Sistema Push vs. sistema Pull en la gestión de la fabricación
Los sistemas push y pull son estrategias de gestión de la cadena de suministro que se utilizan en función de la incertidumbre de la demanda de un producto. Aunque push y pull son enfoques muy diferentes, muchas empresas adoptan también una estrategia híbrida push-pull.
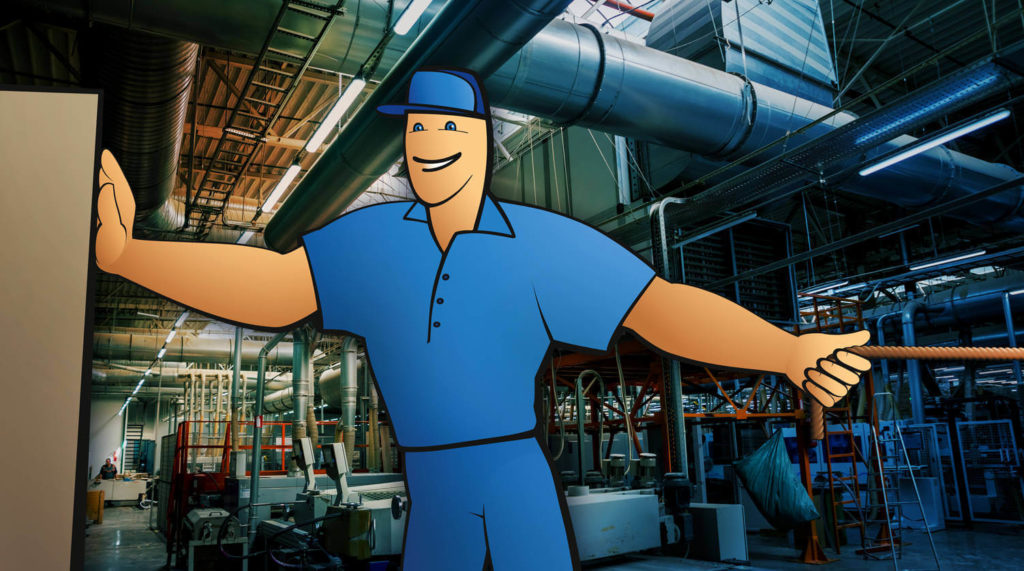
¿Qué es un sistema Push?
En la fabricación, un sistema push significa que una empresa produce bienes según una previsión de la demanda. También se denomina fabricación contra stock y suele utilizarse para producir bienes que tienen pocas posibilidades de sufrir fluctuaciones imprevisibles de la demanda, por ejemplo, alimentos, productos farmacéuticos, productos químicos domésticos, dispositivos electrónicos, etc.
Un sistema push, por tanto, pone en marcha la producción para anticiparse a la demanda futura que se ha estimado según los datos históricos. En este sistema de cadena de suministro, las mercancías son “empujadas” a través de la cadena de suministro, con la previsión de la demanda que desencadena la producción, y con el envío de los productos terminados a los distribuidores o minoristas que luego comercializarán los productos y esperarán a que los clientes realicen la compra.
Un buen ejemplo de uso de un sistema push sería una panadería en la que la decisión sobre qué productos y qué cantidades hornear se hace en función de la cantidad que se espera vender. Como la gente no está dispuesta a esperar una hora por su panecillo matutino después de hacer un pedido, se utiliza un sistema push.
¿Qué es un sistema Pull?
El sistema pull es una estrategia de fabricación ajustada en la que los bienes se producen en función de la demanda real y no de las previsiones. En este tipo de sistema, las empresas sólo mantienen el inventario y producen lo necesario para responder a los pedidos de los clientes existentes.
En un sistema “pull”, las mercancías se “jalan” a través de la cadena de suministro, con un pedido del cliente que desencadena una secuencia de eventos en los que se fabrica la cantidad necesaria de productos y se reponen las materias primas utilizadas en la producción de dichos productos.
Un gran ejemplo de sistema pull es la fabricación justo a tiempo. La idea central del JIT es programar el proceso de manera que los materiales lleguen a las instalaciones exactamente cuando se programe el inicio de la producción, y la producción se programe de manera que se termine justo cuando la mercancía deba despacharse al cliente.
Otro enfoque popular de los sistemas pull es el Kanban. Los Kanbans son señales visuales que activan los movimientos de producción e inventario. Por ejemplo, cuando un artículo tiene un Kanban adjunto y llega al final de la cadena de suministro, es decir, al cliente, el Kanban se envía de vuelta al inicio de la cadena de suministro, desencadenando otro ciclo de producción. Otro enfoque sencillo de Kanban es el sistema de dos contenedores, en el que se mantienen dos contenedores de un producto en el punto de consumo o de venta. Cuando uno de los contenedores se vacía, se envía de vuelta como señal para activar la producción, de modo que el contenedor pueda llenarse de nuevo.
Sistema Push vs. sistema Pull
La principal diferencia entre los sistemas “push” y “pull” es que en un sistema “push”, la producción dicta la cantidad de producto que llegará al mercado, mientras que en un sistema “pull”, la demanda actual dicta la cantidad a producir. Este factor clave de lo que
Inventario WIP
Una de las principales diferencias entre los sistemas “push” y “pull” es la cantidad de inventario WIP permitido. En un sistema push, no hay un límite definido para el inventario WIP porque no hay señales que lleguen a la planta de producción. Sin embargo, en un sistema pull, el propio sistema regula la cantidad de WIP.
Concretamente, el límite de WIP se alcanza cuando no hay productos que puedan venderse o consumirse, es decir, no habrá ninguna señal que desencadene otra reposición. Esto significa que al menos una unidad de producto en WIP debe ser terminada y vendida antes de que pueda haber otra señal de reabastecimiento.
Costes de inventario
Como el sistema push se basa en las previsiones para determinar el volumen de producción, y las previsiones casi nunca son 100% exactas, podría dar lugar a mercancías no vendidas que, en el mejor de los casos, ocuparían recursos de gestión de inventario y espacio de almacenamiento. En el peor de los casos, sin embargo, la mercancía no vendida podría acabar convirtiéndose en stock muerto. En cualquier caso, los costes de inventario serían más elevados de lo necesario.
Sin embargo, un sistema pull sólo produce lo que los clientes han pedido. De este modo, el inventario se mantiene al mínimo en todo momento, ya que los productos acabados se entregan rápidamente a los clientes, los inventarios de materias primas se reponen según sea necesario y el WIP es limitado. Sin embargo, un inventario mínimo significa menos espacio y mano de obra desperdiciada en el almacenamiento y la manipulación de los productos, lo que a su vez significa menores costes de inventario.
Disponibilidad del producto
El objetivo de un sistema push es asegurar un nivel de servicio que garantice la disponibilidad del producto en todo momento. Mientras que un sistema pull reacciona a los pedidos de los clientes, un sistema push se anticipa a ellos y se asegura de que los clientes reciban la mercancía en la cantidad requerida lo antes posible. Esto es especialmente importante en sectores del mercado en los que los plazos de entrega desempeñan un papel importante en los procesos de toma de decisiones de los clientes.
Personalización del producto
Cuando una empresa ofrece a sus clientes opciones de personalización, la mayoría de las veces haría bien en implementar algunas características de un sistema pull en su proceso de producción. De lo contrario, tendría que crear muchas variantes diferentes en el stock, complicando sus procesos de fabricación y ampliando su inventario y los costes asociados en el proceso.
Sin embargo, con un sistema pull, los fabricantes de productos personalizables pueden mantener su inventario al mínimo. En el caso de la personalización masiva, puede aplicarse con éxito una versión híbrida de los dos sistemas. Por ejemplo, un fabricante puede utilizar la estrategia push para abastecerse de productos base sin personalización y luego introducir un elemento pull al final del proceso de producción, en el que la personalización final es provocada por un pedido del cliente. Esto se denomina sistema push-pull.
Sistema push-pull
Los sistemas “push” y “pull” pueden funcionar bien juntos, aportando las ventajas de ambos sistemas. En este caso, los fabricantes utilizan la previsión de la demanda para determinar la cantidad de bienes que se utilizarán como inventario base, pero utilizan los pedidos de los clientes para activar la producción posterior.
Supongamos que un fabricante de muebles de madera de alta gama sabe que vende tres mesas a la semana de media, pero también ha habido semanas en las que los clientes han comprado seis o siete. Como una mesa les lleva un día y medio de trabajo, podrían responder a su demanda media semana a semana sin tener existencias adicionales. Sin embargo, para responder a los picos de demanda, necesitan tener un stock de seguridad. En este caso, el sistema push crea un excedente de mesas que se espera vender, y el sistema pull repone el stock de seguridad cuando los artículos se venden.
Otro ejemplo de sistema push-pull sería cuando un fabricante se abastece de materias primas (sistema push) pero las utiliza en la producción sólo cuando llega un pedido (sistema pull). Lo mismo ocurre con el caso antes mencionado en el que la empresa ofrece opciones de personalización.
Push, Pull y MRP
Aunque la planificación de necesidades de material tradicional (MRP I) puede considerarse un sistema push que actúa en función de un programa maestro de producción basado en previsiones, los sistemas actuales de planificación de recursos de fabricación (MRP II) también pueden complementar los sistemas pull.
Dado que la capacidad de integración de datos de los modernos sistemas de software basados en la nube sienta las bases para la gestión en tiempo real de todos los aspectos de la empresa, los modernos sistemas MRP pueden comprobar la disponibilidad de materiales y programar tanto la producción como las compras en cuanto se recibe un pedido del cliente. El consumo de artículos de stock se refleja en el sistema, se hace un seguimiento de las actividades de producción y del inventario WIP. Por tanto, las señales visuales de un sistema Kanban sólo se transforman en señales digitales, y el software dicta el flujo de información.
Esto significa que los modernos sistemas ERP/MRP pueden utilizarse como herramienta de gestión empresarial tanto en sistemas push como pull, así como en el sistema híbrido push-pull.
Principales aspectos a tener en cuenta
- Un sistema “push” (también llamado “make-to-stock”) significa que una empresa produce bienes en función de una previsión de la demanda. Suele utilizarse para producir bienes con escasa probabilidad de fluctuaciones imprevisibles de la demanda, por ejemplo, alimentos, productos farmacéuticos, productos químicos domésticos, etc.
- El sistema pull es una estrategia de fabricación ajustada en la que los bienes se producen en función de la demanda real y no de las previsiones. En este tipo de sistema, las empresas sólo mantienen el inventario y producen lo necesario para responder a los pedidos de los clientes existentes.
- La principal diferencia entre los sistemas “push” y “pull” es que en un sistema “push”, la producción dicta la cantidad de producto que se “empujará” al mercado, mientras que en un sistema “pull”, la demanda actual “tira” de los bienes, es decir, dicta cuándo y cuánto producir.
- Lo que también diferencia a los sistemas push y pull es la cantidad de inventario WIP permitido, los costes de inventario, la disponibilidad de los productos y la posibilidad de personalizarlos.
- El push y el pull también pueden funcionar juntos en un sistema híbrido push-pull en el que se utilizan tanto las previsiones de la demanda como los pedidos actuales para activar el movimiento de mercancías en varios puntos de la cadena de suministro.
- Aunque el MRP tradicional (planificación de necesidades de material) puede considerarse un sistema push, el MRP moderno (planificación de recursos de fabricación) puede utilizarse como herramienta de gestión de operaciones tanto en sistemas push como pull.
También le puede interesar: Costos de inventario – Una rápida visión de conjunto