¿Qué es la mejora de procesos y cómo implementarla?
La mejora de procesos en la fabricación no consiste únicamente en ajustar unos pocos procedimientos. Implica un enfoque holístico, que integra metodologías probadas como la fabricación ajustada, Six Sigma y Kaizen, con soluciones de vanguardia como el software ERP de fabricación.
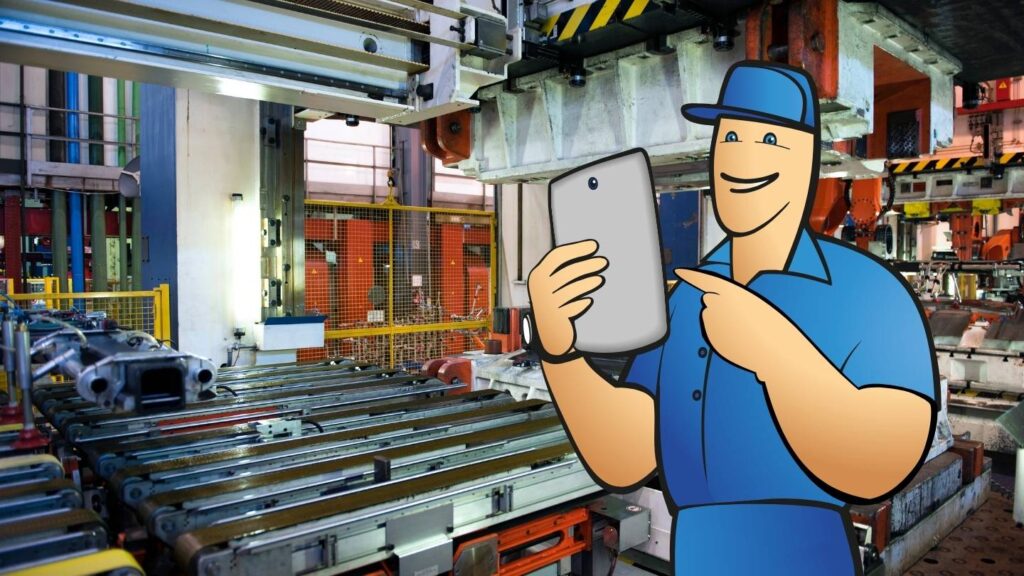
¿Qué es la mejora de procesos?
La mejora de procesos se refiere al enfoque sistemático de identificar, analizar y mejorar los procesos empresariales existentes, especialmente en la industria de la fabricación. El objetivo es optimizar las operaciones, mejorar la calidad y reducir los costos eliminando ineficiencias y errores. Es un esfuerzo continuo que apoya los objetivos de una organización de mantener la competitividad y satisfacer las demandas cambiantes de los clientes.
¿Por qué es importante mejorar los procesos?
La mejora de procesos destaca como una estrategia fundamental, que permite a las organizaciones adaptarse, sobresalir y liderar en sus respectivos sectores. A continuación explicaremos cómo afecta la mejora de procesos a las operaciones empresariales:
- Aumenta la eficiencia operativa. Analizando y perfeccionando los procesos existentes, las empresas pueden reducir los despilfarros y optimizar el uso de los recursos eliminando pasos, materiales y esfuerzos innecesarios, racionalizando las operaciones, todo ello al tiempo que se aceleran los ciclos de producción y la prestación de servicios, y se mejora la capacidad de respuesta a las demandas del mercado.
- Aumenta la calidad y la coherencia de los productos. La mejora de procesos influye directamente en la calidad de los productos al estandarizar las operaciones, identificar y resolver los problemas en una fase temprana e incorporar un control de calidad sistemático.
- Reduce costos de forma generalizada. Cada pequeña mejora de un proceso se traducirá finalmente en una reducción de costos. Y cada céntimo ahorrado puede invertirse en nuevas mejoras, creando un efecto de bola de nieve de eficiencia.
- Aumenta la satisfacción del cliente. En el corazón de toda empresa se encuentran sus clientes. La mejora de procesos repercute en la satisfacción del cliente reduciendo los defectos de productos, acortando los tiempos de entrega y facilitando una comunicación transparente.
- Fomenta la innovación y la adaptabilidad. La mejora de procesos fomenta la reevaluación continua de los procesos y la adaptación constante a los nuevos retos.
- Mejora la motivación y el compromiso de los empleados. La mejora de procesos también tiene un impacto significativo en la mano de obra, ya que facilita el trabajo y lo hace más satisfactorio, crea un sentido de pertenencia y fomenta la capacitación y el desarrollo constantes.
Por lo tanto, la mejora de los procesos no consiste únicamente en ajustar los pequeños detalles —al final, se trata de mejorar el panorama general.
Pasos esenciales para una mejora de procesos eficaz
La mejora de procesos en la industria de la fabricación es un proceso sistemático que implica varios pasos críticos que preparan el camino hacia la eficacia y la excelencia. Comprender y aplicar estos pasos es crucial para cualquier fabricante que desee mejorar sus operaciones.
- Evaluación del estado actual. El primer paso es una evaluación exhaustiva de sus procesos de fabricación actuales. Esto implica identificar los puntos fuertes, los puntos débiles, las oportunidades y las amenazas de sus operaciones. El uso de herramientas como el mapa del flujo de valor puede ser increíblemente útil para visualizar todo el flujo del proceso y ayudarle a identificar las áreas que requieren atención.
- Establecer objetivos claros y alcanzables. Una vez concluida la evaluación, es fundamental establecer objetivos específicos, medibles, alcanzables, pertinentes y con plazos concretos (SMART). Estos objetivos servirán de guía para su plan de mejora de procesos, garantizando que todos los esfuerzos estén alineados y enfocados.
- Seleccionar la metodología adecuada. Una vez establecidos los objetivos, el siguiente paso es elegir la metodología de mejora de procesos adecuada que se ajuste a sus objetivos. Ya sea Lean, Six Sigma o Kaizen, cada metodología ofrece herramientas y técnicas únicas para abordar distintos tipos de ineficiencias.
- Aplicación de los cambios. Esta etapa consiste en poner en práctica la metodología elegida. Puede significar reorganizar el flujo de trabajo, adoptar nuevas tecnologías o cambiar determinados procedimientos operativos. La clave está en empezar poco a poco con programas piloto o pruebas para comprobar la eficacia de estos cambios antes de ponerlos en marcha a gran escala.
- Seguimiento y ajuste. La supervisión continua de los cambios aplicados es vital. Esto implica el seguimiento de los indicadores clave de rendimiento (KPIs) y revisar periódicamente los procesos para asegurarse de que cumplen los objetivos fijados. A partir de ahí, pueden hacerse ajustes para optimizar aún más los procesos.
- Mantener las mejoras. Por último, la atención se centra en mantener las mejoras realizadas. Para ello es necesario integrar los cambios en los procesos en la cultura de la empresa, mediante la incorporación, la capacitación continua, la documentación y el establecimiento de nuevas normas y procedimientos.
Cada uno de estos pasos desempeña un papel crucial en el proceso de mejora, ofreciendo un enfoque estructurado para alcanzar la excelencia operativa en la fabricación.
Identificación de áreas de mejora de procesos
La piedra angular del éxito de cualquier iniciativa de mejora de procesos consiste en identificar con precisión las áreas en las que se producen ineficiencias y cuellos de botella. Esta etapa de evaluación crítica es donde comienza la mejora continua, sentando las bases para una transformación que se alinea estrechamente con los objetivos empresariales y la satisfacción del cliente.
Comprender el flujo de trabajo y la asignación de procesos
Una inmersión profunda en el proceso actual utilizando herramientas como diagramas de flujo y mapas de flujo de valor ilumina el camino que siguen los productos desde las materias primas hasta la entrega al cliente. Esta visualización ayuda a detectar redundancias, complejidades innecesarias y cuellos de botella que dificultan el flujo de operaciones y afectan la rentabilidad.
Aprovechar la información basada en datos
Un enfoque basado en datos para identificar ineficiencias implica analizar métricas y KPIs que reflejen la salud de los procesos existentes. Este análisis cuantitativo ayuda a comprender la variabilidad de la producción y orienta el proceso de toma de decisiones para aplicar cambios.
Involucrar a los miembros del equipo en la mejora continua de los procesos
La participación de los empleados en el proceso de mejora tiene un valor incalculable. Los miembros del equipo que participan directamente en las operaciones cotidianas suelen tener ideas sobre las causas raíz de las ineficiencias que pueden no ser inmediatamente evidentes desde el punto de vista de la dirección. Sus aportaciones pueden dar lugar a iniciativas de mejora de gran impacto.
Análisis centrado en el cliente
Finalmente, el objetivo de cualquier proceso de fabricación es satisfacer o superar las expectativas del cliente. Los comentarios de los clientes proporcionan información directa sobre las áreas en las que se puede optimizar el proceso de fabricación para mejorar la experiencia del cliente.
Técnicas y estrategias comunes de mejora de procesos
Una vez comprendidas claramente las áreas que necesitan mejoras, la atención pasa a centrarse en la selección y aplicación de las metodologías de mejora de procesos más adecuadas.
Fabricación ajustada y Six Sigma
La fabricación ajustada se centra en minimizar los despilfarros dentro de los sistemas de fabricación al tiempo que maximiza la productividad. Identifica las actividades sin valor añadido y las elimina, racionalizando las operaciones para mejorar la eficiencia y reducir los costos. Six Sigma, por su parte, pretende reducir la variación de los procesos y mejorar la calidad identificando los defectos, comprendiendo sus causas y aplicando soluciones basadas en datos y análisis estadísticos.
Juntas, estas metodologías crean una potente herramienta de mejora de procesos al combinar las estrategias de reducción de despilfarros y optimización de flujos de trabajo de Lean con el enfoque de calidad y precisión de Six Sigma. Este enfoque integrado conduce a operaciones más eficientes, productos de mayor calidad y una mayor satisfacción del cliente, lo que lo convierte en una poderosa herramienta para las empresas que pretenden mejorar su competitividad y rendimiento operativo.
Teoría de las restricciones
La teoría de las restricciones es una filosofía de gestión que identifica el factor más limitante de un sistema de producción —denominado restricción— y mejora o elimina sistemáticamente este cuello de botella. Al centrarse en la limitación, la TOC (teoría de las restricciones) trata de gestionar el flujo de trabajo y los recursos para lograr el máximo rendimiento del sistema.
El principio se basa en el entendimiento de que cualquier sistema complejo puede mejorarse sustancialmente concentrándose en el eslabón más débil. La implementación de la TOC implica identificar la limitación, aprovecharla al máximo y, a continuación, hacer mejoras iterativas para elevar el rendimiento de todo el sistema.
Análisis de la causa raíz
El análisis de la causa raíz es un método de resolución de problemas utilizado para determinar la causa fundamental de un problema o falla, en lugar de limitarse a tratar sus síntomas. El RCA (por sus siglas en inglés) parte de la base de que es más eficaz prevenir y resolver sistemáticamente los problemas de base que limitarse a tratarlos cuando se producen.
El proceso consiste en identificar las causas raíz de los problemas o sucesos utilizando herramientas como los 5 porqués, diagramas de espina de pescado, etc., y luego desarrollar soluciones adecuadas para evitar que se repitan. Se utiliza ampliamente en diversos sectores para mejorar la seguridad, la calidad y la eficiencia, ya que garantiza que las medidas correctivas aborden los verdaderos orígenes de cualquier problema, lo que conduce a soluciones más sostenibles y a largo plazo.
Kaizen o mejora continua
El concepto japonés de Kaizen que hace hincapié en los cambios pequeños y continuos, fomenta una cultura en la que todos los empleados, desde las partes interesadas hasta los trabajadores de línea, buscan activamente formas de mejorar. Estas actividades no solo agilizan los flujos de trabajo, sino que también fomentan el compromiso de los empleados y el trabajo en equipo, creando potencialmente un bucle de retroalimentación positiva.
Gestión de la calidad total (TQM) y ciclo PDCA
La visión integral de la gestión de la calidad total (TQM por sus siglas en inglés) sobre la mejora de toda la organización, respaldada por el ciclo Planificar-Hacer-Verificar-Actuar (PDCA – Plan-Do-Check-Act), garantiza que los proyectos de mejora de procesos empresariales se ejecuten sistemáticamente y se ajusten a los objetivos generales de la empresa.
La gestión de la calidad total es un enfoque amplio y estructurado de la gestión organizativa que pretende mejorar la calidad de los productos y servicios mediante perfeccionamientos continuos en respuesta a una retroalimentación continua. La TQM requiere la participación de todos los miembros de una organización en la mejora de procesos, productos, servicios y la cultura en la que trabajan. Los principios de la TQM se centran en la satisfacción del cliente, la mejora de procesos y la participación de los empleados a todos los niveles.
El ciclo Planificar-Hacer-Verificar-Actuar es un modelo de cuatro pasos para un proceso eficaz de mejora continua. Es un elemento fundamental de los sistemas de gestión de la calidad, incluida la TQM:
Planificar: Identificar un objetivo o problema y desarrollar una estrategia para abordarlo.
Hacer: Aplicar el plan a pequeña escala para comprobar su eficacia.
Verificar: Evaluar los resultados de la prueba para determinar si se ha conseguido el resultado deseado.
Actuar: Si el plan ha tenido éxito, aplíquelo a mayor escala. Si no, perfeccione el plan y vuelva a empezar el ciclo.
El PDCA fomenta una cultura de mejora continua en la que los procesos se evalúan y perfeccionan constantemente. Proporciona un sistema sencillo pero eficaz para la resolución de problemas y la mejora de la calidad, garantizando que las organizaciones puedan adaptarse y responder a los cambios y retos con eficacia.
Automatización de procesos
La automatización de procesos consiste en utilizar la tecnología para automatizar procesos y funciones empresariales complejos más allá de las actividades convencionales de manipulación de datos y mantenimiento de registros. Integra aplicaciones informáticas, maquinaria y herramientas digitales para realizar tareas con una intervención humana mínima.
La automatización de procesos puede abarcar desde tareas sencillas, como la generación automática de informes, hasta operaciones complejas, como la automatización robótica de procesos (RPA), en la que los robots imitan las acciones humanas para completar tareas repetitivas.
Al agilizar los flujos de trabajo con la automatización, las empresas pueden lograr resultados más coherentes, mejorar los tiempos de respuesta y liberar recursos humanos para actividades más estratégicas, creativas o complejas de resolución de problemas. Este enfoque basado en la tecnología favorece la escalabilidad, mejora la precisión y puede reducir significativamente los costos operativos, por lo que es un componente clave de las estrategias de transformación digital y mejora de procesos en las organizaciones que aspiran a una alta eficiencia e innovación.
Métricas y control continuo
El establecimiento de puntos de referencia y la supervisión continua del rendimiento mediante datos en tiempo real y KPI garantizan que los esfuerzos de mejora se midan, evalúen y perfeccionen con el tiempo. Este proceso continuo garantiza que las operaciones de fabricación se mantengan alineadas con la evolución de los objetivos empresariales y las demandas del mercado.
El papel de ERP y MRP en la mejora de procesos
La planificación de recursos empresariales (ERP) y planificación de recursos de fabricación (MRP) desempeñan un papel fundamental en la mejora de procesos. Al integrar diversas facetas de las operaciones, como la planificación de la producción, la planificación de materiales, las compras y la programación de la producción, estos sistemas proporcionan una plataforma unificada que agiliza los flujos de trabajo, aumenta la eficiencia de la producción y facilita la gestión eficaz de los proyectos y los procesos empresariales.
Los sistemas ERP/MRP mejoran la planificación de la producción al ofrecer visibilidad en tiempo real de la demanda, los niveles de inventario y la capacidad de producción. Esto permite a las organizaciones anticiparse a los cambios del mercado y ajustar los programas de producción en consecuencia, garantizando niveles óptimos de inventario mediante notificaciones de existencias bajas y reabastecimiento asistido. Los módulos de planificación de materiales y compras de estos sistemas aumentan aún más la mejora de procesos al garantizar que los materiales se piden a tiempo y en las cantidades adecuadas, reduciendo los despilfarros y los costos de almacenamiento.
La automatización de tareas repetitivas, como generar pedidos de compra o programar la producción, no sólo aumenta la eficiencia de la producción, sino que permite al personal centrarse en actividades de mayor valor. Este cambio contribuye significativamente a los esfuerzos de mejora de procesos al fomentar la innovación y la eficiencia.
El control de los indicadores clave de rendimiento (KPI) es otra característica fundamental de los sistemas ERP/MRP, que permite a las empresas realizar un seguimiento del rendimiento en relación con sus objetivos estratégicos. Métricas como los tiempos de entrega de la producción, el costo por unidad y la eficacia general de los equipos (OEE) están fácilmente disponibles, lo que facilita la identificación de áreas de mejora. Estos sistemas también pueden facilitar las estimaciones de costos y tiempos de entrega, con estimaciones precisas siempre a unos pocos clics de distancia.
Los sistemas ERP/MRP ofrecen una plantilla para estandarizar los procesos, lo que resulta esencial para escalar las operaciones y garantizar la coherencia en toda la organización. Cuando se introduce un nuevo proceso, el sistema puede gestionar la transición sin problemas, integrando el nuevo procedimiento con los flujos de trabajo existentes y minimizando las interrupciones.
En resumen, los sistemas de software ERP/MRP son herramientas indispensables para las organizaciones que pretenden optimizar sus procesos empresariales y de producción. Gracias a una programación mejorada, una gestión eficaz de los recursos y un seguimiento exhaustivo de los indicadores clave de rendimiento (KPI), estos sistemas pueden apoyar la mejora continua independientemente de la metodología utilizada, lo que los convierte en una piedra angular de los esfuerzos modernos de mejora de procesos.
Principales aspectos a tener en cuenta
- La mejora de procesos es un esfuerzo continuo vital para mantener la competitividad y satisfacer las cambiantes demandas de los clientes. Implica aumentar la eficacia operativa, mejorar la calidad del producto, reducir costos y aumentar la satisfacción del cliente mediante el análisis sistemático y la mejora de procesos empresariales.
- Una eficaz mejora de procesos de fabricación requiere un enfoque holístico que integre metodologías como la fabricación ajustada, Six Sigma y Kaizen con soluciones modernas como el software ERP para optimizar las operaciones, mejorar la calidad y reducir los costos.
- La mejora de procesos implica pasos cruciales como la evaluación del estado actual, el establecimiento de objetivos claros y alcanzables, la selección de la metodología adecuada, la aplicación de los cambios, la supervisión y el ajuste, y el mantenimiento de las mejoras. Este enfoque estructurado garantiza la excelencia operativa.
- El éxito de la mejora de procesos comienza con la identificación precisa de las áreas de ineficacia y los cuellos de botella mediante técnicas como el análisis del flujo de trabajo, la información basada en datos, la participación de los empleados y el análisis centrado en el cliente.
- Los sistemas de software ERP y MRP son cruciales para respaldar los esfuerzos de mejora de procesos, ya que proporcionan visibilidad en tiempo real de la planificación de la producción, la planificación de materiales y la programación, automatizan las tareas repetitivas, facilitan el seguimiento de los KPI y estandarizan los procesos para lograr eficiencia e innovación.
Preguntas frecuentes
Las empresas miden la eficacia de las metodologías de mejora de procesos fijando objetivos específicos y medibles desde el principio y haciendo un seguimiento de los indicadores clave de rendimiento (KPI) a lo largo del tiempo. Estos KPI pueden incluir métricas como la reducción de los tiempos de producción, la disminución de las tasas de defectos, el aumento de las puntuaciones de satisfacción del cliente y el ahorro de costos, lo que permite a las organizaciones evaluar cuantitativamente el impacto de sus iniciativas.
Las organizaciones suelen enfrentarse a retos como la resistencia al cambio por parte de los empleados, la complejidad de la migración de datos y la adaptación del nuevo sistema a los flujos de trabajo existentes. Las empresas pueden superar las dificultades que plantea la integración de nuevas tecnologías, como los sistemas ERP/MRP, empezando por un programa piloto para resolver los problemas antes de la implementación a gran escala, buscar asesoramiento de expertos o apoyo de proveedores para actividades de capacitación y configuración personalizada, e involucrando a los empleados en las primeras fases del proceso para garantizar su aceptación y una transición fluida.
Los pequeños y medianos fabricantes pueden poner en marcha sus esfuerzos de mejora de procesos aprovechando el software ERP basado en la nube, que ofrece escalabilidad, flexibilidad y rentabilidad sin necesidad de grandes inversiones iniciales en hardware. Esto les permite acceder a herramientas sofisticadas para la planificación de la producción, la gestión de inventarios y la supervisión de los indicadores clave de rendimiento (KPI), lo que les permite tomar decisiones y realizar mejoras basadas en datos incluso con recursos limitados. Empezar con proyectos específicos de gran impacto y ampliar gradualmente el uso de estos sistemas puede proporcionar una base sólida para la mejora continua de los procesos.
También le puede interesar: Los 8 despilfarros de la fabricación ajustada