Las 15 mejores herramientas de fabricación ajustada en 2025
Las herramientas de fabricación ajustada le ayudan a organizar los espacios de trabajo y a solucionar los problemas antes de que puedan generar retrasos. Con estas herramientas, podrá reducir costos, mejorar el control de calidad y ofrecer a sus clientes exactamente lo que quieren.
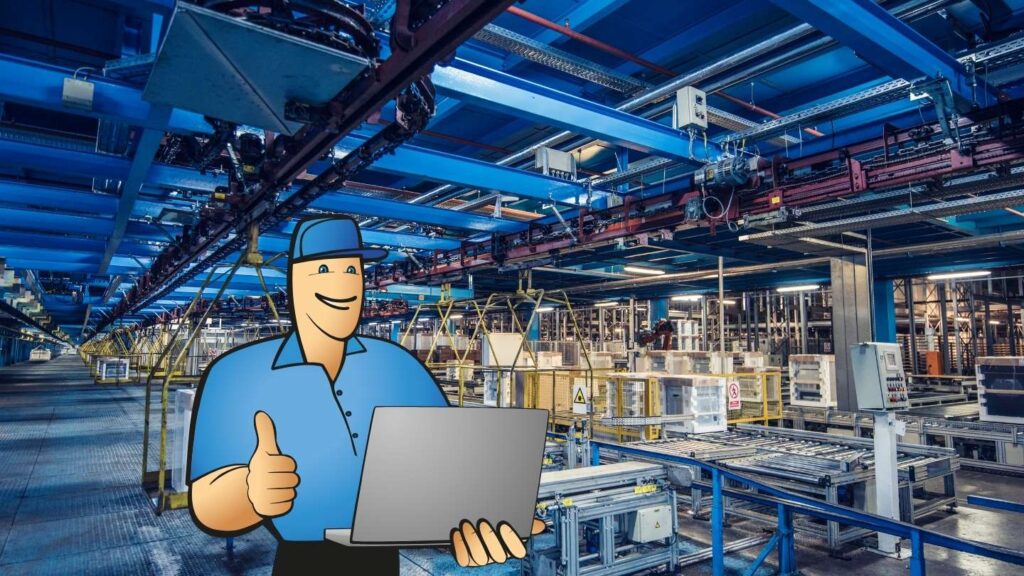
¿Qué es la fabricación ajustada?
La fabricación ajustada, o lean manufacturing, consiste en trabajar de forma más inteligente, no más dura. En esencia, es una forma de reducir los residuos y centrarse solo en lo que aporta valor añadido a los clientes.
La fabricación ajustada se basa en cinco principios fundamentales que guían cada paso del proceso. Comienza por definir el valor, lo que significa centrarse en lo que realmente importa a los clientes y garantizar que cada acción conduzca a su satisfacción. A continuación, los fabricantes mapean el proceso analizando cada paso de la producción para descubrir dónde se están desperdiciando recursos. Una vez identificadas las ineficiencias, el objetivo es racionalizar los flujos de trabajo para que todo se desarrolle sin interrupciones innecesarias. La fabricación ajustada también hace hincapié en el establecimiento de un sistema pull, lo que significa producir sólo lo que se necesita cuando se necesita, en lugar de almacenar existencias.
La fabricación ajustada anima a los equipos a buscar continuamente formas de mejorar. Por muy eficiente que sea un proceso, siempre hay margen de mejora.
Tipos de herramientas de fabricación ajustada
La fabricación ajustada se basa en una serie de herramientas para racionalizar las operaciones, eliminar los residuos y mejorar la productividad. Estas herramientas se dividen en cuatro categorías principales, cada una de las cuales desempeña un papel único en la consecución de los objetivos de Lean.
1. Herramientas de ayuda visual
Las herramientas visuales son esenciales para crear claridad en la fabricación ajustada. Simplifican los procesos complejos y facilitan a los equipos el seguimiento de los avances, la detección de problemas y la respuesta rápida. Algunos ejemplos comunes son los tableros visuales, las tarjetas Kanban y otros sistemas de señalización. Estas herramientas permiten a los trabajadores ver el estado de la producción a primera vista y hacen que los datos sean accesibles sin necesidad de largas explicaciones. Al poner en evidencia las variaciones y proporcionar información procesable, las ayudas visuales permiten a los equipos mantenerse alineados con los objetivos de producción al tiempo que mantienen una cultura de mejora continua.
2. Herramientas de resolución de problemas
Las herramientas de resolución de problemas de la fabricación ajustada se centran en identificar las causas profundas de las ineficiencias y eliminarlas sistemáticamente. Métodos como el análisis de la causa raíz y los ciclos PDCA se utilizan ampliamente para analizar los problemas y descubrir las causas subyacentes. Estas técnicas de resolución de problemas fomentan una mentalidad proactiva, animando a los equipos a abordar los retos en una fase temprana, minimizar las interrupciones y garantizar una calidad constante en todas las operaciones.
3. Herramientas de optimización de procesos
Las herramientas de optimización de procesos en la fabricación ajustada se centran en perfeccionar los flujos de trabajo para eliminar ineficiencias y mejorar la productividad. Por ejemplo, las 5S organizan y estandarizan los espacios de trabajo, creando un entorno eficiente y visualmente manejable. Del mismo modo, el Kaizen promueve la mejora continua fomentando pequeños cambios incrementales que conducen a ganancias significativas con el tiempo. Otra herramienta clave, el Just-in-Time (JIT), minimiza el despilfarro produciendo sólo lo que se necesita, cuando se necesita, alineando estrechamente la producción con la demanda. Estas metodologías no sólo agilizan las operaciones, sino que fomentan una cultura de resolución proactiva de problemas y eficiencia sostenida.
4. Software
Las soluciones de software de fabricación ajustada proporcionan una plataforma digital para gestionar y mejorar los procesos. Estas herramientas incluyen sistemas ERP de fabricación, sistemas de ejecución de fabricación (MES) y software específico de Lean, como las plataformas eKanban. Al ofrecer análisis de datos, seguimiento e informes en tiempo real, este software permite una mejor toma de decisiones y asignación de recursos. La automatización y el análisis predictivo mejoran la planificación de la producción, el control del inventario y la programación del mantenimiento. La integración del software en las prácticas Lean garantiza una mayor precisión, escalabilidad y adaptabilidad para satisfacer las demandas cambiantes.
Las 15 mejores herramientas de fabricación ajustada
Herramientas de ayuda visual
1. Kanban
Kanban es un sistema de programación Lean que ayuda a gestionar el flujo de trabajo y evitar la sobreproducción mediante la visualización de las tareas. Esta herramienta utiliza tarjetas o señales digitales para indicar cuándo es necesario reponer el inventario o las tareas o avanzar al siguiente paso. De este modo, el trabajo sólo avanza cuando hay demanda del cliente.
Establecer un sistema Kanban requiere crear un tablero visual con columnas que representen las distintas etapas de un proceso, como “Por hacer”, “En curso” y “Hecho”. Cada tarea o elemento del inventario está representado por una tarjeta que se desplaza por las columnas a medida que avanza. Este sistema visual ayuda a los equipos a detectar rápidamente los cuellos de botella, gestionar los recursos y responder a las demandas cambiantes.
2. Andon
Andon es un sistema de alerta en tiempo real que permite a los equipos abordar los problemas de inmediato. Andon, originalmente desarrollado por Toyota, utiliza señales visuales, como luces, pantallas o sonidos, para notificar a los trabajadores cuando algo está mal en el proceso de producción. Por ejemplo, un trabajador puede tirar de una cuerda Andon o pulsar un botón para señalar un defecto o un mal funcionamiento del equipo.
Implementar un sistema Andon implica establecer protocolos de comunicación claros y asegurarse de que todos los miembros del equipo entienden cómo utilizar el sistema con eficacia.
3. Mapeo del flujo de valor (VSM)
El Mapeo del Flujo de Valor (VSM) es una herramienta visual de gestión ajustada que se utiliza para trazar cada paso de un proceso con el fin de identificar y eliminar el despilfarro en toda la cadena de suministro. Desarrollado también por Toyota, el VSM ofrece una imagen clara de cómo fluye el valor a través de un proceso y destaca la duración del ciclo y los tiempos de entrega en cada paso para mostrar dónde se desperdician tiempo, recursos y materiales.
El VSM es clave en los métodos lean para localizar el muda (palabra japonesa para “despilfarro” y un concepto central en el Sistema de Producción Toyota).
Cree un mapa del flujo de valor involucrando directamente a los miembros del equipo. Mapee cada paso en secuencia y utilice diagramas de flujo para visualizar dónde puede tener más impacto la mejora del proceso.
Herramientas de resolución de problemas
Cada reto es una oportunidad para mejorar. Las herramientas Lean de resolución de problemas ayudan a los equipos a descubrir las verdaderas cuestiones que subyacen a los problemas y a aplicar soluciones duraderas. Con estas herramientas, los fabricantes pueden convertir los contratiempos en progreso y crear una cultura de mejora continua.
4. Análisis de la causa raíz (ACR)
El Análisis de la Causa Raíz (ACR) es un método utilizado para identificar la causa fundamental de un problema y eliminarla para evitar que se repita. A diferencia de las soluciones rápidas, el ACR profundiza para entender por qué se ha producido un problema. El ACR se utiliza a menudo junto con herramientas como los “5 porqués”, en las que se pregunta “¿Por qué?” repetidamente hasta llegar a la causa raíz. Este enfoque permite a los equipos abordar el problema en su base, en lugar de limitarse a tratar los síntomas.
Para llevar a cabo un ACR, identifique el problema y averigüe todo lo que pueda sobre lo ocurrido. A continuación, utilice los 5 porqués para rastrear el problema hasta su origen. Una vez encontrada la causa raíz, aplique una solución que la aborde directamente y supervise los resultados.
5. Planificar-Hacer-Verificar-Actuar (PDCA)
También denominado ciclo Deming, el Planificar-Hacer-Verificar-Actuar (PDCA) es un ciclo de mejora continua que proporciona un enfoque estructurado para resolver problemas y mejorar procesos. Los cuatro pasos —Planificar, Hacer, verificar y Actuar— guían a los equipos a la hora de probar cambios, revisar resultados y realizar ajustes. El PDCA fomenta el aprendizaje a través de pequeños cambios graduales.
El PDCA comienza con el paso Planificar. En ella se identifica un problema y se desarrolla un plan de mejora. En el paso Hacer, se pone en práctica el plan a pequeña escala. El siguiente paso es Verificar, que se realiza midiendo los resultados y comparándolos con los resultados esperados. Por último, se actúa en función de los resultados. Si el cambio tiene éxito, se implementa de forma generalizada. Si no, se revisa y se repite el ciclo.
Herramientas y metodologías de optimización de procesos
La optimización de los flujos de trabajo y la eliminación de los residuos son la esencia de la fabricación ajustada, y las herramientas de optimización de procesos lo hacen posible. Estas herramientas se centran en mejorar la eficiencia, reducir los errores y maximizar la productividad perfeccionando la forma en que se realiza el trabajo.
6. 5S (Clasificar, Ordenar, Limpiar, Estandarizar, Mantener)
5S es una de las herramientas Lean más fundamentales, creada en Japón como parte del Sistema de Producción Toyota. Se trata de un método sencillo pero potente para crear un espacio de trabajo organizado, limpio y eficiente, con una gestión visual clara para apoyar cada paso.
Las “5S” son cinco palabras japonesas que traducen Clasificar (Seiri), Ordenar (Seiton), Limpiar (Seiso), Estandarizar (Seiketsu) y Mantener (Shitsuke). Cada “S” representa un paso en la creación de un espacio de trabajo eficiente, ordenado y fácil de gestionar y mantener.
El primer paso, Clasificar, consiste en eliminar el desorden del espacio de trabajo. A continuación, Organizar significa organizar las herramientas y los materiales de forma que favorezcan el flujo de trabajo. Limpiar implica limpiar a fondo la zona, para que sea segura y eficaz. Estandarizar garantiza que todo el mundo siga los mismos pasos para mantener el espacio de trabajo organizado y limpio. Por último, Mantener mantiene el sistema a lo largo del tiempo mediante comprobaciones y mejoras periódicas.
Para implementar las 5S, empiece por involucrar a todo el equipo en el proceso de clasificación y organización. Así se crea un sentimiento compartido de pertenencia y responsabilidad en el mantenimiento de la zona. Las auditorías periódicas pueden ayudar a garantizar que se sigue cada paso de las 5S.
7. Kaizen
Desarrollado como parte del enfoque de fabricación de Toyota, Kaizen (que significa “mejora continua” en japonés) es una herramienta Lean que promueve la mejora de los procesos mediante pequeños ajustes en tiempo real. La idea es sencilla: Pequeños ajustes a lo largo del tiempo conducen a grandes ganancias en calidad, productividad y eficiencia.
Este enfoque aborda problemas como el exceso de procesamiento y los retrasos en la línea de producción, impulsando mejoras continuas. Los indicadores clave de rendimiento (KPI) pueden medir la eficacia de Kaizen. Con el tiempo, Kaizen crea un equipo proactivo que invierte en el mantenimiento productivo total (TPM), cuyo objetivo es minimizar las averías.
Para aplicar el Kaizen, las empresas crean un entorno en el que los miembros del equipo a todos los niveles pueden aportar ideas de mejora. Esto puede significar cualquier cosa, desde ajustar la disposición de un puesto de trabajo hasta encontrar una forma más rápida de realizar una tarea repetitiva.
Las mejores prácticas Kaizen incluyen reuniones periódicas, a menudo denominadas “eventos Kaizen” o “blitzes”, en las que los empleados sugieren mejoras y debaten cuestiones que afectan directamente a su trabajo. Con el tiempo, el Kaizen crea un equipo proactivo y comprometido que busca constantemente formas de mejorar.
8. Justo a tiempo (JIT)
Procedente del sistema de fabricación de Toyota, el sistema Justo a Tiempo (Just-in-time o JIT) reduce el exceso de procesamiento produciendo sólo lo que se necesita, cuando se necesita. Como resultado, el JIT minimiza el exceso de inventario y reduce los costos de almacenamiento. La idea principal es “tirar” (pull) de los materiales y productos a través del proceso de producción sólo cuando sea necesario, en lugar de “empujar” (push) grandes cantidades de inventario al almacén.
Para implementar el sistema JIT, las empresas deben colaborar estrechamente con los proveedores para garantizar entregas fiables y puntuales. La planificación de la producción es crucial con el JIT. Los calendarios y los flujos de trabajo deben ajustarse estrechamente a las previsiones de la demanda.
Puede combinar JIT con Kanban porque estas dos herramientas se complementan. JIT reduce el exceso de inventario produciendo sólo cuando es necesario, mientras que Kanban señala visualmente cuándo deben fabricarse o moverse nuevos artículos. Juntas, hacen que la producción responda a la demanda y ayudan a eliminar el despilfarro.
9. Poka-Yoke (Comprobación de errores)
Poka-Yoke, o “a prueba de errores”, elimina las grandes pérdidas previniendo los errores antes de que se produzcan. Creado por Shigeo Shingo en Toyota (quizá esté notando un patrón), el Poka-Yoke pretende diseñar procesos que eviten los errores o los hagan inmediatamente evidentes. Este principio lean aborda el problema del error humano en trabajos repetitivos como la fabricación. Cuando se aplica, elimina las costosas repeticiones y reduce las posibilidades de que los defectos lleguen a los clientes.
Poka-Yoke introduce medidas de seguridad que ayudan a los trabajadores a evitar errores comunes. Un ejemplo de Poka-Yoke es añadir conexiones codificadas por colores que sólo encajan de una manera. Poka-Yoke permite a los equipos trabajar de forma más fiable al incorporar la prevención de errores directamente en el proceso.
10. Control estadístico de procesos (CEP)
El control estadístico de procesos (CEP) es un método basado en datos para supervisar y controlar las variaciones en los procesos de fabricación. Mediante el análisis de las métricas de rendimiento , el CEP ayuda a los equipos a identificar tendencias, detectar posibles problemas con antelación y mantener una calidad constante. Herramientas como los gráficos de control facilitan la visualización de los datos y mantienen los procesos dentro de los límites deseados.
11. Mantenimiento Productivo Total (TPM)
El Mantenimiento Productivo Total (TPM) se centra en maximizar la eficiencia de los equipos minimizando los tiempos de inactividad y las interrupciones. Al implicar a los operarios en el mantenimiento rutinario y crear un enfoque proactivo, el TPM contribuye a la fiabilidad de las máquinas. Este método no sólo mejora la productividad, sino que también alarga la vida útil de los equipos.
Soluciones de software de fabricación ajustada
A medida que evoluciona la fabricación ajustada, la tecnología se ha convertido en un socio esencial para impulsar la eficiencia y eliminar los residuos. Las soluciones de software hacen realidad los principios de Lean mediante la automatización de procesos y la integración de flujos de trabajo clave.
12. MES (Sistema de Ejecución de la Fabricación)
Un sistema de ejecución de fabricación (MES) ayuda a los fabricantes a mantener el control gestionando la producción en tiempo real. Este software realiza un seguimiento y coordina las actividades del taller, lo que proporciona una mayor visibilidad de los procesos a medida que se producen. El MES mantiene el buen funcionamiento de las operaciones mediante la supervisión del rendimiento de los equipos, incluida la eficacia general de los equipos (OEE), el seguimiento de la productividad de los trabajadores y la programación de tareas.
Una de las mayores ventajas de un sistema MES es su capacidad para detectar con antelación posibles cuellos de botella o problemas. Esto permite a los equipos realizar ajustes antes de que los problemas se agraven. Al integrar los datos de toda la planta de producción, el MES ayuda a los fabricantes a mantenerse ágiles y reactivos.
13. SGC (software de gestión de la calidad)
El software de gestión de la calidad (SGC) es clave para mantener una calidad y una conformidad constantes en todos los procesos de fabricación. Automatiza tareas como el seguimiento de defectos, la programación de inspecciones y la gestión de documentación. El SGC ayuda a reducir los residuos y las repeticiones de trabajo identificando los problemas para que pueda resolverlos antes de que afecten a la producción.
El SGC también contribuye al cumplimiento de la normativa manteniendo toda la documentación relacionada con la calidad organizada y actualizada. Esto es especialmente importante en sectores como el automovilístico, el aeroespacial y el sanitario, donde las normas no son negociables.
Software de gestión de proyectos
El software de gestión de proyectos simplifica la organización y ejecución de proyectos de fabricación centralizando la información y proporcionando herramientas para planificar, supervisar y comunicar con eficacia. Además de desglosar los proyectos en tareas, los equipos pueden utilizar este software para fijar plazos y asignar recursos. Con funciones integradas como los diagramas de Gantt, el software de gestión de proyectos mantiene los proyectos dentro de los plazos previstos.
14. MRP I (Planificación de requerimientos de material)
La planificación de requerimientos de material (MRP I) ayuda a optimizar el inventario y la programación de la producción para ajustarse a la demanda de los clientes. Mediante el análisis de las previsiones de demanda, MRP I garantiza la disponibilidad de los materiales adecuados en el momento oportuno. De este modo, se evita la escasez o el exceso de existencias.
MRP I también agiliza las adquisiciones automatizando los puntos de pedido y programando las entregas de material. Es una herramienta esencial para las empresas que buscan un equilibrio entre eficiencia y flexibilidad en sus operaciones.
15. ERP (Planificación de Recursos Empresariales) o MRPII
El ERP de fabricación, también denominado planificación de recursos de fabricación o MRP II, integra todos los aspectos de una empresa en un único sistema cohesionado. Esto abarca la producción, el inventario y las finanzas. El ERP proporciona a los fabricantes una visión completa de sus operaciones para ayudarles en la toma de decisiones y en la coordinación entre departamentos. Con ERP, los fabricantes pueden automatizar procesos y obtener información en tiempo real sobre el rendimiento.
Principales aspectos a tener en cuenta
- La fabricación ajustada se centra en eliminar los residuos y dar prioridad a las acciones que aportan valor a los clientes al tiempo que mejoran la eficiencia.
- Herramientas como Kanban y Andon hacen que los flujos de trabajo sean transparentes, lo que permite a los equipos hacer un seguimiento del progreso y abordar los problemas con prontitud.
- Métodos como el Análisis de la Causa Raíz (ACR) y el PDCA ayudan a descubrir ineficiencias e implementar soluciones que aborden las causas profundas de los problemas.
- Estrategias como 5S y Kaizen garantizan la eficiencia de los espacios de trabajo y la mejora continua de los procesos, fomentando una productividad sostenible.
- Herramientas como MES y ERP integran los procesos y proporcionan información en tiempo real, lo que permite a las empresas adaptarse rápidamente y reducir los residuos.
- El énfasis en la mejora continua y la implicación del equipo es clave para lograr el éxito a largo plazo en la fabricación ajustada.
Preguntas frecuentes
Las pequeñas empresas pueden empezar adoptando herramientas sencillas y de bajo costo, como las 5S y el Kaizen, para organizar los espacios de trabajo y fomentar mejoras graduales. También existen modernos sistemas ERP de fabricación para empresas con presupuestos mínimos.
Mantener las mejoras Lean requiere una capacitación regular, el compromiso de los líderes y auditorías periódicas para garantizar que prácticas como las 5S y el Kaizen siguen siendo eficaces. Fomentar una cultura de mejora continua e involucrar a los empleados en la supervisión y el perfeccionamiento de los procesos ayuda a mantener el progreso.
El tiempo necesario para ver los resultados varía en función de la escala de la implementación y de la complejidad de los procesos. Mientras que algunos cambios, como la implementación de las 5S, pueden producir mejoras inmediatas, las iniciativas de mayor envergadura, como JIT o Mapeo del flujo de valor, pueden tardar semanas o meses en demostrar un impacto significativo. La constancia y el compromiso son la clave del éxito a largo plazo.
También le puede gustar: Los 11 KPIs de gestión de inventarios más importantes en 2025