ERP and MRP Differences: Why MRP is the Smart Choice for Growing Businesses
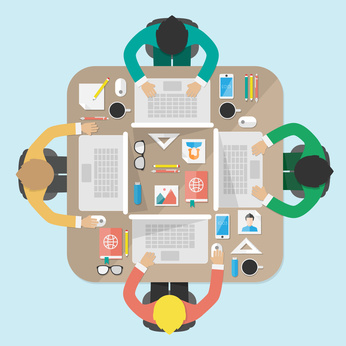
Your growing manufacturing company is preparing to make the leap into manufacturing software. With just a minimal amount of research, you’ve probably already discovered the two primary types of software you’ll need to explore so you can make an informed decision.
They are manufacturing resource planning (MRP) and enterprise resource planning (ERP).
At first glance, you might come away thinking that ERP is your best choice. After all, from all outward appearances, ERP would seem to be a more comprehensive system. It covers more of your departmental needs with its powerful financial module. Doesn’t it make sense to have everything that ERP has to offer?
Well, you’ve gained a lot of experience managing your business over the years, and one thing you certainly have learned is that appearances can be deceiving at times…and this is one of those times.
Let’s take a closer look at these two systems, including their histories, to uncover the ERP and MRP differences. Your growing business deserves not only the highest quality manufacturing software but also the one that best optimizes your company’s processes.
What is MRP?
MRP began as a material requirements planning system. It evolved through the 1940s and 50s and used mainframe computers to digest information from a bill of materials (read about bill of materials software) and provide purchasing plans and a master production schedule for producing a part or component. No other business processes were incorporated into the original MRP software.
But by the 1980s, MRP–now known as manufacturing resources planning–had also combined engineering, marketing, finance, accounting, and human resources into a complete planning process with the help of today’s computer technology. Many called this advanced system MRP II in its nascent stage, but today it is understood that MRP stands for the software that integrates all of these aspects.
MRP begins with a schedule for a finished product. The system then converts that information into schedules of requirements for the parts, subassemblies, and materials needed to produce the final product within the established schedule. It also takes into consideration the shop’s workstation schedule and allocation of labor throughout the plant.
The MRP system of 2018 bears little resemblance to its predecessors. It is a completely accessible production tool that allows input from all departments and supplies real-time information to them.
Learn more about MRP scheduling functionality
What is ERP?
In the 1990s, new systems were introduced that broadened the capabilities of MRP software. Like MRP systems, ERPs managed inventory, orders, and production scheduling. But this new system was advertised not as a replacement for MRP but as one that offered more “breadth” than the traditional manufacturing software.
ERP would handle the whole enterprise (E) while dealing with resources (R) and planning (P). Modules in an ERP system include accounting/finance, sales and marketing, human capital management (HCM), customer relationship management (manufacturing CRM), and human resources (HR), in addition to some of the same modules that are present in MRP.
It sounds as though it has all the features of MRP and more.
But when you look at the differences between the two systems, that clear choice quickly begins to get cloudy!
Which system, ERP or MRP, makes sense for your small business?
The answer to that question will depend on what you believe should be the focus of your business. If you’re a growing business, your primary concern will be centered on continuously optimizing your processes. So, a software system that manages your manufacturing processes – inventory, production, and scheduling – is what you need most.
With that in mind, an MRP system is probably the best fit for your company. It makes little sense to add those extra modules into the mix, pay the higher price of an ERP, and end up with a system that focuses on the financial and recordkeeping aspects of your business instead of production. Understand, too, that the complexity of an ERP system requires that your company have the IT resources to support it.
ERPs are for enterprises where the market has already been adopted, and growing is no longer the most critical element. Unless you are part of a large organization and have the financial wherewithal to install an ERP with a powerful manufacturing module, your best bet is to choose an MRP system. Most ERP systems marketed for smaller, growing businesses are very limited in the areas of production planning and control. And that, of course, is what you need most.
Remember the specific information that is crucial to your growing company’s success:
- Workstation capacity
- Workforce planning
- Inventory management
- Shop floor data collection
- Material traceability
- Procurement processes
You need to have a clear, up-to-the-minute picture of where you stand in inventory, production, sales, and procurement. These areas are dependent on one another and cannot be disconnected from each other. And they are all present in a quality MRP system.
Let us help you make the most of your manufacturing efforts
MRPeasy has the products to bring your employees, equipment, and data together in one place. Let our experts show you how to streamline your manufacturing resource planning with one of our easy-to-use and affordable MPR systems. It is the perfect choice for your growing enterprise!