¿Qué es el tiempo de inactividad? Explicación de los términos clave
El tiempo de inactividad no planificado es algo más que una pérdida de producción –es una carrera contrarreloj para evitar daños excesivos a una empresa. Este artículo analiza el tiempo de inactividad en la fabricación, las formas de mitigarlo y la diferencia crucial entre el tiempo de inactividad no planificado y el planificado.
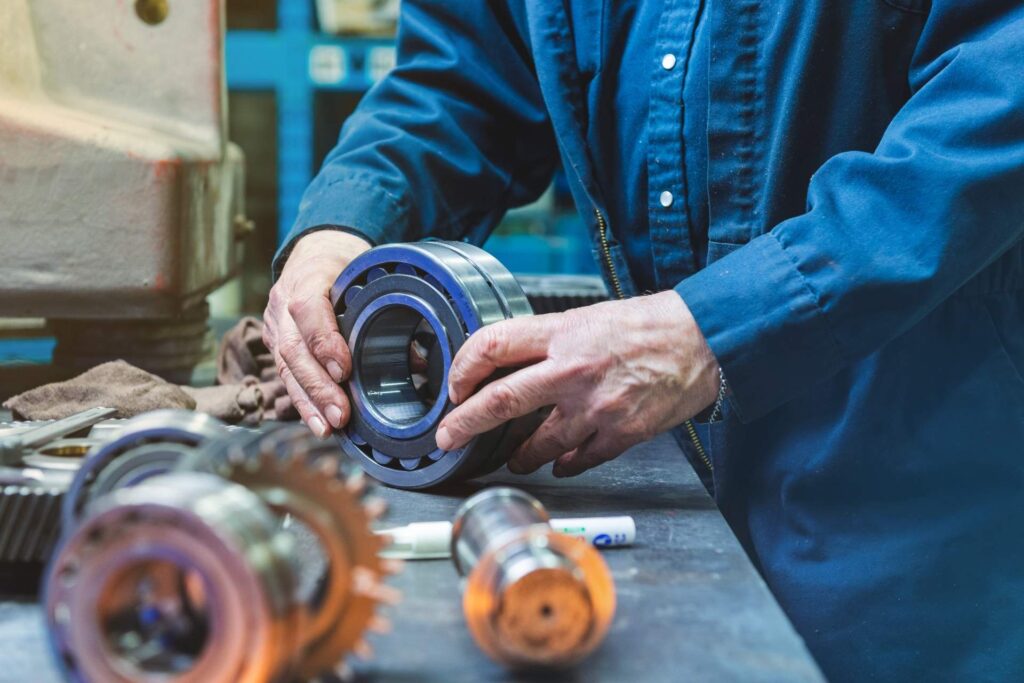
¿Qué es el tiempo de inactividad de la producción?
El tiempo de inactividad de la producción se refiere a cualquier periodo de tiempo durante el cual se detiene un proceso de fabricación, causando una interrupción en el flujo normal de operaciones. El tiempo de inactividad puede deberse a muchas razones, desde fallos de los equipos o huelgas de los empleados hasta mantenimiento programado o interrupciones de la cadena de suministro. Sea cual sea la causa, el tiempo de inactividad dificulta el cumplimiento de los objetivos de producción, poniendo en peligro los índices de satisfacción del cliente y la rentabilidad.
En términos generales, los tiempos de inactividad pueden clasificarse en dos tipos: no planificado y planificado. El tiempo de inactividad no planificado es la interrupción inesperada y a menudo costosa de la producción causada por fallos de los equipos u otros problemas imprevistos. El tiempo de inactividad planificado, por el contrario, es una pausa proactiva e intencionada en la producción, programada para permitir el mantenimiento o las actualizaciones.
Veamos estos dos aspectos con más detalle.
El tiempo de inactividad no planificado es el costoso sonido del silencio
En pocas palabras, el tiempo de inactividad no planificado es cualquier interrupción inesperada o no programada de la producción que afecta o interrumpe el funcionamiento normal. Para un fabricante de tamaño pequeño o mediano (normalmente entre 10 y 200 empleados), los costos asociados a los tiempos de inactividad pueden llegar a ser muy elevados y afectar gravemente a los resultados de la empresa.
Los costos directos del tiempo de inactividad no planificado
Para una pequeña empresa, el costo promedio en tiempo de producción perdido oscila entre $1.000 y $3.000 por hora. Para las empresas medianas, de 50 a 200 empleados, ese costo se eleva a entre $4.000 y $10.000.
Teniendo en cuenta los costos directos potenciales del tiempo de inactividad de un fabricante de tamaño mediano, si se produce entre 20 y 30 veces al mes, el tiempo de inactividad puede suponer una asombrosa pérdida de ganancias de entre $80.000 y $300.000.
Además de los costos de reparación de la maquinaria, hay otros factores a tener en cuenta por la falla de la máquina. El mantenimiento y las reparaciones de emergencia suelen costar entre 3 y 5 veces más que el mantenimiento preventivo. Si las piezas no están en las estanterías de la sala de repuestos, hay que añadir el costo del envío urgente de repuestos.
Luego están los costos de mano de obra. Cada miembro del equipo de producción que no hace nada sigue ganando un salario por hora. Además, hay que recuperar la producción perdida, lo que a menudo conlleva horas extraordinarias. Las horas extraordinarias se cobran normalmente a 1,5 veces el salario por hora normal. En consecuencia, el costo laboral de cada artículo acaba de aumentar.
En resumen, los gastos por tiempos de inactividad no planificados pueden generar una factura enorme que afecte al costo por unidad de la empresa y contribuya a reducir la puntuación de OEE (eficacia general de los equipos).
Costos indirectos del tiempo de inactividad no planificado
En primer lugar, puede haber problemas de control de calidad durante un reinicio de la producción. Las reparaciones pueden haber modificado la alineación y otras mediciones utilizadas para un control preciso. A menudo, esto significa que las primeras piezas fabricadas o los primeros productos procesados no cumplen las especificaciones adecuadas o no están dentro de los parámetros aceptables.
Entonces estos se tiran a la pila de residuos.
La productividad de la fabricación también puede desviarse lo suficiente como para que se incumplan los plazos y se produzcan posibles sanciones. Esto plantea la posibilidad de insatisfacción de los clientes, cancelación de pedidos e incluso pérdida de contratos comerciales cruciales.
Las fallas imprevistas de los equipos cuestan mucho porque la “solución” inmediata es el mantenimiento reactivo. Es una reacción instintiva a un problema que no debería haberse producido.
Tras cualquier tiempo de inactividad no planificado importante, la dirección debe realizar un análisis de la causa raíz de la interrupción. Un análisis adecuado del tiempo de inactividad empezará a desenterrar las razones de cómo y por qué se produjo un fallo en el equipo. Todas las conclusiones deben documentarse, prestando especial atención a las causas y a su seguimiento por máquina.
De hecho, cada máquina debe tener un registro continuo en papel que haga un seguimiento de su eficiencia operativa y de producción. Un historial de tiempos de inactividad de cada máquina puede incluir los KPI (indicadores clave de rendimiento) que determinan si una máquina debe sustituirse en lugar de repararse constantemente.
La verdadera clave para evitar y reducir los tiempos de inactividad es adoptar un enfoque proactivo del mantenimiento de los equipos. Así se reducen los tiempos de inactividad imprevistos y se fomenta un proceso de fabricación ajustado.
El tiempo de inactividad planificado es el sonido de la eficiencia operativa
La otra cara de la moneda del mantenimiento de máquinas es el tiempo de inactividad planificado. A diferencia de los tiempos de inactividad no planificados y no programados, los tiempos de inactividad planificados se programan e incluso se presupuestan, y forman parte del proceso normal de fabricación.
Es un hecho de la vida industrial que cualquier máquina —incluso todas las máquinas— acabará mostrando signos de desgaste. Por ello, hay que planificar los tiempos de inactividad y realizar un mantenimiento proactivo.
Existen dos tipos principales de mantenimiento proactivo del tiempo de inactividad: el preventivo y el predictivo. Aunque comparten características similares, hay ciertos aspectos que los diferencian.
Sin embargo, el objetivo principal de cada uno de ellos es evitar los tiempos de inactividad no planificados y mantener las fábricas y plantas de procesamiento funcionando con una eficiencia operativa óptima. Este objetivo se consigue utilizando un programa de mantenimiento planificado y bien pensado.
Los software, la programación generada por ordenador e incluso la IA (inteligencia artificial) desempeñan un papel cada vez más importante en la gestión del mantenimiento.
El mantenimiento preventivo es crucial para eliminar las interrupciones de producción
Empecemos con un poco de historia del tiempo de inactividad.
Antes de los años 50, el mantenimiento en la fabricación era puramente reactivo, siguiendo el sencillo principio: “Si no está roto, no hay que arreglarlo”. Este planteamiento funcionaba porque la maquinaria era sencilla y la mayor parte del ensamblaje se hacía a mano.
La industria experimentó su primer gran cambio en 1901, cuando Ransom Olds introdujo la cadena de ensamblaje, en la que los trabajadores de estaciones fijas ensamblaban los autos a medida que se llevaban de una estación a otra. Como sabemos, Henry Ford revolucionó este concepto en 1913 con su sistema de cintas transportadoras, inspirado en las plantas de procesamiento de carne. Los trabajadores se especializaban en una sola tarea, con lo que mejoraba espectacularmente la eficiencia, aunque el mantenimiento seguía siendo reactivo.
El auge de la fabricación en la posguerra de los años 50 transformó definitivamente la filosofía del mantenimiento. A medida que la maquinaria de producción se hacía más compleja, surgió el mantenimiento preventivo para reducir los fallos de los equipos y los tiempos de inactividad no planificados. La industria pasó del “no lo arregles si no está roto” al “arréglalo antes de que se rompa”, sentando las bases de las prácticas modernas de mantenimiento.
Esto marcó el comienzo del concepto de mantenimiento preventivo.
El tiempo de inactividad planificado para el mantenimiento preventivo se incluyó en el programa de producción. De hecho, el software de planificación de recursos de fabricación (MRP) pronto incorporó el mantenimiento planificado al desarrollo general del programa, incluido el mantenimiento de un inventario de piezas.
Los periodos de inactividad programados suelen utilizarse para cambiar y actualizar los equipos.
Una parte importante del mantenimiento preventivo es el concepto de MTBF o “tiempo medio entre fallos”. Este concepto se aplicó a todo tipo de piezas de los equipos, sobre todo a las que permitían el movimiento (rodamientos, engranajes y piezas similares) y, con el tiempo, a las piezas eléctricas y electrónicas que tenían una vida útil o esperanza de vida limitada.
Así pues, uno de los principales objetivos del mantenimiento preventivo es sustituir las piezas con un valor MTBF antes de que se dañen. Esto significa que las sustituciones o incluso las revisiones completas de las máquinas se planificaban para los periodos en los que la producción no estaba en marcha. Los fines de semana, las vacaciones y un turno diario dedicado al mantenimiento permitían completar las tareas de mantenimiento preventivo.
¿El resultado? Los tiempos de inactividad no planificados disminuyeron significativamente.
Pero muchas estrategias de mantenimiento preventivo tienen su truco. Las piezas se sustituyen antes de que fallen… a veces mucho antes de que esto ocurra. Mientras que esperar a que una pieza se estropee significa sacarle todo el partido posible, las reparaciones preventivas suponen dejar dinero sobre la mesa por piezas retiradas demasiado pronto.
Sin embargo, en la gran mayoría de los casos, el dinero perdido por sustituir antes de que se produjera el fallo se compensaba con creces al no perder dinero en tiempos de inactividad no planificados.
Es un sacrificio, sí. Pero generalmente vale la pena.
Mantenimiento predictivo —reparaciones “justo a tiempo” y seguimiento del tiempo de inactividad
El mantenimiento predictivo —desarrollado durante la década de 1990 y principios de la de 2000— utiliza una metodología más basada en datos para programar las reparaciones de mantenimiento, lo que reduce aún más los tiempos de inactividad no planificados. Utiliza el análisis predictivo para ayudar a eliminar los tiempos de inactividad inesperados de las máquinas y, de hecho, reduce el costo de los tiempos de inactividad al permitir que el trabajo se realice de forma más eficiente.
Mientras que el mantenimiento preventivo era básicamente una suposición, el mantenimiento predictivo utiliza un conjunto totalmente nuevo de parámetros, técnicas y tecnologías. El mantenimiento predictivo puede supervisar los equipos de fabricación en tiempo real o con la mayor precisión posible.
Por ejemplo, una de las principales causas de las piezas móviles soportadas por rodamientos era y sigue siendo el calor. Lo mismo ocurre con los componentes eléctricos y electrónicos. Una importante tecnología desarrollada, que he utilizado mucho a lo largo de mis 36 años de carrera como mecánico industrial, es la imagen térmica, también llamada termografía.
FLIR es el acrónimo de Forward Looking Infrared (cámara térmica infrarroja). Cuando se apunta el dispositivo hacia un objeto, éste detecta el calor y crea una imagen codificada por colores en una pantalla de visualización. Los distintos colores indican la temperatura del objeto o parte de ella, normalmente en comparación con la temperatura ambiente.
Si conoce la temperatura normal de funcionamiento del componente, puede ver si está empezando a sobrecalentarse, lo que indica un fallo inminente. A continuación, se puede programar la sustitución o reparación del componente en el momento oportuno… justo a tiempo (lo que a menudo se denomina JIT).
Mantenimiento predictivo avanzado en el siglo XXI
Hoy en día, estamos en la era de la Industria 4.0+, y un nuevo conjunto de tecnologías de mantenimiento predictivo están disponibles para mejorar las operaciones de fabricación. Los sensores especializados se fijan a los componentes de la máquina y permanecen en su lugar como guardianes 24/7, listos para advertir de fallos inminentes por problemas potenciales.
Estos sensores suelen conectarse a la red de la instalación o a la nube de mantenimiento, introduciendo datos directamente en el software de seguimiento y programación del mantenimiento a través de conexiones IoT (Internet de las cosas). Cada pieza del equipo puede ser rastreada en tiempo real, comparando su rendimiento con un conjunto de métricas y parámetros operativos definidos.
La IA unida al Machine Learning facilita la programación inteligente del mantenimiento, impulsando un sistema informático de gestión del mantenimiento o GMAO.
Esto prácticamente elimina el error humano en el mantenimiento predictivo. Además, cuando los equipos de mantenimiento son capaces de realizar un mantenimiento predictivo, la OEE mejora aún más. Y eso significa que se minimiza el tiempo de inactividad debido a fallos de los equipos que causan pérdidas de producción.
Sin embargo, no todos los tiempos de inactividad imprevistos se deben a paradas de los equipos.
Usted no puede eliminar todos los tiempos de inactividad no planificados
Pero puede reducirlos.
A lo largo de mis más de 35 años en la industria de la fabricación, he sido testigo de todo tipo de interrupciones imaginables en la producción. Desde pequeños contratiempos en las máquinas hasta paros devastadores en toda la planta, estas interrupciones son una realidad constante para las empresas de fabricación.
A continuación se indican otras causas comunes de los tiempos de inactividad en la industria de la fabricación.
Escasez de materias primas
La escasez interrumpe la producción, aumenta los costos por los pedidos urgentes y perjudica las relaciones con los clientes por el incumplimiento de los plazos. Estas interrupciones se extienden por toda la cadena de suministro y plantean complejos retos a la gestión de inventarios que afectan a toda la operación.
La tecnología moderna ofrece soluciones eficaces mediante sistemas de seguimiento de inventarios en tiempo real y análisis avanzados para mejorar las previsiones. El software de gestión de la cadena de suministro (SCM), integrado con los sistemas de planificación de recursos empresariales (ERP), permite un seguimiento y una gestión exhaustivos de las existencias.
El software de lista de materiales (BOM) refuerza aún más el control del inventario mediante puntos de pedido automatizados, integración de RFID y cálculos precisos de materiales basados en las demandas de producción.
El éxito en la prevención de la escasez de materiales requiere combinar estas herramientas tecnológicas con una planificación estratégica, que incluya el mantenimiento de relaciones con múltiples proveedores y el desarrollo de planes de contingencia claros. Este enfoque integrado ayuda a los fabricantes a mantener una producción constante al tiempo que se minimizan los riesgos de interrupción.
Cortes de electricidad
Los cortes de electricidad suponen un riesgo constante para las fábricas. Pueden producirse por fallos de la compañía eléctrica, problemas eléctricos o catástrofes naturales. Las consecuencias son inmediatas y graves. Las líneas de producción se detienen. Los equipos sensibles pueden sufrir daños. Los objetivos de producción y los plazos se esfuman.
Los fabricantes necesitan una defensa de varios niveles contra estos riesgos:
- Empiece con una infraestructura sólida.
- Instale generadores de reserva y sistemas de alimentación ininterrumpida (SAI).
- Realice pruebas periódicas del banco de carga para verificar la fiabilidad del sistema.
- Desarrolle protocolos claros de interrupción del suministro eléctrico.
- Considere la posibilidad de contratar líneas eléctricas adicionales para una mayor protección.
Los sistemas de supervisión modernos proporcionan otra capa de protección fundamental. Instale herramientas de supervisión analógicas y digitales basadas en software. Éstas controlan el acondicionamiento de la energía y la gestión de la carga. Pueden proporcionar alertas tempranas antes de que los problemas se agraven. Los sistemas de iluminación industrial de alto rendimiento ofrecen una capacidad de reacción adicional.
Juntas, estas soluciones ayudan a los fabricantes a mantener la continuidad durante las interrupciones del suministro eléctrico.
Error humano
Probablemente el más difícil de mitigar, el error humano amenaza a diario el éxito de la fabricación. Estos errores van desde el funcionamiento incorrecto de las máquinas hasta descuidos en el mantenimiento. También pueden incluir errores en los procesos de producción. Las consecuencias son importantes. Las líneas de producción sufren retrasos o interrupciones. Aumentan los problemas de calidad y los residuos. Surgen riesgos de seguridad. Disminuyen la productividad y la eficacia generales.
A continuación presentamos algunos consejos para ayudar a mitigar los errores humanos:
- Desarrolle sistemas de comunicación claros e inequívocos que refuercen todo el flujo de trabajo.
- Implemente programas de capacitación completos utilizando instrucciones de trabajo digitales. Las plataformas digitales de formación ayudan a aumentar la coherencia en la educación de los empleados.
- Instale ayudas visuales en varios idiomas cuando sea necesario.
- Elabore y mantenga procedimientos de trabajo estandarizados (SOP) detallados.
- Las estrictas medidas de rendición de cuentas y las evaluaciones periódicas de las competencias proporcionan otros niveles de protección.
Estas herramientas y procesos ayudan a los fabricantes a mantener la calidad al tiempo que protegen a su mano de obra.
Tiempo de inactividad de producción planificado vs. no planificado —es su elección
Los tiempos de inactividad de la producción no planificados existen como mantenimiento reactivo o interrupciones costosas. Los tiempos de inactividad planificados permiten el mantenimiento de los equipos y la mejora de los procesos e inspeccionar a fondo los equipos, realizar actualizaciones críticas y optimizar los procesos.
El mantenimiento regular prolonga la vida útil de la máquina y evita fallos futuros. Le ahorra horas de inactividad que merman los resultados de su empresa. En cambio, los tiempos de inactividad no planificados interrumpen la producción y cuestan miles de dólares por hora.
El software de planificación de recursos de fabricación ayuda a maximizar el tiempo de inactividad programado para el mantenimiento, al tiempo que evita interrupciones inesperadas. Esto impulsa la eficiencia, reduce los costos y garantiza una producción fiable. La planificación estratégica del mantenimiento conduce a una mayor productividad, un mejor control de la calidad y un importante ahorro a largo plazo.
Principales aspectos a tener en cuenta
- El tiempo de inactividad de la producción es una interrupción de los procesos de fabricación que puede deberse a fallos de los equipos, problemas de mantenimiento, problemas en la cadena de suministro, etc.
- Los tiempos de inactividad no planificados son costosos y perjudiciales. Ocurren de forma inesperada y provocan elevados gastos de reparación, pérdida de productividad e incumplimiento de plazos.
- El tiempo de inactividad planificado es un enfoque proactivo de la eficiencia. Se programa para permitir el mantenimiento y las actualizaciones, reduciendo el riesgo de interrupciones inesperadas de la producción.
- El mantenimiento preventivo reduce los tiempos de inactividad no planificados. Al sustituir piezas y revisar los equipos antes de que fallen, se prolonga la vida útil de las máquinas y se reduce el riesgo de interrupciones.
- El mantenimiento predictivo utiliza modernas tecnologías basadas en datos para optimizar las reparaciones. La supervisión y el análisis en tiempo real ayudan a detectar problemas con antelación, garantizando un mantenimiento puntual y eficiente.
- Entre los retos que plantea la planificación de los tiempos de inactividad figuran la escasez de recursos y los errores humanos. La programación eficaz, la capacitación adecuada y la integración de soluciones tecnológicas modernas son cruciales para superar estos obstáculos.
Preguntas frecuentes
El tiempo de inactividad de la producción se refiere a cualquier periodo durante el cual se detienen las operaciones de fabricación. Puede deberse a acontecimientos no planeados, como fallas en los equipos, o a actividades planificadas, como mantenimiento o actualizaciones. El tiempo de inactividad afecta a la productividad, la satisfacción del cliente y la rentabilidad, por lo que es un factor crítico en la eficiencia de la fabricación.
Sí, el tiempo de inactividad es un indicador clave del rendimiento (KPI) en la fabricación. A menudo se utiliza para medir la eficacia general de los equipos (OEE) y evaluar la eficiencia operativa. Supervisar el tiempo de inactividad ayuda a identificar las áreas problemáticas y a aplicar estrategias para reducir las interrupciones.
Para calcular el tiempo de inactividad de la producción, registre la duración total de las operaciones detenidas durante un periodo concreto. Divídalo por el tiempo total de producción disponible y multiplíquelo por 100 para expresarlo en porcentaje. Esta métrica ayuda a los fabricantes a evaluar la eficiencia de sus procesos e identificar oportunidades de mejora.
También le puede interesar: ¿Qué es el inventario obsoleto y cómo evitarlo?