Inventory Optimization Methods and Techniques
Inventory optimization is the act of balancing inventory costs, service levels, and the complexity of inventory management. While there is no single magical solution for keeping your stock optimized, different methods and techniques are brought together in ERP/MRP systems.
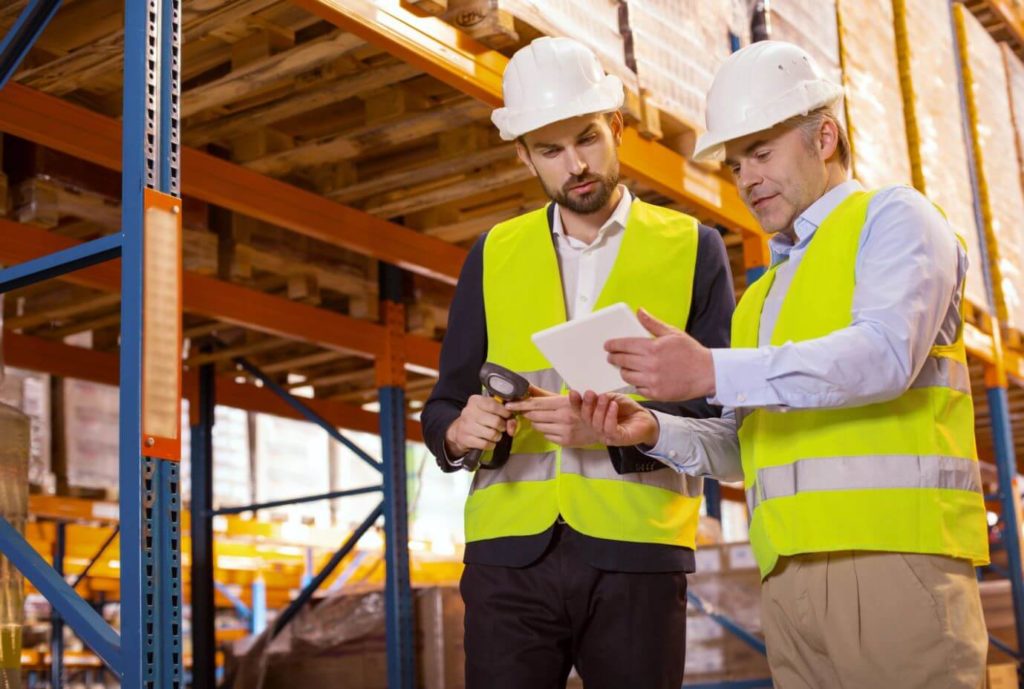
You can also listen to this article:
What is Inventory Optimization?
Inventory optimization is an umbrella term for a variety of methods that are used to balance inventory costs, inventory management complexity, and goals related to product availability.
Managing a large amount of stock keeping units and tracking their movements and performance is a difficult task on its own. Finding and maintaining the optimal inventory levels, however, may often seem like walking a tightrope over a gorge. That is where certain security nets and balancing tools come to your aid.
These methods range from simply keeping a buffer stock of your most important items to very complex, computer-aided systems that give you a real-time overview of your inventory status and requirements.
But in the end, the goal of all of those approaches is to make sure that:
- There are no stockouts or overstocking
- The service levels ensure customer satisfaction and reasonable lead times
- No excess cash is tied up in inventory
- Inventory costs do not eat up the profits
- There is no accumulation of dead stock
That means when inventory is well optimized, the overall operational costs of the company are reduced and service levels are high. On the other hand, ill-managed inventory can result in both low service levels and dead stock, meaning that customers could be lost while some goods could also be spoiled.
Inventory Optimization methods and techniques
To avoid the aforementioned business nightmares, companies use a combination of various methods, techniques, and tools to optimize their inventory. None of these are magical solutions that instantly solve your inventory management troubles, but through disciplined implementation and execution, they can bring on immense benefits over time.
1. Inventory tracking
The first point of order in inventory optimization is inventory tracking. Without exactly knowing what you have in stock and how your items move, it is impossible to start optimizing them. That is why all items need to be assigned a specific stock keeping unit code, stock lot numbers need to be assigned to stock, some individual items need serial numbers, etc. This all helps you track your inventory and get an accurate overview of what is going on in the stockroom.
2. Demand forecasting
By looking at the historical data, you can forecast roughly how much of your products will be sold at any period in case of regular demand. As such, demand forecasting is essential when trying to optimize your inventory. Although by using forecasting, you can prepare your company for regular demand as well as seasonal changes in demand – helping you prevent stock-outs as well as overstocking –, unforeseeable fluctuations require another approach.
3. Safety stock
Safety stock is a buffer of goods that is used to respond to unforeseen fluctuations in demand or in the case of supplier unavailability. Also known as just-in-case inventory, safety stock provides you with the means to continue production and deliveries when there are disruptions in the supply chain. That is why lately many companies that had previously opted for the just-in-time inventory model are reconsidering their policy of not keeping extra stock.
4. Reorder point
Reorder point is a simple yet effective method for preventing stock-outs without stocking excessive amounts of inventory. It is based on the premise of determining a certain level of inventory that would trigger a replenishment. That means when inventory drops lower than the reorder point, it is time to place another order. Of course, reorder points should never be arbitrary, rather they should be determined by taking lead times, demand, and the available safety stock into account.
5. Kitting
A valuable tool for optimizing both raw material inventory as well as products is kitting. In the case of material kitting, parts and materials required for making a product are bundled together to minimize picking time. Product kitting, however, means bundling various items that are often bought together, such as musical instruments and equipment, dining tables and chairs, or hygienic products like shampoos and shower gels. That way, companies can attach slower-selling items to fast-selling items, increase their inventory turnover, and avoid the accumulation of dead stock.
6. SKU rationalization
SKU rationalization basically means cleaning up your product catalog of items that do not sell. Many businesses continuously add items to their product mix, inflating their catalog along with their inventory. And in many cases, the performance of a company’s products will not be static. That is why SKU rationalization is needed – to weed out underperforming SKUs, reduce inventory costs, and free up cash that is tied up in inventory.
7. Stocktaking
Regular stocktakes are a critical part of keeping your inventory shipshape. Even if you have implemented inventory management software, occasional inventory counts help increase inventory accuracy, identify unaccounted-for shrinkage, detect and prevent theft, and eliminate inaccuracy in accounting. Stocktakes are also the only surefire way to discover forgotten inventory that has not been properly tracked.
8. Just-in-time
Just-in-time is a manufacturing and inventory management methodology that aims to absolutely minimize inventory. Its central premise is to work closely with suppliers and make sure that the ordered goods arrive just as production is scheduled to begin or just as the goods are due to be shipped to the customer. When using just-in-time, inventory does not have to be stored in huge warehouses, inventory obsolescence is not a risk, and overall efficiency can be improved while costs can also be minimized.
Inventory Optimization with ERP/MRP
Implementing an ERP/MRP system for inventory management gives you the chance to automate a huge portion of the processes related to the aforementioned inventory optimization methods. This kind of software is designed to help you in standardizing your processes and give you an accurate overview of what goes on in your inventory. They allow you to track your inventory and create accurate forecasts based on the historical data gathered by the software as well as to assess the performance of your SKUs for SKU rationalization. Reorder points and safety stocks can be assigned to your goods to avoid stock-outs and shortages while kitting can be used both for raw materials and to bundle your finished products. Just-in-time can be used in some systems thanks to their backward scheduling functionality. All in all, an ERP/MRP system is the best option if you are looking to reduce inventory management complexity while also drastically improving the efficiency of your processes. Today, these types of inventory optimization software are available for companies of any size at no great cost so often it makes sense to implement one as soon as possible.
Key takeaways
- Inventory optimization is an umbrella term for a variety of methods that are used to balance inventory costs, inventory management complexity, and goals related to product availability.
- There are many different methods and techniques that help companies optimize their inventory.
- The most important goals of inventory optimization are to ensure there are no stock-outs or overstocking, the service levels ensure customer satisfaction and reasonable lead times, no excess cash is tied up in inventory, inventory holding costs do not eat up the profits, and there is no accumulation of dead stock.
- Companies can make use of inventory optimization techniques such as inventory tracking, demand forecasting, safety stock, reorder point, kitting, SKU rationalization, regular stocktaking, and just-in-time.
- All of these approaches bring on benefits on their own, but you can make the most of them by using them together within an ERP/MRP system.
You may also like: Inventory Turnover Ratio – Formula and Tips for Improvement