Garantía de calidad en la fabricación – Buenas prácticas de garantía de calidad para PYMEs
Junto a la cantidad que se produce, la calidad de los productos es una cara igualmente importante de la moneda en la fabricación. La garantía de calidad es el proceso de mantener la coherencia, evitar los productos defectuosos y cumplir la normativa industrial en la fabricación de productos.
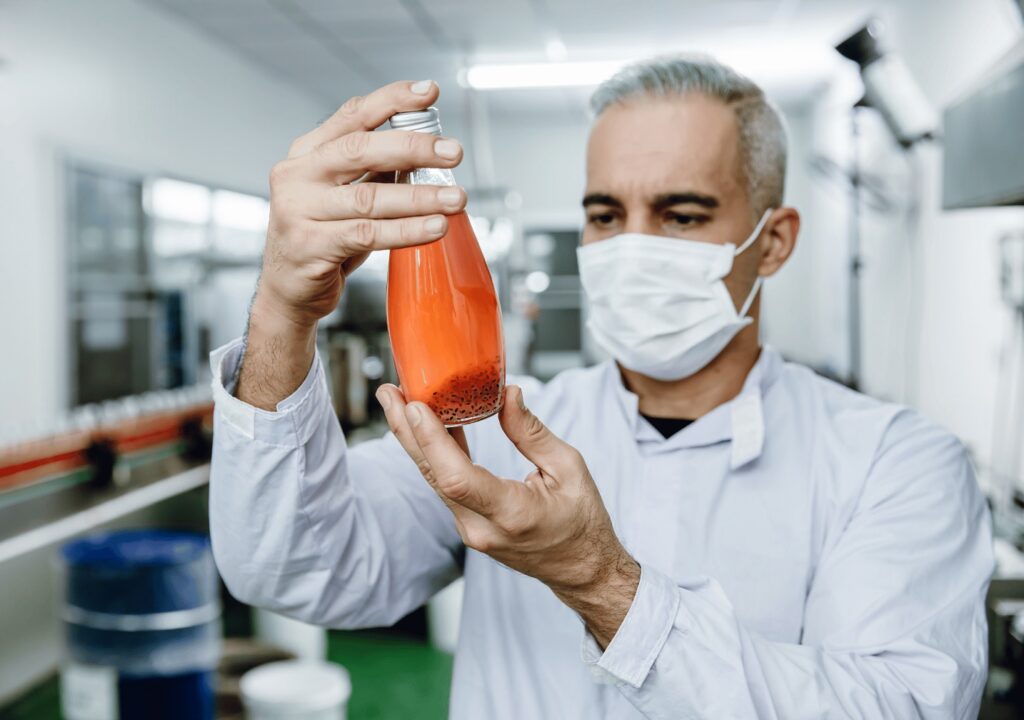
¿Qué es la garantía de calidad en la fabricación?
En la industria de la fabricación, la garantía de calidad (GC) es un proceso sistemático destinado a garantizar que los productos de una empresa cumplen los requisitos especificados y satisfacen las expectativas del cliente. La calidad del producto no sólo depende de unos buenos procesos de fabricación que producen productos sin defectos, sino que también depende de materiales de alta calidad, movimientos oportunos de la cadena de suministro, instalaciones bien organizadas, personal bien formado y otros aspectos empresariales que, en conjunto, trabajan para lograr y mantener una satisfacción constante del cliente.
El proceso de garantía de calidad es un conjunto de prácticas que una empresa aplica y sigue para garantizar una alta calidad constante de sus productos. Es un componente proactivo de la gestión de la calidad, centrado no sólo en los productos, sino también en el cumplimiento de los requisitos de calidad. La definición y aplicación de procesos, la formación de personal o la elección de las herramientas adecuadas para obtener productos de calidad forman parte de este componente. La garantía de calidad forma parte de un proceso más amplio de gestión de la calidad, y la otra es el control de calidad.
Garantía de calidad vs. control de calidad
La garantía de calidad y el control de calidad (CC) son aspectos de la gestión de la calidad que suelen estar interrelacionados, aunque son claramente distintos. La garantía de calidad abarca un amplio espectro del sistema de calidad, centrándose en proporcionar confianza en que se cumplirán los requisitos de calidad. Esta confianza se extiende internamente a la dirección y externamente a los clientes y organismos reguladores.
Por el contrario, el control de calidad tiene que ver más con el cumplimiento de las normas de calidad establecidas por la GC. Por tanto, el control de calidad puede considerarse un subconjunto más práctico de la gestión de calidad que se centra en las técnicas y actividades operativas utilizadas para cumplir los requisitos de calidad. En otras palabras, el control de calidad comprende las prácticas que garantizan que los procesos siguen las medidas de la garantía de calidad. En la fabricación, el control de calidad gira sobre todo en torno a la inspección y el seguimiento de los pasos del proceso de fabricación que ponen a prueba la calidad del producto.
¿Qué es la gestión de la calidad?
En la fabricación, la gestión de la calidad es el proceso sistemático de diseño de los procesos de control de calidad de una empresa, así como la gestión de sus esfuerzos de control de calidad. Se centra en implementar procesos relacionados con la calidad y el cumplimiento y en gestionar sistemas de calidad.
Por tanto, la gestión de la calidad integra la GC y el CC en un único sistema de gestión de la calidad (SGC). La gestión de la calidad consiste en respetar las normas, pero también en garantizar que todas las fases de diseño, desarrollo, fabricación y entrega cumplen las normas. Como ya se ha señalado, la gestión de la calidad es crucial para proteger no sólo los productos terminados, sino también la calidad de las materias primas y los componentes que intervienen en el proceso.
Sistemas de gestión de la calidad
En la fabricación moderna, todas las actividades relacionadas con la calidad se reúnen en un único sistema de gestión de la calidad. Los sistemas de gestión de la calidad (SGC) son marcos formales que guían a las empresas de fabricación en la consecución y el mantenimiento de los niveles de calidad deseados. Estos sistemas abarcan una amplia gama de actividades, como la planificación, la garantía, el control y la mejora de la calidad. Al integrar un sistema de gestión de la calidad, los fabricantes garantizan la coherencia, la eficacia y la mejora continua de sus procesos de producción.
Un SGC suele implicar la aplicación de normas de calidad reconocidas internacionalmente. Estas normas son facilitadas por organizaciones de acreditación, en particular la Organización Internacional de Normalización (ISO). Para los fabricantes, la serie de normas ISO 9000 se encuentra entre las normas más instrumentales orientadas a la calidad. Siendo la raíz de un SGC bien implementado, la ISO 9000 es fundamental para alinear los objetivos de calidad de una empresa con sus procesos operativos y requisitos normativos.
Seguir leyendo sobre las normas ISO en la fabricación.
Implementación de la garantía de calidad en la fabricación
La implementación de la garantía de calidad en la fabricación implica varios pasos clave. A continuación presentamos un resumen de los procesos esenciales. Cada uno de ellos desempeña un papel fundamental en la creación de un marco sólido de garantía de calidad que asegure productos de alta calidad.
- Establecer un Sistema de Gestión de la Calidad. Desarrolle y documente procesos, procedimientos y normas para crear un SGC estructurado. Este sistema sirve de base para un control de calidad coherente en todas las operaciones de fabricación. Adoptar la norma ISO9000 es un primer paso viable para desarrollar un SGC.
- Formar a los empleados. Proporcione una formación completa al personal sobre las normas de calidad, los procedimientos y el uso de las herramientas y equipos pertinentes. Unos empleados bien formados son esenciales para aplicar y mantener eficazmente las prácticas de garantía de calidad.
- Optimización de los procesos. Realice un mapeo de los procesos para identificar los puntos de control críticos, optimizar los flujos de trabajo y aumentar la coherencia de la producción. De este modo se mejora la calidad al aumentar la eficacia y reducir la probabilidad de defectos.
- Garantizar la calidad de los materiales. Trabaje en estrecha colaboración con los proveedores para establecer y mantener las expectativas de calidad de las materias primas y los componentes. Implemente prácticas de gestión de la calidad de los proveedores, incluidas inspecciones y auditorías periódicas.
- Integrar medidas de control de calidad. Incorpore medidas de control de calidad en las distintas fases de producción. Esto incluye inspecciones durante el proceso, pruebas y comprobaciones del producto final para identificar y corregir cualquier variación de las normas de calidad.
- Potenciar el esfuerzo de trazabilidad. Utilice un software de fabricación con trazabilidad integrada. Este software es crucial para mantener registros precisos de los procesos de fabricación y las especificaciones de los productos, lo que permite responder con rapidez a los problemas de calidad.
- Realizar auditorías y aplicar mejoras continuas. Las auditorías internas y externas periódicas evalúan la eficacia del sistema de garantía de calidad. Ayudan a identificar áreas de mejora, garantizar el cumplimiento de las normas y fomentar una cultura de mejora continua de la calidad.
- Definir métodos de mejora. Una característica clave de un sistema eficaz de gestión de la calidad es la mejora de los procesos. La selección de una metodología estructurada, como Lean o herramientas Six Sigma como DMAIC (Design, Measure, Analyze, Improve, Control) u otras, permitirá obtener conclusiones basadas en datos que pueden utilizarse en la optimización de procesos.
La importancia de la garantía de calidad en la fabricación
A continuación, analizaremos algunas de las facetas más importantes de la garantía de calidad en la fabricación.
- Reducción de la tasa de defectos. Reducir la tasa de defectos es un objetivo primordial de la garantía de calidad en la fabricación. Mediante la supervisión de los procesos y las pruebas de los productos, la garantía de calidad ayuda a identificar y rectificar posibles problemas antes de que se conviertan en defectos importantes. Este enfoque proactivo es crucial para evitar productos de mala calidad, garantizar la satisfacción del cliente y proteger la reputación de la marca.
- Cumplimiento. El cumplimiento de la normativa y las normas industriales es fundamental en la fabricación. Los sistemas de control de calidad desempeñan un papel clave en este sentido, ya que garantizan que los productos finales cumplen las normas de seguridad, calidad y otras normas reglamentarias necesarias. Por ejemplo, en el sector de los dispositivos médicos, el estricto cumplimiento de las directrices de la FDA mediante procesos de control de calidad es esencial para la seguridad del paciente y el acceso al mercado.
- Confianza del cliente y de las partes interesadas. La garantía de calidad influye directamente en la confianza de los clientes y las partes interesadas. Al suministrar sistemáticamente productos de alta calidad, los fabricantes pueden reforzar su reputación y fomentar relaciones a largo plazo con clientes y socios comerciales. Esto no se limita a los consumidores finales, sino que se extiende tanto a los proveedores como a los inversores y a los organismos reguladores, todos los cuales desempeñan un papel crucial en el establecimiento de un lugar en el mercado.
- Ahorro de recursos, tiempo y costos. Una garantía de calidad eficaz contribuye significativamente a la optimización de recursos. La detección temprana de defectos y unos protocolos de producción eficaces y seguros ayudan a evitar errores costosos y a evitar el despilfarro de materiales. Esta optimización no sólo mejora los resultados finales, sino que también se ajusta a las prácticas de fabricación sostenible, un aspecto cada vez más importante en el mercado actual, preocupado por el medio ambiente.
- Mejora de la eficacia y la coherencia de la producción. La garantía de calidad contribuye a mejorar la coherencia y la eficiencia de la producción. Mediante la supervisión y el control sistemáticos de los procesos de fabricación, la garantía de calidad ayuda a optimizar las operaciones, lo que se traduce en tiempos de entrega más rápidos y un mayor rendimiento. Esto aumenta la productividad y permite a los fabricantes responder rápidamente a las demandas del mercado y a las necesidades de los clientes.
- Mejora del control de procesos. El control de procesos y el control estadístico de procesos constituyen el núcleo de la garantía de calidad. Se trata de establecer procedimientos operativos normalizados y controles de calidad coherentes que garanticen que todos los aspectos de la producción se supervisan y controlan de cerca. Este nivel de control es crucial para detectar a tiempo las variaciones de las normas. Permite tomar medidas correctivas inmediatas, contribuyendo así a mantener la integridad del proceso de producción.
- Mejora continua. Centrarse en la mejora continua es el sello distintivo de un sistema eficaz de garantía de calidad. Mediante la evaluación y el perfeccionamiento continuos de los procesos, los fabricantes pueden adaptarse a los nuevos retos y avances tecnológicos. Este enfoque proactivo de la gestión de la calidad no sólo ayuda a mantener los niveles de calidad actuales, sino también a identificar oportunidades de innovación y mejora, manteniendo la competitividad de la empresa en un mercado dinámico.
Tendencias en garantía de calidad para las PYMEs
En el mundo de la fabricación, las PYMEs se enfrentan tanto a retos como a oportunidades a la hora de implementar la garantía de calidad. Los recursos limitados exigen un enfoque estratégico. Esto significa a menudo centrarse en las áreas con mayor impacto en la calidad y la satisfacción del cliente, equilibrando al mismo tiempo las limitaciones de presupuesto y personal. Aunque la implementación de algún tipo de SGC es cada vez más vital en la industria de la fabricación, sigue siendo un reto debido a estas limitaciones.
El papel de la transformación digital es cada vez más fundamental en la adopción de sistemas de control de calidad para las pymes. La llegada de las tecnologías de la Industria 4.0, como el Internet de las cosas (IoT), el análisis de macrodatos o la computación en la nube, está transformando por completo la fabricación. Esto permite niveles avanzados de automatización y precisión en los procesos de control de calidad, lo que promete facilitar la detección temprana de defectos, reducir los desechos y mejorar la calidad del producto.
La accesibilidad de los SGC a través de modelos de software como servicio (SaaS) basados en la nube cambia las reglas del juego. Sobre todo porque algunos sistemas MRP y ERP de fabricación han empezado a incorporar mecanismos de control de calidad en sus paquetes. Esto proporciona a las PYMEs herramientas sofisticadas para implementar una sólida gestión de la calidad sin necesidad de inversiones sustanciales.
De cara al futuro, la garantía de calidad en la fabricación va a acelerar su evolución con nuevos avances digitales. La automatización, los análisis basados en IA y la integración de herramientas de realidad virtual y aumentada desempeñarán un papel importante en los procesos de control de calidad. Se espera que esto permita enfoques más predictivos y preventivos de la gestión de la calidad, revolucionando los procesos de formación e inspección. Las pymes que integren eficazmente las prácticas modernas de control de calidad ganarán en eficiencia, calidad del producto y satisfacción del cliente.
Buenas prácticas de garantía de calidad en la fabricación para PYMEs
Por último, daremos un vistazo a seis buenas prácticas de control de calidad para pequeñas y medianas empresas de fabricación.
Implementar un sistema ERP de fabricación
La incorporación de un sistema de planificación de recursos empresariales (ERP) de fabricación es esencial para mejorar los esfuerzos de control de calidad de las PYME. Estos sistemas agilizan la gestión de datos y suelen incluir sistemas de ejecución de la fabricación (MES) y funciones de control de calidad. Esto permite supervisar y gestionar en tiempo real el proceso de producción, garantizando el cumplimiento de las normas de calidad. Muchos sistemas ERP pueden mejorarse aún más mediante integraciones API con soluciones externas, lo que ofrece flexibilidad y adaptabilidad para satisfacer necesidades operativas específicas.
Normalización y reducción de la variabilidad
Un elemento clave para aumentar la calidad constante es estandarizar el proceso de fabricación. Esto implica crear y mantener actualizados los procedimientos normalizados de trabajo (PNT), obtener certificaciones (como la ISO 9000), garantizar el mantenimiento de los equipos y realizar auditorías periódicas. Además, herramientas como la metodología Seis Sigma pueden ser decisivas para mantener unos estándares de calidad constantes. La fabricación ajustada también desempeña un papel crucial en la eliminación de las actividades sin valor añadido y la reducción de los desechos de fabricación, que incluyen los excesos en el transporte, el almacenamiento, la producción y el procesamiento, así como problemas como la repetición de procesos, los retrasos y los defectos.
Trabajo en equipo y formación continua
Las personas son el activo más valioso de cualquier organización. Crear un ambiente de trabajo en equipo e invertir en formación continua son esenciales para aumentar las capacidades tanto individuales como organizativas. Centrarse en crear un entorno de trabajo seguro y limpio también contribuye a aumentar la productividad de los empleados. Al fomentar un equipo cualificado y cohesionado, las PYMEs pueden transformar las materias primas en productos terminados de alta calidad de forma más eficiente.
KPIs estratégicos y comunicación
La implementación de Indicadores clave de rendimiento (KPI) estratégicos de fabricación es crucial para traducir la visión y los objetivos de la organización en metas medibles y alcanzables. La comunicación eficaz es esencial para garantizar que estas métricas contribuyan positivamente a la organización sin afectar negativamente a otros departamentos. Equilibrar los objetivos a corto, mediano y largo plazo, como el volumen de ventas y el rendimiento de la inversión (ROI), es importante para el crecimiento sostenible de las PYMEs.
Crear asociaciones sólidas
Fortalecer las relaciones con los proveedores y clientes adecuados es clave para crear beneficios mutuos y alcanzar los objetivos empresariales. Las PYMEs deben centrarse en estar orientadas al cliente, asegurándose de que sus estrategias se alinean con las necesidades del cliente y no sólo con los procesos internos. Establecer una sólida gestión de proveedores puede conducir a resultados sinérgicos y contribuir al éxito general de la empresa.
Cultura de mejora continua
Adaptarse a los cambios en las preferencias de los clientes, los avances tecnológicos y la dinámica del mercado es crucial para las PYMEs. Implementar una cultura de mejora continua implica actualizar periódicamente la documentación, simplificar los procesos y eliminar controles redundantes y procedimientos burocráticos. Un ERP de fabricación en la nube puede ser una herramienta fundamental para definir, mejorar y mantener los objetivos operativos al facilitar el intercambio de información, la comunicación eficaz y la mejora de las prácticas de fabricación.
Principales aspectos a tener en cuenta
- La garantía de calidad (GC) es un proceso sistemático centrado en asegurar que los productos cumplen los requisitos establecidos y las expectativas de los clientes. Abarca más que la fabricación sin defectos, incluidos materiales de alta calidad, gestión eficaz de la cadena de suministro, personal formado y mucho más.
- La garantía y el control de calidad son aspectos distintos, aunque relacionados, de la gestión de la calidad. Mientras que la garantía de calidad implica planificar y sistematizar los procesos para evitar problemas de calidad, el control de calidad consiste en probar y verificar que los productos cumplen las normas de calidad durante y después de la producción.
- Entre los pasos clave para implementar la garantía de calidad están establecer un SGC, formar a los empleados, optimizar los procesos, garantizar la calidad de los materiales, integrar medidas de control de calidad, mejorar la trazabilidad y realizar auditorías periódicas para la mejora continua.
- Adoptar la norma ISO 9000 e implementar un sistema MRP o un ERP de fabricación con funciones de control de calidad incorporadas es quizá el camino más seguro hacia un control de calidad eficaz para las pequeñas y medianas empresas de fabricación.
Preguntas frecuentes
La garantía de calidad (GC) es crucial en la producción, ya que asegura que los productos cumplen los requisitos especificados y las expectativas de los clientes. Ayuda a mantener la coherencia del producto, reducir los defectos y cumplir la normativa del sector, lo que en última instancia aumenta la satisfacción del cliente y ahorra costos.
En la fabricación, la garantía de calidad y el control de calidad desempeñan funciones diferentes. La garantía de calidad se centra en prevenir los defectos planificando y sistematizando los procesos, mientras que el control de calidad consiste en probar y verificar que los productos cumplen las normas de calidad durante y después de la producción. En resumen, la garantía de calidad se ocupa de la gestión de los procesos, mientras que el control de calidad se ocupa de la evaluación de los productos.
Un ejemplo de garantía de calidad en la fabricación es la implementación de un Sistema de gestión de calidad (SGC) como ISO 9000. Esto implica el establecimiento de procesos estandarizados, la formación periódica de los empleados y la supervisión constante de las operaciones para garantizar que los productos cumplen sistemáticamente las normas de calidad.
El control de calidad consiste en inspeccionar y probar los productos en las distintas fases del proceso de producción. Comprueba si hay defectos y garantiza que el producto final cumple las normas de calidad establecidas. Las actividades de control de calidad pueden incluir inspecciones durante el proceso, pruebas de materiales y revisiones del producto final para identificar y abordar cualquier problema de calidad.
También le puede interesar: ¿Cómo eliminar los cuellos de botella en la fabricación?