Inventory Adjustments Within a Manufacturing ERP
By implementing common sense and best practices for inventory adjustments, a company can realize inventory accuracy that keeps processes on track.
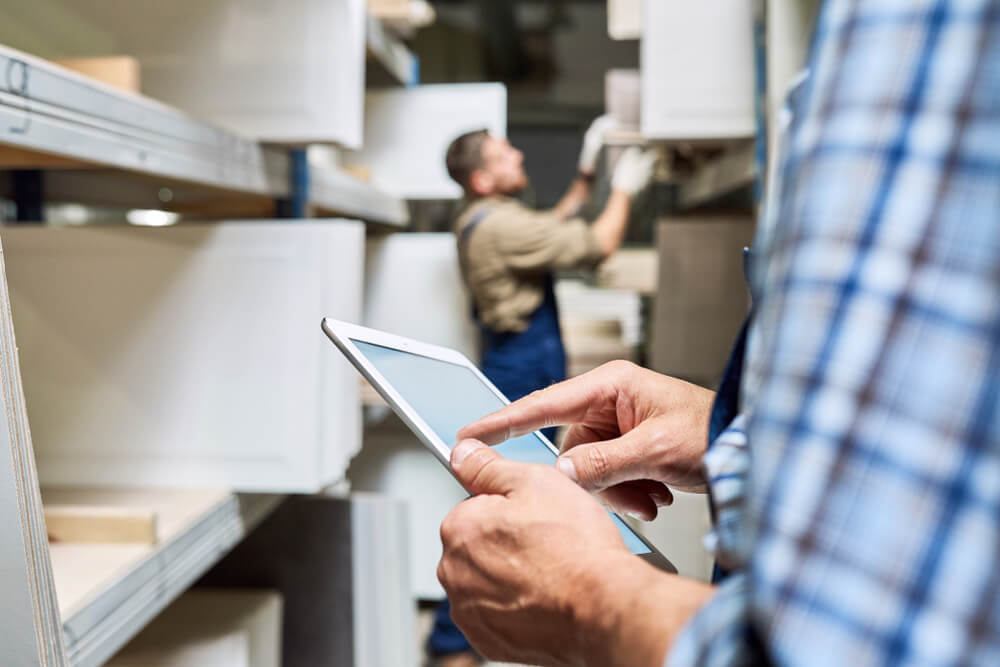
You can also listen to this article:
While manufacturing’s primary focus is production, the upstream and downstream activity within a company is critical to keeping that production optimized and efficient. And few things are as important to continued productivity success than accurate inventory. With it, companies can remain agile and able to supply their customers with goods on demand. But if inventory accuracy wanes, costs can rise, customers may leave, and supply chain management can suffer.
In the complex world of today’s manufacturing, managing inventory using an ERP system is a vital capability. By leveraging the ERP’s capabilities, inventory functions can be automated. It also allows companies to initiate accurate scheduling for production and planning for raw materials and capacity. These tools can be tied together to allow a company to make better business decisions and see further ahead in the curve.
The Case for Strong Inventory Organizational Procedures
Despite the value of having inventory tied closely to a company’s ERP, the ERP system alone cannot be the driver of the inventory system. It is important for the factory to have strong organizational procedures in performing the tasks required to keep the inventory current and accurate. This may include the “ground rules” for conducting inventory, cycle count procedures, inventory adjustment procedures, and inventory reconciliation for problems.
Some best practices for inventory management and the proper setting of organizational procedures to optimize accuracy include:
- Automate Inventory Functions – This does not mean turning management approvals of inventory decisions over to a computer system. Rather, it means that automating inventory control functions within an ERP can make sure that organizational procedures are followed. It may be in the form of alerts for low stock or large swings in on-hand stock of specific items. It can also include regular audits of min/max levels, “buy” alerts, and other functions that use the ERP to enact the procedures management has identified as vital.
- Develop strong vendor relationships – By working with vendors on programs such as Vendor Managed Inventory (VMI), companies can push material qualification and forecasted stock responsibility onto vendors. This helps ensure that what comes into the factory is correct in terms of quality and quantity and reduces overstock.
- Use Analytics Correctly – By setting strong management practices for inventory, managers can utilize the analytical and predictive functionality of their ERP because their confidence in the accuracy of inventory levels are high and are closer to real-time.
- Streamline for JIT – When possible, using the real-time capabilities of an ERP in conjunction with well-managed control allows companies to move to Just in Time (JIT) inventory. This can reduce holding costs and reduce the money tied up in materials to improve cash flow.
Inventory Adjustments
Inventory adjustments are important within manufacturing because they often must be done for different types of inventory. In many manufacturing operations, inventory can mean raw materials, work in process (WIP), or finished goods. As a result, inventory adjustments may be needed to help keep balance sheet data correct for income statements.
Adjustments that are proper and that can be automated include transfers from raw materials to WIP, transfers from WIP to finished goods, and transfers from finished goods to shipped. These are proper inventory adjustments common to most manufacturers. They can be automated within the inventory management system or tied at the BOM level to the ERP to reduce based on shop orders moving through the system.
The value of managing inventory within the constructs of an ERP means that these normal transfers can be done in accordance with standard operating procedures (SOPs). The focus should be on keeping these adjustments as close to real-time as possible. This allows other analytical and predictive capabilities within the WMS or ERP to be accurate and reduces the number of inventory adjustments made.
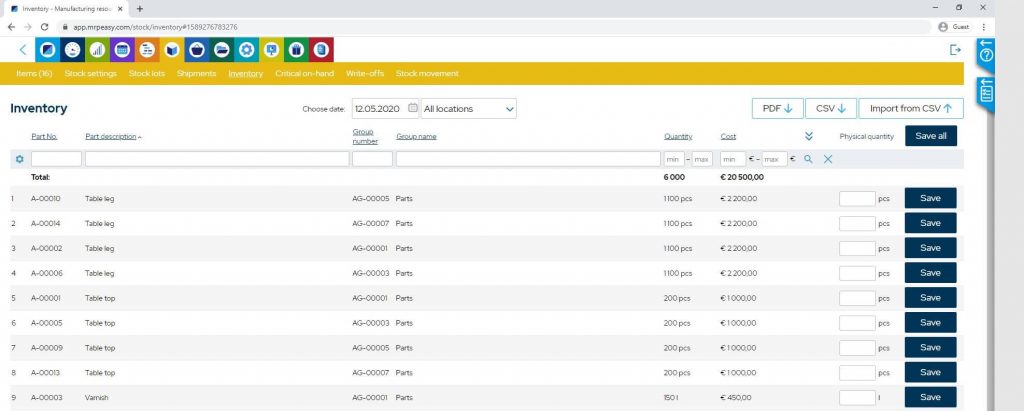
Dangers of Inventory Adjustments
Inventory adjustments work adversely against a manufacturer when they are the result of a lack of strong inventory SOPs or when the data input into the system is incorrect. In these cases, inventory adjustments can impact the ability to meet deliveries, drive up holding costs, create stockouts and overages, and other problems.
Some of the dangers of inventory adjustments include:
- Carelessness – If staff are not properly trained, or do not have the right tools, or have veered from established procedures, they can be careless in transactional data such as transfers, locations, and issuance. As these inaccuracies multiply, they can have a cumulative effect where adjustments are not made for the normal flow of goods between materials, WIP, and finished goods, but are forced adjustments that throw off the accuracy of the whole system. This can destroy stock history and degrade the reliability of the information.
- Training and User Issues – Small to medium-sized companies often have staff members who wear “many hats”. While this is a good way to optimize labor utilization, if someone is not an “expert” in one of their areas of responsibility, the risk of inventory adjustments can increase. Small to medium manufacturers are also prone to lax management of user permissions. This gives unauthorized staff, or staff with little to no experience in inventory, the opportunity to make mistakes that can skew inventory accuracy, and require adjustments as well. These mistakes may be unintentional, but they are costly.
- Vendor Issues – Weak relationships with vendors can also cause unnecessary inventory adjustment. Vendors whose material has not been properly validated, or those who have a history of mislabeling stock or producing stock that is off quality, can force inventory corrections that throw off the accuracy of the system.
Proper Procedures for Inventory Adjustments
To ensure that inventory adjustments are related to material flow and normal procedures and not related to human error or oversight, there are several steps manufacturers can follow to implement best practices.
- Approval Levels for Adjustments – Just because a system is automated does not make it accurate. The data inside a WMS or and ERP is only as good as the data entered. As mentioned, strong organizational procedures are required to keep inventory accurate and transactions correct. This includes proper levels of management approval for any major adjustments. Setting max inventory adjustment levels for inaccurate line items before approval is required can help managers find root causes to correct so that further occurrences can be controlled.
- Proper User Permissions – When required, manual inventory adjustments should be done by a single person or a small group of “super-users” with deep organizational knowledge and equally deep knowledge of the inventory system and the functionality of the ERP. This means they follow the procedures and verify that permission has been given for the adjustment so that arrangements can be made to compensate for the stock difference and so that all areas (production, sales, finance, customer service, etc.) can be notified of an impact if necessary.
- Cycle Counting – When possible, cycle counting should be included as part of established inventory SOPs. Regular stock-taking should count all goods in a full inventory, but cycle counting on a scheduled basis between monthly and quarterly full inventory cycles can help identify needed adjustment before it grows too large and can provide a path for early correction of the root cause.
- Real-Time – By tying inventory to the ERP system, managers can analyze problems as they occur. Like cycle counting, the more “real-time” the inventory analysis, the more likely staff, and management can identify the problem before it grows too large. Much of the analytical functions can be accomplished within the ERP platform, or with a WMS tied to the ERP via an API.
You might also like an article about Inventory Valuation Methods – Finding the Right Method.
Inventory is the lifeblood of production. Without the raw material, WIP, and finished goods smooth flow, costs increase, customers are lost, and the company can suffer. By implementing common sense and best practices for inventory adjustments, a company can realize inventory accuracy that keeps all these things on track.
Learn about other benefits of using MRP/ERP software and find the best suited one for your company’s needs from our list of the Top Six Manufacturing ERP Systems for Small Manufacturers.