Top 10 Mistakes Small Manufacturers Make with ERP Software
Manufacturing ERP software has the potential to transform a company, but beware of these common mistakes small manufacturers make when implementing.
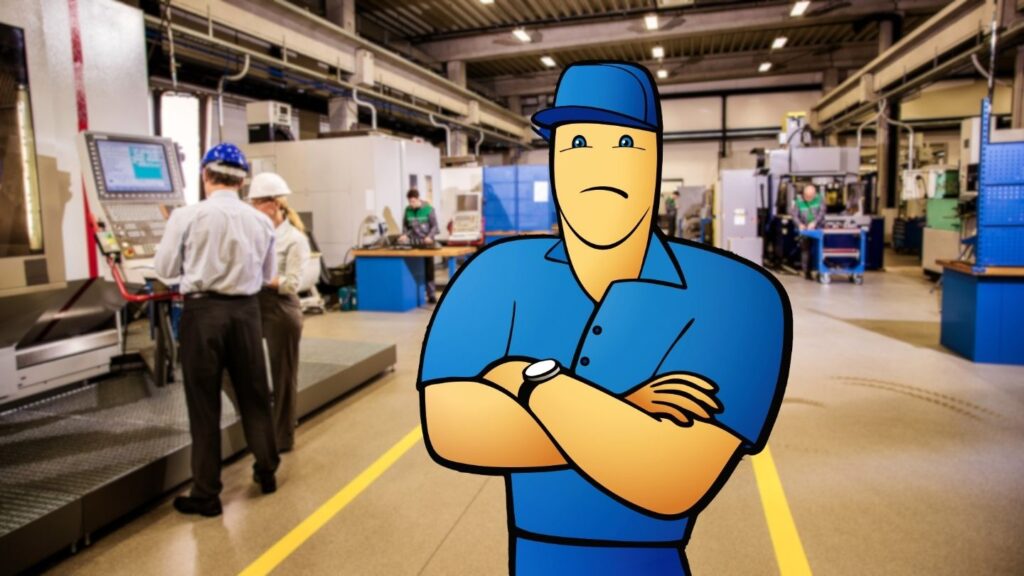
You can also listen to this article:
1. Not considering all their requirements
Knowing your full requirements is crucial in the ERP selection process. However basic this sounds, manufacturing companies often overlook this, either implementing software according to the requirements of a single department or to alleviate their most immediate pains.
If a production manager is tasked with finding appropriate software, they risk focusing on the requirements of the shop floor and neglecting those of other departments such as purchasing, inventory management, or sales. Occasionally, a new manager even brings in a system they worked with in a previous company without evaluating its fit for their current one. The net result is that the chosen system fails to deliver full value for the business.
The solution is to collaborate with stakeholders across the business to create a more complete requirements list.
2. Choosing software only for the short term
While considering your whole operation’s current requirements is difficult enough, you also have to take your future plans into account when choosing a solution. Manufacturing ERP software should be a product with a long lifecycle, which means that your company should be able to grow with it for at least 10-15 years. And while a rudimentary system might fix some issues in the short term, you might quickly exhaust its capability to accommodate your increasingly complex needs.
During my career as a software consultant, I have seen companies that have outgrown their ERP system in less than two years, forcing them to restart the whole implementation process. It is essentially money down the drain.
That is why it is necessary to also consider your future requirements and select software that:
– Is capable of scaling with the business;
– Integrates with various 3rd party apps for added functionality;
– Takes customers’ development proposals into consideration.
3. Developing custom software
Although many small business managers claim to have unique requirements, the issues small manufacturers face and the processes they use are remarkably similar. Regardless, many small manufacturers go down the path of custom software development. While this usually incurs tens or hundreds of thousands of dollars in additional expenses, it also comes with some extra caveats.
Firstly, software developers most often lack experience in manufacturing, which prevents them from understanding the intimate details of managing a production operation and, therefore, creating a robust solution for it.
Secondly, updating the software to eliminate bugs or develop extra functionality will cost extra and depend on the whims of the software developer. It is not uncommon for companies to lose support for the custom-developed system in a few years.
4. Looking for a quick fix
Implementing software that supports functions throughout your operation is not supposed to be easy. While solutions exist that prioritize user-friendliness, even these systems take real effort to set up, even when hiring a consultant to do most of the work.
However, many small manufacturers with little to no experience with ERP software expect a magic wand that would fix all their issues in one fell swoop. They are not willing to dedicate the appropriate resources to the implementation, or they rush the implementation without proper testing or data validation. In addition, often, the priority of the “actual work” takes over, and the implementation momentum is lost. The result is a system that doesn’t work, a return to former manual methods, and money going down the drain.
Instead, manufacturers should manage their expectations and realize that ERP software is not a magic wand but a structure that enables the company to actively fix its own issues. In most cases, implementation should be a gradual process, starting with inventory management and moving along when the previous set of functionalities has been properly set up. Setting realistic short-term KPIs is a good way to demonstrate the return on investment during the implementation process.
5. Using deficient data
“Garbage in, garbage out” is the golden rule of ERP, meaning that low-quality data inevitably leads to low-quality outcomes, and high-quality data is vital for high-quality outcomes. During implementation, however, manufacturers often think that migrating all of the data from their previous system to the new one is sufficient. This might start the whole implementation off on a faulty foundation as the legacy data might be broken, outdated, in the wrong format, or simply not reflective of the new way of work introduced by the ERP implementation.
Before migration, the relevance and quality of the data should be carefully reviewed. It is important to note that starting from scratch is always better than building your system on bad data.
6. Not assigning an implementation lead
Having a clear and appropriate project sponsor is vital for driving the project forward and overcoming obstacles. The sponsor should be someone credible, respected across the business, and with a deep understanding of the company’s operations. Unfortunately, it’s not uncommon for companies to assign this critical role to someone without the necessary authority or understanding of the business, leading to poor implementation outcomes.
For example, appointing a Health and Safety Manager with little knowledge of manufacturing operations as the project lead can lead to a lack of respect from the team and poor buy-in from the workforce. This can cause resistance to the system from day one, jeopardizing the entire implementation.
To avoid this, ensure that the project sponsor is not only involved with the system on a day-to-day basis but also has the authority to drive the project forward, unblock obstacles, and ensure accountability across the project team.
7. Lack of buy-in from stakeholders
Successful ERP implementation requires the engagement and buy-in of key stakeholders from across the organization. Unfortunately, this is often overlooked or only considered as an afterthought. Without the support of these functional leaders, the implementation is likely to face significant hurdles, including resistance to change and lack of proper use of the system.
It’s crucial to identify all key stakeholders early in the project and develop a clear plan to keep them engaged and excited about the new system. Regular communication, updates on progress, and involving them in key decisions can help maintain their interest and support. Remember, a disengaged stakeholder can derail the project, so their involvement is critical from start to finish.
8. Lack of buy-in from the workforce
Change can be unsettling, especially when it involves new technology and processes that alter how people do their jobs. Without proper change management, this natural resistance to change can lead to significant pushback from the workforce, undermining the implementation process.
Managing change effectively through clear, consistent, and two-way communication is essential. Addressing fears head-on—whether it’s fear of technology replacing jobs or concerns about how daily tasks will change—can help to alleviate resistance. Explaining the benefits of the new system and how it will make jobs easier or more efficient can help to win over skeptical employees. Moreover, involving them in the process and providing ample support can turn potential detractors into advocates.
9. Insufficient employee training
Even the best ERP system will fail if employees are not adequately trained. One of the biggest mistakes small manufacturers make is underestimating the importance of thorough and ongoing training. The system will only be as effective as the people who use it, and without proper training, employees may struggle to adapt, leading to errors and inefficiencies.
Training should not only cover how to use the system but also how it will change day-to-day processes for each department or team. By clearly communicating these changes and providing hands-on training, employees can gain the confidence they need to use the system effectively, ensuring a smoother transition and better overall results.
10. Not integrating with other systems
ERP systems are designed to be the central hub for a company’s operations, but they don’t operate in a vacuum. Failing to integrate the ERP with other existing business applications—such as accounting software—can lead to data duplication, errors, and inefficiencies. This not only adds unnecessary complexity but can also result in missed opportunities for automation and data-driven decision-making.
Before implementing the ERP, it’s crucial to identify all existing systems that need to be integrated and plan accordingly. This ensures that data flows seamlessly between systems, reducing the risk of errors and making the entire operation more efficient.
You may also like: Top 3 Common Warehouse Management Mistakes