by no means guaranteed to function universally. Every inventory management process is different and dependent on the type of manufacturing operation that a company has set up, as well as company culture, market considerations, and many other variables.
Nevertheless, there are best practices that anyone looking to perfect their inventory planning process should look into. Here are 4 inventory management recommendations to consider that can be helpful in setting up a good inventory planning process.
- Assign roles and train employees. Even the most intricate inventory management solution is unable to keep the inventory organized if it is poorly implemented or if employees are not properly trained to use it. Make sure that whatever systems are put in place, the workforce is brought up to speed on how to operate them. Clear guidelines should also be set up to determine roles and responsibilities for the various aspects of inventory management including procurement, warehouse management, vendor relationships, etc.
- Enhance inventory tracking efforts. A proper traceability software helps make sure that all relevant information on stock movements is logged and always available for analysis. Inventory tracking systems provide detailed info on all inventory items including procurement and expiration dates, routing histories, vendor details, value, etc. What’s more, a good traceability toolset should include barcoding, batch tracking, quality control, and even RMA functionalities. In essence, traceability is an absolute prerequisite for enhanced inventory control and should be on the shortlist of systems to implement for ensuring good inventory planning.
- Implement a continuous inventory system. Periodic inventory systems that rely on taking physical inventory counts before and after a financial period can still be a relevant means of stocktaking for some use cases and may prove a cost-effective solution for small companies, especially if they do not utilize large WIP inventory. Modern continuous (or perpetual) inventory systems, however, have many fundamental advantages. A continuous inventory system automatically takes count of all procurements, job shop actions, and any other stock movements. In making sure that inventory levels are always in check and the books are updated in real-time, many aspects of inventory planning become easier and more transparent.
- Automate inventory management with a dedicated IMS/MRP system. Last but not least, implementing a dedicated inventory management solution or manufacturing ERP represents by far the biggest boost to a company’s inventory planning efforts as well as overall productivity. Whereas spreadsheets-based inventory planning might be cost-effective for small and simple operations, the level of automation and added functionality offered by modern production management software cannot be overstated. A new generation of SME-oriented systems constitute fully integrated production software that often matches big-ticket ERPs in terms of functionality at a fraction of the cost. This type of software significantly simplifies the inventory planning process while also reducing human errors.
MRPeasy is an all-in-one manufacturing ERP system purpose-built for small and medium distributors and manufacturers. This Software as a Service (or SaaS), 100% cloud-based ERP incorporates a powerful inventory management and production planning solution that unifies all business processes and even third-party financial, eCommerce, or fulfillment apps into a single digital ecosystem. MRPeasy includes a host of tools that make inventory planning easy and intuitive, including comprehensive production planning and scheduling tools, a procurement module, advanced inventory tracking, automatic reporting, vendor and supply chain management, real-time job shop reporting, sales management, and much more.
Key takeaways
- Inventory planning is a set of inventory management practices designed to help businesses keep optimal stock levels at any given time.
- In manufacturing, inventory planning mostly revolves around the planning ahead and timely replenishment of the raw material inventory in order to keep the WIP inventory in balance.
- Finished goods inventory also needs to be kept at optimal levels to avoid opportunity loss and mounting overhead costs.
- There are many different methods how to conduct inventory planning; best-known examples include demand forecasting, economic order quantity (EOQ), automating reorder points, or the Just-In-Time manufacturing principle.
- Inventory planning best practices include assigning roles and responsibilities to employees, ensuring sufficient inventory traceability is in place, adopting a continuous (perpetual) inventory system, and implementing an inventory management system or manufacturing ERP.
MRPeasy is free to try, easy to implement, and always affordable. Start your free trial today.