Gestión de mantenimiento – aumentar la eficacia mediante la proactividad
La gestión de mantenimiento es esencial para toda empresa que desee aumentar la eficacia y la seguridad en el lugar de trabajo. Adoptar un enfoque proactivo en las políticas de mantenimiento resulta fácil y asequible con las funciones de gestión de mantenimiento de un software de fabricación moderno.
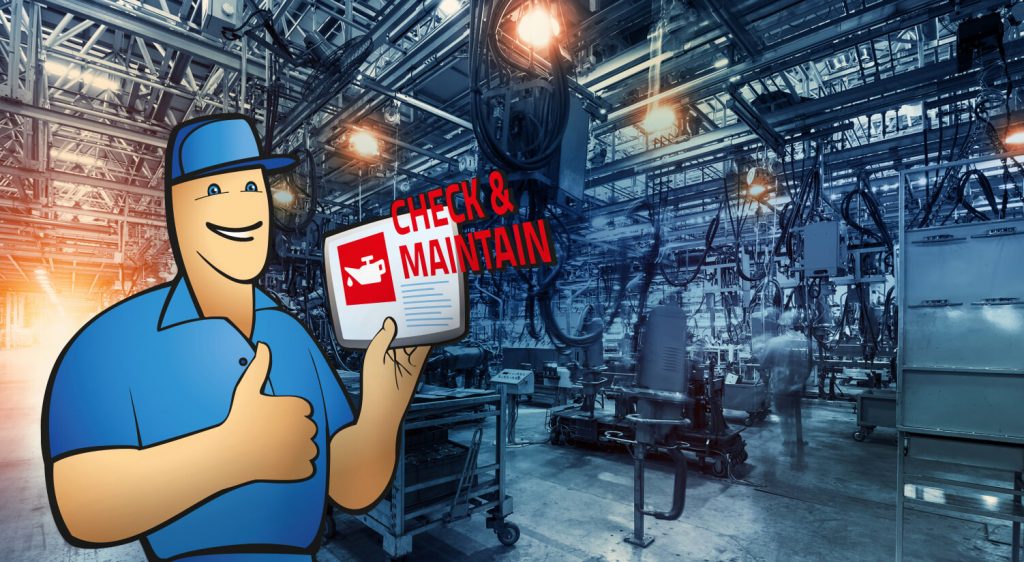
¿Qué es la gestión de mantenimiento?
La gestión de mantenimiento es el conjunto de procedimientos utilizados para atender los equipos de fabricación de una empresa con el fin de mantenerlos seguros, funcionales y eficientes.
Ya sea un productor de alimentos con grandes máquinas agrícolas y de procesamiento; una carpintería con sierras de mesa, tornos y taladros; o un fabricante de prendas de vestir que utiliza máquinas de hilar, cortar y coser –un mantenimiento adecuado de la maquinaria es esencial en cualquier empresa de fabricación.
Sus prácticas de gestión de mantenimiento se reflejarán siempre en el rendimiento de toda su empresa.
La Eficacia General de los Equipos, la Utilización de la Capacidad, el Rendimiento, el Costo de Fabricación por Unidad, el Tiempo de Parada en Proporción al Tiempo de Funcionamiento –todas estas métricas importantes están directa o indirectamente relacionadas con el estado de sus equipos.
Cuando una máquina se avería, en última instancia supone pérdidas para la empresa debido a costos de reparación imprevistos, sustituciones de máquinas, retrasos y la pérdida de ingresos causada por la interrupción de la producción.
Si su equipo no recibe un mantenimiento adecuado, también podría contribuir a la disminución de la calidad de sus productos y al aumento del consumo de energía en sus instalaciones.
Sin embargo, con la introducción de procedimientos de mantenimiento adecuados, puede mantener las fallas de la maquinaria al mínimo, garantizando la máxima eficacia posible de sus equipos y la seguridad de sus trabajadores.
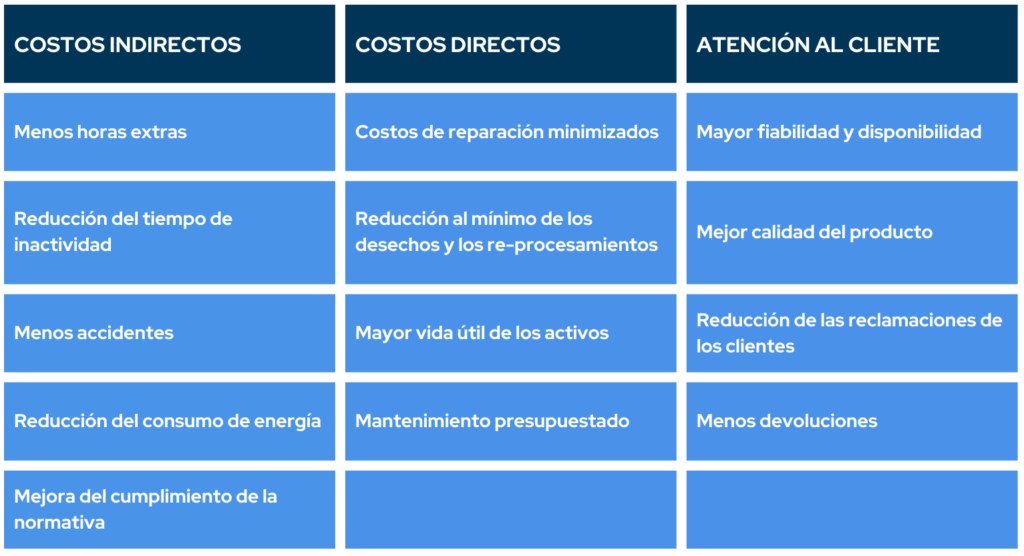
Mantenimiento reactivo vs. Mantenimiento proactivo
El mantenimiento reactivo consiste en reparar los equipos cuando se producen averías.
El enfoque proactivo, sin embargo, pretende reducir al mínimo las averías de la maquinaria utilizando medidas preventivas y predictivas.
Aunque un programa de mantenimiento proactivo requiere algunas inversiones iniciales, el resultado es un equipo más rentable, eficiente y duradero.
Las medidas preventivas son asequibles incluso para las empresas más pequeñas, ya que sólo requieren la aplicación de un plan de mantenimiento basado en el tiempo o en el uso.
Por ejemplo, puede realizar el mantenimiento una vez al trimestre, después de cada mil horas de uso o después de una cantidad determinada de piezas procesadas.
Este programa de mantenimiento regular es una solución muy fácil de introducir, pero podría ahorrarle decenas de miles en reparaciones.
Las medidas predictivas, sin embargo, utilizan alta tecnología como IoT, sensores y otros equipos de supervisión del estado para medir parámetros como la temperatura, la vibración, la resistencia, etc. con el fin de predecir cuándo debe realizarse el mantenimiento o cuándo debe sustituirse una pieza de una máquina.
Los sistemas de mantenimiento predictivo son muy eficaces, pero también muy complejos y caros, por lo que sólo resultan viables cuando la empresa es bastante grande.
Para los más pequeños, basta con un programa de mantenimiento preventivo.
¿Con qué frecuencia debe realizarse el mantenimiento?
Por lo general, el manual del OEM le proporcionará directrices sobre la frecuencia con la que debe inspeccionarse, limpiarse o mantenerse el equipo.
Como regla general, debería realizar el mantenimiento más a menudo en el caso de los activos que se utilizan más, son fundamentales para sus operaciones o son más caros y susceptibles de sufrir averías.
Por otra parte, los recursos asignados al mantenimiento de maquinaria no crítica, menos costosa o poco utilizada pueden reducirse al mínimo.
Lo ideal sería conservar datos sobre la correlación entre el mantenimiento y la mejora de la eficiencia, y basar en ellos las prácticas de gestión de mantenimiento.
Además, deben establecerse procedimientos operativos estándar que fijen un modelo de cómo se realiza cada tarea, para que el mantenimiento sea coherente.
Funcionalidad de gestión de mantenimiento en el software de fabricación
Algunos sistemas ERP de fabricación modernos incluyen un sistema de gestión de mantenimiento.
Esta capacidad de mantenimiento preventivo permite al usuario realizar un seguimiento automático de los ciclos de mantenimiento de sus puestos de trabajo.
Los ciclos de mantenimiento pueden establecerse para cada estación de trabajo en días naturales, horas de uso o unidades procesadas.
La página de la estación de trabajo mostrará entonces cuántos días, horas o unidades quedan hasta que haya que volver a realizar el mantenimiento.
Cuando pasa el tiempo o cuando los trabajadores informan de operaciones de fabricación, estos contadores de mantenimiento se actualizan consecuentemente; cuando se realiza el mantenimiento de la maquinaria, los contadores se ponen a cero.
Aunque esta funcionalidad es muy sencilla y clara, podría servir de base para los procesos de mantenimiento de su empresa.
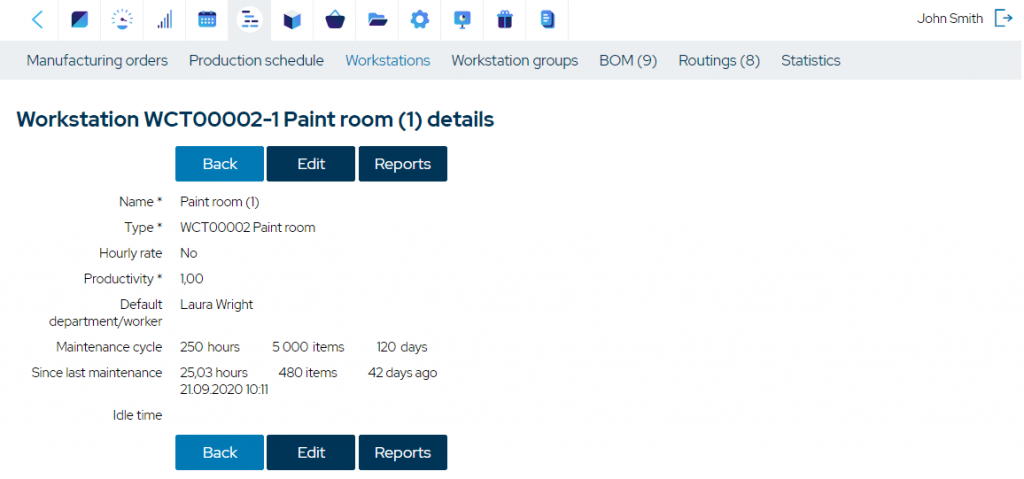
Establecer un plan de mantenimiento de activos
Un buen plan tiene en cuenta todos los aspectos –no sólo hay que especificar el inventario de activos y sus métodos individuales de mantenimiento, sino también detallar los recursos humanos, herramientas, tiempo y materiales (incluidas las piezas de repuesto) utilizados para el mantenimiento.
Para tener en cuenta todos los factores que intervienen en la planificación del mantenimiento de los activos, se debe anotar todo hasta la mezcla de lubricantes que se va a utilizar.
Esto significa que cada vez que cambia una variable, hay que revisar y modificar también el plan –incluso cambiar el aceite que se utiliza podría alterar el resultado debido a las diferencias en su composición química y sus características.
Una vez definidos los detalles, debe crearse un horario de acuerdo con el manual del OEM.
También puede introducir la información del manual del OEM en su sistema MRP para que le avise automáticamente de cuándo debe realizarse el mantenimiento.
Disponer de un plan sólido y muy detallado, con instrucciones claras y concisas, puede ayudarle a presupuestar y a evitar errores humanos cuando el mantenimiento deba ser realizado por personal con menos experiencia.
Lista de mantenimiento
Para que los procedimientos estándar sean fáciles de seguir, sería útil disponer de una lista de comprobación.
Una buena lista de comprobación comunica los pasos de una secuencia, de forma clara y exhaustiva.
Incluye los requisitos de:
- Herramientas
- Piezas de repuesto y materiales
- Tiempo
- Equipo de protección
Luego, detalla:
- Instrucciones de seguridad
- Atributos específicos de los activos
- Secuencia de acciones
Además, debe incluir:
- Ayudas visuales como fotos o diagramas
- Requisitos de conformidad
Deben guardarse copias de la lista de comprobación de mantenimiento junto al activo, con el manual del OEM y en una carpeta de mantenimiento.
Un buen software MRP también permitiría adjuntar documentos y notas a las estaciones de trabajo, haciendo que las instrucciones y listas de comprobación sean fácilmente accesibles en la planta de producción con un dispositivo móvil.
Aparte de revisar sus equipos de fabricación, el mantenimiento debe realizarse regularmente en todas las instalaciones.
Conclusión
Toda empresa de fabricación necesita realizar una gestión de mantenimiento para mantener sus equipos en buen estado de funcionamiento, ahorrar en reparaciones, aumentar la seguridad en el lugar de trabajo e incrementar los niveles de satisfacción del cliente ofreciendo productos de alta calidad en el plazo especificado.
Aunque pueda parecer mucho trabajo, ser proactivo en su política de mantenimiento de activos ya no consume muchos recursos si opta por un enfoque preventivo.
El uso de software de fabricación para realizar un seguimiento del uso de la maquinaria o de la duración del ciclo de mantenimiento de los equipos le permite planificar y programar fácilmente el mantenimiento de sus activos.
A su vez, un plan adecuado con una lista de comprobación reducirá al mínimo la posibilidad de que se produzcan errores humanos, maximizará la eficacia de sus equipos y, en última instancia, hará de sus instalaciones un lugar de trabajo más seguro.