Control de producción – Guía práctica
El control de producción es el conjunto de procesos que gestionan y supervisan los flujos de trabajo que intervienen en la fabricación de un producto. La aplicación de prácticas y herramientas fiables de control de producción aumenta la eficacia en el lugar de trabajo, mejora la gestión de la cadena de suministro y reduce los costos.
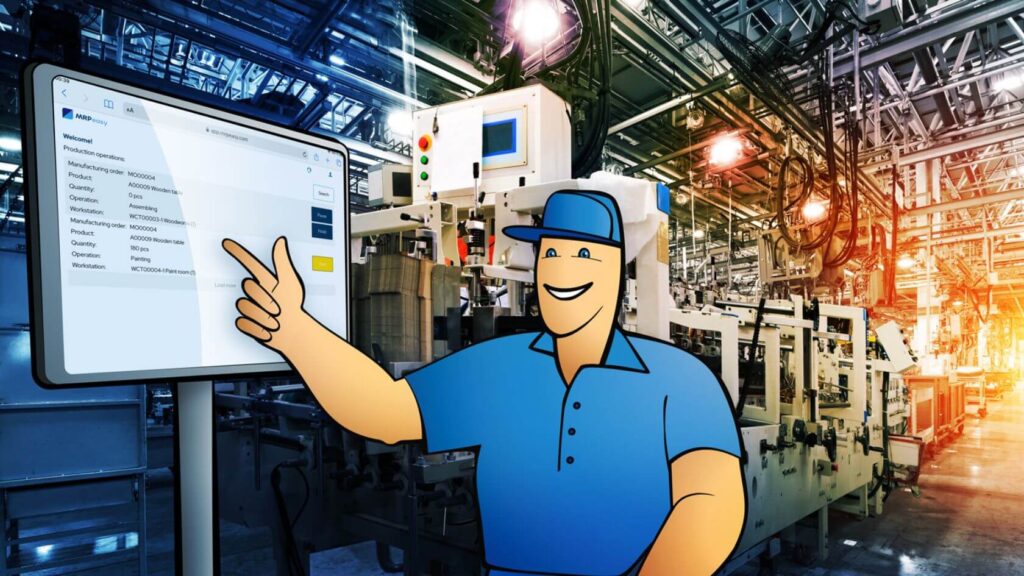
¿Qué es el control de producción?
El control de producción es el conjunto de procesos dentro de la fabricación que gestiona, orquesta y supervisa el flujo de materiales y actividades en un proceso de producción. Esto puede incluir la planificación de la demanda, la planificación de la capacidad, la programación de la producción, la gestión de inventarios, el cálculo de costos, la supervisión de la planta de producción, el control de calidad y otras actividades relacionadas con la producción, pero también proporcionar a los clientes los tiempos de entrega y el estado de los productos.
Al coordinar eficazmente las distintas fases de la producción, desde las materias primas hasta los productos terminados, el control de producción garantiza que los procesos de fabricación se desarrollen sin problemas, con eficacia y dentro de los tiempos establecidos. Por lo tanto, no se puede subestimar su importancia, ya que repercute directamente en su rendimiento operativo.
El control de producción es una parte esencial de una eficaz gestión de las operaciones de fabricación en empresas de cualquier tamaño.
¿Por qué es importante el control de producción?
El control de producción desempeña un papel crucial en la fabricación y es esencial para el éxito de una empresa. Estas son las razones de su importancia:
- Optimiza la planificación de la producción. El control de producción garantiza que la planificación de las operaciones de fabricación se ajuste al flujo de trabajo real. Esta alineación es vital para cumplir los objetivos fijados y mantener la eficiencia.
- Aumenta la eficacia de la producción. El control de producción agiliza los procesos en la línea de producción, reduciendo los cuellos de botella que pueden interrumpir las operaciones de producción.
- Mejora la gestión de la cadena de suministro. Al integrar los procesos de compras y de la cadena de suministro, el control de producción ayuda a gestionar los recursos con eficacia, evitar desabastecimientos y garantizar que los materiales estén disponibles cuando se necesiten.
- Facilita una previsión precisa de la demanda. El control de producción facilita una previsión de la demanda precisa mediante la integración de datos en tiempo real procedentes de diversas fases del proceso de fabricación, lo que permite comprender de forma exhaustiva las tendencias actuales del mercado y las necesidades de los clientes. Este proceso garantiza que la producción se ajuste a la demanda del mercado, reduciendo así el riesgo de sobreproducción o desabastecimiento.
- Garantiza la calidad del producto. Al hacer cumplir las normas de calidad en todo el proceso de fabricación, el control de producción garantiza que el producto terminado cumpla los criterios de calidad deseados.
- Reduce los costos de producción. Un control eficaz de la producción minimiza los desechos y optimiza el uso de los recursos, lo que se traduce en menores costos de producción y mejores resultados financieros.
- Mantiene los tiempos de entrega. El control de producción desempeña un papel fundamental a la hora de garantizar que las operaciones de fabricación cumplan los tiempos de entrega, lo que es crucial para la satisfacción del cliente y el mantenimiento de la reputación de la empresa.
En resumen, el control de producción es vital para que las operaciones de fabricación sean eficaces y rentables. Garantiza el buen funcionamiento de los procesos de producción, el mantenimiento de la calidad de los productos y el cumplimiento de las expectativas de los clientes, al tiempo que gestiona eficazmente los costos y los recursos.
Estado del control de la producción en las pequeñas empresas
Históricamente, las empresas de fabricación gestionaban la producción manualmente, utilizando programas de producción en papel, realizando estimaciones y dando instrucciones verbales. Con el tiempo, esto dio paso a las hojas de cálculo y luego al software local diseñado para ayudar a áreas funcionales específicas a completar sus tareas de manera más eficiente.
Estos sistemas surgieron de la creciente complejidad de la fabricación a escala de grandes volúmenes. Las pequeñas y medianas empresas (PYME) podían utilizar equipos para producir productos con rapidez. Pero la creciente velocidad de los equipos obligó a utilizar programas informáticos para realizar tareas que las simples estimaciones y hojas de cálculo no podían controlar eficazmente.
Tradicionalmente, las PYMEs han estado en desventaja frente a competidores más grandes. Con programas informáticos locales antiguos o análisis arcaicos basados en hojas de cálculo, las PYMEs no podían desplegar recursos para un control adecuado de la producción, lo que generaba despilfarro y aumentaba los costos.
Pero para una PYME nueva o en crecimiento, el control de producción es esencial. Puede impulsar la mejora de procesos, reducir costos y mejorar las entregas. Y hoy en día, las PYMEs pueden beneficiarse de sistemas de control de producción que combinan y simplifican los sistemas heredados en silos con los que sus competidores más grandes han luchado durante muchos años. Al poder aprovechar una plataforma de software unificada para el control de producción, los fabricantes pueden evitar los mismos errores y producir al mismo nivel que las grandes empresas.
8 pasos para un control de producción eficaz
Los pasos esenciales del control de producción en un entorno de fabricación abarcan un proceso integral para garantizar la eficacia, la calidad y la entrega puntual de los productos. Estos pasos incluyen:
- Planificación de la producción. Este paso inicial implica fijar objetivos de producción y crear un plan detallado para alcanzarlos. Incluye determinar la capacidad de producción, los recursos necesarios, los plazos establecidos y la programación de la producción.
- Enrutamiento. La hoja de ruta en la fabricación decide el flujo de trabajo y la secuencia de operaciones dentro del proceso de producción. Esboza el camino que sigue un producto desde el principio hasta el final de la producción, detallando la secuencia de operaciones, las máquinas o centros de trabajo implicados y los métodos que deben utilizarse.
- Programación. Este paso consiste en asignar plazos específicos a las distintas fases de producción. La programación de la producción garantiza que cada tarea se complete dentro de un plazo establecido, optimizando el uso de los recursos y ajustándose a los compromisos de entrega.
- Despacho. El despacho es la fase de ejecución en la que se autoriza el trabajo planificado y se envía a la planta de producción. Incluye la emisión de las instrucciones, documentos y materiales necesarios para iniciar el proceso de producción.
- Seguimiento y control. Este paso crucial implica el seguimiento del progreso de la producción con respecto al plan. Incluye la supervisión del uso de los recursos, el flujo de trabajo y el cumplimiento de los plazos establecidos. Cualquier desviación o cuello de botella se identifica para adoptar medidas correctivas.
- Inspección y control de calidad. El control de calidad está integrado en todo el proceso de producción, con inspecciones en distintas fases para garantizar que el producto cumple las normas de calidad establecidas.
- Medidas correctivas. Cuando se detectan discrepancias o problemas, se toman medidas correctivas para realinear el proceso de producción con el plan original. Esto puede implicar ajustes en la programación, el flujo de trabajo o la asignación de recursos.
- Retroalimentación y mejora continua. El último paso consiste en analizar el ciclo de producción completado para identificar áreas de mejora. La retroalimentación se utiliza para perfeccionar los planes de producción futuros, aumentar la eficiencia y mejorar la calidad del producto.
Estos pasos, cuando se gestionan eficazmente, garantizan que el control de producción contribuya al buen funcionamiento de los procesos de fabricación, cumpliendo los objetivos tanto de calidad como de entrega.
Sistemas de control de producción
Los sistemas de control de producción pueden dividirse a grandes rasgos en dos grandes grupos: sistemas de tipo push y pull. Profundicemos un poco más en el significado real de estos términos:
- Los sistemas push se basan en previsiones de la demanda, es decir, en la predicción de la demanda futura. En este caso, los procesos de fabricación se inician sin esperar a los pedidos reales de los clientes. Por tanto, los productos son “empujados” (pushed) a través de la cadena de suministro independientemente de la demanda inmediata. Esto también se denomina producción para almacenamiento (MTS) ya que los productos se fabrican para almacenarlos y venderlos más tarde.
- Por otra parte, los sistemas pull dependen de la demanda real. En este caso, el proceso de producción se inicia con un pedido del cliente. Por tanto, los productos son “sacados” (pulled) por el cliente a través de la cadena de suministro. En un sistema pull, los productos se fabrican a medida que se necesitan, lo que minimiza los desechos y reduce el exceso de inventario y sus costos asociados. Los sistemas pull incluyen la fabricación bajo pedido y el ensamblaje bajo pedido, la configuración bajo pedido y la ingeniería bajo pedido.
- Los sistemas híbridos push-pull combinan elementos de los sistemas push y pull. Normalmente, las fases iniciales de la producción se inician de acuerdo con las previsiones, mientras que las fases finales se activan en función de la demanda real. Por ejemplo, un fabricante de automóviles puede producir componentes estándar como motores, chasis, sistemas de transmisión, etc. según la previsión, mientras que un pedido de un cliente desencadenaría el ensamblaje final en el que se aplican las personalizaciones. Por tanto, el producto base se produciría para su almacenamiento y las personalizaciones se añadirían bajo pedido.
La decisión de fabricar con el sistema push, pull o push-pull dependerá del producto y de su demanda. Los productos estándar de venta rápida suelen fabricarse con el sistema push, mientras que los artículos personalizados se fabrican con el método pull.
Técnicas y herramientas de control de producción para PYMEs
Hay muchas técnicas de control de producción que pueden implementarse en una empresa de fabricación en crecimiento sin hacer grandes inversiones. He aquí algunas de las opciones de eficacia probada:
Kanban
Kanban es una herramienta de fabricación ajustada diseñada para mejorar la eficiencia y minimizar los desechos en los procesos de producción. De origen japonés, Kanban utiliza señales visuales —a menudo tarjetas— para representar los elementos de trabajo en un ciclo de producción. Se trata de un sistema pull, lo que significa que la producción se basa en la demanda real del cliente y no en previsiones.
En un sistema Kanban típico, una tarjeta se desplaza por un tablero o se pasa entre equipos a medida que un producto avanza por las distintas fases del proceso de fabricación, desde la planificación hasta la finalización. El número de tarjetas permitido en cada etapa está limitado para reducir el inventario de trabajo en proceso y los cuellos de botella. Esta naturaleza visual de Kanban permite a los equipos seguir el progreso e identificar rápidamente las limitaciones o la escasez de existencias. Al producir sólo lo que se necesita cuando se necesita, Kanban ayuda a reducir el exceso de inventario y a mejorar la eficiencia del flujo de trabajo.
Un ejemplo sencillo de Kanban sería cuando una tarjeta llega al final de la cadena de suministro (es decir, el producto se expide al cliente) y se envía de nuevo al inicio para desencadenar otro ciclo de producción. Otro enfoque sencillo de Kanban es el sistema de dos contenedores (two-bin system), en el que se mantienen dos contenedores de un artículo en el punto de consumo. Cuando un contenedor se vacía, se envía a reabastecer. De este modo, los materiales se introducen en el sistema en función de la demanda real, evitando desabastecimientos y excesos de existencias.
CONWIP
CONWIP o Trabajo constante en proceso (Constant Work-in-Process) es una técnica influenciada por Kanban en la que un número determinado de tarjetas o fichas que representan cada una un único producto circulan por el proceso. Cuando se termina de trabajar en un producto, la ficha se devuelve al principio, donde puede utilizarse para empezar a trabajar en otro artículo o lote. Cuando no quedan fichas en el punto inicial del proceso de producción, no pueden iniciarse nuevos procesos de producción.
Imaginemos una fábrica que produce productos electrónicos. Digamos que hay 50 tarjetas CONWIP disponibles para toda la línea de producción. Cada aparato que inicia la producción lleva una tarjeta desde el principio del proceso. A medida que los artículos avanzan por las distintas fases –desde el ensamblaje de los componentes hasta la instalación del software, pasando por los controles de calidad–, la tarjeta se desplaza con ellos.
Cuando un dispositivo (gadget) está totalmente ensamblado y pasa el control de calidad final, se considera terminado, y la tarjeta asociada se devuelve al inicio del proceso. En este punto, se puede iniciar un nuevo dispositivo, tomando la tarjeta devuelta. Si las 50 tarjetas están en uso (es decir, hay 50 dispositivos en distintas fases de producción), no se pueden iniciar nuevos dispositivos, lo que evita la sobrecarga de la línea de producción.
Justo a tiempo (JIT)
Justo a tiempo (JIT) o Just-in-time, es un método de gestión de la producción de tipo pull en el que los materiales se piden y los productos se producen justo a tiempo para su consumo o expedición. Esto significa que los proveedores no entregan grandes cantidades de piezas para almacenarlas en el almacén de la planta, sino que las entregan en sincronía con el programa de producción.
Este enfoque reduce la necesidad de grandes espacios de almacenamiento y de una amplia gestión de inventarios, lo que disminuye los costos de mantenimiento. Cuando se aplica con éxito, el sistema JIT también puede dar lugar a mejoras significativas en la eficiencia de la fabricación, la reducción de desechos y una respuesta más rápida a las necesidades del cliente y los cambios del mercado.
Para ser eficaz, el sistema JIT requiere una coordinación precisa y unas relaciones sólidas con los proveedores, así como un proceso de producción estable. La mejor forma de utilizar este método es con un software de fabricación compatible con la programación regresiva, lo que significa que las actividades de producción pueden programarse a partir del momento de la expedición.
Por ejemplo, si un concesionario encarga autos a un fabricante de automóviles que utiliza el método JIT, el fabricante iniciará la producción en el último minuto posible, entregando los autos justo cuando estén terminados, evitando así la acumulación de existencias de productos terminados.
Planificación de requerimientos de materiales (MRP I)
La planificación de requerimientos de materiales (MRP I) es uno de los métodos de planificación y control de producción basados en software más antiguos, ya que se desarrolló por primera vez en la década de 1950. MRP integra datos de previsiones de demanda, registros de inventario y listas de materiales (BOM) para calcular las cantidades de materiales y componentes necesarios, así como los plazos para pedirlos y recibirlos.
Imaginemos, por ejemplo, una empresa que fabrica bicicletas. El Programa Maestro de Producción (MPS) de la empresa podría indicar que se van a producir 500 bicicletas en el próximo mes. Utilizando el software MRP, el jefe de producción introduce esta demanda en el sistema. A continuación, el MRP calcula cuántas unidades de cada componente (según la lista de materiales) se necesitan para fabricar 500 bicicletas, teniendo en cuenta las existencias en almacén.
Por ejemplo, si la empresa ya tiene 200 neumáticos en inventario pero necesita 1.000 neumáticos para 500 bicicletas (dos por bicicleta), el sistema MRP recomendará pedir 800 neumáticos adicionales. También calculará cuándo deben realizarse estos pedidos en función de los tiempos de entrega de los proveedores, garantizando que todos los materiales lleguen a tiempo para la producción sin crear un exceso de inventario.
Aunque tradicionalmente MRP I es un sistema de tipo push, también puede utilizarse para la planificación de materiales en sistemas pull. Cada vez que llega un pedido de un cliente, pueden calcularse instantáneamente los requerimientos de materiales y los tiempos de pedido para esa orden en particular.
Planificación de recursos de fabricación (MRP II)
La planificación de recursos de fabricación (MRP II) es una ampliación del sistema básico MRP I. Mientras que MRP I se centra principalmente en el control de materiales e inventarios, MRP II incluye componentes adicionales como la planificación de la capacidad, la programación de la producción y la elaboración de informes, el seguimiento de inventarios y pedidos, el control de calidad, etc. Por lo tanto, integra todas las funciones de fabricación en un solo sistema, proporcionando a las empresas una visión completa de su funcionamiento. Cuando a las funciones de planificación de los recursos de fabricación se añaden un CRM y un módulo financiero, el software también puede denominarse sistema ERP de fabricación.
En un sistema push, MRP II puede utilizar las listas de materiales y la previsión de la demanda o el plan maestro de producción (MPS) para crear programas muy precisos de producción y compras.
En un sistema pull, puede crear y actualizar instantáneamente la programación cada vez que entra un nuevo pedido, lo que permite a los fabricantes ofrecer a sus clientes estimaciones precisas de plazos y costos en unos pocos clics.
Independientemente del tipo de sistema de producción, MRP II o ERP de fabricación permite a las empresas de fabricación lograr una trazabilidad de extremo a extremo, supervisar la eficiencia de la producción, realizar un seguimiento del progreso de los pedidos y los niveles de inventario, establecer puntos de pedido de inventario, realizar análisis financieros y mucho más para situar a la empresa en el camino de la mejora continua y el crecimiento sostenible.
Principales aspectos a tener en cuenta
- El control de producción es el proceso de gestión del flujo de materiales y actividades en la fabricación, que afecta a todo, desde la planificación de la demanda hasta el control de calidad.
- Garantiza la eficacia del flujo de trabajo y el cumplimiento de los planes y programaciones de producción, reduciendo los costos y permitiendo a las empresas cumplir los objetivos de producción y realizar las entregas a tiempo.
- Al integrar los procesos de compras y cadena de suministro, el control de producción gestiona eficazmente los recursos y evita el desabastecimiento y la acumulación de exceso de existencias.
- Al integrar datos en tiempo real, el control de producción ayuda a prever la demanda con precisión, alineando la producción con la demanda del mercado.
- Las prácticas rigurosas de control de producción también hacen cumplir las normas de calidad en todo el proceso de fabricación, lo que garantiza la alta calidad del producto.
- Las pequeñas y medianas empresas pueden aprovechar los modernos sistemas de control de producción, como el MRP o el software ERP de fabricación, para mejorar los procesos y reducir costos, lo que les permite competir eficazmente con empresas más grandes.
Preguntas frecuentes
El control de producción se refiere al proceso de gestionar, orquestar y supervisar el flujo de materiales y actividades en un entorno de fabricación para garantizar la eficacia de las operaciones de producción.
Las etapas del control de producción suelen incluir la planificación de la producción, el enrutamiento, la programación, el despacho, el seguimiento y la supervisión, la inspección y el control de calidad, las medidas correctivas y la retroalimentación para la mejora continua.
El principal objetivo del control de producción es garantizar que los procesos de fabricación se desarrollen con eficiencia y eficacia, cumpliendo las normas de calidad y los tiempos de entrega establecidos, al tiempo que se optimiza la utilización de los recursos y se minimizan los costos de producción.
También le puede interesar: Control de stock – Una guía sencilla para PYMEs