What Is Lot Tracking and How to Use It?
Lot tracking, also known as batch tracking, is an important process for ensuring quality, most commonly for traceability and recall purposes. It is a crucial part of doing business in highly regulated industries, but it has its advantages regardless of the product.
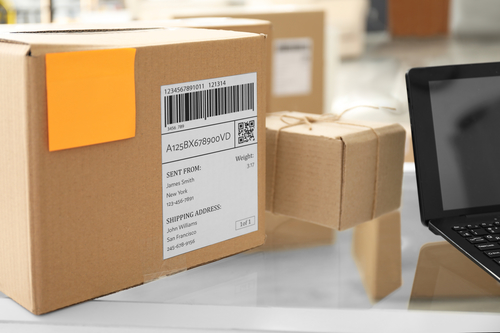
You can also listen to this article:
What is Lot Tracking?
Lot tracking is the act of recording the movements of stock lots. In inventory management, a stock lot is one batch of some Stock Keeping Unit. When a lot of goods arrives in a facility, or when a batch of products is manufactured, the lot is assigned a stock lot number that applies to every unit from that particular lot. This code can later be used to determine:
- the quantity, value, and location of the goods;
- which lot was used in the production of which products;
- which suppliers the materials or goods came from and when;
- which customers have received products related to this stock lot.
This process of recording and tracing the movement of goods and materials is the essence of lot tracking. Even though lot tracking is critical to companies that need to comply with strict regulations, it should be a part of any modern manufacturer’s or distributor’s business process and inventory optimization toolkit.
Benefits of Lot Tracking
Lot tracking is something that provides an array of benefits that can apply to any company regardless of their industry. These include:
- Getting organized. Lot tracking requires you to mark down each inventory movement so when consistently applied, you will have a real-time view of where your inventory items are, in which quantity, and how much they are worth. Knowing which materials or goods are used more, you can also optimize your inventory space as well as the resources allocated to different stock-keeping units.
- Ensuring quality. With proper traceability measures in place, a company is able to identify issues and trace them back to specific events, people, or materials. This allows businesses to detect inconsistencies on the suppliers’ side, find training gaps within their staff, diagnose machinery errors, etc. Finally, it allows them to correct the problems and drastically reduce the number of faulty goods ending up in the hands of customers.
- Tracking expiry dates. Lot tracking allows companies in industries that deal with perishable goods to keep an eye on the expiration dates of their materials or products. Utilizing the First In First Out (FIFO) or the First Expired First Out (FEFO) method along with lot tracking ensures that inventory waste is kept at a minimum.
- Achieving regulatory compliance. Lot tracking is a must in sectors such as food, pharmaceuticals, automotive, aviation, etc. where even the smallest inconsistency could be dangerous to human health and wellbeing. Having the documentation regarding the lifecycle of your lots available makes you always ready for an inspection.
- Easier product recalls. Product recalls are made much more efficient if you know exactly which customers received the faulty goods. This way you do not have to call back every one of the products you sold in the determined time frame, which could be very bad for customer satisfaction and business in general.
If you are having trouble with any one of the aspects mentioned above, you already have a good reason to implement a lot tracking system.
Lot Tracking Software
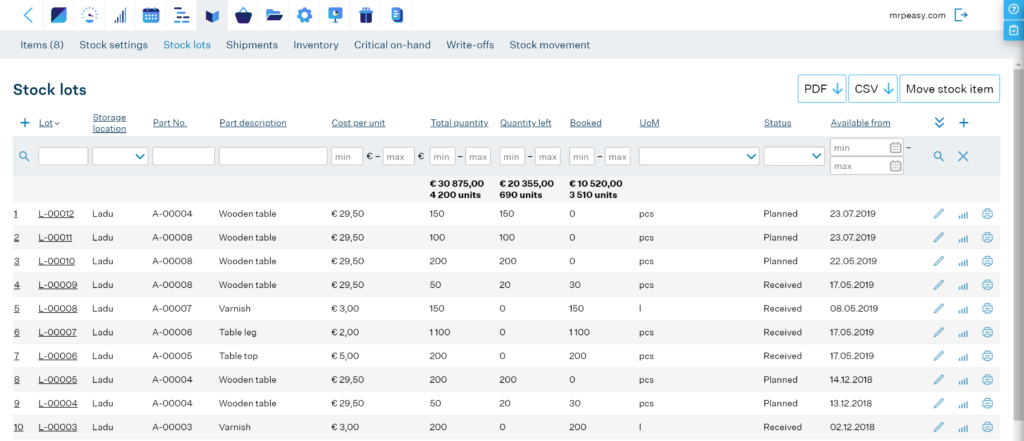
Having a lot tracking and traceability system is critical to companies that need to follow strong regulations and strict quality standards – generally in the food, pharmaceutical, electronics, aviation, defense, automotive and similar industries. But as seen above, all types of businesses can benefit from it.
There may be many different people involved with the handling of products and materials in various steps of the process. Usually, lot codes need to be recorded at each point of handling.
Using paper and pen or spreadsheets to do this can be very time-consuming and a sure recipe for disaster, since a small mistake in tracking can cascade into massive problems for the whole company.
An inventory management software that ties the various operations together into a single platform makes the whole lot tracking process mostly automated, usually thanks to the following abilities:
- Automated lot management, which is a core part of inventory and warehouse management.
- A single source of truth – the ability to follow lots through all of the different processes, from purchase receipt, use in production, warehouse movements, and sales to shipping.
- Automatically managing the usage of items according to FIFO or FEFO principles, which saves time, prevents confusion, and minimizes data entry errors.
The Lifecycle of a Lot
So, what does lot tracking look like within an ERP/MRP system?
- For example, when receiving goods, an inventory employee can simply print out an automatically generated, unique label to stick on the box of received items, which identifies the specific lot.
- Then, when the next handling operation takes place, e.g. moving items to the shop floor, the next worker only has to look at the ERP system to see what their task is, what materials they must pick, from which lot and storage location.
- When production is finished, the new, unique labels are stuck on the products and stored in the warehouse.
- Once products should be picked from the warehouse and shipped to the customer, the warehouse worker can again pick the products from stock according to the instructions from the ERP system.
- For double-checking, workers may even use barcode scanners to ensure they are handling the right items and get instant feedback from the system.
- If necessary, it is always possible to manually intervene and tell the software which lots were actually used, if for some reason the originally planned lots are not available for use.
Making a Product Recall
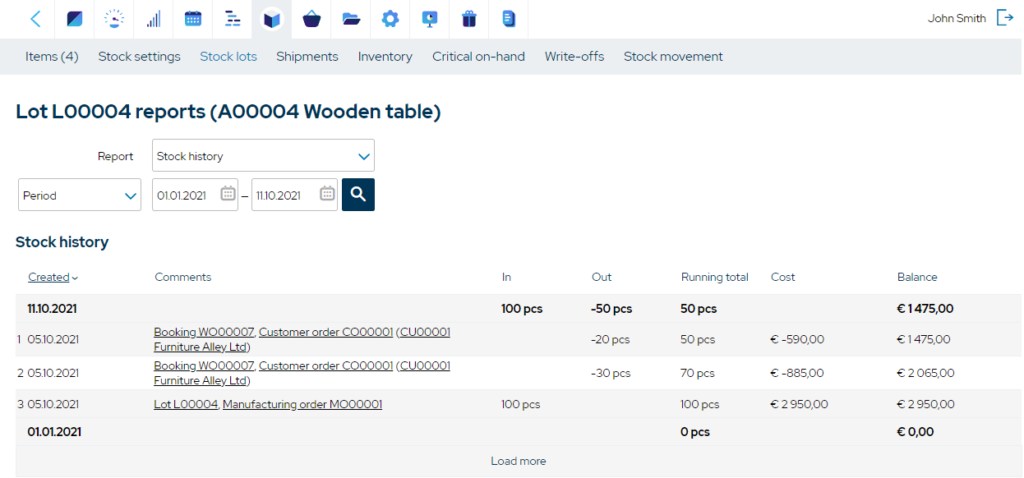
When you find out that there was a problem with a lot of materials, you can easily pull a report that tells you:
- Which lots of products were manufactured using these specific materials
- Which customers received the affected products
Or, if you later find out that there were issues in the production process, or you have found that there’s an issue with a specific lot of products, you can pull another report that tells you exactly which customers received those products.
Based on those reports, you can recall only those products that belong to the affected lot.
Also read about Return Merchandise Authorization – Managing Product Returns.
Investigating the Root Cause of a Defect
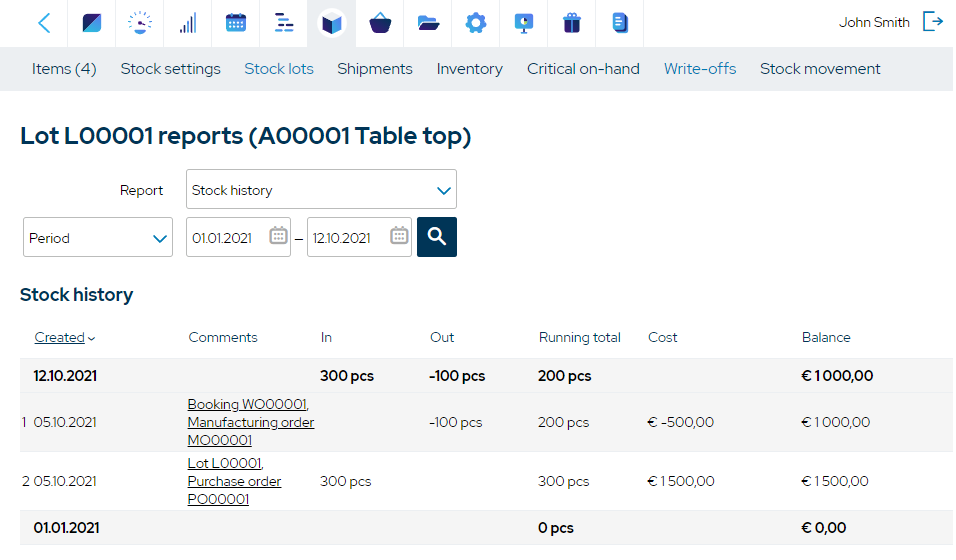
When a customer returned a defective product, you pull up the lot tracking report to see exactly when the production operations were performed, on which machines, who did it, which lots of materials were used, and all other relevant information.
This information can direct you to the root cause and possibly even identify other products that could be affected by the same issues.
Furthermore, if while inspecting the defective product you find a specific part that failed, it is easy to track down when and from which vendor it was purchased. Then, you can ask for a replacement and, at the same time, help your vendor identify issues in their production processes so they can improve their product quality and consistency.
Key takeaways
- Lot tracking means recording and tracing the movement of inventory by using lot numbers assigned to different shipments and batches of products.
- This presents companies with the opportunity to know which materials were used in which products, which suppliers the materials came from, which customers received the products, etc.
- Among other things, lot tracking helps with optimizing the business, ensuring quality, tracking expiry dates, achieving regulatory compliance, and organizing product recalls.
- Having a lot tracking and traceability system is critical first and foremost to companies that need to comply with strict regulations. Implementing traceability measures is, however, a good idea regardless of what the company sells.
- Manual lot tracking gets more difficult as a company grows, but an inventory management software that ties the various operations together into a single platform makes the whole lot tracking process mostly automated.
- An ERP system with strong lot tracking functionality also uses tools such as labeling and barcode scanners to make data entry easier for employees.
You may also like: What Is Batch Production and What Are Its Advantages?