¿Cómo calcular la Eficiencia General de los Equipos (OEE)?
La eficiencia general de los equipos o OEE (Overall Equipment Effectiveness) es un KPI que mide la eficacia de las máquinas y los equipos en una instalación de fabricación. El seguimiento de la OEE permite identificar posibles problemas que puedan estar afectando a la eficiencia de la producción.
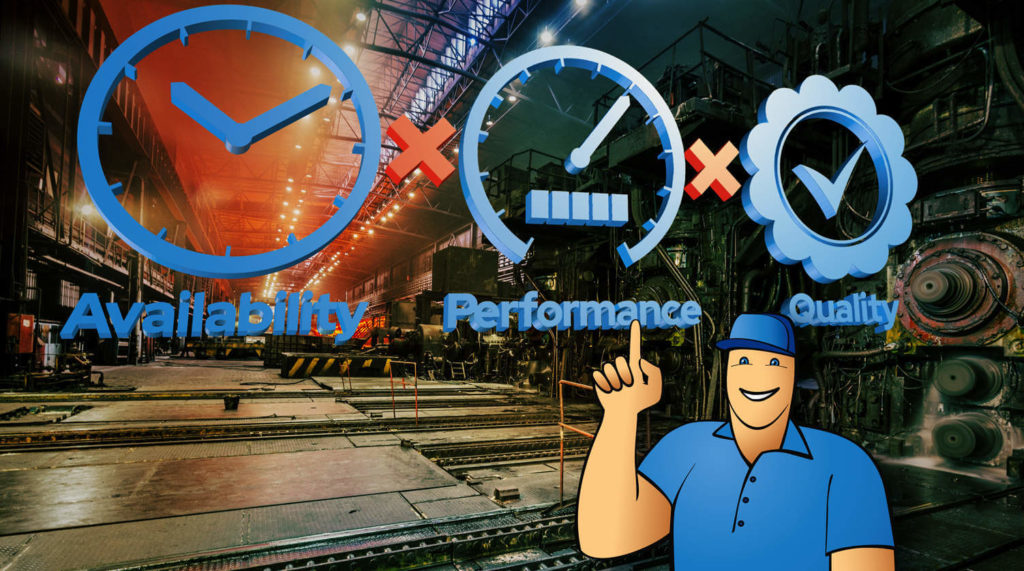
¿Qué es la Eficiencia General de los Equipos (OEE)?
La Eficiencia General de los Equipos (OEE) es un KPI de fabricación que mide la eficiencia alcanzada en un proceso de producción, concretamente la eficacia con la que funcionan las máquinas y los equipos. En términos más básicos, la OEE es la relación entre los siguientes factores:
- La disponibilidad o el tiempo de funcionamiento de su equipo durante un periodo (también llamado tiempo de actividad).
- Rendimiento o número de piezas producidas por periodo (también llamado tasa de proceso).
- Calidad o porcentaje de piezas terminadas que han pasado las inspecciones (también llamado rendimiento).
Presentada como un porcentaje del ideal, la Eficiencia General del Equipo da una indicación de cuánto es posible aumentar la eficiencia en el proceso de producción.
¿Por qué es importante la Eficiencia General de los Equipos?
La Eficiencia General de los Equipos es uno de los mejores indicadores clave de rendimiento que se pueden seguir en la fabricación. Esto se debe a que ofrece a los directivos una muy buena idea del rendimiento del departamento de producción, teniendo en cuenta muchos aspectos.
El seguimiento de la OEE le permite:
- Comprender la eficacia del proceso de producción
- Ver si las cosas mejoran o empeoran con el tiempo
- Comparar el rendimiento de varias estaciones de trabajo
- Descubrir las áreas que se pueden mejorar
Por ejemplo, el desglose de la OEE en sus tres componentes le permite ver si una sola área está teniendo un efecto negativo en la eficiencia general.
Pero primero entendamos cómo calcular la OEE y luego entremos en los detalles de cómo utilizarla.
¿Cómo calcular la Eficiencia General de los Equipos?
Como se ha dicho anteriormente, la Eficiencia General de los Equipos se compone de tres medidas subyacentes: Disponibilidad, Productividad y Calidad. Cada una de esas tres medidas se ha diseñado para que excluya los efectos de las otras dos.
Disponibilidad
La disponibilidad muestra el tiempo de actividad puro o el tiempo que la estación de trabajo o la máquina estuvo realmente en funcionamiento. Se representa como un porcentaje del tiempo ideal programado, con pérdidas de disponibilidad que se acumulan debido a eventos como la configuración y el calentamiento, los ajustes y las averías.
Disponibilidad = Tiempo de ejecución real / Tiempo planificado
Por ejemplo, si un programa de producción especifica un tiempo de ejecución de 10 horas al día, pero la configuración y el calentamiento tardan 30 minutos y durante el día hay que hacer seis ajustes, cada uno de los cuales consume 10 minutos, entonces el tiempo de ejecución real es de 8,5 horas.
Por lo tanto, la tasa de disponibilidad es:
8.5 / 10 = 0.85 = 85%
Eso significa que el puesto de trabajo estuvo disponible el 85% del tiempo.
Rendimiento
El rendimiento, también conocido como tasa de proceso, mide la velocidad a la que la estación de trabajo o la máquina procesa las unidades. También se representa como un porcentaje del ideal, siendo las pérdidas de rendimiento causadas por problemas logísticos, búsqueda de herramientas, pequeñas paradas, ineficacia del operario, disminución de la velocidad de la máquina, etc.
Rendimiento = (Unidades totales x Tiempo de ciclo ideal) / Tiempo de ejecución real
Sigamos con el ejemplo anterior y digamos que del turno de 10 horas, una máquina tuvo un tiempo de ejecución real de 8,5 horas. Digamos que el tiempo de ciclo ideal por unidad es de 3 minutos (0,05 h) y que la estación de trabajo procesó un total de 140 unidades en esas 8,5 horas.
Por lo tanto, la tasa de rendimiento es:
(140 x 0.05) / 8.5 = 0.82 = 82%
Eso significa que la máquina funcionó al 82% de su velocidad ideal.
Calidad
La calidad en OEE, también llamada rendimiento del proceso, representa las unidades buenas procesadas como porcentaje de las unidades totales. Las pérdidas de calidad se producen, por ejemplo, por las pérdidas de arranque y los defectos.
Calidad = Piezas buenas / Piezas totales
Continuemos con el ejemplo anterior, en el que se procesaron un total de 140 unidades durante un tiempo de ejecución de 8,5 horas. De esas 140 unidades, 135 no tenían defectos.
Por lo tanto, el índice de calidad era:
135 / 140 = 0.96 = 96%
Esto significa que el 96% de las unidades procesadas no tenían defectos.
Eficiencia General de los Equipos
Ahora podemos finalmente calcular la OEE utilizando la fórmula:
OEE = Disponibilidad x Rendimiento x Calidad
Con los números de los ejemplos anteriores, llegaremos a una OEE de:
85% x 82% x 96% = 67%
Por tanto, la eficiencia total del puesto de trabajo era del 67%. Ahora podemos analizar e identificar las áreas de mejora.
¿Cómo utilizar la OEE para mejorar su negocio?
La Eficiencia General de los Equipos puede ser de gran ayuda para detectar áreas problemáticas y cuellos de botella en el proceso de producción.
Esto le permite comparar varios equipos entre sí y ver cómo se comportan en diferentes situaciones. Esto le ayuda a identificar las oportunidades de mejora en todos los ámbitos. Por ejemplo, si una pieza de la maquinaria tiene una puntuación de OEE significativamente más baja que otras, puede indicar que hay problemas con la forma en que se está operando o manteniendo, y esas cuestiones deben abordarse antes de que se conviertan en problemas graves.
El examen de las métricas subyacentes -Disponibilidad, Rendimiento y Calidad- podría ayudar a identificar las áreas que necesitan ser tratadas:
- Si la disponibilidad es baja, hay que optimizar los tiempos de preparación, hacer un mantenimiento preventivo, etc.
- Si el rendimiento es bajo, hay que evitar pequeñas paradas y retrasos, mejorar la eficacia de los operarios, etc.
- Si la calidad es baja, hay que minimizar las pérdidas por arranque y otros defectos.
El objetivo es mejorar los procesos mediante la definición de una métrica que muestre la salud general y el progreso de la operación. Todos los empleados que tienen acceso a los indicadores deben ser educados en la esencia de la OEE y sus métricas subyacentes y cómo podrían ayudar personalmente a elevarla.
Es importante tener en cuenta que la OEE y sus métricas subyacentes sólo pueden utilizarse para comparar una fábrica consigo misma, no con otras fábricas, ya que las medidas subyacentes pueden variar mucho y no existe una norma industrial. Tampoco es una herramienta en sí misma que pueda mejorar las cosas, es simplemente un indicador importante que refleja la situación. Son los trabajadores de la fábrica los que tienen que entender lo que les dice la OEE y actuar adecuadamente.
El objetivo de mejorar la OEE debe hacerse de forma conservadora: no un 30% al año, sino quizás un 3% al año. Un solo percentil de crecimiento puede ser un gran paso adelante y requeriría reevaluar los antiguos procesos, implantar otros nuevos y formar al personal. Lo importante es la mejora continua.
Si no hace un seguimiento de la OEE a lo largo del tiempo, no sabrá si sus esfuerzos están dando resultado, o si hay otra forma de utilizar sus recursos de forma más eficaz. El seguimiento periódico de la OEE proporciona datos útiles sobre lo que constituye una operación eficaz y sobre lo que aún puede mejorarse.
¿Qué es el TEEP y cómo se calcula?
El Rendimiento Total Efectivo del Equipo o TEEP (Total Effective Equipment Performance) es una medida del rendimiento de los equipos que está estrechamente relacionada con la OEE. Se utiliza para indicar la eficiencia total de una estación de trabajo y cuánto puede aumentar el rendimiento de producción de una estación de trabajo, teniendo en cuenta la OEE así como el tiempo de funcionamiento potencial total, es decir, 24 horas al día, 168 horas a la semana, etc.
La fórmula TEEP incluye cuatro componentes clave: disponibilidad, rendimiento, calidad y utilización. Por lo tanto, la fórmula TEEP es:
TEEP = OEE x Utilización
La utilización se refiere al porcentaje de tiempo que una máquina está prevista que esté en funcionamiento frente al tiempo total disponible en un periodo.
Utilización = Tiempo planificado / Tiempo total
Continuando con el ejemplo anterior de OEE de un día (24 horas) con un único turno de 10 horas, llegaremos al siguiente índice de utilización:
10 / 24 = 0.42 = 42%
Con nuestra OEE previamente calculada del 67%, el TEEP será:
67% x 42% = 28%
Eso significa que la estación de trabajo está funcionando a un 28% de eficiencia.
Además de aumentar la OEE, la instalación podría añadir otro turno de 10 horas o crear tres de 8 horas para aumentar el TEEP. Si ya se trabaja las 24 horas del día, el TEEP es igual al OEE.
El seguimiento de estas dos métricas, OEE y TEEP, junto con sus indicadores subyacentes -Disponibilidad, Rendimiento, Calidad y Utilización- ofrece una buena visión general de la salud general de la producción e indica la dirección que toma la empresa. Estas pueden ser métricas importantes que ayudan a tomar decisiones sobre qué hacer a continuación y hacia dónde dirigir la atención.
OEE en el software ERP de fabricación
Aunque los cálculos anteriores parecen bastante claros y sencillos, calcular el OEE y el TEEP de cada puesto de trabajo de forma coherente es una tarea que requiere mucho tiempo y es propensa a errores, especialmente cuando se realiza mediante informes manuales.
Sin embargo, los sistemas ERP de fabricación están diseñados para recoger precisamente los datos necesarios para los cálculos de OEE. Si desea un sistema que le ayude a realizar un seguimiento de los datos de producción necesarios para los cálculos de OEE, debe buscar funcionalidades como los informes de taller (con seguimiento de tiempos y unidades) y el control de calidad.
Los mejores sistemas ERP con funcionalidad de software de taller incluso calculan automáticamente la OEE y generan gráficos visuales que le permiten seguir fácilmente los cambios en la OEE durante períodos específicos. Al disponer de esta información rápida y fácilmente accesible, podrá realizar las correcciones necesarias mucho antes y mejorar la eficiencia de su operación a un ritmo más rápido.
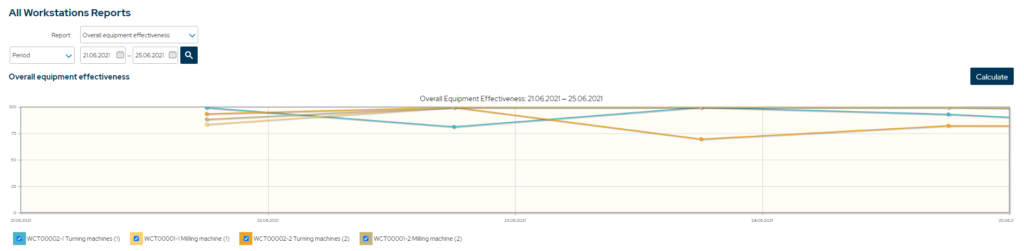
Principales aspectos a tener en cuenta
- La Eficiencia General de los Equipos (OEE) es un KPI que mide la eficacia de las máquinas y equipos en la fabricación.
- La OEE es una relación entre la disponibilidad, el rendimiento y la calidad.
- El seguimiento de la OEE permite a los fabricantes conocer su eficiencia de producción y saber cuánto podría aumentar y dónde, así cómo ha cambiado a lo largo del tiempo.
- Si la disponibilidad es baja, hay que optimizar los tiempos de preparación, hacer un mantenimiento preventivo, etc.
- Si el rendimiento es bajo, hay que evitar pequeñas paradas y retrasos, mejorar la eficacia de los operarios, etc.
- Si la calidad es baja, hay que minimizar las pérdidas por arranque y otros defectos.
- La OEE sólo puede utilizarse para comparar la empresa consigo misma, no con otras empresas.
- El TEEP o Rendimiento Total Efectivo del Equipo es una métrica que se utiliza para medir cuánto podría aumentar el rendimiento de la producción.
- El uso de un sistema ERP de fabricación permite a las empresas realizar un seguimiento de OEE y TEEP sin esfuerzo.
También te puede gustar: Utilización de la capacidad – Una guía sencilla