Planificación de capacidad – Una guía esencial para los fabricantes
La planificación de capacidad es una herramienta esencial que se utiliza en las empresas manufactureras que funcionan bien. Determina la capacidad necesaria para satisfacer la demanda y, como tal, es un requisito previo para la programación eficiente de la producción, la planificación de la cadena de suministro, la gestión de inventarios y cualquier otro aspecto de la empresa.
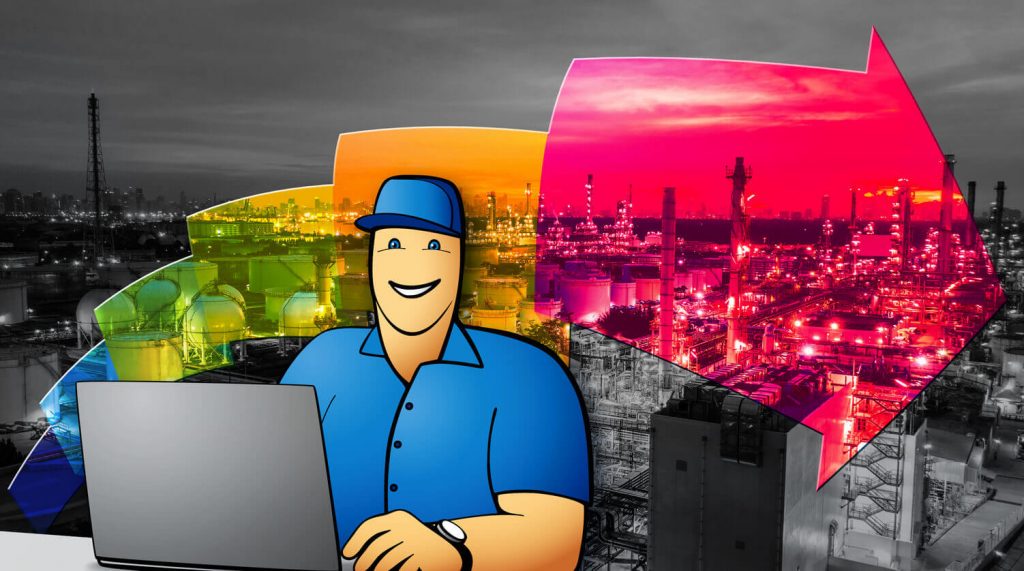
¿Qué es la planificación de capacidad?
El ámbito de la fabricación actual es muy complejo, con productos que van desde los productos básicos hasta los artículos de alta gama fabricados por encargo. Independientemente del producto, es importante una planificación adecuada en todas las etapas. Esto incluye la planificación de la cadena de suministro, la programación de la producción y la planificación de la demanda para que el fabricante sepa qué bienes producir y con qué frecuencia.
Pero hay otra área en la que la planificación es igual de crucial para cumplir los objetivos de producción. Esta área influye en los costes, la eficiencia y la rentabilidad tanto como las demás, y no tenerla en cuenta y planificarla adecuadamente es peligroso. Este tipo de planificación se denomina planificación de las necesidades de capacidad (PRC). La planificación de capacidad es un proceso que determina la capacidad de producción necesaria para satisfacer la demanda de fabricación. Como tiene en cuenta la capacidad de producción finita, la planificación de capacidad está vinculada a la planificación de la cadena de suministro, la gestión de inventarios, el mantenimiento, la programación y a todos los demás aspectos de la operación.
La planificación de capacidad tiene en cuenta el número de máquinas, el tamaño de la base de empleados necesarios para operar esas máquinas, las horas o turnos disponibles, la mezcla de productos que se van a fabricar, la utilización de los equipos y la eficiencia general. Estos factores se calculan para que una operación sepa si tiene la capacidad necesaria para cumplir la previsión demandada. Si el plan de capacidad es correcto, los directivos pueden añadir o restar recursos de forma proactiva para cumplir los compromisos.
Impacto de la planificación de capacidad en los costes presupuestarios clave
La planificación de capacidad influye en muchos costes de una empresa. Y es importante que una empresa no sólo comprenda esos costes, sino que utilice esa comprensión para aceptar las limitaciones y determinar un camino que le permita cumplir los objetivos de servicio. Esto puede incluir turnos extra, horas extras, aumento de la compra de capex, subcontratación de trabajo y muchas otras tácticas que les permitan mantenerse a la vanguardia.
La planificación de capacidad afecta a las áreas de costes, entre ellas:
- Costes de explotación – Si la demanda de productos no está sincronizada con la capacidad, una empresa puede verse en la necesidad de programar horas extras o añadir turnos. Del mismo modo, podría significar que necesitan reducir la mano de obra y omitir las instalaciones rápidamente. Un cálculo erróneo de cualquiera de las dos cosas puede elevar los costes operativos y aumentar el coste por unidad.
- Costes fijos – Si no se conoce la capacidad, elementos como los costes de almacenamiento pueden afectar a la línea de costes fijos. Esto puede ser el resultado de un exceso de espacio en el almacén que puede no ser necesario. Dado que este tipo de acuerdos se manejan a menudo con espacio y equipos alquilados, calcular mal la capacidad obligará a las empresas a cargar con mayores costes fijos cuando no se están utilizando.
- Costes de inversión – Si una empresa no conoce la capacidad necesaria para determinados niveles de demanda, puede subcomprar los equipos de capital necesarios para producir, obligando a utilizar horas extras o a subcontratar la producción. También pueden invertir en el tipo de equipo equivocado, lo que les lleva a tener un equipo inactivo que no es necesario, mientras que el equipo necesario para las líneas de productos calientes se ve forzado.
Planificación de capacidad agregada vs. desagregada
La planificación de capacidad debe realizarse en varios niveles temporales. Comenzando con períodos de tiempo más largos y ajustando posteriormente los factores en cubos de tiempo más cortos, las empresas pueden reducir sus necesidades y aumentar la precisión del plan a medida que el marco temporal se hace más pequeño y refleja las necesidades cercanas a la fecha.
La planificación de capacidad agregada es un método de planificación en el que las necesidades a medio plazo se determinan en un periodo de 2 a 18 meses. El objetivo es determinar el tipo de capacidad que se necesita, la cantidad que se necesita y el plazo en que se necesita. Al trazar los planes de capacidad con datos precisos, las empresas pueden determinar una trayectoria que les permita tener tiempo para reaccionar y añadir -o eliminar- recursos según indique la demanda.
La planificación de capacidad agregada también requiere que la empresa determine una estrategia para su plan de capacidad. Hay varios modos de estrategia, según la naturaleza de la operación y su mercado. Las estrategias agregadas incluyen:
- Capacidad de liderazgo – En esta estrategia, la capacidad se añade antes de la demanda. Esto ayuda a los dirigentes de la empresa a satisfacer la demanda antes de que se produzca. Si una empresa tiene una curva de demanda de producción estable con poca o ninguna estacionalidad, esta estrategia le permitirá planificar la capacidad de forma ajustada con confianza.
- Capacidad diferida – En este método, la capacidad se añade después de que se haya producido la demanda. Esta estrategia puede ser útil para las empresas con una producción que requiere pocos pasos de producción, o aquellas en las que el equipo necesario para aumentar la capacidad está fácilmente disponible “off-the-shelf” y se puede añadir al flujo de producción rápidamente. Requiere un alto grado de agilidad y supone un riesgo porque la inversión se retiene hasta después de que se haya producido la curva de la demanda.
- Capacidad de adaptación – Esta estrategia de planificación de la capacidad es una estrategia de “pago por uso”, ya que la capacidad sólo se incrementa de forma gradual a medida que aumentan las necesidades de volumen. También requiere que la empresa sea muy ágil y rápida de responder y es una buena opción para las PYMES que son sensibles a las restricciones causadas por un flujo de caja limitado.
La planificación de capacidad desagregada está más centrada en el nivel de operaciones. El plan desagregado utiliza cubos de tiempo más pequeños basados en el plan agregado para desarrollar un programa de capacidad que puede expresarse en horas, turnos, días, semanas y meses. Si los datos y el análisis utilizados en el plan agregado son precisos, el plan desagregado dará lugar a programas que permitan a la empresa cumplir sus objetivos de producción.
Medir la capacidad de una operación
Para determinar la capacidad, hay que medirla. Las empresas pueden utilizar estas mediciones de la capacidad para determinar las cifras de eficiencia y utilización para seguir el progreso con respecto al plan.
- Capacidad de diseño – es el estado ideal de la producción. Expresa una capacidad máxima teniendo en cuenta las velocidades de las máquinas establecidas por los fabricantes de equipos originales, así como el flujo ideal de mano de obra y materiales. Aunque no es posible alcanzar la producción máxima ideal por muchas razones, esta cifra sirve de referencia para medir otras variables.
- Capacidad efectiva – Aunque los equipos tengan una velocidad máxima, hay muchos factores que influyen en la producción real. Entre estos factores se encuentran la mezcla de productos, los cambios en la programación y en los pedidos, las interrupciones en la cadena de suministro, el mantenimiento no planificado y factores laborales como el absentismo. En la mayoría de las empresas, estos factores también se miden para crear una formulación que significa que la capacidad efectiva es la producción máxima cuando se considera el impacto de estos factores a lo largo del tiempo.
- Producción real – La producción real es la tasa de producción alcanzada.
Con estas mediciones, una empresa puede determinar dos estados de la producción: la eficiencia y la utilización de la producción. La eficiencia es una función de la producción real dividida por la capacidad efectiva. La utilización es una función de la producción real sobre la capacidad de diseño. Estas mediciones permiten a la empresa conocer la eficacia de su sistema en términos de capacidad.
Más información sobre la capacidad de producción y cómo calcularla.
Ventajas de la planificación de capacidad
La planificación de capacidad puede ayudar a las empresas de fabricación a planificar la demanda y a comprender qué recursos y costes serán necesarios para esa demanda. Proporciona una estructura y una hoja de ruta para que otros planes, como la planificación de la cadena de suministro, la planificación del mantenimiento, la programación e incluso las ventas, puedan saber lo que es posible actualmente y lo que se puede hacer con el tiempo para cumplir los objetivos de nivel de servicio ahora y en el futuro. Los beneficios de la planificación de capacidad incluyen:
- Controlar y reducir los costes – Al conocer la capacidad actual y comprender lo que se necesita para añadir o reducir la capacidad, las empresas pueden controlar y reducir los costes. Dado que se miden las variables de producción, como la mano de obra, la velocidad de los equipos y la combinación de líneas de productos, los directivos pueden utilizar las desviaciones entre los planes agregados y los desagregados para controlar los costes y hacer cambios para mantenerse en el camino a lo largo del tiempo.
- Planificar el crecimiento – La mayoría de las empresas quieren crecer con el tiempo. Pero lo mejor es que ese crecimiento sea controlable y pueda hacerse de forma incremental de manera que no afecte al flujo de caja ni sobrepase los planes de capex. Conocer la capacidad de su fábrica ayuda a planificar ese crecimiento de forma medida y rentable.
- Recursos humanos – Como la mano de obra es una parte importante de las capacidades de producción, forma parte de la planificación de capacidad. Con unos planes de capacidad precisos, los responsables de recursos humanos pueden planificar la contratación, la formación y otras tareas relacionadas con el personal de forma que se optimice el coste de incorporación de personal (o su reducción en caso de recesión). Esto significa que los niveles de personal serán correctos cuando la demanda cambie.
- Mayor rentabilidad – Cuando no existe una planificación de capacidad, pueden producirse lagunas en la producción a medida que cambia la demanda. Los directivos pueden no saber qué recursos se necesitan y cómo ajustarlos. Al utilizar la planificación de capacidad, se eliminan estas lagunas. Esto se traduce en menos horas extras, empleados mejor formados y una utilización optimizada de los equipos.
- Mejora continua – La precisión de la planificación de capacidad exige la medición de los factores clave de la producción, tal y como se ha mencionado anteriormente. Gracias a la medición de estas variables, se pueden identificar áreas de mejora y tomar medidas proactivas para ajustar o cambiar un proceso. Estos cambios pueden mejorar la eficiencia y crear capacidad adicional mediante el uso de los recursos existentes.
Planificación de capacidad sin MRP
Muchas pequeñas y medianas empresas (PYMES) operan su fabricación con software. Sin embargo, muchas siguen utilizando una mezcla ad hoc de hojas de cálculo, suposiciones, historial de productos y sensaciones viscerales para la planificación. Esto es cierto para todos los tipos de planificación dentro de esas empresas. Es fundamental que los fabricantes apliquen la planificación de capacidad, especialmente en el caso de las PYMES, donde un error de cálculo en la capacidad puede significar la pérdida de pedidos durante la alta demanda o un alto coste durante los tiempos de inactividad.
Para planificar la capacidad sin utilizar un sistema MRP, las empresas deben limitarse a la capacidad aproximada. Por lo general, la capacidad aproximada utiliza métodos manuales para analizar los factores de producción, equipamiento y personal con el fin de identificar posibles cuellos de botella. Las personas encargadas de la planificación deben comparar los requisitos del programa maestro disponibles con la capacidad disponible en varios centros de trabajo. Como se ha comentado anteriormente, estos factores contribuyentes deben medirse incluso si no se utiliza un MRP para que los responsables de la toma de decisiones puedan determinar si el programa maestro de producción debe modificarse para ajustar las futuras cargas de trabajo en los centros de trabajo.
Para una planificación aproximada que pueda realizarse sin un MRP, existen varias opciones:
- Capacidad mediante factores generales – Todo lo que se necesita para esta técnica de planificación de capacidad aproximada es el programa maestro de producción y los estándares de producción previamente medidos. Analizando estos dos elementos frente a la posición del pedido, los planificadores pueden convertir las necesidades de productos acabados para determinar la carga del puesto de trabajo. La capacidad mediante factores globales es un proceso manual.
- Listas de capacidad – Las listas de capacidad se centran en el tiempo y son utilizadas por aquellos que tienen listas de materiales (BOM) precisas y específicas. En las listas de materiales, estas listas de materiales se utilizan junto con las hojas de ruta. Esto permite a los planificadores especificar dónde se fabrica y cuál será el tiempo de ejecución del puesto de trabajo. Si esto se hace manualmente, lo más probable es que la lista de materiales sea de un solo nivel o, como mucho, sólo explotable a uno o dos niveles adicionales debido a la complejidad del producto que conllevan los procesos manuales.
- Perfiles de recursos – Al igual que las facturas de capacidad, esta técnica utiliza listas de materiales y hojas de ruta. La diferencia es que también se tiene en cuenta el plazo de entrega.
Ejemplos de planificación de capacidad sin un sistema MRP
Los ejemplos de utilización de la planificación de capacidad sin un sistema MRP demuestran que se puede hacer, pero también ponen de manifiesto su margen de error. Por ejemplo: Para una fábrica que hace letreros de vinilo serigrafiados para abastecer a una base de clientes grande y consistente, la capacidad mediante factores generales puede significar que no necesitan una verdadera lista de materiales y pueden simplemente programar diseños establecidos en cantidades predecibles en un cronograma con la confianza de que los cambios de volumen y proceso son mínimos. Sin embargo, si el proceso requiriera una redacción rápida o nueva con regularidad, o si las nuevas iteraciones requirieran una verdadera lista de materiales que incluyera algo más que vinilo y tinta, la capacidad sería más difícil de predecir.
Otro ejemplo en el que se utiliza Capacity Bills podría ser el mismo producto, rótulos de vinilo serigrafiados, pero utilizando una verdadera lista de materiales para un producto más complicado. Este producto utilizaría una verdadera lista de materiales que incluyera el vinilo, la tinta, el dobladillo de los bordes, la instalación de ojales, los soportes para colgar y montar y otros componentes. Una vez más, dado que estos procesos pueden medirse con precisión, las hojas de ruta y los tiempos de cada componente necesario para su realización podrían acompañar a la lista de materiales para determinar el tiempo y establecer el centro de trabajo.
Y, por último, el mismo escenario podría hacerse manualmente, sin un MRP, utilizando perfiles de recursos. Sería esencialmente lo mismo que el ejemplo anterior. Sin embargo, una vez establecidos el lugar y la hora de la ejecución, se podría utilizar el tiempo de espera para establecer un orden de prioridad para su realización.
Muchos fabricantes utilizan este tipo de técnicas de planificación de capacidad. Sin embargo, estas técnicas son propensas al error humano y dependen de los datos históricos para su éxito. No están orientadas al futuro y no tienen en cuenta las ventajas de los sistemas MRP modernos, como la optimización de inventarios, el análisis ABC, las rutas automatizadas, la gestión de órdenes de cambio y muchas otras características que simplemente no pueden ser gestionadas por planificadores humanos en los complejos entornos de fabricación actuales.
Planificación de necesidades de capacidad y MRP
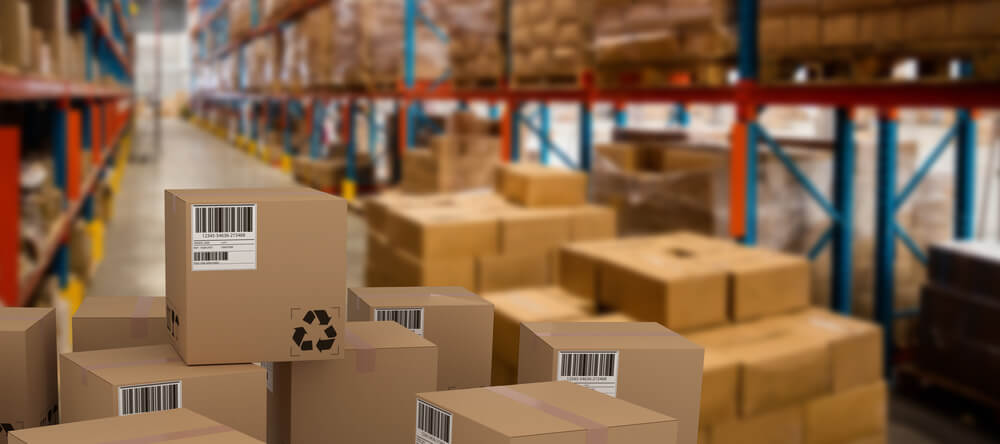
Las tres técnicas anteriores pueden utilizarse sin MRP pero también con un sistema MRP. Sin embargo, la única técnica de planificación de capacidad que requiere absolutamente un sistema MRP es también la más precisa y flexible. La planificación de las necesidades de capacidad (CRP) compara la capacidad disponible en toda la empresa en todos sus puestos de trabajo con los planes de necesidades de material. La CRP puede ayudar a crear cargas de trabajo alcanzables y también puede mejorar la utilización ante recursos limitados.
Un sistema MRP permite a una empresa utilizar los datos no sólo en un sentido histórico para comparar con las mediciones. También proporciona un marco dinámico de datos casi en tiempo real, así como transacciones históricas para mejorar la planificación de capacidad y hacerla más precisa y predecible. En lugar de utilizar una capacidad aproximada para calibrar un rango de lo que se necesita, el CRP utiliza la profundidad de la funcionalidad de un MRP para convertirlo en una herramienta verdaderamente predictiva y desbloquear la capacidad adicional a través de la planificación proactiva con el MRP.
Entre los ejemplos de cómo se facilita la planificación de capacidad con un MRP se incluyen:
Planificación de la producción
Todos los MRP tienen módulos de planificación de la producción que son fundamentales para su éxito. Esta planificación de la producción incluye, por supuesto, funciones como los registros de órdenes de fabricación y el programa de producción. Pero también incluye los puestos de trabajo, los grupos de puestos de trabajo, las listas de materiales y las hojas de ruta. Todos estos elementos son necesarios para la planificación de la capacidad de producción. Al utilizar la precisión y el análisis del sistema MRP, la planificación de capacidad es más fácil. Los planificadores de capacidad pueden ver los programas de mantenimiento y cualquier edición realizada en la estación de trabajo que mejore o reduzca su rendimiento.
Lo mismo ocurre con las listas de materiales y las hojas de ruta, ambas cruciales para la planificación de capacidad. Con un MRP, las listas de materiales no sólo están actualizadas y son precisas. Cualquier cambio en el proceso que afecte a las listas de materiales se actualiza automáticamente en todo el sistema. También se pueden desglosar en una lista de materiales de varios niveles, lo que reduce la complejidad de los planes de capacidad y elimina la redundancia necesaria para calcular manualmente los distintos niveles de la lista de materiales. Lo mismo ocurre con las hojas de ruta, donde los cambios, incluidos los avisos de cambios de ingeniería, se transmiten a todo el sistema para que los planificadores de capacidad no pierdan información crucial.
Análisis ABC
Por muy importante que sea la planificación de capacidad, su importancia es paralela a la de otras áreas críticas de la gestión empresarial, como el control de costes, la optimización de las compras y la compra y valoración de inventarios. Los sistemas MRP pueden ayudar a realizar el análisis ABC, en el que se utiliza el principio de Pareto para asignar una valoración ponderada a los materiales y componentes que mide su uso e importancia para los productos acabados, y las listas de materiales, en los que se utilizan.
El análisis ABC ayuda a los responsables de la toma de decisiones a elaborar niveles de stock y planes de compra optimizados para maximizar el valor del dólar gastado. Estos planes de compra pueden automatizarse para incluir cualquier cambio en las listas de materiales debido a sustitutos u otras cuestiones. Estos cambios están disponibles inmediatamente en todo el sistema y pueden aplicarse a los planes de capacidad para mejorar su precisión en función del valor del inventario en relación con su importancia ponderada.
Más información sobre el análisis ABC (regla 80/20) en la gestión de inventarios.
Recursos humanos
Los sistemas MRP actuales cuentan con una profunda funcionalidad que lleva las órdenes de producción, las cargas de trabajo en todos los puestos y otros factores hasta el nivel de personal. Esto significa que RRHH puede calcular el personal necesario en cada puesto de trabajo hasta el número de empleados necesarios. La mano de obra y el personal son una parte integral de la planificación de capacidad. Al utilizar la funcionalidad nativa de un sistema MRP para la mano de obra dentro de RRHH, la planificación de la capacidad puede incluir los requisitos exactos de personal que hacen que su plan sea más preciso.
Programación de la producción
Un sistema MRP también tendrá un módulo de planificación de la producción para programar el taller. Esto significa que las tareas de programación de la producción se automatizan y se reducen los errores. Los planificadores de la producción pueden utilizar tanto la programación hacia delante como hacia atrás para programar las órdenes de fabricación en el primer momento disponible y con la garantía de que los recursos estarán allí para hacer el producto terminado. También pueden ver y editar los puestos de trabajo e incluso programar los servicios subcontratados.
Debido a que la mayoría de los fabricantes operan con maquinaria hecha por muchos OEMs diferentes, no todas las máquinas son iguales. La planificación de la producción dentro de los sistemas MRP puede mostrar las órdenes de fabricación (MO) como operaciones individuales, además de verlas como un bloque. Esto les permite optimizar las configuraciones por grupos o programarlas individualmente en función del tamaño de la orden o la prioridad. Esta optimización repercute directamente en la planificación de la capacidad, ya que la visualización de las órdenes de trabajo para reducir los tiempos de cambio de artículos similares puede desbloquear la capacidad que estaba oculta anteriormente. La mayoría de estos sistemas cuentan con una función dinámica de arrastrar y soltar que tiene en cuenta la disponibilidad y la capacidad de los materiales.
Más información sobre la programación progresiva y la programación regresiva en la planificación de la producción.
El valor de la MRP en la planificación de capacidad
Si bien la planificación de la capacidad a grandes rasgos se puede lograr sin un sistema MRP, el valor de la funcionalidad comentada anteriormente, así como la funcionalidad adicional, no sólo facilitan la planificación de capacidad. También la hace más precisa, más ágil y más flexible. Cuando la planificación de capacidad se realiza junto con un sistema MRP, la profunda funcionalidad, los análisis avanzados y el uso y cálculo nativo de muchos de los elementos necesarios para los planes de capacidad fiables hacen que no tenga sentido planificar la capacidad sin el uso de un software de planificación de capacidad.
Principales aspectos a tener en cuenta
- La planificación de capacidad determina la capacidad necesaria para satisfacer la demanda y, como tal, es un requisito previo para la planificación y programación eficientes en toda una empresa de fabricación.
- La planificación de capacidad tiene en cuenta el número de máquinas y los empleados necesarios para operar esas máquinas, las horas o turnos disponibles, la mezcla de productos que se van a fabricar, la utilización de los equipos y la eficiencia general.
- La planificación de capacidad también influye en áreas financieras como los costes de explotación, los costes fijos y los costes de gastos de capital.
- La planificación de capacidad debe realizarse tanto a nivel agregado como desagregado. La planificación de capacidad agregada contempla un marco temporal más largo -de 2 a 18 meses-, mientras que la planificación de capacidad desagregada se centra en tramos temporales más pequeños basados en el plan agregado más largo.
- Para planificar la capacidad, primero hay que determinarla. Esto puede hacerse midiendo el rendimiento cuando la planta está funcionando a plena capacidad, utilizando una planificación de capacidad aproximada o utilizando un sistema MRP.
- La planificación de capacidad puede ayudar a las empresas a controlar y reducir los costes, planificar el crecimiento sostenible, planificar las necesidades de recursos humanos, aumentar la productividad y los beneficios, y sentar las bases para la mejora continua en toda la empresa.
- Aunque la planificación de capacidad puede hacerse manualmente, utilizando una planificación de capacidad aproximada, este método es propenso a errores y no proporciona los beneficios que un sistema ERP/MRP.
- Los sistemas ERP/MRP facilitan la planificación de capacidad a los fabricantes gracias a que mantienen actualizados los datos necesarios para la planificación de capacidad. El software también ayuda a las empresas a realizar análisis ABC para optimizar los niveles de stock y mejorar la precisión del plan de capacidad, planificar mejor las necesidades de personal, crear automáticamente programas de producción utilizando la programación progresiva y regresiva, y aportar análisis avanzados al proceso de toma de decisiones.
También te puede gustar: ¿Cómo utilizar la teoría de las restricciones?