¿Qué es un ciclo de producción y cómo optimizarlo?
El ciclo de producción es el motor de toda empresa de fabricación. Cada etapa de este ciclo es crucial para mantener la eficiencia. Pero, ¿cómo gestionar eficazmente todas estas etapas? En este artículo explicaremos qué es un ciclo de producción, exploraremos sus componentes clave y compartiremos estrategias para mejorar la eficiencia.
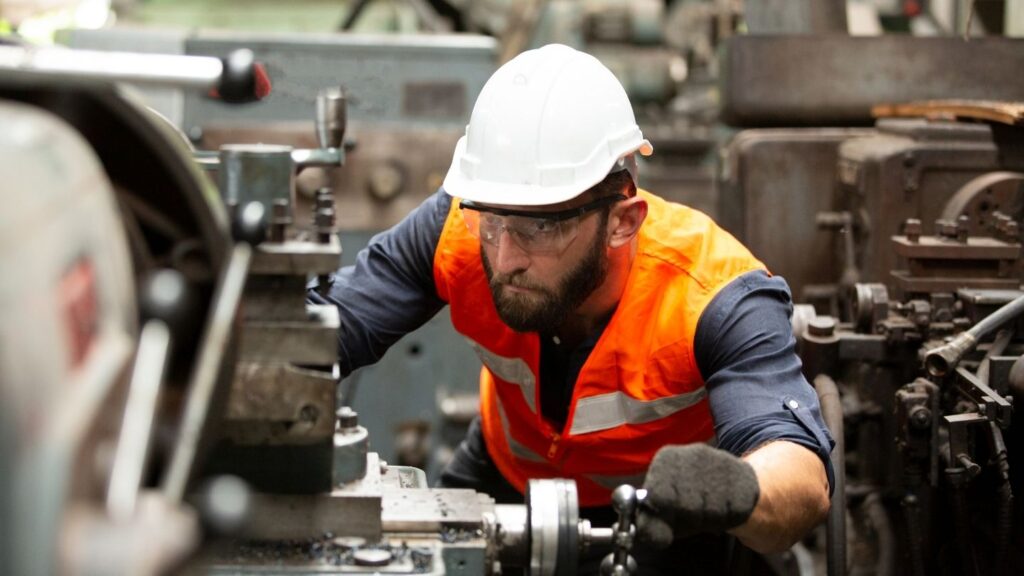
¿Qué es un ciclo de producción?
Un ciclo de producción, en su forma más simple, es el proceso de convertir materias primas en productos terminados. Comienza cuando las materias primas entran en producción y termina cuando el producto final está terminado y listo para enviar o vender. En esta definición, sólo nos centramos en el proceso de producción en sí. Dejamos fuera aspectos como el diseño del producto, el marketing o cualquier otra cosa que ocurra después de la producción.
El ciclo de producción es la parte de la operación que afecta directamente a la eficiencia con la que se utilizan los recursos (materiales, mano de obra y máquinas), a la rapidez con la que se completan los productos y a la consecución de los objetivos de producción de una empresa. Dado que todo en la fabricación gira en torno a la transformación de materias primas en productos, el ciclo de producción se sitúa en el centro de estas operaciones.
¿En qué consiste exactamente el ciclo de producción? Podemos dividirlo en cuatro etapas:
1. Preparación del material
El proceso de producción comienza con la preparación de los materiales o componentes para la producción. En esta etapa se preparan las materias primas para la fabricación, ya sean de origen externo o de producción interna. Esto puede implicar pasos básicos como la limpieza, el corte o la organización. El objetivo es garantizar que todo esté listo para la producción.
2. Procesamiento
Una vez preparados, los materiales pasan a la fase de procesamiento. Aquí es donde los materiales se transforman, ensamblan o moldean en componentes del producto final. Dependiendo del producto que se fabrique, esto puede ir desde la mecanización hasta la mezcla, pasando por la costura o el simple ensamblaje.
3. Control de calidad e inspección
Tras el procesamiento, los inspectores revisan el producto para confirmar que cumple las normas exigidas. Este paso es crucial para detectar los defectos de fabricación antes de finalizar el producto. Los inspectores pueden realizar controles en distintas fases de la producción, pero son especialmente necesarios hacia el final del ciclo de producción para confirmar que el producto está listo para la siguiente fase.
4. Finalización del producto final
El ciclo de producción termina cuando el producto final está terminado y ha superado todos los controles de calidad. En este punto, los productos están listos para su envasado, envío o almacenamiento, dependiendo de lo que venga después en el proceso empresarial. Pero tal y como la hemos definido, esta etapa marca el final del ciclo de producción propiamente dicho.
En estas cuatro etapas vemos cómo el ciclo de producción influye en la transformación de las materias primas en productos terminados. Cada etapa requiere una gestión cuidadosa para minimizar los retrasos, reducir los residuos y cumplir los objetivos de producción.
¿Qué procesos apoyan el ciclo de producción?
Dado que el ciclo de producción es el eje central de la fabricación, vamos a desglosar los procesos clave que mantienen la producción en marcha.
Adquisición y disponibilidad de materias primas
Dado que el ciclo de producción comienza con las materias primas, tenerlas a mano o fácilmente accesibles es esencial para que todo siga avanzando. Tanto si proceden de proveedores externos como si se producen internamente, su prioridad es asegurarse de que los materiales y componentes que necesita estén siempre listos cuando empiece la producción.
Si estos materiales no están disponibles cuando los necesita, todo se retrasa. Por eso debe garantizar una gestión adecuada de los materiales trabajando con proveedores fiables y controlando en todo momento la cantidad de existencias que tiene a mano. Es importante que disponga de suficientes materiales para satisfacer las demandas de producción sin tener un exceso de existencias y desperdiciar espacio y dinero. Mantener un equilibrio entre lo que se necesita y lo que hay disponible es el secreto de un ciclo de producción fluido.
Programación laboral y gestión de recursos humanos
La mano de obra es otra parte importante del ciclo de producción. No se trata sólo de tener suficientes trabajadores. También se trata de asegurarse de que las personas adecuadas estén disponibles en el momento adecuado. Si los trabajadores no se programan correctamente, la producción puede retrasarse o puede acabar pagando demasiado por la mano de obra adicional. Una buena programación mantiene el ritmo de producción y ayuda a controlar los costos laborales.
Otra razón para gestionar eficazmente el tiempo de sus empleados es evitar que trabajen en exceso o se agoten. Cuando los trabajadores están agotados, son menos eficientes y más propensos a cometer errores. Esto, por supuesto, puede ralentizar la producción y perjudicar la calidad general. Con el tiempo, también puede provocar una mayor rotación de los empleados, lo que dejará a la empresa corta de personal y con la necesidad de gastar más en la contratación y capacitación de los reemplazos.
Mantenimiento, disponibilidad y capacidad de las máquinas
Las máquinas son esenciales para la producción, y un mantenimiento regular mejora la eficiencia al tiempo que evita fallos que provocan retrasos y mayores costos. Un plan de mantenimiento proactivo es clave para evitar problemas inesperados.
La disponibilidad de las máquinas también debe programarse cuidadosamente para evitar el uso excesivo o los tiempos muertos. Escalonar el uso de las máquinas y disponer de opciones de reserva puede ayudar a evitar cuellos de botella en la producción. Además, conocer la capacidad de los equipos garantiza que se ajustan a las necesidades de producción sin sobrecargar ni infrautilizar los recursos, lo que mantiene el ciclo de producción en perfecto funcionamiento.
¿Cómo planificar eficazmente la producción?
Una planificación eficaz de la producción es clave para mantener un funcionamiento fluido y satisfacer la demanda de los clientes. Un plan bien organizado ayuda a evitar retrasos, reducir el despilfarro y aprovechar al máximo los recursos disponibles. A continuación le mostramos cómo planificar eficazmente la producción:
Prevea su demanda y capacidad
El primer paso en la planificación de la producción es conocer su capacidad de producción. Esto significa saber cuánto se puede producir en un plazo determinado, en función de la disponibilidad de máquinas, mano de obra y materiales. Comparando las previsiones de demanda con la capacidad, puede ajustar los planes de producción para alcanzar objetivos realistas.
Cree programas de producción
Una vez que la demanda y la capacidad están claras, el siguiente paso es crear una programación de la producción. Esto implica decidir cuándo y cómo tendrá lugar la producción. La programación debe tener en cuenta todas las fases de la producción, desde la preparación de la materia prima hasta el producto final, así como los periodos de mantenimiento o de inactividad de las máquinas.
Un programa de producción bien estructurado ayuda a agilizar la producción y evita los cuellos de botella. Pero tenga en cuenta que la programación de la producción es también un documento vivo. Puede y debe ajustarse a medida que cambien las condiciones.
Coordine los materiales y la mano de obra
Para que la producción fluya sin problemas, los materiales y la mano de obra deben estar sincronizados. Coordine las compras de materias primas con los tiempos de producción para que los materiales lleguen a tiempo y evitar retrasos en la producción. Su programación también debe ajustarse a las necesidades de producción, con el número adecuado de trabajadores asignados a las tareas correctas en los momentos adecuados.
Para lograrlo, muchos fabricantes confían en herramientas como el software ERP de fabricación, que ayuda a automatizar y optimizar la coordinación de materiales, mano de obra y máquinas.
Siguiendo estos pasos —previsión de la demanda y la capacidad, creación de programas de producción alineados y coordinación eficaz de los recursos— las empresas pueden planificar la producción con eficacia y garantizar que las operaciones se desarrollen sin contratiempos.
¿Cómo controlar y mejorar la eficiencia de la producción?
Para controlar y mejorar la eficiencia de la producción, empiece por hacer un seguimiento de los indicadores clave de rendimiento (KPI) esenciales, en concreto de aquellos que ponen de relieve áreas de mejora.
1. Defina sus KPI. Estos son los principales KPI en los que debe fijarse en su ciclo de producción:
- Eficiencia general de los equipos (OEE). Realiza un seguimiento de la utilización de la máquina accediendo a la disponibilidad, el rendimiento y la calidad.
- Tiempo de ciclo. Mide el tiempo que se tarda en completar una sola unidad o un lote en una estación de trabajo específica, por ejemplo, el torneado de un componente o la mezcla de un lote de masa.
- Rendimiento. Muestra la calidad indicando la proporción de unidades que cumplen las normas.
- Costo unitario. Calcula el costo por unidad para identificar oportunidades de ahorro.
- Utilización de la capacidad. Evalúa la eficacia en el uso de los recursos. Una mayor utilización de la capacidad indica un uso más eficiente de los recursos.
2. Implemente la supervisión en tiempo real. Utilice herramientas de datos en tiempo real, como los sistemas ERP de fabricación, para supervisar el rendimiento y el tiempo de inactividad de las máquinas.
3. Lleve a cabo un análisis de las causas raíz. Analice los cuellos de botella y las causas de los tiempos de inactividad para abordar las ineficiencias básicas que puedan estar ralentizando la producción. El análisis periódico de estos factores ayuda a determinar dónde se necesitan mejoras.
4. Optimice la programación y la planificación. Alinee la producción con las previsiones de demanda para reducir los tiempos muertos, la sobreproducción y el despilfarro de recursos.
5. Promueva la mejora continua. Adopte métodos como Kaizen, Lean o Six Sigma. Estos enfoques ayudan a reducir el despilfarro introduciendo pequeñas mejoras continuas para optimizar sus procesos.
Siguiendo estos pasos y realizando un seguimiento de los KPI, podrá mejorar continuamente la eficiencia de la producción.
Optimización del ciclo de producción con ERP de fabricación
El software MRP o ERP de fabricación puede automatizar varios aspectos del proceso de producción. Como resultado, este software puede ayudarle a gestionar sus recursos de forma más eficiente y a reducir el tiempo de inactividad. A continuación le mostramos cómo este software puede mejorar su ciclo de producción:
Estandarización de procesos
La implementación del software MRP le ayuda a estandarizar y documentar sus procesos. Esto le permite encontrar la forma óptima de hacer las cosas y establecerla como predeterminada. Disponer de una fórmula concreta para procesar los artículos también prepara el terreno para el análisis del rendimiento, ya que le permite descubrir las anomalías con respecto a la norma.
Medición de la eficacia de la producción
El software ERP de fabricación recopila datos de todas sus operaciones y los utiliza para generar estadísticas e información sobre la eficiencia de sus procesos. Esto le permite detectar ineficiencias y otros problemas y encontrar la forma de solucionarlos, garantizando la mejora continua de sus operaciones.
Control y ajustes en tiempo real
El software MRP le ayuda a seguir todo el proceso de producción en tiempo real. De este modo, puede realizar ajustes inmediatamente. Por ejemplo, si una máquina se avería o los materiales se retrasan, puede utilizar sus sistemas MRP para reprogramar rápidamente las tareas según sea necesario.
Asignación eficaz de recursos
El software MRP le ayuda a asignar la mano de obra, los materiales y las máquinas de forma más eficaz. Al automatizar la programación y la planificación, puede alinear los recursos para que su equipo no esté infrautilizado y sus empleados no trabajen en exceso.
Mantenimiento preventivo para minimizar los tiempos de inactividad
Algunos sistemas ERP ofrecen la posibilidad de aplicar el mantenimiento preventivo. Al establecer intervalos de mantenimiento en función de las piezas procesadas o las horas trabajadas, puede realizar un mantenimiento proactivo de la maquinaria y reducir el riesgo de fallos inesperados.
Con el software MRP, puede reducir significativamente las tareas manuales, mejorar la precisión y mantener la producción sin problemas.
Principales aspectos a tener en cuenta
- Un ciclo de producción es el proceso de transformación de materias primas en productos terminados, desglosado en cuatro etapas principales: preparación del material, procesamiento, control de calidad y finalización del producto.
- Los principales procesos que sustentan un ciclo de producción saludable son la gestión de materiales, la planificación de capacidades y la gestión del mantenimiento.
- La supervisión de indicadores clave de rendimiento (KPI), como la eficiencia global de los equipos y el tiempo de ciclo, junto con el análisis de datos en tiempo real, ayuda a identificar y resolver las ineficiencias para mejorar continuamente la producción.
- El software ERP de fabricación aumenta la eficacia mediante la estandarización de procesos, la supervisión en tiempo real, la optimización de recursos y el mantenimiento preventivo, reduciendo las tareas manuales y los tiempos de inactividad.
Preguntas frecuentes
Los KPI más importantes dependen de sus objetivos de producción específicos. Comience con métricas universales como la eficiencia general de los equipos (OEE) para el rendimiento de la maquinaria, el tiempo de ciclo para la velocidad y el rendimiento para la calidad, y luego amplíe a otras como el costo unitario o la utilización de la capacidad en función de sus necesidades operativas específicas.
El software ERP puede realizar un seguimiento del uso de las máquinas y programar el mantenimiento en función de parámetros como las horas trabajadas o las unidades producidas. Este enfoque proactivo minimiza los fallos inesperados y garantiza que las máquinas funcionen con una eficiencia óptima, reduciendo el tiempo de inactividad y los costos de reparación.
Si la demanda supera la capacidad, considere estrategias como optimizar los horarios, añadir turnos o subcontratar temporalmente partes de la producción. Las soluciones a largo plazo pueden incluir la inversión en recursos adicionales, como maquinaria o mano de obra, para aumentar la producción de forma sostenible.
También le puede interesar: Programación progresiva vs. programación regresiva en la planificación de la producción