¿Qué es el tiempo de rendimiento en la fabricación?
El tiempo de rendimiento es un KPI importante en la gestión de la fabricación, que ayuda a las empresas a mejorar los resultados tanto en el taller como en la cadena de suministro. Profundicemos en esta métrica.
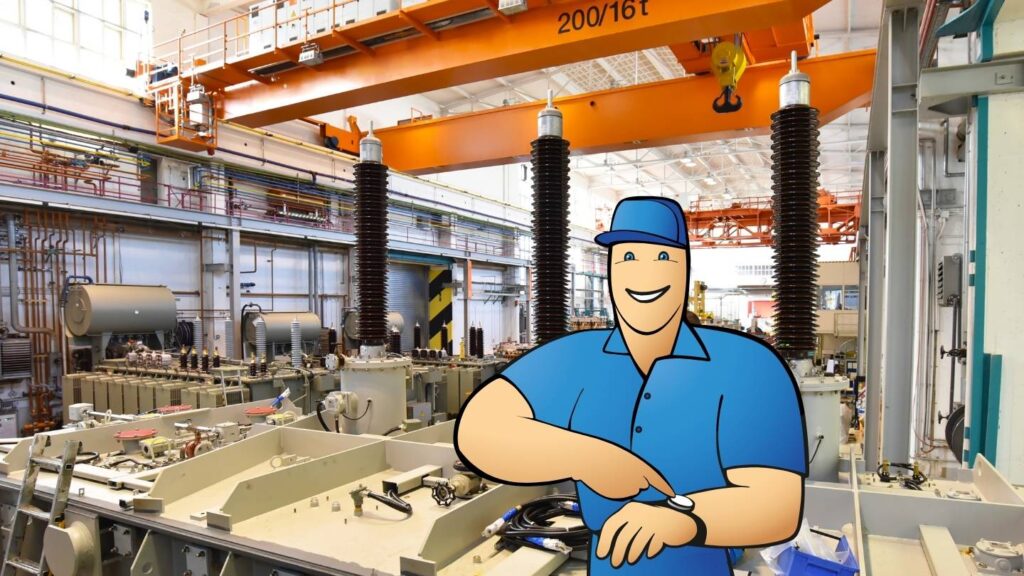
¿Qué es el tiempo de rendimiento?
El tiempo de rendimiento es el tiempo que se tarda en fabricar un producto de principio a fin. La medición del tiempo de rendimiento comienza con el traslado de las materias primas al taller y termina con una unidad o lote terminado listo para su envío. Como tal, es una métrica importante para evaluar la eficiencia de su producción y mejorar los flujos de trabajo en el taller, pero también es un aspecto clave de la planificación de la cadena de suministro, la previsión, la planificación de la capacidad y la programación de la producción.
Componentes del tiempo de rendimiento
Además del tiempo real que el producto pasa en la fase de procesamiento, el tiempo de rendimiento también incluye el tiempo de inspección, el tiempo de desplazamiento y el tiempo de espera. Veamos con más detalle estos cuatro componentes:
- Tiempo de procesamiento
- Tiempo de inspección
- Tiempo de desplazamiento
- Tiempo de espera
El cálculo del tiempo de rendimiento, por tanto, sigue la siguiente fórmula
Tiempo de rendimiento = Tiempo de procesamiento + Tiempo de inspección + Tiempo de desplazamiento + Tiempo de espera
Tiempo de rendimiento vs. tasa de rendimiento
Mientras que el tiempo de rendimiento mide el tiempo que tarda un producto en terminarse, la tasa de rendimiento se refiere al número de unidades terminadas en un periodo de tiempo determinado, normalmente por hora o por día.
Al igual que el tiempo de rendimiento, la tasa de rendimiento es una medida importante para evaluar la eficiencia de los procesos de fabricación. Una tasa de rendimiento más alta indica que el sistema de fabricación está funcionando a un nivel óptimo, produciendo más en un período determinado. Por el contrario, una tasa de rendimiento baja puede indicar cuellos de botella, ineficiencias o limitaciones de capacidad en el proceso de producción.
Para calcular la tasa de rendimiento, utilice la siguiente fórmula:
Tasa de rendimiento = Unidades terminadas / tiempo
Por ejemplo, supongamos que un equipo completa 40 dispositivos en un turno de 8 horas. La tasa de rendimiento por hora en este caso sería:
Tasa de rendimiento = 40 / 8 = 5 unidades/hora
Tiempo de rendimiento vs. tiempo de ciclo vs. tiempo de entrega
El tiempo de rendimiento también se confunde a menudo con otras métricas basadas en el tiempo, especialmente el tiempo de ciclo y el tiempo de entrega. Veamos en qué se diferencian.
El tiempo de rendimiento es el tiempo total empleado en fabricar un producto, desde el traslado de los materiales al taller hasta la entrada en el almacén del producto terminado.
El tiempo de ciclo es el tiempo que una única estación de trabajo dedica a procesar una unidad o lote de mercancías. Cuando un proceso de fabricación consta de varios subprocesos, el tiempo de ciclo se mide por separado para cada uno de ellos. Por ejemplo, la fabricación de una mesa de madera puede constar de 1) ensamblaje y 2) acabado. Por lo tanto, la parte del tiempo de procesamiento del tiempo de rendimiento está formada por todos los tiempos de ciclo de la secuencia del proceso de producción.
Sin embargo, el tiempo de entrega puede tener distintos significados. El tiempo de entrega de un pedido, o tiempo de entrega al cliente, se mide desde la recepción del pedido de un cliente hasta la entrega final del pedido completo. Esto incluye la compra de las materias primas necesarias y el tiempo de transporte. El tiempo de producción es un concepto similar al tiempo de rendimiento, pero se mide desde la creación hasta la finalización de una orden de fabricación.
Ventajas del seguimiento del tiempo de rendimiento
El tiempo de rendimiento, un KPI de fabricación esencial, puede utilizarse para evaluar y mejorar diversos aspectos de sus operaciones.
Optimización de los procesos de producción Mediante el seguimiento del tiempo de rendimiento, las empresas pueden establecer puntos de referencia e identificar ineficiencias en el proceso de producción, como retrasos o cuellos de botella. Esto permite realizar ajustes, garantizando flujos de trabajo más fluidos y mejorando el rendimiento operativo general.
Mejorar de la rentabilidad La reducción del tiempo de rendimiento minimiza los costos de mano de obra y maquinaria, al tiempo que aumenta el rendimiento de la producción. Estos aumentos de eficiencia reducen los gastos operativos y mejoran los márgenes, lo que contribuye a mejorar la rentabilidad.
Alineación de la planificación de la producción con la demanda de los clientes Conocer el tiempo exacto de rendimiento permite a los fabricantes planificar programas de producción que satisfagan la demanda de los clientes sin excederse ni quedarse cortos en la producción. Así se garantiza la entrega a tiempo y se reducen los pedidos pendientes o el exceso de existencias.
Mejora de la planificación de la producción Disponer de datos precisos sobre el tiempo de rendimiento permite mejorar la programación y la asignación de recursos. Los planificadores de la producción pueden establecer objetivos realistas que equilibren la capacidad y la demanda, evitando sobrecargar o infrautilizar los recursos.
Reducción de los tiempos de inactividad Identificar las áreas en las que las máquinas o los trabajadores están inactivos ayuda a minimizar el tiempo de inactividad. Al abordar estos problemas, los fabricantes pueden mantener la línea de producción funcionando de forma constante y eficiente.
Apoyo a la gestión de inventarios El seguimiento del tiempo de rendimiento permite a los fabricantes reducir el inventario de trabajo en proceso (WIP) asegurándose de que los materiales y componentes se mueven rápidamente a través de la producción. Esto reduce los costos de almacenamiento y el riesgo de exceso de existencias u obsolescencia del inventario. Además, conocer su tiempo de rendimiento permite a los fabricantes crear programas de producción más precisos y prever las necesidades de inventario para periodos específicos, lo que les permite evitar la falta y el exceso de existencias.
Se obtiene una ventaja competitiva Unos tiempos de producción y entrega más rápidos permiten a las empresas responder con mayor celeridad a las necesidades de los clientes y a las tendencias cambiantes del mercado, lo que les da una ventaja sobre sus competidores más lentos.
Mejora el retorno de la inversión en maquinaria y personal Al optimizar el tiempo de rendimiento, las empresas aprovechan mejor los recursos como la maquinaria, la mano de obra y los materiales. La eficiencia resultante mejora el retorno de la inversión en infraestructura de producción y personal.
Mejora de la calidad Los tiempos de rendimiento bien controlados mejoran la coherencia del proceso, lo que reduce al mínimo los defectos de fabricación y la necesidad de repeticiones, ahorrando tiempo y recursos.
Aumento de la satisfacción del cliente Unos procesos de producción más rápidos y predecibles hacen que los clientes reciban sus pedidos con prontitud, lo que aumenta su satisfacción y fomenta la fidelidad.
¿Cómo mejorar el tiempo de rendimiento?
Mejorar el tiempo de rendimiento es esencial para lograr una mayor eficacia operativa y optimizar todo el proceso empresarial. A continuación presentamos algunas formas de empezar a reducir los tiempos de rendimiento:
Reorganice físicamente sus instalaciones
Aunque las fábricas modernas se construyen con un flujo de producción optimizado para reducir los desplazamientos y las etapas de producción, muchas empresas utilizan edificios antiguos o espacios no diseñados específicamente para la fabricación. La clave está en organizar la distribución del espacio para facilitar un flujo más rápido de las mercancías desde el inventario a la producción y viceversa. Además, agrupar los procesos relacionados cerca unos de otros mejora el flujo y reduce los retrasos innecesarios.
Mejore la disponibilidad del inventario
Los retrasos suelen deberse a la falta de insumos o a que éstos llegan con retraso. Al reforzar la gestión de su cadena de suministro, los fabricantes pueden garantizar que las materias primas y los componentes estén disponibles cuando se necesiten, manteniendo la producción en marcha.
Implemente prácticas de mejora continua
Las prácticas de mejora continua, como Six Sigma y Lean Manufacturing, ayudan a identificar ineficiencias y eliminar residuos. Garantizan la optimización de los procesos de producción, el mantenimiento de la calidad y la reducción constante del tiempo de rendimiento.
Introduzca la automatización
Automatizar las tareas repetitivas acelera la producción y garantiza una calidad constante. La automatización permite a los fabricantes reducir los errores manuales y garantizar la entrega puntual del producto terminado.
Realice un mantenimiento regular
El mantenimiento preventivo garantiza el funcionamiento eficaz de las máquinas y evita averías inesperadas que interrumpen los procesos y aumentan el tiempo de producción.
Implemente la supervisión en tiempo real
La utilización de sistemas de datos en tiempo real, como un software ERP de fabricación, permite a los fabricantes realizar un seguimiento del progreso de la producción, identificar los cuellos de botella y abordar los retrasos de inmediato. Esto ayuda a mantener un flujo constante de materiales y garantiza transiciones más fluidas entre los procesos.
ERP para fabricación y tiempo de rendimiento
Aunque la mayoría de los sistemas ERP de fabricación no realizan un seguimiento directo del tiempo de rendimiento, sí son compatibles con varios procesos asociados a él. Al integrar funciones clave como la planificación de la producción, la gestión del inventario y la gestión del taller, los sistemas ERP ayudan indirectamente a controlar y reducir el tiempo de rendimiento. Aquí explicamos cómo:
- Programación optimizada de la producción. Los sistemas ERP de fabricación permiten planificar y programar la producción con precisión, equilibrando la capacidad y la demanda de los clientes. Esto minimiza los retrasos y reduce el tiempo de espera, garantizando un proceso de producción más fluido.
- Supervisión en tiempo real. Los sistemas ERP proporcionan actualizaciones en tiempo real sobre el progreso de la producción, lo que ayuda a los fabricantes a identificar y abordar rápidamente los cuellos de botella o los tiempos de inactividad. Esto garantiza flujos de trabajo coherentes y ciclos de producción más cortos.
- Mejor gestión del inventario. Al garantizar la disponibilidad puntual de materias primas y componentes, los sistemas ERP reducen los tiempos de espera y mantienen la producción en marcha sin problemas. Esto evita retrasos innecesarios en el tiempo de rendimiento.
- Mejor control de calidad. Los sistemas ERP de fabricación realizan un seguimiento de las métricas de calidad y ayudan a descubrir problemas que podrían provocar repeticiones o retrasos. Los procesos de control de calidad eficientes mantienen un tiempo de rendimiento constante al tiempo que garantizan que el producto final cumple las especificaciones.
- Procesos empresariales optimizados. Los sistemas ERP consolidan los flujos de trabajo y los datos, lo que permite a los fabricantes agilizar las operaciones. Al integrar múltiples funciones —compras, producción y entregas— los sistemas ERP reducen los errores manuales y mejoran la eficacia operativa general.
- Apoyo a las prácticas de mejora continua. Muchos sistemas ERP ofrecen herramientas para implementar las metodologías Lean y Six Sigma. Éstas ayudan a los fabricantes a analizar datos, identificar ineficiencias e implementar mejoras que reducen el tiempo de rendimiento.
Aunque es posible que los sistemas ERP no midan directamente el tiempo de rendimiento como métrica independiente, su capacidad para integrar y optimizar los procesos empresariales los convierte en una poderosa herramienta para mejorar el tiempo de rendimiento y lograr una mayor productividad.
Principales aspectos a tener en cuenta
- El tiempo de rendimiento es el tiempo total necesario para fabricar un producto, desde el traslado de las materias primas al taller hasta la creación de una unidad terminada. Es crucial para evaluar la eficiencia de la producción, mejorar los flujos de trabajo y optimizar la planificación de la cadena de suministro.
- El tiempo de rendimiento incluye cuatro componentes: tiempo de procesamiento (trabajo que añade valor), tiempo de inspección (control de calidad), tiempo de desplazamiento (transporte de mercancías) y tiempo de espera (espera debida a limitaciones o ineficiencias).
- El seguimiento del tiempo de rendimiento ayuda a optimizarlos flujos de trabajo, reducir el tiempo de inactividad, alinear la planificación de la producción con la demanda, minimizar los costos de inventario y mejorar la rentabilidad, el retorno de la inversión y la satisfacción del cliente.
- Las empresas pueden reducir el tiempo de rendimiento reorganizando los diseños de producción, garantizando la disponibilidad puntual del inventario, aplicando prácticas Lean y Six Sigma, automatizando tareas, manteniendo los equipos y utilizando herramientas de supervisión en tiempo real.
- Los sistemas ERP de fabricación mejoran indirectamente el tiempo de rendimiento optimizando la programación de la producción, gestionando el inventario, mejorando el control de calidad, racionalizando las operaciones y apoyando iniciativas de mejora continua como Lean y Six Sigma.
Preguntas frecuentes
Businesses can use manufacturing execution systems (MES) or ERP software with real-time monitoring capabilities. These tools provide data on individual process times, help identify delays, and allow for tracking key metrics directly from the shop floor.
Metrics like throughput rate, overall equipment effectiveness (OEE), and lead time can be used alongside throughput time. Comparing these metrics with industry standards or historical data for similar processes helps identify if improvements are needed.
Companies should perform a bottleneck analysis to identify which component has the most significant impact on total throughput time. Factors like frequency of delays, cost implications, and alignment with production goals will help prioritize improvement efforts effectively.
También le puede interesar: ¿Qué es un ciclo de producción y cómo optimizarlo?