Inventory Control – An Essential Guide for Small Manufacturers
Reliable inventory processes are the foundation for a well-functioning and profitable manufacturing or distribution business. In this post, we look at essential topics for achieving a high level of control over your stocking process.
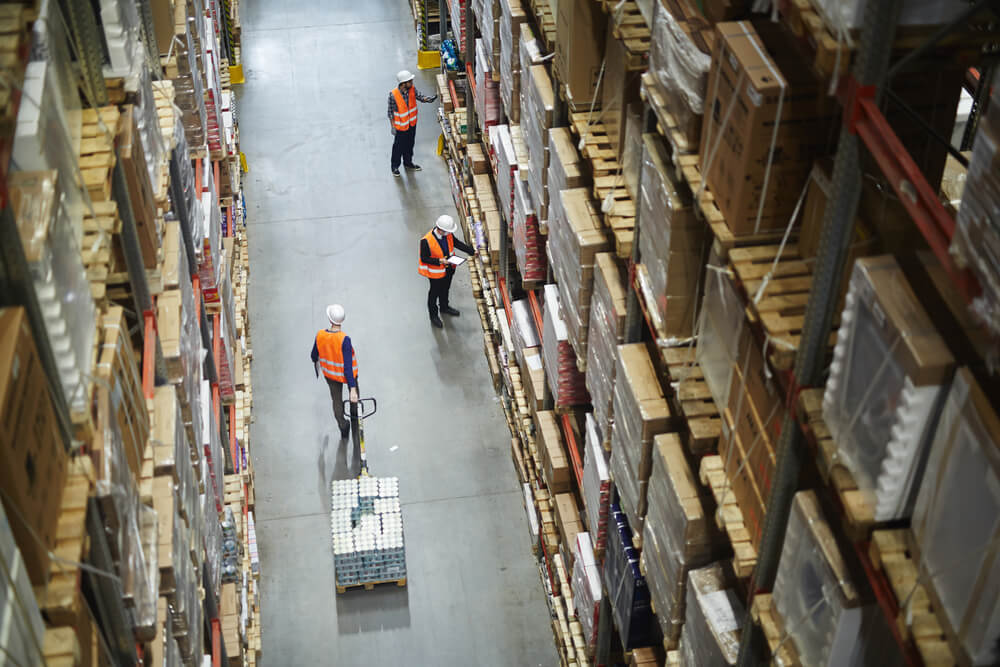
What is inventory control?
Inventory control is the process of ensuring that the right amount of the right inventory items is on hand at the right time. It consists of various means to monitor the movement, location, status, quantities, and even the quality of goods in a company. These might include:
- stock tracking systems,
- inventory counting procedures,
- warehouse management practices,
- supply chain management processes, etc.
Inventory control aims to keep the optimal amount of goods in stock, avoiding overstocking and stockouts—the two biggest cash drains in inventory management. Thus, inventory control helps balance holding costs and material availability, making it an essential business process for maintaining profits and ensuring financial liquidity.
Inventory control vs inventory optimization
Inventory control is a subset of the larger inventory management process that focuses on inventory already in stock. Think maintaining the right inventory levels, ensuring stock quality, avoiding waste or spoilage, and having good in-house inventory practices.
On the other hand, inventory management is more encompassing, including further processes like procurements, supply chain management as a whole, the distribution and returns of finished goods, warehousing, inventory accounting, forecasting, and more.
Another term often used interchangeably with inventory control is inventory optimization. The two are distinct, however, in that inventory optimization utilizes data analysis and demand forecasting to optimize inventory costs with service levels. So, whereas inventory control is about maintaining stock stability, optimization tries to maximize long-term efficiency by fine-tuning stocking levels across the supply chain.
Types of inventory control systems
Inventory control can be achieved in numerous ways, from paper-based checklists to automated software. Inventory control systems are sets of protocols and processes for systematically conducting relevant stocking practices. They can be manual or automated and focus on any number of tasks, from tracking stock to detecting inventory shrinkage.
Let’s look at three types of inventory control systems and how they differ.
Manual and paper-based systems
Manual inventory control methods rely on physical records, such as logbooks, stock cards, or printed forms, to track stock levels and movements. This approach requires employees to document inventory transactions by hand. Manual tracking is easy to use but prone to human error. Very small businesses with limited stock complexity may find manual tracking sufficient. However, as complexity grows, inaccuracies are a common sight.
Manual inventory control can be cost-effective upfront, but its inherent inefficiencies often lead to increased labor costs and operational slowdowns over time. For example, physically counting stock and manually updating records to reflect stock levels makes real-time tracking difficult and increases the risk of imbalances. Still, despite its limitations, many businesses use this method as a backup or in combination with digital systems for double-checking inventory accuracy.
Spreadsheets and other periodic inventory systems
Spreadsheets are a step up from manual inventory control techniques. They offer a more structured way to record stock data. Businesses using spreadsheet apps like Excel typically update inventory records periodically—daily, weekly, or monthly—rather than in real-time. This approach provides more flexibility than strictly manual methods but still lacks automation, making it susceptible to errors or version control issues.
The periodic inventory system of spreadsheets-based inventory control relies on regular stock counts to reconcile records with actual inventory for detecting discrepancies between reported and real stock levels. Businesses using spreadsheets must carefully manage formulas, data input, and version history to prevent errors from cascading throughout their inventory records. While this system can work reasonably well for small businesses with simple inventories, larger operations and complex inventories with a multitude of stock keeping units (SKUs) require more robust solutions to maintain accuracy and efficiency.
Inventory management software
Inventory management software offers an automated and data-driven approach to inventory control. These systems integrate different aspects of inventory management and use internet kiosks, barcode scanning, RFID, and other tech to monitor and report inventory movements in real time. They include a perpetual inventory system—one that continuously updates stock levels with each transaction or stock movement. This eliminates many inefficiencies of manual methods, reduces errors, and improves decision-making.
Inventory software automatically updates quantities as purchases, sales, production, or even product returns occur. Inventory management systems often integrate with other business software like accounting, fulfillment, or e-commerce systems, offering a streamlined data flow across operations. This provides unmatched long-term benefits, helping to maintain optimal stock levels.
Continue reading about perpetual vs periodic inventory systems.
Functions of inventory control
As we have seen, inventory control deals mostly with maintaining healthy stock levels and tracking and managing stock movements for items at the warehouse or production facility. More far-reaching SCM and inventory aspects like vendor management, shipping, and distribution or sales processes are involved only inasmuch they contribute to the above. Let’s go over the main functions of inventory control.
Stock levels and reordering
Keeping just the right amount of stock on hand is the cornerstone of inventory control. This involves setting reorder points, finding and adjusting effective safety stock levels based on demand patterns, and triggering replenishment orders for raw materials before they run out. The goal is to avoid running out of stock while also ensuring you’re not over-investing in slow movers or holding capital hostage in unused inventory.
Inventory tracking
Inventory control also means knowing exactly where your stock is at any given time. Whether on a shelf, in a production line, or in transit between locations, inventory control means maintaining visibility, avoiding misplaced items, and ensuring stock records match the reality on the warehouse or shop floor. Inventory control is both a means of furthering traceability as well as reliant on tracking systems for efficiency.
Integration between production and sales
Inventory is not an isolated process—it’s a connecting thread between production, procurement, and sales. Inventory control needs to ensure that when production needs materials, they’re there; when sales promises delivery, the stock actually exists; and when procurement places orders, they’re based on real stock levels, not guesswork. Cross-departmental visibility is necessary to avoid last-minute scrambles and keep the entire operation running smoothly.
Inventory accounting and financial stability
Every stock movement, from incoming deliveries to internal transfers, consumption, scrap, and final sales, must be accurately recorded and reconciled with your accounting system. Without this alignment, it’s impossible to produce reliable financial statements or to fully understand the amount of tied-up cash.
Inventory control plays a critical role in accurate cost of goods sold (COGS) calculations and inventory valuations, which feed directly into profitability analysis and tax reporting. Whether your company relies on FIFO, LIFO, weighted average cost, or specific identification, inventory control processes ensure that physical stock, financial records, and valuation methods are all in sync. Inventory control simplifies compliance, boosts financial transparency, and gives management a clearer view of cash flow health.
Maximizing inventory profitability
As noted, inventory is tied directly to your profitability. Effective inventory control helps you avoid the silent profit killers: dead stock, obsolete materials, expired goods, and unnecessary holding costs. It’s also the foundation for leaner operations, where every item in stock has a purpose, moves quickly, and supports cash flow instead of draining it. After all, effective inventory management boils down to maximizing your stock’s profitability.
Forecasting demand
While forecasting is a broad topic in its own right, it’s directly linked with inventory control. Accurate data on stock turnover, lead times, and consumption rates flows from the inventory system into forecasting processes, helping shape more reliable and adaptable demand plans. At the same time, insights from historical sales and market trends feed back into inventory control, helping to determine the optimal amount of inventory, guide procurement decisions, and even influence pricing strategies to keep inventory balanced and profitable.
Analytics and reporting
Modern inventory control is as much about analyzing trends and tracking inventory data as it is about counting physical inventory. How fast do materials turn over? Which products tend to tie up the most capital? Where are errors or shrinkage coming in? Well-set-up inventory control processes feed data into dashboards and reports that give managers greater visibility to make decisions faster and spot problems before they escalate. They also provide actionable metrics for compliance and regulatory audits.
Common challenges in inventory control
Inventory control has many inherent challenges. For small manufacturers, these can stem from limited resources, fragmented business management, and, crucially, outdated inventory processes.
Inventory visibility is one of the most persistent issues and one from which most troubles stem. When stock data is spread across spreadsheets, manual records, or disconnected systems, it’s difficult to get a clear picture of what’s actually available or when it’s coming in. Lack of transparency and resulting inaccuracies inevitably lead to delays, order mistakes, and a lot of extra time spent tracking down materials.
Poor integration between inventory, purchasing, production, and sales processes is a closely related issue. If the above functions operate in isolation, business-critical information on purchase orders, production schedules, and customer demand doesn’t flow smoothly. Without a connected system, businesses risk constant material overordering, stockouts, missed delivery deadlines, or running into production bottlenecks.
Human error plays a big role in stock control, especially in smaller businesses that still rely on manual processes. Data entry mistakes, poor communication between departments, or forgetting to report jobs significantly erode inventory accuracy over time. Even small discrepancies can become costly problems if left unchecked.
To overcome these challenges, businesses can apply a range of tried-and-true inventory control techniques tailored to their size and complexity.
Inventory control methods and approaches
Next, let’s take a look at some inventory management techniques that delve into inventory control from different angles. While some of these overlap with broader inventory management strategies, they each provide valuable insight for keeping stock under control, whether through prioritization, valuation, timing, or ongoing checks.
ABC analysis
ABC analysis is an inventory prioritization method that segments inventory into three categories based on value and importance: A-items are the most valuable and typically the most tightly controlled, while B-items are moderately important, and C-items have the lowest value and need the least attention. This approach helps businesses allocate control efforts where they matter most so that high-value items receive the most frequent monitoring and inventory checks.
This is especially useful for smaller operations with limited resources because it helps focus inventory control efforts where they deliver the highest return. ABC analysis lets companies streamline inventory audits and cycle counts, appointing tighter control for the products that most affect the bottom line.
Find out more about ABC analysis.
Stock control by inventory valuation
Inventory control is not just about operational efficiency but also about financial health. This approach focuses on controlling inventory based on how much value is tied up in it by cost or profit potential. How inventory is valued directly affects how businesses should approach optimal stock levels and reorder decisions. Different valuation methods, like First In, First Out (FIFO), Weighted Average, and Specific Identification, each paint a slightly different picture of inventory value and the cost of goods sold.
For example, FIFO shows higher inventory values during rising prices, encouraging businesses to be more cautious about carrying excess stock. On the other hand, LIFO (Last In, First Out) reduces taxable income by showing higher costs, which could make businesses more comfortable carrying larger inventories in some cases. Weighted average smooths out price fluctuations, offering a more stable view of inventory value, while specific identification allows businesses to closely tie stock to actual costs — especially useful for high-value or custom products. Like this, stock valuation approaches feed directly into the actionable insights of inventory control systems, shaping decisions around reordering, write-offs, and pricing strategies.
Continue reading about different inventory valuation methods.
Just-in-time inventory
Just-in-time inventory aims to minimize on-hand inventory by timing deliveries to arrive exactly on time for production or order fulfillment. In this approach, inventory is constantly moving in and out, with very little sitting idle on shelves. While JIT is often considered a holistic inventory and production philosophy, its day-to-day execution relies heavily on tight inventory control, tracking supply chain movements, and real-time stock level monitoring to ensure gapless operation.
For small manufacturers, JIT can be both a major cost-saving opportunity and a risk. It reduces storage and carrying costs but leaves less room for error if deliveries are delayed or forecasts miss the mark. Successful JIT requires precise inventory control, close collaboration with reliable suppliers, and crystal-clear visibility into both incoming materials and current production needs.
Read more about Just In Time inventory management.
Cycle counting
Cycle counting is a sampling-based inventory control method used to increase inventory accuracy and detect discrepancies. Inventory is checked in small sections on a regular basis rather than performing a full physical inventory count all at once. Different items are counted on rotating schedules, with high-value or high-turnover items counted more frequently than slower-moving stock. By spreading inventory counts throughout the year, businesses can spot discrepancies early, correct errors sooner, and maintain accurate inventory records without disrupting daily operations.
For small manufacturers, cycle counting is a practical way to keep inventory records reliable without a large inventory management team. When combined with ABC analysis, cycle counting becomes a cost-effective way to maintain tight control over essential materials and products. It also helps businesses catch operational issues like picking errors, unrecorded scrap, or supplier delivery errors before they impact production or customer orders.
Continue reading about inventory cycle counting.
Tips and best practices for effective inventory control
Effective inventory control is as much about counting stock as it’s about building working systems, habits, and strategies to keep inventory accurate and costs manageable. Below are practical tips and proven techniques to help strengthen your inventory control processes.
Practical processes for better inventory control
- Develop clear SOPs for inventory processes. Standardized processes keep everyone on the same page, whether receiving raw materials, recording stock, or picking items. When staff follow the same steps every time, inventory data becomes more reliable — and surprises become far less common.
- Train staff on inventory systems, processes, and the importance of accurate recordkeeping. Inventory control only works when the people handling stock understand their role in keeping records accurate. Whatever inventory control system is being used, investing time in training saves far more time (and money) down the road.
- Track inventory comprehensively across locations and stages. Stock items need to be accounted for, whether sitting in raw materials storage, on the shop floor, or packed for shipping. Gaps in visibility create gaps in decision-making, and those gaps tend to show up right when you can least afford them.
- Monitor key inventory KPIs like turnover, carrying costs, and stock accuracy. Inventory management metrics are crucial for gauging your inventory efficiency. Knowing how quickly items move compared with your averages, how much stock is sitting idle, or how often your counts match reality forms the basis for data-based decision-making.
- Conduct regular inventory counts, with cycle counting for high-priority items. Even with good systems, physical counts are essential to ground-truth your inventory data. Breaking counts into smaller, regular cycles makes them more manageable and helps you catch discrepancies when they’re still small enough to fix easily.
- Adopt barcoding or RFID systems to improve tracking accuracy. Manual data entry will always have limits – barcode systems or RFID (Radio-frequency identification) tagging remove much of the guesswork. Automating how stock is logged, moved, and picked saves time and helps protect you from small errors quietly adding up.
- Optimize your warehouse layout to speed up picking and reduce errors. Warehouse management—the physical flow of your goods, optimal storage layouts, and picking and handling protocols—matters a lot. Investing time in things like organizing physical storage locations, grouping frequently used items together, clearing physical bottlenecks, and making sure stock locations are clearly labeled all add up to a smoother stocking operation.
Strategic techniques for long-term inventory optimization
- Explore statistical methods like economic order quantity (EOQ) or reorder quantity. Replenishment decisions shouldn’t be guesswork, especially when data can tell you exactly when to reorder and how much to bring in. Using methods like EOQ or reorder quantity helps you fine-tune these decisions to avoid excessive overages or shortages.
- Use inventory optimization techniques to balance stock levels with demand. Inventory optimization is about finding the perfect balance in stock levels to maximize cash flow and lower storage costs. By blending demand forecasts with actual turnover data and other metrics, inventory optimization helps strike the balance.
- Proactively manage aging and obsolete inventory to free up space and capital. Inventory that doesn’t move ties up money and storage that could be better used in other ways. Regularly reviewing older stock for clearance, repurposing, or disposal keeps your inventory lean and responsive.
- Explore consignment or selective vendor-managed inventory (VMI) for certain materials. In some cases, your suppliers may be better equipped to handle stocking decisions for key materials. Consignment inventory or VMI agreements can lighten your inventory load, especially for expensive or long-lead items, as long as your vendor relationships are strong.
- Invest in inventory management software and automation for better visibility and control. Good software connects purchasing, production, and sales into a single, always up-to-date system. Automation helps you scale without losing visibility or control as your business grows.
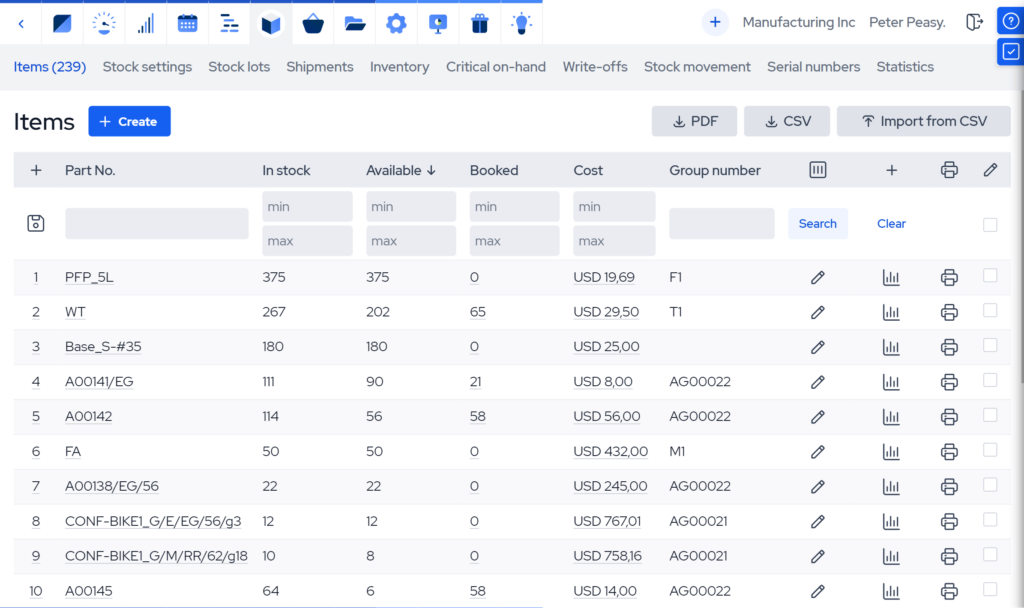
Stock control with inventory control software
As we’ve seen, inventory control encompasses many processes — from tracking stock movements and maintaining accurate records to preventing waste and aligning inventory with demand. Effective inventory control is about making sure inventory decisions actively support profitability, operational efficiency, and customer satisfaction.
This is where inventory management software can make a real difference. By automating many of the core inventory control tasks, these systems reduce manual work, improve data accuracy, and make stock information instantly accessible across departments. From receiving to production to shipping, every transaction updates inventory levels automatically, ensuring everyone works with the same information.
Inventory software does far more than just track stock. It connects inventory control with procurement, production planning, sales, and even financial reporting. Integrating your inventory process enables near-complete visibility into stock levels and the processes that impact them, turning inventory into a strategic advantage.
Benefits of inventory software
For small manufacturers juggling production, procurement, and sales with limited staff, having one integrated system greatly simplifies operations and reduces the risk of errors.
- Cloud-based systems provide real-time access from anywhere. Managers, production planners, and sales workers all work from the same up-to-date data, whether they’re on-site or remote.
- Automation reduces human error. Manual updates are replaced with automatic stock adjustments when materials are received, used, or shipped.
- Automated tracking instantly captures every inventory movement. Full traceability makes it easier to resolve discrepancies, manage recalls, and track lot history.
- Integrated production management links inventory to work orders. Material availability, production progress, and finished goods are all visible in one place.
- Built-in barcode systems streamline stock handling. Every scan updates stock levels automatically, improving both speed and accuracy.
- KPI tracking tools provide actionable insights. Track turnover rates, carrying costs, stock accuracy, and more to spot trends and fine-tune inventory strategies.
- Seamless integrations with fulfillment, accounting, and e-commerce platforms. Data flows smoothly across systems, eliminating manual reconciliations and reducing the risk of errors.
- Inventory software turns control into a competitive advantage. Accurate data, faster processes, and better visibility across departments all contribute to smarter, more profitable operations.
Key takeaways
- Inventory control is the process of ensuring the right materials and products are available at the right time and in the right quantities. It focuses on tracking, managing, and maintaining stock already in-house.
- Inventory control is important to avoid costly stockouts or excess inventory, cash flow problems, and production delays. It supports both day-to-day operations and long-term profitability.
- Inventory control systems can be manual, spreadsheet-based, or fully automated using inventory management software. The right system depends on your business’s size, complexity, and needs.
- Essential inventory control functions include tracking stock levels, managing reorder points, integrating with production and sales, maintaining accurate inventory valuations, and generating actionable reports.
- Some inventory control methods to focus on include ABC analysis, cycle counting, economic order quantity (EOQ), and just-in-time (JIT) inventory. Combining these methods helps balance accuracy with efficiency and cost control.
- Inventory management software offers small manufacturers real-time visibility, automation, and seamless integration across departments. It helps businesses scale efficiently while reducing errors and improving decision-making.
Frequently asked questions (FAQ)
Inventory control is the process of monitoring, managing, and maintaining stock levels of in-house goods to ensure the right items are available at the right time. It focuses on tracking stock movements, preventing errors, and keeping inventory records accurate.
Inventory can be valued using either the FIFO (First In, First Out), LIFO (Last In, First Out), Weighted Average Cost (WAC), or Specific Identification method. Which method best suits your needs depends on your product types, cost structure, and financial goals.
Good inventory control prevents overstocking, stockouts, and excess holding costs, freeing up working capital and reducing waste. Accurate inventory data also supports better purchasing, production planning, and pricing decisions, all of which improve profitability.
You might also like: Top 11 Supply Chain KPIs – Guide for 2025