What Is Distributed Manufacturing?
In distributed manufacturing, production facilities are scattered throughout an extended geographical area, each one serving their local market, with their work coordinated with the help of cloud-based software. Distributed manufacturing is gradually gaining ground thanks to providing benefits such as shorter lead times and lower distribution costs.
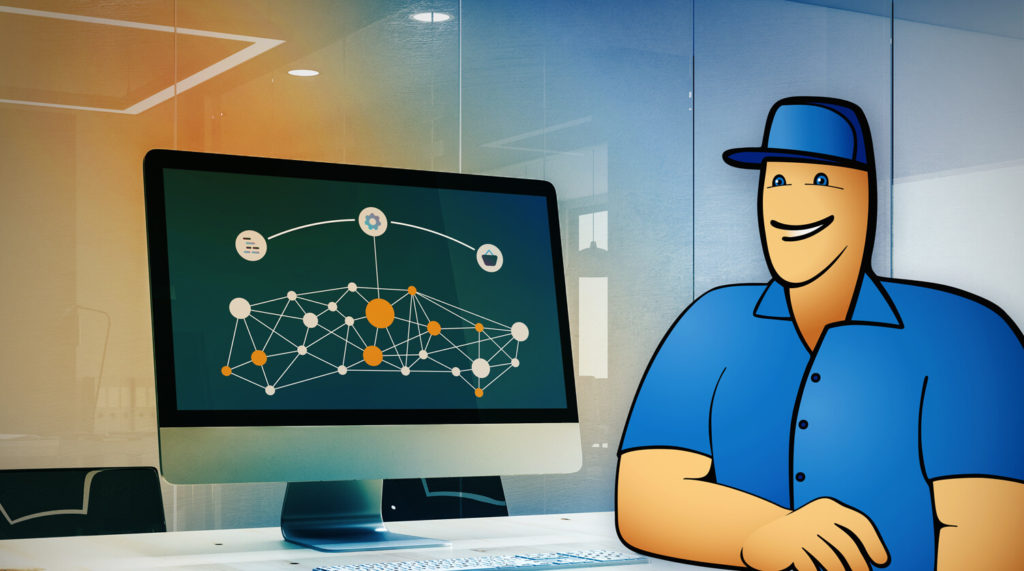
You can also listen to this article:
What is Distributed Manufacturing?
Distributed manufacturing is a business model in which goods are produced in many facilities over a large area, instead of all at one central location. While big conglomerates have benefitted from having manufacturing plants in different parts of the world for decades, distributed manufacturing refers more to single smaller companies or cooperative networks that spread their production facilities over a region. This way they can produce, source, or distribute locally while having a market presence on a regional scale and keeping shipping times and costs lower.
These dispersed facilities often produce customized products for the local market while being managed centrally from elsewhere, often with the help of cloud-based software. Under the motto “design globally, produce locally”, designs for products are shared, however, products are manufactured and distributed according to local demand.
For example, in the traditional approach, a company would find or create a large manufacturing plant anywhere in the world to produce their goods with the lowest cost possible while upholding the necessary quality standard. Goods would be mass-produced and shipped from the factory to the target market, which could be very far away due to offshoring.
In distributed manufacturing, however, a company could find micro-producers that are local to the target markets, provide them with product designs and customer orders, sometimes even managing their inventory and purchases. Goods would be produced in smaller quantities and promptly shipped to customers located in the same area. Although production is likely to be more expensive, this disadvantage would be offset by much shorter lead times, lower distribution costs, and often higher quality products. This effect is becoming amplified by the flexibility and increasing efficiency of modern small manufacturing solutions and technologies.
Benefits of distributed manufacturing
The distributed manufacturing business model has various advantages that are rapidly bringing the approach to the attention of the mainstream. These include:
- Reduction in distribution costs. One of the central tenets of distributed manufacturing is to produce close to the end consumers. This cuts out lengthy shipping processes and saves a lot of money on distribution and logistics.
- Shorter lead times. As deliveries are made locally, lead times are cut by a large margin. Ideally, materials are also sourced more locally, shortening the time to market even further.
- Less capital investment is needed. A distributed manufacturing company usually requires much less capital investment before they can kick start their business. A credible strategy is to seek out and employ local micro-producers that already have their own equipment and manufacturing facilities (e.g. a workshop).
- More flexibility in capacity. Utilizing the labor of independent contractors who are only working when there is demand for the products in their area gives companies a chance to increase or reduce production capacity as seen fit. The business can be contracted or expanded according to demand and the company can remain agile in the face of fluctuations.
- Better capacity utilization. Small manufacturing shops can benefit from the distributed manufacturing model by filling up holes in their production schedules with small orders coming in from elsewhere. This can lead to better capacity planning, increased capacity utilization rates, a healthier cash flow, and a thicker bottom line.
- Larger pool of experts. Not being constrained to a single area, companies that use the distributed manufacturing model have access to a larger number of experts to employ, whether they are manufacturing specialists, engineers, or administrative workers. Using cloud-based software means that tasks such as product design, the procurement of goods, production planning, finances, sales, etc. can be done remotely.
- Diffusion of risk. Having many production facilities that service their local markets eliminates the risk of stoppages affecting the whole business and increases overall resilience. In a traditional manufacturing company, disruptions in production or in the supply chain can affect the whole business. In distributed manufacturing, when one workshop in the network is experiencing downtime, the others can continue their work without a problem.
- Boost to local economies. Creating jobs in the market where you want to sell your products is beneficial to both the local economy and your company. Some of the money put into circulation there will inevitably end up back on your own balance sheet.
- Sustainability. Small-scale manufacturing near the suppliers of the raw materials as well as end-customers is not only feasible from the economical viewpoint. It is also a viable measure for tackling the issues of ecological damage created by the global distribution of goods. Cutting transportation miles off supply chains drastically reduces emissions and the overall carbon footprint of the goods.
Examples of distributed manufacturing
Some of the best-known examples of distributed manufacturing are platforms such as Xometry and Hubs that pool together thousands of workshops and allow people to upload their 3D models to have them manufactured as close to their location as possible.
But there are also specialized companies that use a network of local workshops to manufacture and distribute their products. One of the prime examples is AtFAB, a furniture design company from New York that offers its products on Opendesk, a platform for distributed furniture manufacturing.
WikiHouse is another distributed manufacturing company that designs and produces building blocks for constructing sustainable housing. Customers can order the CNC-machined blocks, have them manufactured in the nearest workshop, and assemble them on their own.
All of the above examples are innovators in their fields, however, distributed manufacturing can also work in more traditional settings. with the help of an ERP/MRP system.
Distributed manufacturing and ERP/MRP software
In order to centrally manage a network of micro-producers, a company has to implement an ERP/MRP system that supports managing several things at once:
- Subcontracted manufacturers. You can list your outsourced manufacturers, and issue and track purchase orders for them.
- Outsourced production operations. You can schedule manufacturing operations for the manufacturers and keep track of the progress.
- Multiple stocks and production sites. With this functionality enabled, you can manage geographically scattered facilities, create manufacturing and purchase orders for specific locations, and sell items from different stocks.
Many of such systems also offer integrations with various e-commerce platforms such as Shopify, WooCommerce, or BigCommerce, so that companies could set up their e-shops to communicate with the manufacturing software. When a customer order comes in, you can assign the work to a specific location or book the required products from the nearest stock.
Key takeaways
- Distributed manufacturing is a business model wherein the manufacturing facilities of an operation form a network over an extended geographical area.
- The networks can consist of autonomous members tied together by software or they can be companies that employ local micro-manufacturers to produce and distribute their products on a more limited scale.
- Goods are produced in smaller quantities and promptly shipped to customers located in the same area. Although production is likely to be more expensive, this disadvantage would be offset by much shorter lead times, lower distribution costs, and often higher-quality products.
- Other benefits of distributed manufacturing are lower costs of distribution, minimal requirements for capital investments, better flexibility and capacity utilization, diffusion of risk, and sustainability.
- Some of the more well-known distributed manufacturing platforms and brands are Xometry, Hubs, AtFAB, Opendesk, and WikiHouse.
- Distributed manufacturing could potentially also be set up with the help of an ERP system that supports subcontracting, outsourced production operations, and multiple stocks and production sites.
Frequently asked questions
Some of the best-known examples of distributed manufacturing are platforms such as Xometry and Hubs that pool together thousands of workshops and allow people to upload their 3D models to have them manufactured as close to their location as possible.
The key advantages of distributed manufacturing include reduced logistical costs, shorter lead times, more flexible supply chains, improved sustainability, diffusion of business risks, and boosts to local economies.
One of the central tenets of distributed manufacturing is to produce close to the end consumers. This cuts out lengthy shipping processes and saves a lot of money on distribution and logistics. As deliveries are made locally, lead times are also cut by a rather large margin.
You may also like: What Is Agile Manufacturing?