How Manufacturing ERP Improves Team Communication
Every company communicates. But not every company communicates well or effectively. Often, it seems that communication within an organization can be repetitive, circular, or can lead to a dead-end while critical functions go unattended.
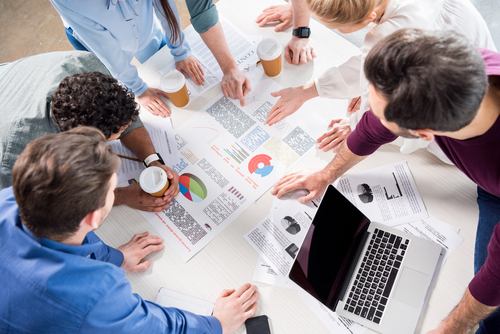
You can also listen to this article:
And while company culture plays a part in the quality of communication, it may also be a function of the system used in manufacturing that contributes to the disparity ineffective communication.
But how can a company operating system for manufacturing affect team communication? The answer is that it can do so in several ways.
- Many small to medium companies operate on patchwork or cobbled together systems that either overlap or produce a gap between functional areas. As a result, communication may not take place at critical times for equally critical processes.
- Because different areas of manufacturing utilize different software and systems to manage their tasks, data is often “siloed”. The use of spreadsheets, repetitive data entry and different units of measure from department to department can almost make it seem like the communication that does take place is being done using different “languages”.
- Data from department to department then is not always transferable in raw form and must be “translated”, or converted, for useful analysis, and then the procedure repeats as it moves to the next department.
- Employees on the team are often desensitized to communication. Having long communicated to no result, many may reduce communication further dragging down the manufacturing system. But the opposite may be true as well. They may also become desensitized by having to repeat the same information over and over. This repetition can lead to a missed opportunity for conveying critical information to other departments as they have become so unaccustomed to having to repeat themselves.
ERP to the Rescue
For companies experiencing situations like the one above, a manufacturing ERP system can have a huge impact on improving efficiency and cost in terms of a company’s operations. However, manufacturing ERP can also be used to improve team communication as well. Here are a few of the ways a manufacturing ERP can improve communication:
A Unified Database – One way an ERP system does this is by creating a single version of the truth. Data is unified in a single database that is not specific to executives, or scheduling, or purchasing or manufacturing. The data is standardized with a common unit of measures and is easily accessible. The unified database removes the need for different “languages” between departments and brings everyone under a common umbrella. As the data is standardized, the communication is streamlined to that which is relevant to the single database, eliminating the many different “languages” in the previous system.
All Inclusive – A second way that manufacturing ERP can improve communication is that everyone is included within the new system. Effective communication within an organization shouldn’t leave anyone out. As the data is standardized, each functional area can communicate more effectively. It is no longer a conversation between manufacturing and scheduling alone. Now, finance, inventory control, purchasing, supply chain and executives can see the system in action and understand their place and functionality within the system. By including all departments in its core functionality and calculations, a manufacturing ERP system can help everyone feel like part of a unified team working in the same direction. In this way, communication is made more effective.
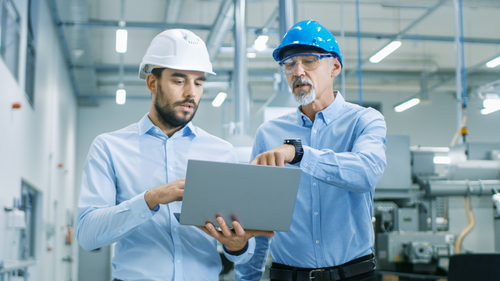
Higher Quality of Communication – A manufacturing ERP makes analysis and decision making easier and more effective. No one wants to believe that their communication is not being heard or that something must be repeated over and over to be heard. With manufacturing ERP systems, workflows are automated and, in most systems today, they are also modular, cloud-based and customizable. Many tasks that were previously performed manually, or that required interpreting for use within a department, are done automatically. This frees staff to make qualitative decisions based on the accurate and fast analysis provided by the system. With a common database and fewer repetitive tasks, analysis is faster, easier to understand and more inclusive. It motivates teams to communicate because they no longer feel the communication is not being heard nor do they feel that it must be stated over and over. This frees team members and allows for high-quality communication throughout the organization.
Empowered Employees – Today’s ERP systems are highly integrated and automated. Cloud-based systems can receive continuous updates and the system need not be hosted on a company server on site. These systems are also highly agile in that they can be customized to each company to streamline their effectiveness specifically for that company’s products and only for the functions it needs. Because of this, information is easily understood, repetitive tasks are reduced, and accuracy and efficiency are improved. And thanks to this, communication between team members is more valuable and is higher quality compared to the previous system. This empowers employees to continue communicating and to do so at a more productive level. And given the ease of use of most modern ERP systems, this improvement in communication can be achieved as part of the learning curve for the initial implementation. By adopting an easier and more intuitive platform, better and more simplified communication empowers staff to learn and further customize the system to deliver better results.
You may also like – How Manufacturing ERP Improves Quality in the Workplace
Doubling the Benefits of an ERP
An agile, cloud-based, modular ERP system can have a transformative effect on a small to medium-sized manufacturer. It can create an opportunity for large efficiency improvements, reduce operating and holding costs, assist in better planning for staffing and labour and improve quality. But those same benefits can motivate and empower a team to communicate better as well. Because their data is unified and inclusive, team members feel more comfortable relaying critical data, trends and ideas to managers because as they recognize that the quality of the operation has gone up, so too has the quality of communication and the ability to communicate clearly. This improvement affects a company’s culture, its bottom line and its competitiveness and improves the ROI on the ERP system as a whole.
You may find useful Top Six Manufacturing ERP Systems for Small Manufacturers.