Mejora continua – Implementación de la mejora continua en la fabricación
En el competitivo panorama actual de la fabricación, la mejora continua (CI por sus siglas en inglés) es una estrategia crucial para aumentar la eficiencia, la calidad y el rendimiento general de la empresa. En este artículo, exploramos varios modelos de mejora continua y proporcionamos ideas prácticas sobre cómo los fabricantes pueden implementar y beneficiarse de las iniciativas de CI.
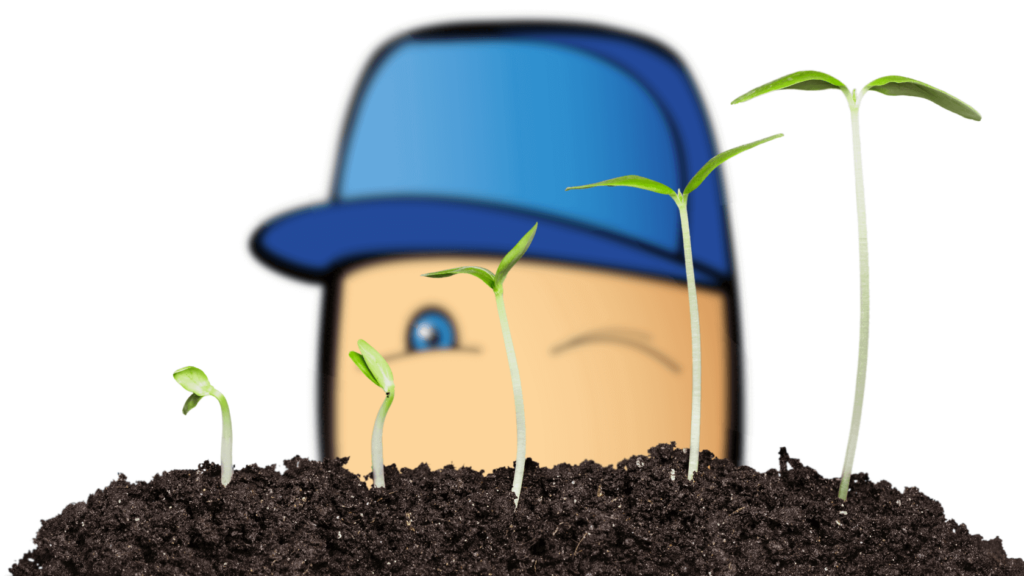
¿Qué es la mejora continua?
La mejora continua (CI) es un proceso estratégico que consiste en identificar, analizar y aplicar cíclicamente mejoras en los flujos de trabajo y los productos. El objetivo de la mejora continua es aumentar la productividad y la eficacia de los procesos de fabricación, minimizando al mismo tiempo los despilfarros y los defectos. Estas mejoras pueden variar enormemente en cuanto a su naturaleza y alcance. Pueden ser incrementales a lo largo del tiempo o lograrse mediante avances significativos. Un aspecto clave de la CI es que se basa en datos empíricos e indicadores clave de rendimiento para orientar la toma de decisiones, garantizando que las mejoras generen beneficios reales.
El rápido ritmo de los avances tecnológicos y las expectativas cambiantes de los consumidores hacen que la CI sea crucial para las empresas de fabricación modernas. Adoptar la CI de una forma u otra permite a las empresas aumentar su adaptabilidad y ajustar sus operaciones para satisfacer las demandas cambiantes de los mercados, manteniendo al mismo tiempo una alta calidad y eficiencia.
La CI tiene mayor importancia para las pequeñas y medianas empresas (PYME), donde los recursos suelen ser más limitados y el impacto de las ineficiencias puede ser más perjudicial que en las grandes organizaciones. Gracias a ella, las PYME pueden optimizar el uso de sus recursos, racionalizar sus operaciones y mejorar su competitividad, a menudo sin necesidad de grandes inversiones de capital.
CI incremental vs CI de avance
La CI incremental consiste en introducir pequeñas mejoras de forma regular a lo largo del tiempo. Los cambios incrementales suelen ser más fáciles de aplicar y menos arriesgados que introducir nuevos procesos a gran escala. La CI incremental se centra en perfeccionar los procesos existentes, reducir los despilfarros y mejorar la eficiencia gradualmente.
La CI de avance, por su parte, implica cambios importantes cuyo objetivo es lograr mejoras significativas con rapidez. Este enfoque puede incluir la implementación de nuevas tecnologías, la revisión de los procesos de producción o el replanteamiento de estrategias empresariales completas. Aunque potencialmente más impactantes, los proyectos de CI de avance conllevan mayores riesgos y requieren inversiones sustanciales y esfuerzos de gestión del cambio más exhaustivos.
Beneficios de la mejora continua
Las iniciativas de mejora continua aportan un sinfín de beneficios a las organizaciones, mejorando diversos aspectos de las operaciones y produciendo ganancias sustanciales a largo plazo. A continuación se detallan las principales ventajas de integrar las prácticas de mejora continua en una empresa.
Eficacia operativa
La mejora continua tiene como objetivo estratégico la eficiencia operativa mediante la racionalización de los procesos, la eliminación de pasos innecesarios y la optimización del uso de los recursos, al tiempo que fomenta una mentalidad proactiva entre los empleados. Este enfoque da lugar a ciclos de producción más rápidos y a una utilización más eficiente de la mano de obra. Como resultado, las organizaciones pueden lograr una mayor productividad con menos recursos, lo que en última instancia conduce a una mayor rentabilidad y competitividad.
Mejora de la calidad
La mejora de la calidad es otro resultado fundamental de la CI. Al evaluar y mejorar continuamente los procesos, las personas y los productos, las organizaciones pueden reducir significativamente la incidencia de defectos y errores. De este modo, la CI mejora directamente las prácticas de garantía de calidad y promueve la elaboración de productos de mayor calidad que satisfagan las necesidades de los clientes, al tiempo que mejora la reputación de la empresa, encaminándola hacia el éxito a largo plazo.
Control de costos
Más eficiencia equivale a menos costos. Sin embargo, además de reducir el gasto, la CI proporciona una comprensión más profunda de dónde se incurre en los costos junto con formas proactivas de optimizar el costo de la calidad, destacando las oportunidades de ahorro que no comprometen la calidad. Al conocer las complejidades de los factores de costo dentro de los procesos, las organizaciones pueden tomar decisiones informadas que equilibren la eficiencia de costos con la calidad de los resultados, lo que conduce a prácticas empresariales más sostenibles.
Compromiso de los empleados
El compromiso de los empleados es un aspecto crucial de la mejora continua, ya que aumenta significativamente el sentido de pertenencia y responsabilidad de los empleados hacia su trabajo. Esta mayor implicación conduce a una mayor motivación y compromiso, ya que los miembros del equipo se sienten más conectados a los resultados de sus esfuerzos.
Muchas iniciativas de CI incorporan la participación activa, animando a los empleados de todos los niveles a aportar ideas y soluciones. Esta participación activa fomenta el desarrollo personal y profesional, al tiempo que contribuye directamente a un entorno de trabajo más dinámico y satisfactorio. Al vincular los esfuerzos individuales a los objetivos más amplios de la organización, los empleados pueden ver las repercusiones tangibles de sus contribuciones, lo que aumenta su compromiso.
Reducción de despilfarros
Las metodologías de CI, en particular las derivadas de las prácticas Lean, se centran en gran medida en la reducción de despilfarros, no sólo físicos, sino también de tiempo, energía, costos y mano de obra. Identificar y eliminar las prácticas que generan despilfarro en todas las áreas operativas ayuda a conservar los recursos y a adoptar prácticas sostenibles, esenciales para la eficiencia operativa y la creciente atención mundial a la conciencia medioambiental.
Oportunidad e innovación
La mejora continua fomenta un entorno propicio para la innovación. Al fomentar una mentalidad que siempre busca mejores formas de hacer las cosas, las organizaciones se vuelven más innovadoras de forma natural. Esta búsqueda continua de mejoras puede dar lugar a grandes avances en productos y procesos, abriendo nuevas oportunidades de crecimiento y competitividad.
Mayor satisfacción del cliente
Mejorar la satisfacción del cliente es otro beneficio significativo de la CI. Al mejorar continuamente la calidad de los productos y servicios y responder de forma proactiva a las opiniones de los clientes, las empresas pueden establecer relaciones más sólidas con ellos. Los clientes satisfechos son más propensos a ser fieles, a repetir la compra y a remitir nuevos clientes, lo que contribuye a un crecimiento sostenible de la empresa.
Reducción de riesgos
La aplicación de prácticas de CI ayuda a mitigar los riesgos asociados a los procesos empresariales. Al evaluar y perfeccionar continuamente las operaciones, las empresas pueden identificar a tiempo los riesgos potenciales y aplicar medidas preventivas. Este enfoque proactivo de la gestión de riesgos protege a la empresa contra fallos operativos, al tiempo que mejora su cumplimiento de las normas y reglamentos del sector.
Modelos centrales de mejora continua
La mejora continua no es una metodología única, sino más bien un espectro de estrategias que pueden adaptarse a las necesidades específicas de una organización. Estos modelos proporcionan marcos a través de los cuales las empresas pueden abordar metódicamente la mejora de los procesos de manera continua. A continuación analizamos cuatro modelos fundamentales de mejora continua, cada uno con sus propios principios y prácticas adaptados a diferentes necesidades y objetivos operativos.
Kaizen
Kaizen, que se traduce como “cambiar para mejorar”, es una filosofía japonesa que hace hincapié en la mejora continua e incremental en la que participan todos los empleados, desde la alta dirección hasta los trabajadores de la cadena de ensamblaje. Es una de las metodologías esenciales que dieron origen a la mejora continua como proceso sistemático de mejora del rendimiento en la fabricación. Era una parte esencial de The Toyota Way, un conjunto de principios desarrollados en Toyota Motor Corporation para introducir la innovación en la cultura organizativa.
Kaizen fomenta las sugerencias y la participación de todos los empleados para crear un entorno en el que todos se sientan capaces de contribuir a los esfuerzos de mejora. El modelo se basa en la idea de que los pequeños cambios positivos y continuos pueden reportar grandes beneficios. Entre las prácticas habituales del Kaizen figuran la organización de sesiones de intercambio de ideas, la mejora de la funcionalidad del espacio de trabajo y la simplificación de procesos.
PDCA (Planificar-Hacer-Verificar-Actuar)
El ciclo PDCA, también conocido como ciclo Shewhart o ciclo de control, es una metodología iterativa de cuatro pasos para lograr la mejora continua de los procesos empresariales. Proporciona un enfoque sencillo pero eficaz para resolver problemas y gestionar cambios, garantizando que las ideas se apliquen de forma eficiente, se pongan a prueba y se optimicen. El ciclo fue popularizado por el Dr. W. Edwards Deming, considerado por muchos el padre del control de calidad moderno. Sin embargo, el PDCA fue desarrollado originalmente por el Dr. Walter A. Shewhart, de los Laboratorios Bell.
- Planificar. El primer paso consiste en identificar un problema y formular una hipótesis sobre cómo resolverlo. Incluye analizar la situación actual, fijar objetivos y planificar los cambios necesarios para alcanzarlos. La planificación detallada en esta fase garantiza que los cambios en los procesos estén bien pensados y se ajusten a los objetivos de la organización.
- Hacer. Esta fase consiste en aplicar el cambio previsto a pequeña escala. El propósito es probar el cambio y ver si aporta mejoras. Actúa como un periodo de prueba en el que se minimizan las interrupciones y se puede observar la aplicabilidad en el mundo real de los cambios propuestos.
- Verificar. Tras implementar el cambio, la fase de verificación evalúa los resultados en relación con los objetivos previstos. Se recopilan y analizan los datos y resultados para saber si los cambios han dado lugar a una mejora. Esto es fundamental porque determina si la hipótesis está confirmada o si se necesitan más ajustes.
- Actuar. Si los resultados de la fase de verificación son satisfactorios, los cambios del proceso se normalizan y se aplican a mayor escala en toda la organización. Si, por el contrario, el cambio no conduce a mejoras, los conocimientos adquiridos se utilizan para refinar la hipótesis, y el ciclo se repite con un nuevo plan.
La naturaleza iterativa del ciclo PDCA permite perfeccionamientos y ajustes continuos, lo que lo convierte en una herramienta inestimable para lograr la mejora continua dentro de cualquier organización. Al pasar repetidamente por estas etapas, las empresas pueden fomentar una cultura de aprendizaje y mejora sostenidos, aumentando progresivamente la eficiencia y eficacia de los procesos.
Fabricación ajustada y Just-in-Time
La fabricación ajustada y el Just-in-Time (JIT) son dos filosofías estrechamente relacionadas que se centran en maximizar la eficiencia y reducir los despilfarros en el proceso de fabricación. Ambas son esenciales para la mejora continua y comparten el objetivo último de aumentar la capacidad de respuesta y la rentabilidad de las operaciones.
La fabricación ajustada se centra en la eliminación de los despilfarros, definidos como todo aquello que no aporta valor añadido al cliente y a menudo denominados los 8 despilfarros de Lean. La metodología Lean lo consigue racionalizando los procesos de producción, reduciendo los tiempos de ciclo, mejorando la calidad del producto, etc. Hace hincapié en comprender el valor para el cliente, alinear los procesos para ofrecer ese valor y mejorar continuamente estos procesos basándose en los comentarios de los clientes y en datos empíricos. Técnicas como el mapa del flujo de valor, el flujo continuo y la capacitación de los empleados son fundamentales en Lean, ya que contribuyen a reducir los despilfarros derivados de la sobreproducción, los defectos, el transporte innecesario, etc.
El Just-in-Time (JIT), a menudo implementado como elemento clave de la fabricación ajustada, se centra específicamente en la gestión de inventarios y en los flujos de trabajo de fabricación de tipo Pull. La idea central del JIT es minimizar el inventario y reducir los despilfarros asociados al almacenamiento de materiales no utilizados. Al producir y entregar los componentes sólo cuando se necesitan, el JIT contribuye a reducir los costos y a aumentar la eficacia de los sistemas de producción. Este enfoque requiere una coordinación precisa y a menudo depende en gran medida de las relaciones con los proveedores y de previsiones fiables de la demanda para evitar retrasos y desabastecimientos.
La sinergia de Lean y JIT (Justo a tiempo) es evidente, ya que la reducción del inventario contribuye directamente a los objetivos de Lean al disminuir los costos de mantenimiento y reducir el riesgo de deterioro u obsolescencia. Además, el JIT amplifica el enfoque Lean hacia la calidad, ya que los defectos y los problemas se hacen más evidentes y pueden tratarse con mayor rapidez al haber menos inventarios y procesos en curso en el sistema.
Continúe leyendo acerca de la Fabricación justo a tiempo (JIT).
Six Sigma
Six Sigma es una metodología rigurosa, basada en datos, cuyo objetivo es eliminar defectos e ineficiencias en cualquier proceso, aumentando la calidad y mejorando los resultados. Originada en los años 80 en Motorola, Six Sigma se desarrolló como una forma de mejorar los procesos de fabricación mediante métodos estadísticos que reducen la variabilidad en los resultados de los procesos. Se centra en identificar y eliminar las causas de los defectos y minimizar la variabilidad en los procesos empresariales y de fabricación mediante un conjunto de métodos de gestión de la calidad.
La metodología se estructura principalmente en torno al marco DMAIC (por sus siglas en inglés): Definir, Medir, Analizar, Mejorar y Controlar.
- Definir los problemas, los objetivos del proyecto y las demandas de los clientes (internos y externos).
- Medir los aspectos clave del proceso actual y recopilar los datos pertinentes.
- Analizar los datos para investigar y verificar las relaciones causa-efecto. Determinar cuáles son las relaciones e intentar asegurarse de que se han tenido en cuenta todos los factores.
- Mejorar u optimizar el proceso actual basándose en el análisis de datos mediante técnicas como el diseño de experimentos, el poka-yoke (comprobación de errores) y el trabajo estándar para crear nuevos procesos para el futuro.
- Controlar el proceso del estado futuro para garantizar que cualquier variación del objetivo se corrige antes de que se traduzca en defectos. Esto ayuda a mantener los logros institucionalizando el proceso mejorado mediante la redacción de políticas, procedimientos y controles, y aplicándolos en toda la organización.
Los profesionales de Six Sigma suelen utilizar los términos Cinturón Negro, Cinturón Verde, etc., para indicar un nivel de competencia y formación en estos métodos. Estas certificaciones reflejan la capacidad de la persona para dirigir equipos de proyecto, definir proyectos de mejora que se ajusten a los objetivos estratégicos y aplicar la metodología rigurosa para lograr mejoras cuantificables. Six Sigma no son sólo técnicas, sino también una filosofía que impulsa una cultura de mejora a través del análisis disciplinado de datos y la toma de decisiones.
Otras metodologías asociadas a la mejora continua
Además de los modelos mencionados en los que muchas empresas basan sus esfuerzos de CI, analicemos también cuatro estrategias sistemáticas para adoptar y fomentar diversos principios de la mejora continua en la fabricación.
Análisis de la causa raíz
El análisis de la causa raíz (RCA por sus siglas en inglés) es un enfoque metódico para identificar las causas que originan los problemas o incidentes con el fin de resolverlos eficazmente. El RCA se basa en el principio de que para resolver eficazmente un problema no basta con tratar sus síntomas, sino que hay que identificar y abordar sus causas profundas. En la fabricación, esto puede conducir a mejoras significativas en la calidad del producto, la eficiencia y la seguridad de los empleados.
Una herramienta popular de RCA es el método de los 5 porqués, que consiste en preguntarse “¿por qué?” varias veces hasta descubrir la causa fundamental de un problema. Por ejemplo, si una máquina deja de funcionar, el primer “por qué” puede revelar que ha fallado una pieza. Si se vuelve a preguntar “¿por qué?”, se descubrirá que el mantenimiento de la pieza era inadecuado. El cuestionamiento continuo llevaría a una comprensión más profunda, que tal vez revelaría la falta de mantenimiento programado como la causa raíz. Al abordar esto, la solución se hace evidente: mejorar el programa de mantenimiento.
Teoría de las restricciones
La teoría de las restricciones (TOC) es una metodología que se centra en identificar el factor limitante más importante (es decir, la restricción) que se interpone en la consecución de un objetivo y, a continuación, mejorar sistemáticamente esa restricción hasta que deje de limitar el rendimiento. Desarrollada por el Dr. Eliyahu M. Goldratt en su libro de 1984 The Goal, la TOC propone que casi todos los sistemas complejos, incluidos los procesos de fabricación, pueden mejorarse sustancialmente centrándose en sus restricciones.
La TOC utiliza una metodología conocida como los cinco pasos del enfoque para abordar y optimizar las restricciones identificadas. Estos pasos proporcionan un enfoque sistemático para gestionar las mejoras y están diseñados para garantizar un avance continuo hacia los objetivos de la organización. Los pasos son:
- Identificar la restricción. El primer paso consiste en determinar la parte específica del proceso que limita la capacidad de todo el sistema para lograr un mayor rendimiento. Puede tratarse de una máquina, una política, un procedimiento o incluso una demanda del mercado.
- Explotar la restricción. Una vez identificada la restricción, hay que encontrar la manera de maximizar su rendimiento sin grandes inversiones. Esto significa aprovechar al máximo lo que se tiene. Por ejemplo, asegurándose de que la restricción nunca esté inactiva, reduciendo las ineficiencias inmediatamente antes o en el punto de restricción, o preparando los materiales con antelación.
- Subordinar todo lo demás. El tercer paso consiste en adaptar todo el sistema o los procesos a las necesidades del proceso restringido. Esto significa hacer que los demás elementos del proceso funcionen de manera que la restricción pueda funcionar con la máxima eficacia.
- Elevar la restricción. Si la restricción sigue existiendo después de explotarla y subordinarla, el siguiente paso es introducir cambios permanentes para superarla. Esto podría implicar aumentar la capacidad en el cuello de botella, añadir recursos o externalizar partes del proceso.
- Repetir el proceso. Este último paso enfatiza el interés de la TOC por la mejora continua. Una vez superada la restricción actual, vuelva al primer paso e identifique la siguiente restricción. El objetivo es lograr un ciclo continuo de mejora.
Al centrarse en el elemento más restrictivo del proceso empresarial o de fabricación, la TOC ayuda a las organizaciones a conseguir mejoras significativas y sostenibles en el rendimiento. La TOC anima a las empresas a considerar positivamente las restricciones como oportunidades y catalizadores de la innovación y el crecimiento.
Las 5S
Al igual que Lean y Kaizen, el sistema 5S es otra metodología japonesa asociada a menudo con la mejora continua. Las 5S son un enfoque sistemático de la organización y estandarización del lugar de trabajo que ayuda a mejorar la eficiencia y a fomentar el sentido de pertenencia entre los empleados. Los principios de las 5S incluyen:
- Seiri (Clasificar): Elimine las herramientas, piezas e instrucciones innecesarias. Conserve sólo los artículos esenciales y elimine lo que no sea necesario, eliminando así posibles obstáculos para el trabajo.
- Seiton (Poner en orden): Disponga e identifique los elementos necesarios para que sean fácilmente accesibles y utilizables. Coloque los componentes en función de su uso, con los artículos de uso frecuente más cerca de las zonas de trabajo.
- Seiso (Limpiar): Limpiar el espacio de trabajo y el equipo con regularidad para mantener los estándares y garantizar que los defectos se manifiesten más rápidamente.
- Seiketsu (Estandarizar): Las prácticas de trabajo deben ser coherentes y estandarizadas. Todos los puestos de trabajo para un trabajo en particular deben ser idénticos.
- Shitsuke (Mantener): Mantener y revisar las normas. Una vez establecidas las 4S anteriores, se convierten en la nueva forma de operar. Manténgase centrado en esta nueva forma y no permita que se produzca un retroceso gradual a las viejas formas.
Kanban
Kanban es un sistema de gestión visual que apoya la fabricación JIT y Lean controlando la cadena logística desde el punto de vista de la producción y armonizando así la producción con la demanda. En Kanban, los elementos de trabajo se visualizan para que los participantes comprendan claramente el progreso y los flujos del proceso, y para limitar el trabajo en proceso en función de la capacidad del sistema.
Este sistema está diseñado para promover la eficacia limitando los proyectos en curso a un nivel manejable. Esto puede evitar la sobreproducción, uno de los principales desperdicios en la fabricación ajustada. Kanban fomenta un flujo de trabajo fluido y permite identificar y resolver rápidamente los cuellos de botella.
El proceso de mejora continua
La implementación de la mejora continua es un proceso dinámico e iterativo. Las aplicaciones y etapas específicas de la mejora continua pueden variar considerablemente según las empresas, los sectores y los objetivos finales. Sin embargo, independientemente de la metodología que se adopte, las herramientas de mejora continua se centran principalmente en racionalizar los procesos, eliminar los despilfarros y mejorar la productividad general.
La variabilidad reside en cómo se priorizan y alcanzan estos objetivos, y cómo influyen en ellos las necesidades organizativas únicas, las condiciones del mercado y los recursos disponibles. Esto hace que la CI sea adaptable, permitiendo a cada organización adaptarla a su contexto específico.
Sin embargo, el proceso de CI tiene algunos principios comunes, independientemente del dónde, el quién y el cómo. A menudo implica una serie cíclica de pasos: planificación, ejecución, evaluación y mejoramiento. Esto ayuda a garantizar que las mejoras se basen en datos precisos y reacciones reales, que los cambios positivos se mantengan y amplíen con el tiempo, etc.
Ejemplo de aplicación de la CI
Para implementar eficazmente un proceso de CI, las organizaciones suelen seguir una ruta similar a los siguientes pasos:
- Identificar objetivos. El primer paso para que una iniciativa de CI tenga éxito es definir claramente lo que se quiere conseguir. Una buena manera de trazar los objetivos es seguir el método SMART, es decir, averiguar si sus metas son específicas, medibles, alcanzables, relevantes y con un plazo determinado. Establecer objetivos claros desde el principio proporciona orientación y un punto de referencia para medir los progresos.
- Establecer y definir el proceso. Una vez fijados los objetivos, el siguiente paso es trazar un mapa de los procesos existentes para detectar ineficiencias y áreas susceptibles de mejora. Un mapa detallado ayuda a comprender el flujo de trabajo y a identificar los cuellos de botella o los puntos del sistema en los que se producen despilfarros.
- Comunicar e implementar el proceso. Tras determinar cómo pueden mejorarse los procesos, el siguiente paso es implementar los cambios. Esto implica no sólo el despliegue físico de nuevos métodos o herramientas, sino también una comunicación eficaz en toda la organización. Asegurarse de que todas las partes interesadas entienden los cambios y las razones que los justifican es crucial para la aceptación y el cumplimiento.
- Hacer seguimiento y medición. Una vez implementados los nuevos procesos, es importante hacer un seguimiento de los resultados y medir los efectos de las mejoras con respecto a los objetivos fijados. Este seguimiento debe utilizar los indicadores clave de rendimiento (KPI) pertinentes para proporcionar información basada en datos sobre el rendimiento de las mejoras.
- Revisar y rehacer. El último paso consiste en revisar los resultados y el proceso general. Esto implica analizar lo que ha funcionado y lo que no, hacer los ajustes necesarios y prepararse para repetir el proceso. La mejora continua consiste en aprender de cada ciclo y estar preparado para introducir cambios continuos que mejoren aún más el sistema.
Buenas prácticas de CI para pequeñas empresas
Para las pequeñas empresas, la aplicación de prácticas de mejora continua puede ser tanto una ventaja estratégica como una necesidad para seguir siendo competitivos en un mercado en rápida evolución. A continuación presentamos cinco buenas prácticas que pueden ayudar a las pequeñas empresas a incorporar eficazmente la CI a sus operaciones:
- Establezca una capacitación y un desarrollo regulares. La mejora continua tiene que ver tanto con la capacitación de los empleados como con la actualización de los procesos. Implementar programas de capacitación periódicos puede ayudar a los empleados a dominar nuevas tecnologías, comprender metodologías de mejora continua como Lean o Six Sigma y aplicar estas habilidades de forma eficaz en su trabajo. Además, el compromiso con la formación continua contribuye a aumentar la satisfacción y la retención de los empleados.
- Aumente la participación de los empleados. Recopile información de aquellos que mejor conocen el trabajo: los empleados. Involucrar a los trabajadores en la práctica ofrece perspectivas valiosas que pueden conducir a mejoras significativas de los procesos. Fomente las ideas a través de encuestas o grupos de reflexión y ponga en marcha mecanismos para que los empleados den regularmente su opinión sobre los procesos. Este enfoque incluyente puede ayudar a mejorar los procesos, pero también empodera a los empleados, lo que se traduce en una plantilla más comprometida.
- Mejore el lugar de trabajo. Mejorar el entorno físico y organizativo del lugar de trabajo puede aumentar la eficacia de las operaciones y la satisfacción de los trabajadores. Esto incluye organizar el espacio de trabajo para que sea eficiente (utilizando conceptos como las 5S), garantizar que se cumplen las normas de seguridad y crear un entorno de trabajo más acogedor y cómodo. Las mejoras en el lugar de trabajo pueden aumentar la productividad y motivar a los empleados para que den lo mejor de sí mismos.
- Implemente la tecnología digital y la automatización. Invertir en tecnología que automatice las tareas repetitivas y agilice los procesos es crucial para las pequeñas empresas. Herramientas como los sistemas de planificación de recursos empresariales (ERP), la gestión de inventarios y el software de seguimiento y análisis pueden aumentar sustancialmente la eficiencia.
- Aproveche IoT y el aprendizaje automático. La integración de las tecnologías de Internet de las cosas (IoT) y aprendizaje automático puede transformar radicalmente los procesos de fabricación. Los dispositivos IoT pueden supervisar y recopilar datos de toda la planta de fabricación en tiempo real, mientras que los algoritmos de aprendizaje automático analizan estos datos para predecir fallas, optimizar las operaciones y mejorar la toma de decisiones. Esto puede dar lugar a una comprensión más profunda, mantenimiento predictivo y procesos de fabricación más inteligentes.
¿Cómo puede ayudar el software de fabricación con la CI?
Los software de fabricación, en particular los sistemas de planificación de recursos de fabricación o sistemas MRP, desempeñan un papel fundamental en el impulso de la mejora continua. Estos sistemas integran varios aspectos de la gestión de la fabricación, desde el control de inventarios y la planificación de la producción hasta la garantía de calidad y la trazabilidad. El software de fabricación proporciona una base sólida para la mejora continua al aumentar la visibilidad, mejorar la comunicación y dotar a los directivos de herramientas de análisis basadas en datos reales de fabricación.
Por ejemplo, MRPeasy ofrece a los pequeños y medianos fabricantes una solución intuitiva y completa que apoya la ejecución y el seguimiento de las estrategias de CI. Permite a las empresas gestionar los programas de producción, el inventario, las relaciones con los clientes y las compras en un sistema unificado, lo que reduce la probabilidad de errores e ineficiencias.
MRPeasy facilita además el análisis de datos en tiempo real, el seguimiento de KPI y la elaboración de informes exhaustivos, cruciales para identificar cuellos de botella, prever la demanda y optimizar la asignación de recursos, permitiéndole tomar decisiones basadas en información real e implementar cambios de forma rápida y fiable.
Principales aspectos a tener en cuenta
- La mejora continua es un proceso estratégico de identificación, análisis y aplicación recurrentes de mejoras en los flujos de trabajo y los productos para mantener los procesos de fabricación en continuo aumento de productividad y eficiencia.
- Existen muchos tipos diferentes de modelos, métodos e iniciativas de mejora continua, como Kaizen, Lean, Six Sigma, Planificar-Hacer-Verificar-Actuar o la fabricación Just-in-Time.
- La mejora continua aporta una gran cantidad de beneficios a los fabricantes, desde la reducción de despilfarros y la mejora del trabajo en equipo hasta la simplificación de la gestión de procesos, el recorte de costos y el fomento de la innovación en el lugar de trabajo.
- Un ejemplo de ciclo de CI incluye pasos para identificar objetivos, establecer y definir el proceso, comunicar e implementar el proceso, seguir y medir los resultados, e implementar el cambio a escala.
- Las mejores prácticas de mejora continua incluyen encontrar formas innovadoras de aumentar el compromiso de los empleados, mejorar el entorno de trabajo, aprovechar la tecnología digital como IoT y los dispositivos de aprendizaje automático, etc.
Preguntas frecuentes
Medir el ROI de las iniciativas de mejora continua implica cuantificar los beneficios directos e indirectos, incluida la reducción de costos, el aumento de la productividad y la mejora de la calidad del producto. Los KPI como el tiempo de ciclo, la tasa de defectos o el rendimiento pueden correlacionarse directamente con las métricas financieras para evaluar el ROI. Además, otras métricas más generales, como el compromiso de los empleados y la satisfacción de los clientes, pueden proporcionar información sobre el impacto más amplio de las inversiones en CI.
La integración de tecnologías avanzadas como IoT y el aprendizaje automático en los marcos de CI existentes suele plantear retos como los elevados costos iniciales, la complejidad de la implementación y la necesidad de conocimientos especializados. Además, puede haber resistencia al cambio por parte de los empleados acostumbrados a los métodos tradicionales. Superar estas barreras suele requerir una planificación exhaustiva, capacitación continua y una comunicación clara sobre las ventajas que aportan estas tecnologías.
La mejora continua puede mejorar significativamente las relaciones entre proveedores y clientes. En el caso de los proveedores, una colaboración más estrecha y unos objetivos de mejora continua compartidos pueden mejorar la calidad de los materiales y la fiabilidad de las entregas. En cuanto a los clientes, las mejoras constantes en la calidad de los productos y el servicio al cliente pueden aumentar su satisfacción y fidelidad.
También le puede interesar: Control estadístico de procesos – Guía del fabricante