How MRP System Improves Purchase Planning
Manufacturing Resource Planning (MRP) Systems have been around for many decades, initially known as Material Requirements Planning Systems. These systems operate on the principals of determining what is needed, how much is needed and when the materials are needed to complete production in a timely and cost-effective manner.
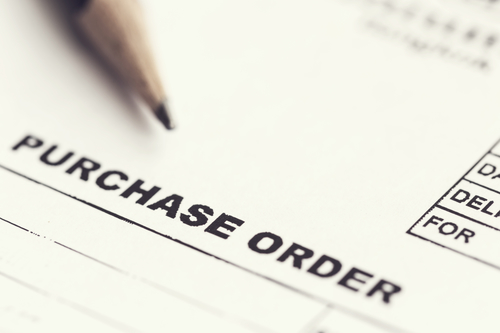
You can also listen this article:
MRP systems use sales forecasts in conjunction with input variables such as machine and labour units to calculate requirements and recommend a “buy” position, or strategy, to complete the schedule in an optimized manner.
MRP systems are highly dependent on accurate BOM inputs. And in addition to what, when and how much material is required, these systems may also take other variables into accounts such as perishability, current “on-hand” inventory and lot size for both materials and finished goods to plan and recommend purchasing decisions. In the past, MRP systems were largely utilized by large manufacturing companies with economies of scale that could deploy the system on an on-site basis to optimize production. Today, however, cloud-based computing, advanced analytics, and modularity of MRP systems have “leveled the playing field” to allow small and medium-sized businesses (SMB) to take advantage of MRP systems as a tool regardless the size and scale of a company.
Who Uses an MRP System?
MRP systems are “push” systems. As such, they are ideal for Make to Stock (MTS) and discreet manufacturing where consistent quantities of material are required over a roughly predictable list of materials obtained from combined BOM line items. MRP Systems also work well within process manufacturing operations where finished products are produced in bulk such as chemical batches, food-grade consumables, and other commodified bulk consumption goods. However, MRP systems can be successfully used within Make to Order (MTO), Assemble to Order (ATO) and Engineered to Order (ETO), provided that those production modes share a high proportion of common parts or sub-assemblies and have enough volume among the various iterations to build a consistent and dependable sales forecast.
MRP’s Impact on Purchase Planning
Purchase prompts, or “buy” suggestions, are key to MRP systems. The software driving an MRP system is designed to run calculations and notify planners and schedulers when it is time to purchase material. This is driven by demand, lead time and “on-hand” inventory and open purchase orders for materials in transit. Manual planning of modern manufacturing is extraordinarily difficult at minimum and in cases of complex multi-level BOMs, close to impossible. Using an MRP to drive informed purchasing decisions has several impacts:
- Improved Inventory Accuracy and Control – Today’s global supply chains can be complex mechanisms within themselves. For many manufacturers, it is common to source certain materials and components locally. These materials may have lower minimum purchasing requirements, shorter lead times and may benefit from the absence of customs clearance or tariffs. These “short-tailed” supply chain components can be purchased in small quantities near JIT status.
- Alongside these locally sourced components, that same manufacturer may require the purchase of materials from a distant source. Minimum purchase quantities may be required as well as longer lead times and higher “landed costs” for these “long-tailed” supply chain legs to bring the goods into the factory. As a result, manufacturers find themselves managing both “short-tailed” and “long-tailed” components of their supply chain and trying to balance the purchasing requirements for both. An MRP system can help by analyzing lead times and managing vendor purchase orders to suggest optimum buy strategies for each to smoothen the flow of materials.
- Optimized WIP Inventory – WIP can be a major drain on cash for any manufacturing company and a special concern for SMBs who cannot afford to tie up valuable cash flow on excess WIP. By calculating the requirements to forecast and balancing it against machine and labor factors required to complete orders, WIP can be optimized to include only that which is necessary to facilitate a consistent workflow. This frees up cash for other essential functions and allows for better planning overall.
- Lower Expediting Costs – Manually managed purchasing systems are inherently plagued by constant expediting, rush status and manual intervention in logistics and shipping. This drives up cost across the board in the form of expediting through extraordinary means to keep production moving smoothly. An MRP system that balances short and long-tail supply chain legs manage vendor purchase orders and calculates production based on the balance of these variables will eliminate expediting and its associated costs.
- Optimized Production Flow – An optimized workflow requires the right materials in the right place at the right time at the appropriate quantity. By utilizing the functionality of an MRP system, purchasing is no longer an overhead function, but a balanced value-added part of the system that helps drive an optimized workflow. That precision reduces waste, requires less handling and keeps production on schedule according to the forecast.
- Quality and Safety Stock – Modern manufacturing requires fast changeover and smaller lots to be competitive. In this mix, inevitably quality concerns will occur. As these concerns are addressed through design change mechanisms, an MRP can add clarity to a purchase plan to take historical quality failures into account as part of the system. This results in fewer shortages at “end-of-lot” production and therefore less “make-up” production for those shortages.
- Vendor Negotiation – The complexity of the modern supply chain requires tight management of vendor relationships. These relationships manifest themselves most often through long-term purchasing contracts to secure the best price and delivery terms to the manufacturer. MRP systems can accurately track vendor Pos, associated costs, landed cost calculation and other variables so that when contract negotiations are in order, decision-makers have the most accurate information available to allow them to negotiate favorable contracts.
MRP systems have changed a lot in the last decade. Today’s MRP systems are modular, customizable and cloud-based meaning SMBs have access to current system iterations at the same rate as larger manufacturers. They are also real-time and always-on. This increases the ability to purchase and produce goods at a competitive level on par with larger companies and allows them to control purchasing costs to produce what is needed, at the quantities that are needed and on schedule with delivery times to meet customer demand.