¿Qué es un plan maestro de producción (MPS)? Con ejemplos
El plan maestro de producción (MPS) es una herramienta de planificación de la producción que ayuda a calcular qué cantidad de un producto debe fabricarse en distintos periodos. Esta sencilla programación puede utilizarse como base para la planificación y programación posteriores en toda la empresa de fabricación.
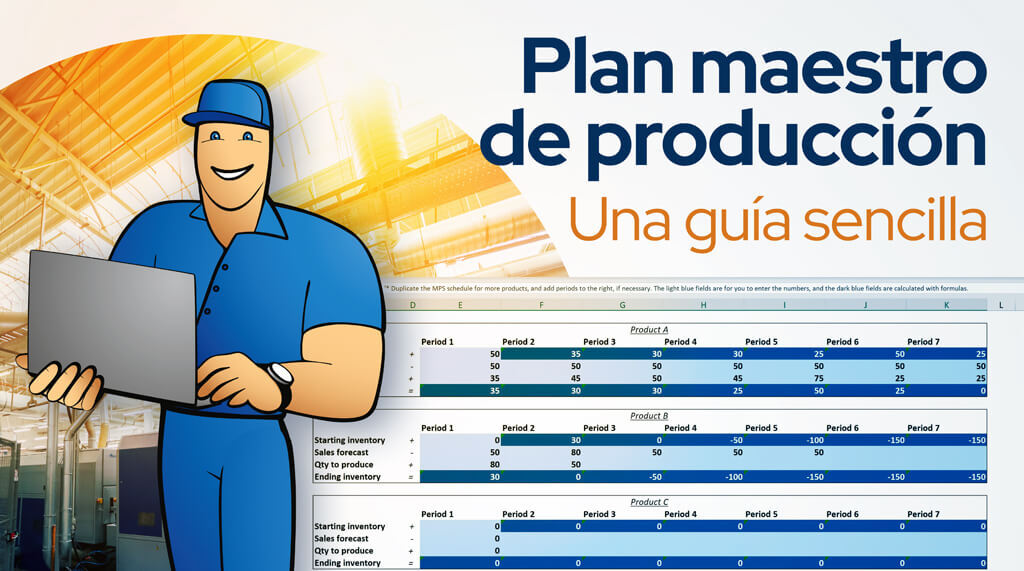
¿Qué es un plan maestro de producción (MPS)?
El plan maestro de producción (Master Production Schedule o MPS) es una herramienta de planificación de la producción que describe qué productos deben fabricarse, en qué cantidad y cuándo. Un plan maestro de producción (MPS) no entra en detalles sobre las operaciones de producción, la secuenciación, los empleados asignados a las tareas, etc. Es más bien como un contrato entre el departamento de ventas y el de fabricación que equilibra la oferta y la demanda definiendo las cantidades necesarias para producir dentro de unos plazos específicos.
El plan maestro de producción (MPS) es una herramienta vital en los entornos de producción para almacenamiento (make-to-stock), en los que la previsión de la demanda dirige la planificación de la producción. Dado que un MPS se utiliza a menudo como principal impulsor de la actividad de producción, debe ser preciso y viable para que tenga un efecto positivo en la rentabilidad de una empresa.
El MPS también puede utilizarse en determinados entornos de fabricación bajo pedido y operaciones de fabricación de modo mixto en las que una empresa fabrica productos estándar. En este caso, la previsión de ventas y el plan maestro de producción se utilizan sobre todo para planificar el inventario necesario para la producción.
Un plan maestro de producción (MPS) estándar es un plan a largo plazo elaborado para cada producto por separado. Se crea con un horizonte de planeación de unos meses a varios años, con un intervalo de tiempo mínimo (el marco temporal más pequeño especificado) de 1 semana.
Ventajas de un plan maestro de producción (MPS)
La introducción de un MPS en una empresa de fabricación tiene múltiples ventajas:
- Proporciona una base sólida para construir, mejorar y seguir la previsión de ventas.
- Ayuda a determinar y alcanzar los niveles de inventario deseados, evitando así el desabastecimiento y el exceso de existencias.
- Es una entrada para calcular las cantidades de piezas, sub-componentes o materias primas que hay que comprar o producir, como parte de la siguiente fase de la Planificación de requerimientos de materiales.
- Permite calcular la cantidad de trabajadores y turnos necesarios con muchos meses de antelación.
- Permite optimizar la capacidad instalada y equilibrar la carga de la planta con antelación, lo que permite a las empresas evitar cuellos de botella.
- El departamento de fabricación puede utilizar el MPS para estimar los costos de producción y mantenimiento asociados a los puestos de trabajo.
- El departamento financiero de la empresa puede derivar los ingresos y gastos previstos del MPS y generar una previsión de tesorería. Entre otras ventajas, esto ayudará a elaborar planes de inversión.
- El departamento de RRHH puede aprovechar el MPS para anticiparse a las necesidades de contratación de trabajadores.
- Una planificación y ejecución precisas del MPS pueden mejorar significativamente el servicio y la satisfacción de los clientes al garantizar el cumplimiento de los pedidos y mantener los niveles de servicio necesarios.
- El MPS define objetivos visibles, claros y medibles para las operaciones de la empresa, así como un plan para alcanzarlos.
El MPS debe reflejar el plan de negocio lo más fielmente posible. Esto requiere una actualización constante por parte de todos los departamentos de la empresa.
Por ejemplo, si el departamento de marketing planifica una promoción de ventas, el aumento de la demanda debe reflejarse en el MPS y en la previsión. Si el equipo de ventas desincentiva la venta de una línea de productos en favor de otra, habrá que ajustar el MPS y la previsión.
¿Dónde debe utilizarse el MPS?
Aunque los planes maestro de producción (MPS) se asocian con mayor frecuencia a los flujos de trabajo de producción para almacenamiento, también pueden respaldar la planificación de la producción en entornos de fabricación bajo pedido, ensamblaje bajo pedido, producción por lotes y personalización masiva. A continuación un breve resumen de dónde puede aplicarse el MPS con mayor eficacia:
1. Producción para almacenamiento (MTS). En los entornos producción para almacenamiento (MTS o Make-to-stock), en los que los productos se fabrican para su almacenamiento en función de las previsiones de demanda, el MPS se utiliza para alinear los planes de producción con la demanda prevista. Al predecir la cantidad de productos necesarios, los fabricantes pueden evitar la sobreproducción o los desabastecimientos, optimizando los niveles de inventario y reduciendo los desechos.
2. Fabricación bajo pedido (MTO). Incluso en situaciones de fabricación bajo pedido (MTO o Make-to-order), en las que los productos se fabrican una vez recibido el pedido de un cliente, el MPS puede ser útil. Permite a los fabricantes planificar su capacidad y sus recursos de forma eficiente, garantizando que pueden cumplir los pedidos dentro de los plazos prometidos.
3. Ensamblaje bajo pedido (ATO). Los fabricantes de ensamblaje bajo pedido (ATO o assemble-to-order), que ensamblan productos a partir de pedidos de clientes utilizando componentes prefabricados, también se benefician de MPS. El cronograma ayuda a planificar las operaciones de ensamblaje, garantizando que los componentes estén disponibles cuando se necesiten y que los productos finales se ensamblen a tiempo.
4. Producción por lotes. En entornos en los que se fabrican productos similares en grupos o lotes, la MPS ayuda a determinar el tamaño de lote óptimo y a secuenciar los lotes para maximizar la eficiencia y minimizar los tiempos de preparación o cambio.
5. Personalización masiva. La personalización masiva es una mezcla de MTS y MTO, en la que los productos básicos se fabrican en masa y después se personalizan según las necesidades del cliente. Coordinando la producción de componentes genéricos con planes maestro de producción y personalizándolos después según pedidos específicos, los fabricantes pueden satisfacer la demanda de forma más eficiente.
Datos de entrada de un plan maestro de producción (MPS)
Los datos de entrada básicos que necesita para crear un plan maestro de producción viable son los siguientes:
1. Inventario inicial. ¿Cuántas unidades de la SKU están ya disponibles en existencias?
2. Previsión de ventas / plan de demanda. ¿Cuántos pedidos se esperan para el periodo?
3. Portafolio actual de pedidos. ¿Cuántos pedidos están ya previstos para ese periodo?
4. Cantidad a producir. ¿Cuántas unidades hay que producir durante el período para mantener el equilibrio entre la oferta y la demanda?
Descargue gratis una plantilla de plan maestro de producción.
Ejemplo
Supongamos que usted fabrica muebles de madera, como sillas, mesas de comedor y mesas de centro.
Al principio del periodo, tiene 40 sillas en existencias. La previsión de ventas indica que venderá 200 sillas. Eso significa que tendrá que producir 160 sillas durante ese periodo para satisfacer la demanda.
En consecuencia, el inventario inicial de su próximo período será 0. Como el negocio es estable, se prevén otras 200 ventas de sillas. Esto significa que ahora tendrá que producir 200 sillas en un período para satisfacer la demanda.

Plan maestro de producción (MPS) y stock de seguridad
A menos que haya perfeccionado absolutamente el modelo de fabricación justo a tiempo (just-in-time), siempre querrá mantener una cierta cantidad de unidades como reserva en caso de que se produzca un pico imprevisible de la demanda. Por eso podemos complementar el plan maestro de producción con:
5. Stock de seguridad. ¿Cuántas unidades quiere tener en existencias por si se producen picos de demanda?
En el plan maestro de producción, el stock de seguridad se expresa como parte del inventario final del período que se transferirá al siguiente período como inventario inicial.
Ejemplo – continuación
Ahora, continuando con el ejemplo anterior, imagine que desea mantener siempre 40 sillas como stock de seguridad. Por tanto, 160 sillas no serán suficientes para satisfacer la demanda y reponer su stock de seguridad durante el primer periodo. Esto significa que tendrá que producir 200 sillas en total para satisfacer a sus clientes y mantener el colchón necesario.

Más información sobre Stock de seguridad y cómo calcularlo.
Plan maestro de producción y planificación de la capacidad preliminar
A la hora de planificar la producción, siempre hay que tener en cuenta la cantidad exacta que se puede producir en un periodo determinado. Si recibe pedidos que le exigen producir mil sillas en un mes, pero sólo tiene medios para producir 500, defraudará a sus clientes y a su empresa. Por eso, siempre es conveniente hacer cuentas:
6. Capacidad de producción. ¿Cuántos productos podría fabricar durante el periodo, siempre que todo funcione correctamente?
La planificación de la capacidad preliminar es una herramienta importante que debe utilizarse junto con el plan maestro de producción. Para calcular su capacidad de producción, necesitará conocer el tiempo de procesamiento de sus productos y el total de horas productivas de su taller.
Una vez creado el plan maestro de producción inicial, puede comprobar su viabilidad creando un plan de la capacidad preliminar de acuerdo con el MPS. Si el plan de capacidad muestra que su capacidad de producción no puede acomodar los niveles de producción en cualquier periodo establecido en el MPS, tendrá que encontrar la manera de aumentar la capacidad o modificar el MPS.
El plan maestro de la producción (MPS) y la planificación de la capacidad preliminar son un proceso de ida y vuelta. Esto significa que cualquier cambio en uno de ellos exige revisar el otro.
Más información sobre la capacidad de producción y la planificación de la capacidad preliminar.
Consideraciones adicionales sobre MPS
Congelación del plan maestro de producción
Congelar el MPS significa bloquear el primer par de periodos un cierto tiempo, por ejemplo una semana o dos, antes de que empiece la producción según lo previsto. Esto se hace para evitar cambios de última hora que puedan ralentizar la producción y, en última instancia, arruinar sus planes.
Disponible para promesa
Disponible para promesa es el número de unidades que puede prometer entregar adicionalmente a los clientes (como pedidos confirmados) en el periodo en cuestión. Se calcula en función del plan maestro de producción. Tiene en cuenta todos los pedidos confirmados y las cantidades planificadas a lo largo del horizonte del MPS. El ATP desempeña un papel importante en la gestión de la cadena de suministro.
Criterios de lote
A la hora de elaborar un plan maestro de producción, siempre hay que tener en cuenta el tamaño de los lotes, es decir, cuántos productos se fabrican en una ronda. Eso determinará el nivel de sus cantidades. Por ejemplo, si fabrica lotes de 25 productos, la cantidad a producir no puede ser 240, sino 250 o 225.
Inventario máximo
El MPS es una gran herramienta para planificar y prepararse con antelación para los picos de demanda. Sin embargo, existen limitaciones físicas y prácticas a las cantidades que puede almacenar en existencias. Aunque se disponga de capacidad de producción, puede que no sea posible utilizarla si las existencias están llenas. O, a partir de un determinado nivel de existencias, puede quedar demasiado efectivo inmovilizado en ellas.
6 consejos para gestionar un plan maestro de producción
Dominar el plan maestro de producción (MPS) es vital para una planificación eficaz de la producción y unos procesos de fabricación optimizados. He aquí seis consejos clave para gestionar eficazmente un MPS:
1. Equilibrar la demanda y la oferta. Un MPS eficaz equilibra la demanda de los clientes con la capacidad de producción. Aunque es crucial satisfacer los pedidos de los clientes a tiempo, sobrecargar la línea de producción puede provocar un aumento de los costos e ineficiencias. Por otro lado, la infrautilización de la capacidad puede provocar pérdidas de ventas y reducir la rentabilidad. Encuentre el equilibrio adecuado en función de su estrategia empresarial y las condiciones del mercado.
2. Alinear el MPS con los objetivos empresariales. Su MPS debe alinearse con sus objetivos empresariales generales. Si su objetivo es reducir los costos de mantenimiento de inventario, por ejemplo, su MPS debe estar diseñado para producir justo a tiempo (just-in-time) para satisfacer la demanda. Si su objetivo es alcanzar altos niveles de servicio, su MPS puede necesitar incluir stock de seguridad o estar orientado a tiempos de respuesta rápidos.
3. Revisar y actualizar periódicamente. En el cambiante panorama de la oferta y la demanda, un MPS estático puede quedar obsoleto rápidamente. Revise y ajuste periódicamente su MPS en función de los datos de ventas en tiempo real, los pedidos de los clientes, los niveles de inventario y las condiciones de la cadena de suministro para garantizar su precisión y eficacia. Como regla general, un MPS debe revisarse semanalmente.
4. Colaborar entre departamentos. Un MPS afecta a múltiples departamentos de una empresa, desde producción hasta ventas y compras. Asegúrese de que todas las partes implicadas participan en su creación y revisión. Este enfoque colaborativo puede mejorar la precisión de las previsiones, la asignación de recursos y la eficacia general del MPS.
5. Utilizar la tecnología adecuada. Utilice un sistema ERP de fabricación que pueda automatizar gran parte del proceso MPS y de planificación de la fabricación. Estos sistemas pueden proporcionar datos en tiempo real, ayudando a agilizar el proceso, reducir los errores y mejorar la capacidad de respuesta a los cambios en la demanda o la oferta.
6. Realizar un seguimiento de las métricas y mejorar continuamente. Hay muchos KPI que se pueden controlar para evaluar la precisión y utilidad de un MPS. Entre ellos se incluyen el cumplimiento y la consecución de la programación, los niveles de inventario, la tasa de utilización de la capacidad, el OTIF, etc. Medir el rendimiento de su MPS y compararlo con los datos históricos le permite comprender cuándo es necesario mejorar algún aspecto del proceso de planificación. Recuerde que un MPS no es una herramienta que se fija y se olvida. Requiere una gestión y un ajuste continuos para reflejar la realidad actual e impulsar un rendimiento óptimo de la producción.
Plan maestro de producción vs. Planificación de los recursos de fabricación
El plan maestro de producción es uno de los puntos de partida para la planificación de requerimientos de materiales (MRP I) y la planificación de los recursos de fabricación (MRP II). Sin embargo, además del MPS, MRP utiliza datos como el estado de las existencias, las listas de materiales, las hojas de ruta, los requerimientos y los costos de material, los registros financieros, la dotación de personal y la capacidad de las máquinas, etc., para crear un plan muy detallado de todos los recursos relacionados con la producción y ofrecerle una visión general de su empresa en tiempo real, mejorando la gestión global de las operaciones y no solo la planificación de la producción.
A diferencia de la creación de un plan maestro de producción, la complejidad de la planificación de los recursos de fabricación hace que sea imposible realizarla manualmente. Hoy en día, hay muchos proveedores de software que ofrecen sistemas MRP, pero muchos de ellos han crecido a partir de software de contabilidad o de gestión de inventario y están limitados en sus capacidades de planificación de los recursos de fabricación. Sin embargo, el uso de un software MRP adecuado es cada vez más importante para mantener la competitividad en el sector de la fabricación.
MRPeasy es una de las pocas soluciones basadas en la nube que reúne las funciones de software de planificación y programación de la producción, lo que significa que el sistema admite tanto la planificación a largo plazo basada en MPS como la programación a corto plazo.
Proceso de programación maestra dentro de un sistema MRP
Aunque puede utilizar Excel para crear un plan maestro de producción sencillo, los sistemas MRP/ERP de fabricación modernos (o al menos los que tienen una funcionalidad MPS) hacen que utilizar el plan maestro de producción como base para una planificación y programación más avanzadas sea extremadamente sencillo. Así es como un sistema MRP utiliza el MPS:
1. Entrada automática de datos. El software MRP rellena automáticamente varias entradas en función de los datos de que dispone: pedidos de venta confirmados, órdenes de fabricación ya programadas, pedidos de compra e inventario inicial. Cuando cambia alguno de estos valores, el MPS se actualiza automáticamente, dando a los equipos de ventas, producción y compras información en tiempo real y permitiéndoles tomar las medidas necesarias, por ejemplo, cambiando el MPS, aumentando la capacidad o pidiendo materiales adicionales.
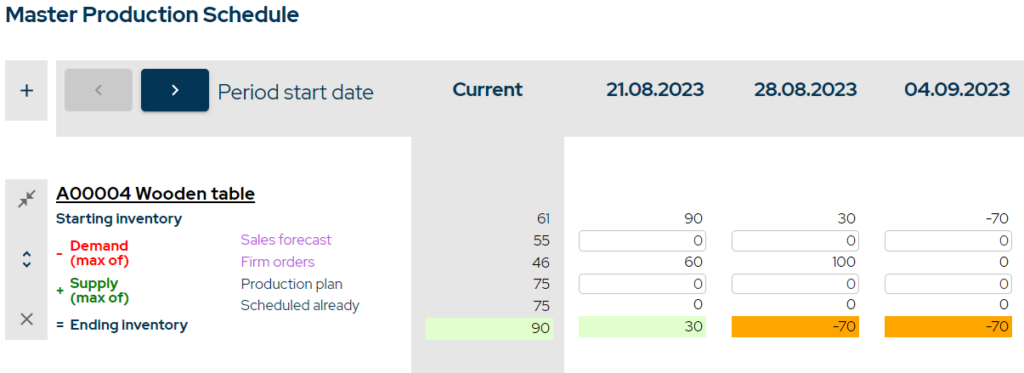
2. Planificación de la demanda. El equipo de ventas utiliza los datos históricos y las tendencias para prever la demanda de los próximos periodos. Tras introducir los pedidos de venta confirmados y la demanda prevista, el sistema los compara con los niveles actuales de inventario para determinar las cantidades necesarias para producir durante el periodo. Este es el plan maestro de producción básico.
Es importante señalar que la previsión de la demanda sólo es válida hasta que las cantidades de los pedidos confirmados no superen la demanda prevista.
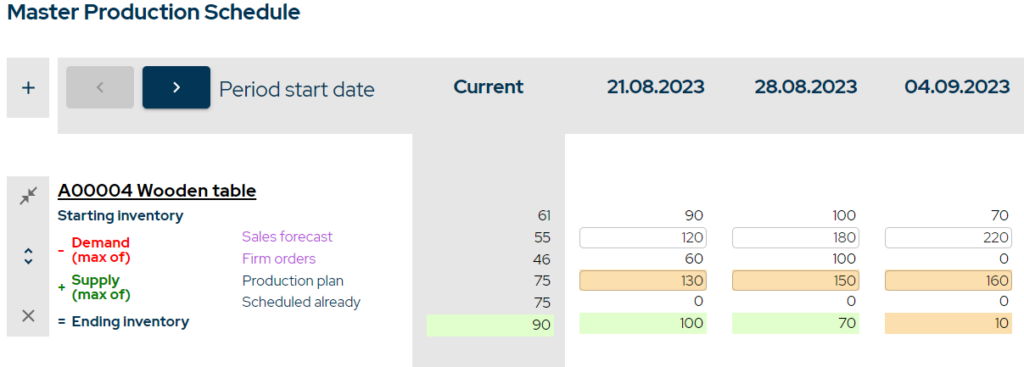
3. Planificación de la capacidad. Una vez creado el MPS básico, interviene el planificador de la producción. El sistema MRP utiliza el MPS para realizar la planificación de la capacidad preliminar (RCCP). Esto implica comprobar si hay suficiente capacidad disponible (en términos de maquinaria y mano de obra) para cumplir con el programa de producción esbozado en el MPS. Si la capacidad disponible no satisface las necesidades de capacidad, el planificador de la producción debe ajustar el MPS o aumentar la capacidad de producción, por ejemplo, añadiendo un turno.
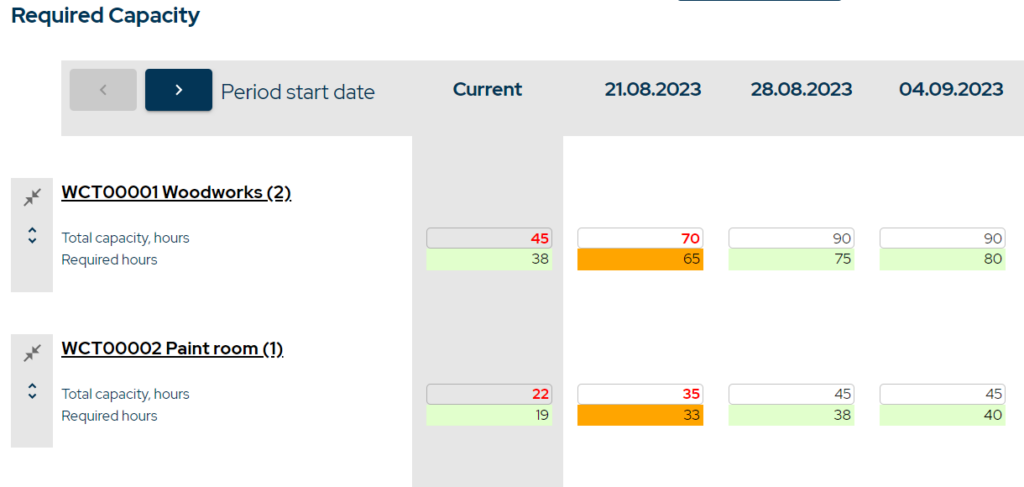
4. Planificación de las compras. Una vez establecido el MPS, el sistema lo utiliza como entrada para calcular las necesidades de material de cada periodo. El software MRP toma el plan maestro de producción y la lista de materiales (BOM) de cada producto, así como el inventario actual de materias primas, y calcula las cantidades necesarias de cada material o componente y cuándo se necesitan. El equipo de compras puede entonces utilizar este plan para asegurarse de que los materiales necesarios se adquieren a tiempo para la producción y se optimizan los niveles de inventario.
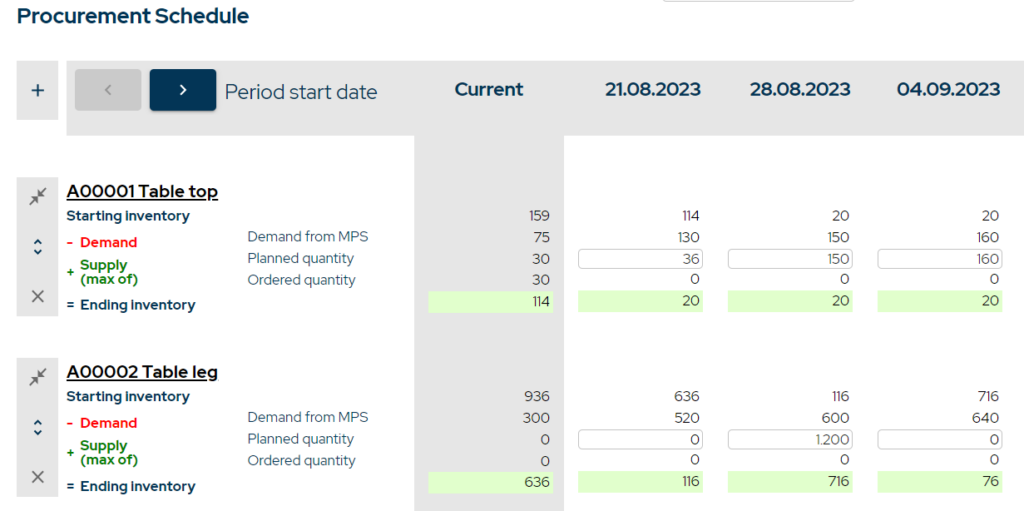
5. Programación de la producción. Un sistema MRP puede utilizarse para convertir los pedidos de los clientes en órdenes de fabricación y programarlas automáticamente en función de los recursos disponibles o de la fecha de vencimiento del pedido. Alternativamente, los planificadores de la producción pueden crear manualmente órdenes de fabricación (que luego se programan automáticamente) para alinear la producción con el MPS.
6. Ajustes en tiempo real. Como se ha mencionado anteriormente, los sistemas MRP/ERP pueden utilizarse para ajustar el MPS y los planes posteriores en tiempo real a medida que cambian las condiciones, como un aumento de la demanda o un retraso en la recepción de materias primas. Esta agilidad permite a los fabricantes responder rápidamente a los cambios en el entorno empresarial, reduciendo los riesgos y las posibles pérdidas, y manteniendo a todas las partes informadas e implicadas en el proceso. También facilita el análisis de escenarios hipotéticos, lo que permite a los fabricantes estar mejor preparados para una variedad de situaciones posibles.
Al integrar el MPS en un sistema MRP, los fabricantes pueden automatizar y optimizar su proceso de planificación de la producción, mejorando la eficacia, reduciendo los costos y aumentando su capacidad para satisfacer la demanda de los clientes.
Principales aspectos a tener en cuenta
- El plan maestro de producción (MPS) es una herramienta de planificación de la producción que alinea la producción con la demanda, detallando productos, cantidades y plazos con un horizonte de planificación de varios meses a años.
- Entre las ventajas de la programación maestra se incluyen la optimización del inventario, la evaluación comparativa de la precisión de las previsiones, una planificación precisa de la capacidad, la mano de obra y las finanzas, y un aumento potencial de la satisfacción del cliente.
- Aunque el MPS se asocia sobre todo a entornos de producción para almacenamiento, puede utilizarse tanto en la fabricación bajo pedido como en la fabricación de modo mixto.
- Los datos clave del MPS incluyen el inventario actual, la previsión de la demanda, los pedidos de venta confirmados y las cantidades de producción. Además, las empresas pueden tener en cuenta el stock de seguridad y la capacidad de producción.
- Una gestión adecuada de los planes maestros de producción implica equilibrar la demanda y la oferta, alinear los planes con los objetivos empresariales, actualizar periódicamente el MPS, colaborar entre departamentos, utilizar software ERP habilitado para MPS y realizar un seguimiento de las métricas clave.
Preguntas frecuentes
Un plan maestro de producción (MPS) le indica la cantidad de cada producto que debe fabricarse periodo a periodo.
Un ejemplo de plan maestro de producción sería que un fabricante de muebles tuviera 40 sillas en existencias. Su previsión de ventas dice que venderá 200 de ellas durante el periodo, lo que significa que necesitará producir 160 sillas durante ese periodo para satisfacer la demanda.
La diferencia entre el MRP y el plan maestro de producción es que el MPS se centra en cuándo y cuánto producir, mientras que el MRP determina los materiales y recursos necesarios para cumplir el MPS.
En lean, el plan maestro de producción (MPS) es un plan racionalizado que dirige la producción en función de la demanda real, minimizando al mismo tiempo los desechos y las existencias.
También le puede interesar: Programación progresiva frente a programación regresiva en la planificación de la producción