Gestión de materiales – Mejores prácticas para pequeños fabricantes
Una gestión adecuada de los materiales permite a las empresas asegurarse de que las materias primas con el mejor precio y la mejor calidad llegan al taller en el momento y la cantidad adecuados. Siga estas mejores prácticas para controlar mejor este segmento esencial de la cadena de suministro.
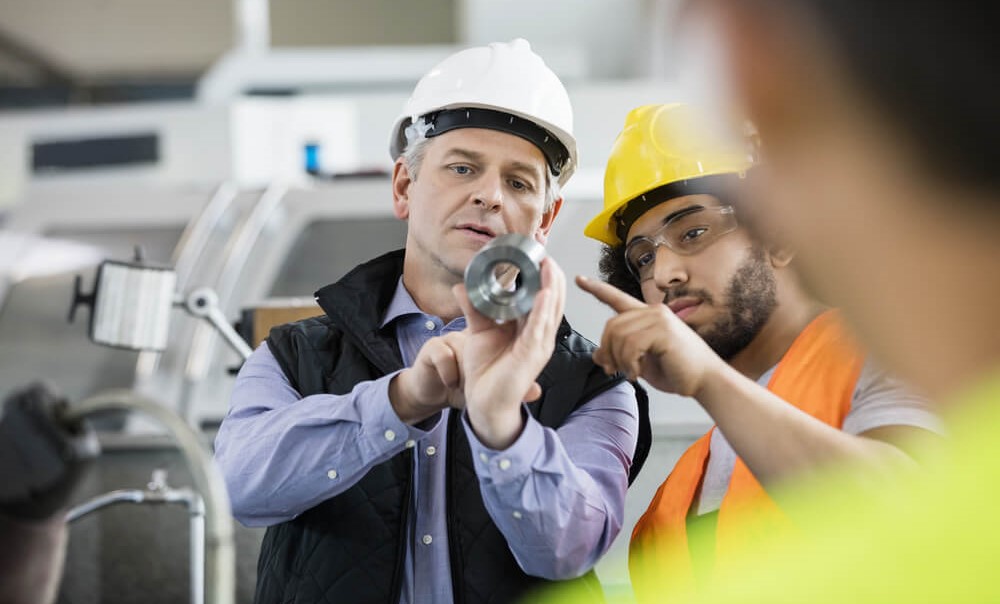
¿Qué es la gestión de materiales?
La gestión de materiales es la parte de la cadena de suministro de una empresa de fabricación que se encarga de controlar todos los aspectos relacionados con las materias primas utilizadas en la producción. El proceso tiene por objeto gestionar la calidad, el abastecimiento y el precio de los materiales, así como su ubicación y movimiento dentro de la cadena de fabricación. El trabajo del gestor de materiales consiste en coordinar estrechamente el inventario, las compras y la producción para establecer procedimientos de comunicación de las necesidades de materiales y distribuir las materias primas a lo largo de la cadena de suministro.
Mientras que algunas organizaciones pueden designar la gestión de materiales como una subsección de la gestión general de compras, otras empresas las tratan como entidades separadas que sirven a diferentes áreas de un negocio. Otras aún pueden dividir las funciones de la gestión de materiales entre muchos departamentos empresariales como compras, cadena de suministro, logística, etc. Este suele ser el caso de las grandes empresas de fabricación o construcción.
Como parte de la gestión de compras, la gestión de materiales incluye todo lo relacionado con el abastecimiento y la compra de materiales. Sin embargo, si se trata como una subsección separada de la gestión de la cadena de suministro, se convierte en un vínculo entre las compras y la producción, que se ocupa principalmente de la planificación de requerimientos de materiales, la coordinación del despliegue y el reabastecimiento de materiales, y la realización de controles de calidad y análisis de inventario de materiales directos.
Cabe mencionar que los materiales utilizados en la fabricación suelen dividirse en materiales directos e indirectos. Los materiales directos son las materias primas de las que se componen los productos que fabrica una empresa. El caucho en los neumáticos, el azúcar en la soda, etc. Los materiales indirectos son elementos y materiales utilizados en el proceso de fabricación que no componen el producto en sí. Pueden ser pegamentos, grapas, equipos o piezas de repuesto. En la mayoría de los casos, la gestión de materiales incluye el control del flujo de ambos.
Mejores prácticas en la gestión de materiales
Establecer normas para las especificaciones y la calidad de los materiales
El director de materiales es quien toma las decisiones en última instancia cuando se trata de controlar la calidad y aprobar las materias primas que se van a comprar. Sin embargo, el responsable de materiales no puede estar al mando de todos los procesos de compra ni de todos los controles de calidad, por lo que debe establecer los procedimientos operativos estándar que deben seguir quienes participan en el proceso. Esto incluye establecer las especificaciones de los materiales y los requisitos de calidad. Esta es la base para maximizar la conformidad del producto y minimizar la no conformidad.
Realizar controles de calidad periódicos para garantizar la conformidad con las normas.
Un control de calidad eficaz empieza antes del proceso de producción. Por supuesto, ninguna empresa es capaz de evaluar la calidad de cada unidad de materia prima que reciben, pero los controles de calidad deben hacerse con regularidad, tan a menudo y tan a fondo como sea financieramente viable. En la mayoría de los casos, los fallos debidos a la mala calidad (sobre todo los fallos internos, es decir, los detectados por el cliente, los que requieren devoluciones, reparaciones, etc.) son más caros que las medidas adoptadas para garantizar una buena calidad.
Conozca la cantidad exacta y la ubicación de sus materiales directos e indirectos
Para proporcionar a la planta de producción los materiales necesarios en el momento oportuno, tendrá que saber dónde están y en qué cantidad. El marcado y la organización correctos son imprescindibles en todo inventario. Los recuentos físicos deben realizarse periódicamente para detectar incoherencias o extravíos, pero deben utilizarse soluciones tecnológicas para contabilizar el inventario en el día a día.
Controle sus costos directos/de inventario de materias primas
Una parte sustancial de los gastos de un fabricante promedio procede de los costos directos de material. Por lo tanto, es absolutamente esencial asegurarse de que el exceso de inventario no está inmovilizando efectivo que podría aprovecharse en otro lugar. Además, mantener existencias durante demasiado tiempo puede provocar que los productos se deterioren o se estropeen. Esto es especialmente cierto en el caso de los materiales que tienen fecha de caducidad. Los fabricantes deben considerar diferentes métodos de valoración de las existencias (por ejemplo, FIFO, LIFO, Promedio ponderado) en función de la naturaleza de su negocio.
Más información sobre Métodos de valuación de existencias.
Cree un plan y sígalo
La planificación de requerimientos de materiales (MRP I) y la planificación de recursos de fabricación (MRP II) son dos enfoques estrechamente relacionados de la gestión de materiales.
Mientras que MRP I tiene sus inicios a mediados del siglo XX y se ocupa de la planificación básica de la producción y el control de inventarios (qué se necesita y en qué cantidad), MRP II es un avance de este método.
MRP II o Planificación de Recursos de Fabricación examina la planificación de la producción a través del punto de vista añadido de la previsión de la demanda (cuándo hay que pedir los materiales) y la planificación de la capacidad (cuándo puede y debe empezar la producción) al tiempo que se gestionan aspectos como el control de inventarios, las compras, la planificación empresarial, las necesidades de personal, etc.
Por tanto, permite optimizar mejor el uso de la maquinaria y los recursos, obtener una mejor visión financiera, y controlar y coordinar mejor la producción y las existencias.
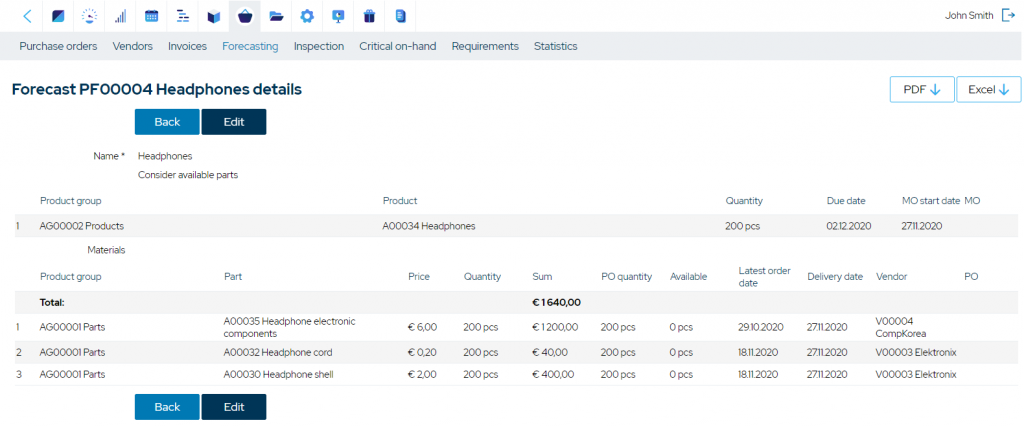
Utilizar técnicas de control de inventario
El uso de técnicas de control de inventarios de eficacia probada podría ofrecerle una mejor visión del rendimiento de sus SKU y proporcionarle los conocimientos que le ayudarían a minimizar sus costos de inventario.
Análisis ABC (+XYZ)
Al aplicar el principio de Pareto (o regla 80/20) a la gestión de inventarios, el análisis ABC le permite priorizar sus SKU en función de su valor de consumo. La realización de un análisis ABC dividirá sus materiales en tres categorías:
– La A para aproximadamente el 20% del total de SKU que suponen alrededor del 80% del valor total de consumo. Estos artículos recibirán la mayor atención: mayores niveles de servicio, más tiempo de revisión, etc.
– La B para cerca del 30% de las SKU, que representan alrededor del 15% del valor total del consumo. Recibirán menos atención que los artículos de categoría A y más que los de categoría C.
– La C para aproximadamente el 50% de las SKU que representan sólo el 5% del valor total de consumo. Estas serán las que menos recursos tengan asignados.
En caso de que un solo parámetro resulte demasiado básico para priorizar sus artículos, añadir el análisis XYZ a la ecuación también le permite tener en cuenta las fluctuaciones en los patrones de consumo de las SKU.
Lea más en este artículo sobre Análisis ABC y XYZ.
Stock de seguridad y punto de reorden
El stock de seguridad es la reserva de materiales que se tiene para evitar el desabastecimiento y continuar la producción en caso de que se produzcan irregularidades en el suministro debido a cambios en la oferta o la demanda.
El punto de pedido es el nivel de inventario establecido a partir del cual se activa un pedido de una SKU cuando llega el momento de reponer sus existencias.
Si sólo se fija un punto de pedido, cuando los plazos de entrega superen el tiempo previsto para un desabastecimiento, sus materiales se agotarán y la producción se detendrá hasta que lleguen nuevos materiales.
Sin embargo, disponer de una reserva de seguridad también evitará que eso ocurra.
Ambos valores deben definirse matemáticamente para que funcionen como es debido.
Puede obtener más información sobre estas técnicas en las entradas de nuestro blog sobre Stock de seguridad y Punto de pedido.
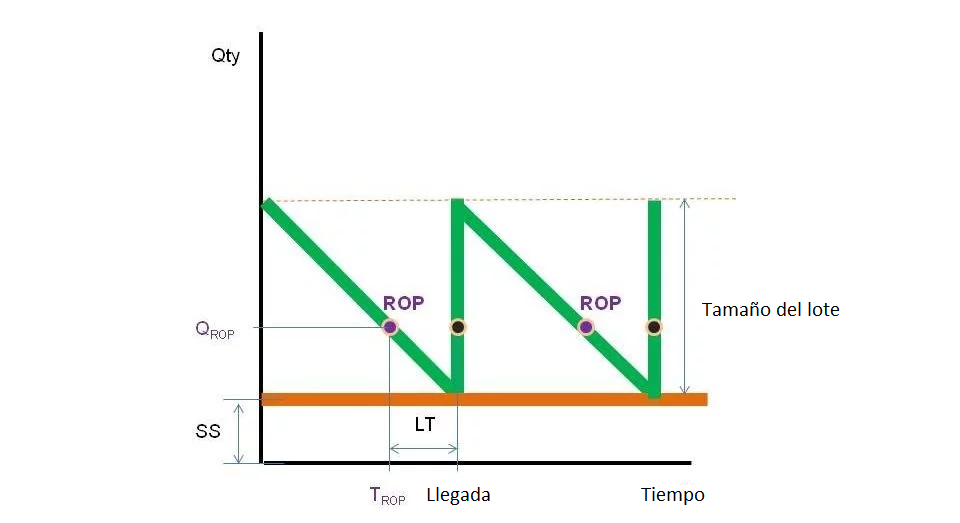
Justo a tiempo (Just-in-time)
Just in Time no es sólo un método de control de inventarios, sino también un enfoque general de la fabricación que pretende minimizar el tiempo que pasa un producto en la cadena de suministro – desde el proveedor de los materiales hasta el consumidor final.
De este modo, los fabricantes pueden evitar la sobreproducción, reducir los cuellos de botella y el tiempo de espera en los procesos de producción, y evitar tener un exceso de existencias.
Cuando hablamos de gestión de materiales, la idea general de JIT es suministrar los materiales a medida que se necesitan, lo más cerca posible de la demanda.
Como consecuencia, se agiliza el movimiento de materiales y se reducen drásticamente los niveles de inventario, el espacio de almacenamiento y los costos.
Más información sobre la fabricación justo a tiempo (Just-in-time).
Minimizar el tiempo de búsqueda mediante el uso de kits de materiales
El kit de materiales consiste en agrupar los componentes de una lista de materiales en un set listo para el consumo antes de que lleguen a la planta de producción.
Esta técnica simplifica el inventario en línea y mejora la velocidad de preparación de pedidos, los informes y los procesos de control de calidad.
Como regla general, la práctica de los kits (o kitting), sería más beneficiosa cuando se trata de grandes variedades de pequeños componentes, productos personalizados con diferentes variables, o una falta de espacio en el taller que no permite mucho inventario en línea.
Utilizar la tecnología para hacer más eficientes los procesos
Existen numerosas soluciones tecnológicas que pueden ayudar a los fabricantes y gestores de materiales a mejorar sus procesos empresariales.
Los códigos de barras, los dispositivos RFID e IoT y el software de gestión de almacenes ayudan a gestionar y seguir de cerca su inventario.
Pero lo que complementa todas las áreas de gestión de materiales junto con todos los demás departamentos de una empresa de fabricación es un sistema ERP de fabricación.
Hoy en día, “sistema MRP” y “ERP de fabricación” se utilizan a menudo como términos intercambiables, aunque en teoría, este último tiene una gama más amplia de funcionalidades (CRM y contabilidad, por ejemplo).
Un buen ERP de fabricación permite a los fabricantes coordinar todo su negocio en un único programa.
Esto incluye procesos de gestión de materiales como la planificación de los requerimientos de materiales, el despliegue y la reposición de material, el control de calidad, control y análisis de inventario, kitting, etc.
Conclusión
A menudo se considera que la gestión de materiales forma parte de las compras, pero gestionarla por separado y de forma más centrada podría dar mejores resultados en términos de calidad y eficiencia.
En pocas palabras, las mejores prácticas que debe seguir un gestor de materiales están relacionadas con el control de la calidad y el flujo de materiales.
Para lograr una producción fluida con un mínimo de cuellos de botella y fallos, se recomienda utilizar técnicas de control de inventarios como las existencias de seguridad y el punto de reorden, o Just in Time (JIT), junto con soluciones tecnológicas que ayuden al seguimiento y la evaluación de los materiales.
También le puede interesar: 5 consejos para que la planificación de material sea más eficaz