Planificar-Hacer-Verificar-Actuar (PDCA) – Implementación del PDCA en la fabricación
La mejora continua es una fase importante de la fabricación moderna. Una de las metodologías más conocidas es Planificar-Hacer-Verificar-Actuar, o PDCA por sus siglas en inglés. En este artículo analizamos los principios de PDCA, sus ventajas y la mejor forma de llevarlo a cabo.
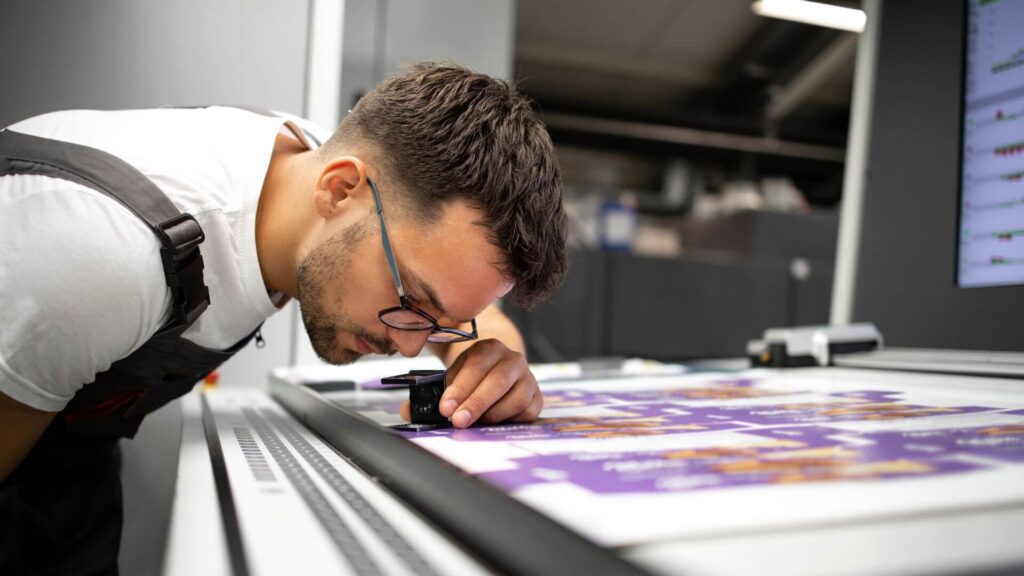
¿Qué es Planificar-Hacer-Verificar-Actuar?
Planificar-Hacer-Verificar-Actuar (PDCA – Plan, Do, Check, Act) es un método de gestión empresarial de cuatro pasos cuyo objetivo es aplicar la mejora continua en la gestión de procesos empresariales. A veces también denominado Planificar-Hacer-Estudiar-Actuar o ciclo PDSA, es un modelo repetitivo que fomenta un enfoque disciplinado e iterativo de la resolución de problemas. Las cuatro fases –Planificar, Hacer, Verificar, Actuar– proporcionan un enfoque sencillo pero eficaz para gestionar el cambio y garantizar que las ideas se prueban adecuadamente antes de comprometerse a su aplicación completa.
El PDCA se originó con Walter Shewhart, estadístico e innovador en la gestión de la calidad. Sin embargo, fue el economista W. Edwards Deming quien popularizó el modelo. Deming destacó la importancia de la interacción constante entre investigación, diseño, pruebas y producción como base para la mejora continua. Como tal, el PDCA también se denomina a veces “ciclo de Deming”, “rueda de Deming” o “ciclo de Shewhart”.
La implementación del ciclo PDCA en la fabricación tiene varias ventajas, como el enfoque sistemático para la identificación y resolución de problemas, la mejora de la comunicación entre departamentos y el fomento de una cultura estratégica de mejora continua. En el cambiante sector de la fabricación, el PDCA ayuda a las empresas a mantener su competitividad aumentando su capacidad de adaptación al cambio, mejorando la eficacia y optimizando la calidad de los productos.
PDCA y otros métodos de mejora continua
Aunque el PDCA es un modelo destacado para mejorar los procesos empresariales, existen otros modelos de mejora continua (IC), cada uno con su enfoque y su conjunto de herramientas. A continuación se presentan cuatro de estos modelos y se explica en qué se diferencian del PDCA y en qué se complementan:
- Kaizen es un modelo japonés de mejora contínua que hace hincapié en la participación de todos los miembros de la empresa, desde los directivos hasta los operarios de taller, para centrarse en pequeñas mejoras diarias de la calidad. A diferencia de los pasos estructurados del PDCA, el Kaizen fomenta pequeños cambios que conducen a mejoras importantes con el tiempo. Al igual que el PDCA, el Kaizen también es cíclico, aunque se trata más de una mentalidad o parte de la cultura de una empresa que de un único proceso.
- La fabricación ajustada es una metodología centrada en la fabricación cuyo objetivo es reducir los despilfarros de fabricación como el despilfarro de tiempo, recursos, habilidades, etc., al tiempo que aumenta la productividad. Introduce herramientas específicas, como el mapeo del flujo de valor, que ayudan a identificar y eliminar los despilfarros. Estas herramientas pueden funcionar bien junto con el PDCA para identificar y resolver problemas de fabricación específicos.
- Six Sigma es una metodología estadounidense de mejora de procesos desarrollada en Motorola en los años 80 que se basa principalmente en el análisis de datos para mejorar la calidad. Sigue un conjunto específico de pasos conocidos como DMAIC (Definir, Medir, Analizar, Mejorar, Controlar) para detectar y resolver defectos o cuellos de botella en los procesos del sistema. En comparación con PDCA, Six Sigma es más detallado y se basa más en los datos.
- El análisis de causa raíz es un proceso de gestión de la calidad que trata de encontrar las razones subyacentes a los problemas para garantizar que no vuelvan a ocurrir. Suele emplearse en la fase de planificación o verificación del PDCA cuando es necesario profundizar en un problema para averiguar qué ha fallado.
El proceso PDCA
El ciclo Planificar-Hacer-Verificar-Actuar crea un proceso estructurado para identificar y probar sistemáticamente los cambios y, a continuación, aplicar las estrategias exitosas a mayor escala. Cada fase se basa en la anterior, lo que garantiza que las mejoras se basan en datos sólidos y pruebas en el mundo real, lo que ayuda a perfeccionar los procesos y lograr mejoras sostenidas de la productividad.
Repasemos las etapas con un poco más de detalle.
Planificar
En la fase Planificar se sientan las bases de las posibles mejoras. En esta fase, los equipos identifican las áreas problemáticas que necesitan mejoras, establecen objetivos claros y tangibles, formulan hipótesis sobre qué cambios podrían conducir a mejores resultados y trazan indicadores clave de rendimiento (KPI) para medir los resultados del próximo ciclo PDCA.
La fase de planificación implica una investigación exhaustiva y la recopilación de datos para comprender los procesos actuales y detectar las ineficiencias. A continuación, se desarrollan planes para implementar soluciones diseñadas para abordar los problemas identificados, que se completan con métricas de fabricación para guiar las siguientes fases.
Veamos un ejemplo. Una pequeña empresa identifica un problema: un despilfarro excesivo de material en su cadena de producción. El equipo se fija el objetivo claro de reducir los despilfarros en un 20% en un plazo de tres meses. Recopilan datos sobre los niveles actuales de despilfarros, analizan las ineficiencias del flujo de trabajo y plantean la hipótesis de que el ajuste de la configuración de la máquina de corte podría minimizar el exceso de material. A continuación, se desarrolla un plan detallado para probar estos nuevos ajustes, que incluye cómo medirán los despilfarros durante el periodo de prueba.
Hacer
A continuación, la fase Hacer pone en marcha el plan de forma controlada y a pequeña escala para comprobar la eficacia de los cambios propuestos. Esta fase experimental es crucial para mitigar los riesgos, ya que limita el alcance de la aplicación a un tamaño manejable, lo que facilita la observación de los resultados y la recopilación de datos valiosos sin interrumpir toda la operación. Es esencialmente un ensayo de lo que se ha planeado que proporciona un primer vistazo a las mejoras potenciales.
Siguiendo con nuestro ejemplo, el fabricante aplica a continuación los nuevos ajustes en una sola de sus máquinas de corte. Esto permite supervisar los cambios sin alterar toda la línea de producción, minimizando así el riesgo. Durante la fase Hacer, el fabricante sigue de cerca la cantidad de despilfarros de material producidos por la máquina ajustada y observa cualquier problema imprevisto, así como los beneficios adicionales que puedan derivarse de los nuevos ajustes.
Verificar
En la fase Verificar se analizan en detalle los resultados de la fase Hacer. Aquí se comparan los datos recopilados durante la ejecución del ensayo con los resultados esperados y los valores de referencia para evaluar el éxito de la intervención. La fase Verificar es fundamental para comprender la eficacia del plan y el impacto de los cambios realizados.
Es una oportunidad para la reflexión y el estudio en la que las empresas pueden identificar discrepancias, recopilar información y determinar si se han realizado las mejoras previstas. Si se consideran necesarios más cambios, el ciclo suele volver a la fase de planificación.
En nuestro ejemplo, el equipo analiza a continuación los datos recogidos en el proyecto piloto. Descubren que los nuevos ajustes de la máquina han reducido el despilfarro de material en un 15% –ligeramente por debajo del objetivo previsto, pero aun así una mejora significativa. Sin embargo, también ha surgido un beneficio inesperado: la operación de corte en la máquina probada es ahora un 10% más rápida. Al revisar estos resultados, el equipo descubre el motivo por el que no se ha alcanzado totalmente el objetivo y determina que no es posible sacar más partido de la mejora.
Actuar
Por último, la fase Actuar consiste en tomar decisiones fundamentadas basadas en la información obtenida en la fase Verificar. Si los cambios de prueba resultan satisfactorios, Actuar se centra en estandarizar las mejoras e implementarlas a mayor escala en toda la organización.
Si los resultados no son los esperados, la fase Actuar sirve como bucle de retroalimentación en el que el plan inicial se revisa y perfecciona sobre la base de las lecciones aprendidas, preparando al equipo para entrar de nuevo en el ciclo PDCA. La fase Actuar garantiza que las mejoras se consoliden en las operaciones de la empresa y que se perpetúe el ciclo de mejora continua.
En nuestro ejemplo, el fabricante decide adoptar los nuevos ajustes de la máquina en todas las máquinas de corte, dado el éxito de la reducción de despilfarros y el aumento de la productividad. Actualizan los materiales de capacitación para los operarios de las máquinas con el fin de incluir los nuevos ajustes y procedimientos, y programan seguimientos periódicos para supervisar la aplicación generalizada. También deciden revisar el ciclo PDCA trimestralmente para identificar nuevas mejoras.
Buenas prácticas PDCA para fabricantes
A continuación, demos un vistazo a cuatro buenas prácticas PDCA para fabricantes y distribuidores.
Fomentar los equipos interfuncionales
Las diferentes perspectivas pueden dar lugar a soluciones más innovadoras y aumentar la probabilidad de detectar posibles problemas o mejoras. Involucre en el ciclo PDCA a diversos departamentos, como ingeniería, producción, existencias, control de calidad, etc. Este enfoque colaborativo enriquece aún más el proceso de planificación y resolución de problemas y facilita su aceptación e implementación en toda la empresa.
Definir claramente los objetivos y los parámetros
Unos objetivos claros y comprensibles y unas métricas concretas son esenciales para medir el impacto de sus acciones en el ciclo PDCA y garantizar la alineación con sus objetivos empresariales generales.
Establezca objetivos específicos, medibles, alcanzables, pertinentes y sujetos a plazos, es decir, objetivos SMART, al principio de la fase Planificar. Determine qué indicadores clave de rendimiento (KPI) le ayudarán a medir el éxito de la forma más eficaz, y realice un seguimiento de los mismos a lo largo del ciclo PDCA para evaluar el progreso y la eficacia de los cambios implementados. También es imprescindible documentar los resultados de forma coherente.
Involucrar y capacitar a los empleados
Involucrar y capacitar a los miembros del equipo a todos los niveles en el proceso PDCA les capacita para contribuir a la eficacia del ciclo de mejora. Cuando los empleados comprenden cómo sus acciones pueden influir en el rendimiento de la empresa, es más probable que asuman como propias sus funciones y participen activamente en la resolución de problemas y la optimización de procesos.
Consejos para involucrar a los empleados:
- Desarrolle programas de capacitación que describan los fundamentos del ciclo PDCA y su importancia para los objetivos de la empresa.
- Utilice ejemplos reales de sus operaciones para ilustrar cómo funciona cada fase del ciclo junto con su impacto.
- Involucre a los empleados en cada ciclo PDCA asignándoles funciones específicas relacionadas con sus conocimientos e intereses.
Revise y adapte periódicamente el ciclo
Las condiciones del mercado, la tecnología y los procesos empresariales internos evolucionan constantemente. Por lo tanto, el propio ciclo PDCA debe someterse a revisiones y adaptaciones periódicas para seguir siendo eficaz.
Programe revisiones periódicas de sus procesos PDCA para examinar su eficacia y relevancia en el entorno empresarial actual. Actualice sus enfoques y estrategias en respuesta a los nuevos conocimientos y cambios del sector para asegurarse de que el modelo PDCA sigue impulsando mejoras significativas.
¿Cómo puede ayudar el software de fabricación a introducir mejoras continuas?
El software de fabricación puede desempeñar un papel fundamental en el fomento de un entorno de mejora continua dentro de las operaciones industriales. Al integrar una solución de software unificada, los fabricantes pueden agilizar sus procesos, mejorar la comunicación entre departamentos, reducir errores y mantener estándares de calidad más consistentes. Veamos algunas de las formas en que el software de fabricación puede apoyar eficazmente sus esfuerzos de mejora continua.
Recopilación y análisis de datos mejorados
El software de fabricación automatiza la recopilación y el análisis de datos críticos procedentes de diversos puntos del proceso de producción. De este modo, se obtienen cuadros de mando de las métricas de rendimiento e información en tiempo real sobre los cuellos de botella en la producción y las necesidades de mantenimiento. Con acceso a datos precisos y oportunos, las empresas pueden identificar áreas de mejora, predecir posibles problemas antes de que ocurran y tomar mejores decisiones con mayor rapidez.
Trazabilidad y conformidad
El software de fabricación mejora significativamente la trazabilidad y ayuda a cumplir los estrictos requisitos normativos. Al mantener registros detallados de todo el proceso de fabricación, desde las materias primas hasta los productos terminados, los sistemas MRP garantizan el seguimiento de cada componente a lo largo de todas las fases de producción. Esta trazabilidad es crucial para identificar el origen de los defectos, controlar los efectos de los cambios en el proceso y garantizar que todos los productos cumplen las normas de calidad.
Estandarización de los procesos
Una de las principales ventajas de un software de fabricación bien implementado es su capacidad para estandarizar las operaciones en toda la planta de producción. La estandarización es crucial para eliminar la variabilidad en la calidad del producto y la eficiencia de la producción. Los procesos coherentes facilitan la detección de variaciones y su corrección, lo que se traduce en una producción de mayor calidad y fiabilidad.
Facilita la comunicación
La comunicación eficaz es fundamental en los marcos de mejora continua. El software de fabricación mejora la comunicación y la gestión de recursos humanos proporcionando una plataforma unificada para el intercambio de información entre diferentes departamentos. Las actualizaciones, los cambios y los comentarios pueden difundirse de forma rápida y clara, garantizando que todos los miembros del equipo estén en la misma página y puedan responder rápidamente a la nueva información o a los ajustes en el ciclo de producción.
Apoyo al mantenimiento proactivo
El software de fabricación incluye herramientas para supervisar el rendimiento de la maquinaria y los equipos, lo que ayuda a aplicar estrategias de mantenimiento proactivas. Al anticiparse a las necesidades de mantenimiento antes de que provoquen tiempos de inactividad, los fabricantes pueden mantener sus operaciones funcionando sin problemas y evitar interrupciones que podrían afectar a la productividad y la calidad. Este enfoque proactivo forma parte integral de las fases “Verificar” y “Actuar” del ciclo PDCA, en las que se realizan ajustes continuos para mantener un rendimiento óptimo.
Principales aspectos a tener en cuenta
- El PDCA (Planificar-Hacer-Verificar-Actuar) es un enfoque cíclico de cuatro pasos para la mejora continua que ayuda a las organizaciones de fabricación a abordar y resolver sistemáticamente los problemas para mejorar la productividad y la calidad de los productos.
- El ciclo Planificar-Hacer-Verificar-Actuar es importante para mantener la competitividad en la industria de la fabricación, ya que fomenta la adaptabilidad y la mejora continua de los procesos.
- El ciclo PDCA consiste en Planificar para identificar y evaluar los problemas, Hacer ensayos a pequeña escala de las posibles soluciones, Verificar los resultados frente a los previstos y Actuar para aplicar ampliamente los cambios que hayan tenido éxito o perfeccionar el plan y volver a probarlo.
- Las mejores prácticas de PDCA para los fabricantes incluyen empezar con proyectos pequeños y manejables, definir claramente los objetivos y las métricas, involucrar y capacitar a los empleados de todos los niveles, y revisar y adaptar periódicamente el ciclo para adaptarlo a la evolución de las condiciones del mercado y los cambios operativos internos.
Preguntas frecuentes
Los pequeños fabricantes pueden evaluar el impacto financiero del ciclo PDCA mediante el seguimiento de métricas específicas antes y después de realizar los cambios. Los indicadores clave de rendimiento, como los costos de producción, la reducción de despilfarros, el tiempo de comercialización y los defectos de calidad del producto, pueden analizarse para determinar el ahorro de costos y el aumento de los ingresos. Además, realizar análisis del antes y el después en proyectos piloto puede proporcionar una imagen clara de los beneficios financieros.
Entre los retos habituales de los pequeños fabricantes se encuentran la escasez de recursos para realizar pruebas exhaustivas y la resistencia a cambiar los procesos establecidos. Para superarlos, los fabricantes pueden empezar con proyectos piloto a pequeña escala que demuestren la eficacia del PDCA sin necesidad de grandes recursos iniciales. Involucrar a los empleados mediante la capacitación y una comunicación clara sobre las ventajas del PDCA también puede ayudar a mitigar la resistencia al cambio.
El ciclo PDCA puede integrarse con los sistemas ERP existentes u otras soluciones tecnológicas utilizadas por los pequeños fabricantes. La mayoría de los softwares de fabricación modernos admiten la recopilación y el análisis de datos, que son cruciales para la fase Verificar del PDCA. Los fabricantes pueden aprovechar estas herramientas para automatizar la recopilación y el análisis de datos, alinear las actividades PDCA con otros procesos operativos y garantizar que las mejoras se basan en datos precisos y oportunos.
También le puede interesar: ¿Qué es el Poka-yoke y cómo utilizarlo en la fabricación?