Different purchasing practices for manufacturers
A robust and accurate planning system is critical to any manufacturer. In this article, we are comparing different purchasing practices – ROP/ROQ Principles vs MRP System Planning.
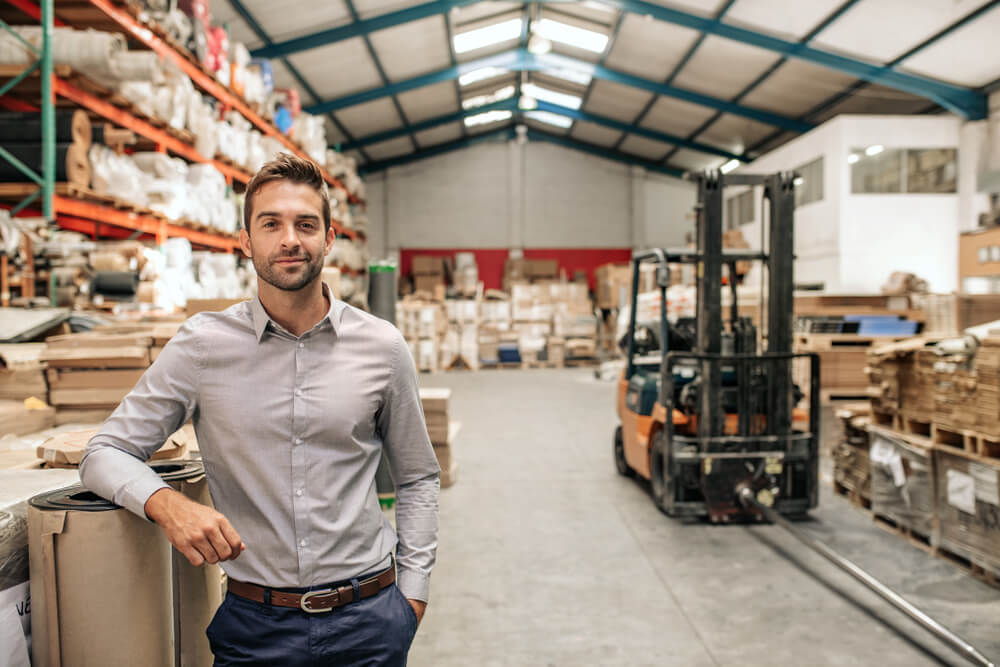
A robust and accurate planning system is critical to any manufacturer. However, unlike larger producers, small and medium-sized businesses (SMB) are often much more cash conscious as a matter of survival and or to shelter their growth plans. If the plan is too aggressive, companies may find themselves with too much inventory, tying up valuable cash-flow required for day to day operations. If the plan is too timid, companies may find themselves with stockouts that cause loss or cancellation of orders.
One long-running discussion on the value of which planning system to use has centered on whether a manufacturer should use a Reorder Point /Reorder Quantity planning system (ROP/ROQ) versus a Materials Requirement System (MRP) software. To understand which is best, it helps to look at what each system really is.
ROP/ROQ Planning
ROP/ROQ planning systems are consumption-based planning tools and formulas used to determine when to reorder material and in what quantities. With reorder point planning, orders for material are triggered by the depletion of stock items as orders are placed. Once a stock level for a component reaches a predetermined minimum, an order is placed for that component. This type of planning also uses a Reorder Quantity (ROQ) to determine how much stock to order for replenishment. Each of the two segments of this planning method utilizes a simple formula set.
ROP = (Lead Time in Days x Unit Sales per Day) + Safety Stock
This then yields the number of units where new components and raw materials orders should be placed to keep the factory running with no stoppage and without holding excess inventory.
ROQ = Square Root of ( 2 X Required Quantity X Cost per Order / Carrying Cost per Unit)
This then yields the quantity of the component to order at the reorder point.
A helpful book – Smart Inventory Solutions: Improving the Management of Engineering Materials By Phillip Slater.
While the formulas are simple, the two have important distinctions. ROP defines the when of the planning system, and ROQ defines how much. Also, ROQ is simply an inventory planning component, whereas ROP may be influenced by management due to cash-flow and current business conditions. Effectively, ROP is a more strategic and more stable aspect of the system, ROQ is a tactical aspect and one that may change due to many factors.
ROQ also carries with it the impact of a larger number of external factors such as freight costs, volume discounts and other things that affect inventory cost either positively or negatively. As such, it is an operational component that requires additional scrutiny in order to optimize costs.
Example: If a factory requires 5000 units of a component from an overseas supplier and a standard container holds 4,000 units, then a decision must be made to optimize the acquisition of the balance of the remaining 1,000 units. Shipping by another method increases cost, while deferring may risk stockouts. Or, the decision can be made to order two containers and “go long” on the additional component to optimize costs.
Material Requirements Planning
While ROP/ROQ systems can be done manually or with additional software, MRP systems are software-based inventory planning systems that help automate the planning and purchase of raw materials and components. It is also a forecast based system that takes sales forecast, production capacity and other forecasted aspects of production and develops a plan for components purchases for the Bill of Materials (BOM) of all parts required for final production.
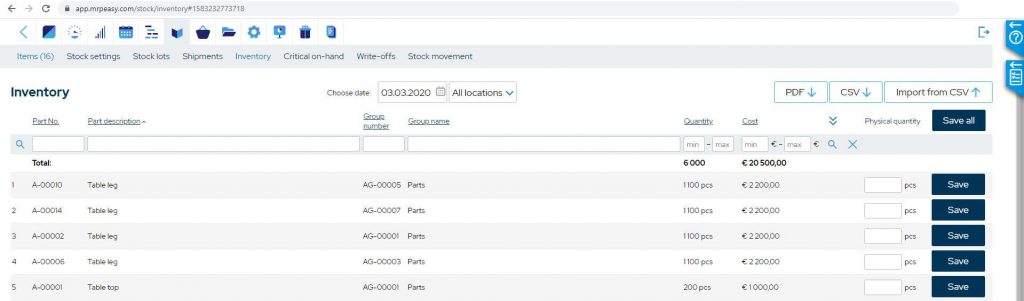
MRP systems also incorporate data such as quality, labor, process routing, FIFO, to create an optimized purchasing plan for all components. This helps companies maintain lower inventory levels while ensuring that the levels held are optimized for production resulting in a balance where few materials are held in excess yet stockouts do not occur.
MRP systems generally work backward from a production plan and use the Bills of Material to determine the raw materials required. The system answers not only when and how much, but what is required. This is done by using internal and external forecasting to determine what timeframe is required for ordering and completion. The forecasts and plan can be used over relatively shorter or longer time periods, depending on the total lead time required for production or for planning far ahead.
Comparisons of the Two Systems
MRP is a forecast-based planning system while ROP/ROQ is a non-forecasted planning system. Many argue that ROP/ROQ systems are more dependable because they can allow for reaction to greater levels of uncertainty involved in some production environments. For example, it has been noted that ROP/ROW planning is useful when raw materials and components are difficult or impossible to forecast.
ROP/ROQ is also said to be a good choice when demand is extremely stable, with only slight variations over time. This would include commodified high-volume goods where the unit cost is very small.
However, these conceits may be due to legacy issues where the familiar seems a better option, but practice proves otherwise. Academic studies have shown that when tested head to head, MRP systems outperform ROP/ROQ planning systems on all levels in terms of inventory efficiency. The study further indicated that while issues such as difficult forecasting, hyper-stable demand and fractional cost of the end-use product may significantly reduce the risk of using an ROP system, MRP’s automation and the broader application perform at a much more reliable level by comparison.
MRP planning can also perform reliably across different modes of production including MTO, MTS, ETO or blended modes and still provide benefits through actionable data and reports across a broader spectrum of a manufacturer and its managers. These include planned order schedules, order releases and changes to orders. Managers can use such data to optimize inventory levels, track material flow and requirements, compute optimal lot sizes matched to capacity and labor, and better control calculations for safety stock.
Perhaps the starkest difference is that today’s MRP systems are automated with deep analytical capability built into the platform. ROP/ROQ planning may utilize a dedicated software or it may not. In the case where it does, this system may be siloed causing interoperability issues with other software and risking the integrity of the data and analysis. And for those that are still done manually, the product and BOM complexity of many finished goods can outrun a human being’s capacity to calculate it and draw useful inferences from those calculations.
Today’s MRP systems are modular, agile, flexible and can often be purchased a la carte. They also tend to be cloud-based, providing up-to-date delivery of advancements and improvements to the software. ROP/ROQ systems are still a valid planning method. But compared to an MRP system’s ability to provide real-time inventory overview, accurate production planning and reporting, a broader view of the operation, and the ability to control and manage inventory costs, ROP/ROQ planning is less dependable, more prone to human error and at the risk introducing error in very complex manufacturing environments.
Key takeaways
- A robust and accurate procurement planning system is critical to any manufacturer.
- Some of the most important planning systems are Reorder Point /Reorder Quantity planning system (ROP/ROQ) and Materials Requirement System (MRP) software.
- ROP/ROQ planning systems are consumption-based planning tools and formulas used to determine when to reorder material and in what quantities.
- MRP systems are software-based inventory planning systems that help automate the planning and purchase of raw materials and components.
- While ROP/ROQ still has its uses, modern manufacturers are quickly moving toward implementing MRP systems.