What are Inventory Discrepancies and How To Avoid Them?
Whether consumers or vendors, your customers rely on you to get quality products delivered on time and in full. Inventory discrepancies caused by inventory data errors are a leading cause of delayed delivery, often resulting in reputational damage and loss of trust.
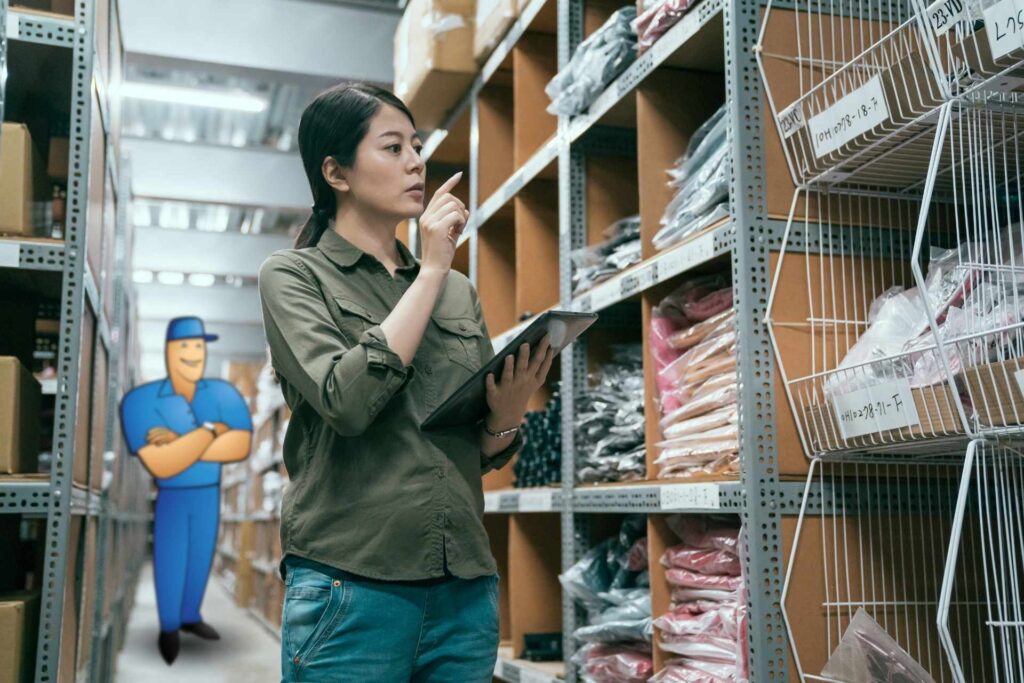
What is an inventory discrepancy?
Inventory discrepancy is a mismatch of inventory data. It means that what you think you have in stock doesn’t match the actual stock count. There can be several reasons for inventory discrepancies. We’ll discuss those in a minute. But they could easily lead to both stockouts and overstocked items.
Just like a stone dropped in a pool of water, inventory shortfalls have a ripple effect on your company. They affect almost every part of your business operations. Before we look at why they happen, let’s define the various types and common causes of inventory discrepancies.
Types and causes of inventory discrepancies
Not all inventory errors are due to a lack of expected inventory. Some are caused by having more products than you thought. Both are detrimental as one keeps you from fulfilling orders while the other may actually devalue your product.
Mismatched inventory counts
This simply means that what your inventory system says you have in stock doesn’t match what you have on hand. This often affects you on the production level because you don’t have the parts needed to complete an order. For instance, the system says you have 100 table legs when you only have 90 in stock. Your inventory records don’t match what you have in stock.
There are several reasons this could happen. For example, if a shipment of parts isn’t carefully counted to ensure accuracy during the receiving process, your receiving department may report items you didn’t actually receive. Inaccuracies in shipping records for accepted shipments is a supply chain issue that needs to be resolved.
Miscounting when physically tallying shelf inventory is another root cause for discrepancies. It’s easy for an item to be missed, particularly if it’s small. Incorrect data entry is another culprit. Entering in-stock values into the incorrect field or hitting the wrong key is often a human error.
Out-of-stock situations
While mismatched inventory counts usually refer to parts, stockout situations usually pertain to finished products. Your system says you have X number of widgets, but you really only have Y, a number less than expected.
This is sometimes discovered after a customer places a purchase order and you accept it, only to find out you don’t have enough for fulfillment. In the worst case, the customer gets disgruntled and buys from someone else, and that company becomes their vendor of choice.
Some of the common causes are delays in inventory records or errors in the integration between inventory systems and ordering platforms, particularly online ordering for e-commerce.
Another example is when someone “gifts” a product but never reports the amount to warehousing. For example, a manager may donate a food product to a worthy cause but fail to report it properly. This is just one of the unknown ways unrecorded shrinkage could happen in your inventory.
Overstocking and dead inventory
While not necessarily a discrepancy per se, overstocking and dead inventory are often the result of poor sales forecasting. Overstocking means you have more stock on the shelves than needed to meet demand. This excess stock often leads to price reductions, and you make less than desired on a product, sometimes selling retail products at wholesale prices or below.
Dead inventory items are those products that sit on the shelf for so long that they are no longer sellable or have become obsolete. Food items with expiration dates or those with a limited shelf life are two common examples. While overstocked items can be written down, meaning their value is refigured at a lower cost, dead inventory has to be written off. Both hurt your profit margins.
Either scenario has a negative impact on your business’s financial health and bottom line.
Misplaced inventory
Your inventory records show you have a product in stock. You know you have the product in stock. You just can’t find it. Misplaced inventory often happens due to changes in storage locations. A pallet of the product might be moved to another warehouse location. But the new location hasn’t been updated in the system. Another common reason is mislabeled products. If the wrong label is slapped on a product or pallet when scanned into the system, it’s entered incorrectly. Both can be largely mitigated using an effective warehouse management system.
Shipping errors
Most inventory discrepancies occur at the production or warehouse level, but shipping errors can also cause them. Shipping the wrong quantity than indicated on the order or shipping the wrong product affects inventory. This causes a discrepancy between inventory records and the shipping manifest.
Even damaged products, whether your or the shipping company’s fault, can cause inventory discrepancies. For example, if a damaged product is replaced, it’s taken from available inventory. Now, other orders based on the original stock count can’t be fulfilled.
Even though there are several cost implications in shipping errors, two of the major ones are the extra expenditure caused by reshipping the order and the return shipment fees for incorrect or damaged products. Either way, customer satisfaction is tainted.
The impact of inventory discrepancies
Stock inaccuracies happen. But if it’s widespread, it can seriously affect a company’s financial and operational performance. Direct financial losses, for instance, happen when overstocking requires that you have to lower the unit cost or write off a batch of products.
Inventory discrepancies can cause serious operational deficiencies that reduce productivity. Delays in order fulfillment and the increased labor needed to search for products and reconcile the books can really affect your profits. Missing raw materials when they’re needed for production disrupts production schedules and affects the whole workflow. This is especially true if you use optimized inventory and manufacturing systems such as just-in-time.
Discrepancies ultimately lead to unfulfilled or even canceled orders. Shipping delays, supply chain disruptions, and inaccurate order information lead to customer dissatisfaction and potential customer churn, where they leave for another vendor, never to return. Churn caused by a poor customer experience is a key metric for determining your business’s health.
How to find inventory discrepancies?
There are several ways to find and guard against inventory discrepancies. Many are done manually. However, the key to their effectiveness is regular, consistent action.
Below, we look at three types of inspections. All of them are methods of stocktaking, a fundamental process for ensuring accurate inventory records. In a stocktake, you physically count and record inventory levels, then compare them to your inventory data.
Visual inspection
Even if you use technology to maintain your inventory list, there’s no substitute for walking the warehouse aisles and getting eyes on the stock to maintain inventory control. You might not see everything, but regular visual inspections as part of your overall inventory management system significantly help highlight glaring issues.
Spot-checking or cycle-counting
This inventory tracking method takes small, random samples of a product or part. You physically count them and compare them to recorded amounts. This can give you a quick snapshot of both your inventory management process’s effectiveness and inefficiencies.
Cycle counts are similar to spot checking, where a small portion of your inventory is checked manually. The difference is that this audit is done more regularly on a set schedule.
Regular audits
While time-consuming, a full audit allows you to evaluate your inventory process more comprehensively. Many companies conduct audits periodically, quarterly, biannually, or once a year. Since every item is manually counted, it’s labor intensive. But it pretty much guarantees a comprehensive overview.
There are several benefits to using stock counts:
- Inventory accuracy – ensures that inventory records reflect actual inventory levels.
- Reduced shrinkage – identifies loss due to theft, damage, obsolescence, or spoilage.
- Improved order fulfillment – avoids stockouts and ensures customers get their orders on time.
- Effective stock management – acts as a gauge for inventory management, leading to the identification of trends, optimization of stock levels, and improvement of the overall quality of your inventory system.
Preventing and avoiding inventory discrepancies
The key to an efficient inventory management system is consistency. In addition to regular stocktaking, here are essential steps you can take to minimize discrepancy rates and ensure a successful business.
Software implementation
Using inventory management software for traceability is something most manufacturing companies do. It’s a practical option to gain real-time insight into inventory statistics. Choosing the correct solution goes a long way in making sure your inventory records stay in sync. If the stock management system is standalone, you also need to integrate it with other business software that you use, especially sales and order-taking programs. However, good manufacturing software provides an all-in-one solution.
Automation technologies, such as RFID, barcode inventory control systems and scanners, and QR codes tied to product SKUs, can be further implemented or come built into modern inventory software. These greatly increase accuracy in data collection and entry.
Remember to train your production and warehousing teams to use these tools properly. Proper employee training on new technologies is critical when they are used.
Operational improvement
As you begin to employ your inventory management, you’ll likely find ample opportunities to streamline your processes. Developing SOPs (standard operating procedures) and guidelines helps with consistent use. Be sure to set quality control standards to help keep damaged products or incorrect shipments from going out the door. SOPs give you a foundation for determining the root causes of inaccurate inventory counts. Here again, you’ll need to offer employee training to ensure success.
Continue reading: 12 tips for improving inventory management efficiency.
Security measures
It’s frustrating, but sometimes products—particularly small electronics and food items—tend to sprout legs and walk out the door. Employee theft is a root cause of shrinkage. Part of any effective inventory management program is security. Physical premise security might include closed-circuit cameras and security guards. Some employees might find this invasive, but remind them it’s for the security of their jobs as well.
Access control measures are definitely a good idea to prevent entry by unauthorized persons. This is often accomplished by employing badge readers, which can be customized for each user.
Network system security is also critical to protect data from hackers. Cloud-based solutions are often more secure than on-premise infrastructures.
Increase inventory accuracy through automation
Several good software solutions exist that help you moderate and lessen inventory discrepancies. MRP (Material Requirement Planning) systems delineate the parts needed for product manufacturing. Better applications will check through existing inventory, allowing you to automatically adjust production schedules and book items into orders. Fully integrated solutions form comprehensive manufacturing ERP systems that tie your whole business management together.
The hardware required to automate your inventory records depends on the solution you use. For most cloud-based solutions, team members can access the information on portable devices such as laptops, smartphones, and tablets. In-house programs will require an IT infrastructure, sometimes a complex and expensive one, to store and access recorded inventory data.
Whatever you choose, automating stages of your inventory processes and procedures has massive benefits. Limiting human error, particularly in data entry, avoids many inventory inaccuracies. You may also find several efficiency improvements and cost savings.
For example, when inventory collection is automated, it frees up personnel for more useful labor-intensive tasks that require the human touch. Additionally, the data stored in the system can provide cost analysis data and enable production forecasting, often with the press of a few buttons.
Best practices for ensuring inventory accuracy
What many manufacturers discover is that maintaining inventory accuracy comes down to a combination of both physical and software-based applications:
- Perform routine, consistent stock counts as listed above to identify discrepancies quickly, permitting swift mitigation.
- Adopt a cycle counting program where portions of your inventory in specific locations are assessed to keep inventory control manageable.
- Security measures help prevent loss from theft, damage, and spoilage.
- Use a more defined, structured storage system to avoid warehousing mistakes and ensure everything is in its correct location.
- Ensure proper supply chain tracking and SOPs are in place and being followed.
- Make sure your inventory management software is synced up with your sales process, including e-commerce business websites, to maintain real-time statistics.
Finally, upgrading your inventory management process to include software and hardware like barcode scanners or RFID provides better data accuracy. These solutions, along with your human workforce, keep your business operations running more smoothly.
Key takeaways
- Inventory discrepancy is a mismatch between recorded and actual inventory. It occurs when your system indicates a certain stock level that doesn’t match what is physically available, leading to potential stockouts or overstock situations.
- Discrepancies are mostly caused by human error and process lapses. Common causes include miscounts during physical stocktaking, data entry errors, shipping mistakes, and unreported product movements.
- Inventory discrepancies are important to avoid because they directly impact business performance. They can lead to production delays, customer dissatisfaction, and financial losses due to inefficient stock management and lost sales.
- Both manual and automated methods are essential in detecting and mitigating discrepancies. Regular stock counts, visual inspections, and cycle counting, when combined with technology like barcode scanners and RFID, help ensure that inventory records remain accurate.
- Integrated inventory software streamlines operations and improves accuracy. By syncing real-time data across production, warehousing, and sales channels, these systems reduce human error, enhance efficiency, and support better decision-making.
Frequently asked questions (FAQ)
Inventory discrepancies typically arise from human errors during physical stock counts and data entry, as well as shipping mistakes and mislabeling. These issues can occur when received shipments aren’t accurately recorded or when products are misplaced due to improper handling.
To calculate an inventory discrepancy, subtract the actual physical count from the recorded inventory number in your system. A negative result indicates a shortage, while a positive one suggests overstock. This calculation is essential for identifying errors and implementing corrective measures.
Common causes for stock discrepancy include miscounts during manual stocktakes, inaccurate data entry, and errors in shipment documentation. Additionally, misplaced items or unreported stock movements can lead to mismatches between your system and physical inventory.
You might also like: 11 Most Important Inventory Management KPIs in 2025