What Is Decoupling Inventory?
Decoupling inventory is the strategic buffer stock of subassemblies and WIP that could be used when suppliers are unavailable, when there are internal disruptions like machinery breakdown, or when demand is greater than expected. It allows companies to prevent all-around stoppages and mitigate the bullwhip effect.

You can also listen to this article:
What is decoupling inventory?
Decoupling inventory is the buffer stock kept to supplement strategic stages of the manufacturing process to counter disruptions in the company’s supply chain. It means stocking up on specific subassemblies and work-in-process inventory in order to shorten lead times or to prevent stoppages in one area of production from spreading over to the whole operation.
For example, a furniture manufacturer with just two workstations – assembly and painting – might want to keep an extra inventory of products that are assembled, but not yet painted. In this case, when assembly breaks down due to supplier issues, employee illness, etc., the painting department can continue work on the assembled furniture set aside as decoupling inventory, thereby being able to fulfill customer orders on time. Having this extra WIP inventory can also help the company respond to unexpectedly high demand.
Another example would be modern automobile manufacturers that often first assemble almost-ready vehicles, store them in inventory, and then add customizations like paint and extras according to incoming customer orders. In this case, the core product is used as decoupling inventory to ensure prompt deliveries to customers.
This inventory management technique can be used, however, in any environment with multiple interdependent workstations. Keeping extra decoupling WIP inventory between these stages of production (in the decoupling points) can ensure that when a breakdown occurs in one workstation, the others down the line can continue work as usual. Likewise, if one stage of the production process is slower than the others, keeping extra inventory at the decoupling point between this and the next leg of production can significantly reduce lead times. The same goes for when raw materials are delayed. As such, decoupling inventory can be a very effective antidote against the bullwhip effect.
What is a decoupling point?
A decoupling point is a point between different stages of production where decoupling inventory is held. This does not necessarily mean that the extra stock is physically stored in an area between different workstations. Rather, these subassemblies and WIP are still held in the warehouse and brought to the production floor when needed.
For example, in the aforementioned furniture workshop, the decoupling point is between assembly and painting. This means that the decoupled inventory is assembled but not painted.
More complex systems can, however, have multiple decoupling points, thereby creating a more flexible supply chain.
Advantages of decoupling inventory
The advantages of keeping decoupling inventory are:
- Prevents stoppages due to supplier
unavailability. - Prevents stoppages due to internal factors such
as employee illness or machinery breakdown. - Enables the company to respond to spikes in
demand. - Mitigates the bullwhip effect by creating a
barrier between supply and demand, thereby reducing the fluctuations on both
ends. - Allows the company to perform maintenance on
certain workstations without halting production. - Could be used to minimize lead times.
The most discernible disadvantages of decoupling inventory are the higher inventory costs and extra space requirements, but if approached analytically, the advantages will surely outweigh the disadvantages.
Decoupling inventory vs. safety stock vs. pipeline inventory
There might be considerable confusion regarding the terms “decoupling inventory”, “safety stock”, and “pipeline inventory” as they all refer to some kind of an inventory buffer. But the difference is quite easy to understand.
As we already learned, decoupling inventory means building up a stock of extra inventory to be used in production when a disruption breaks the normal manufacturing cycle. Generally, decoupling inventory is associated with the internal supply chain of the company. That means it is used to mitigate the risk of stoppages due to machinery breakdown or maintenance, employee unavailability, etc. This is done by supplying the decoupling points between different stages of production with extra subassemblies and WIP inventory.
Safety stock, on the other hand, refers to a buffer of raw materials or finished products that are used to respond to disruptions on the suppliers’ side or to spikes in customer demand. The term “safety stock” is therefore generally used in the context of countering issues in the external supply chain of the company. Companies that make to order can use the safety stock of raw materials and parts to continue production when suppliers are delayed while companies that make to stock can use a safety stock of finished goods to respond to unexpectedly high demand.
Pipeline inventory, however, refers only to the suppliers’ side of the supply chain. It consists of the parts and raw materials that the company has already ordered but which have yet to arrive at the facility. Businesses might want to keep a pipeline inventory when suppliers’ lead times are very long. This way, some quantities of the required raw materials and parts are constantly in transit and arrive at regular intervals that are much shorter than the lead time of the supplier.
Decoupling inventory in ERP/MRP systems
The easiest way to set up decoupling inventory in an ERP/MRP system is to create multi-level bills of materials for your goods. Within this functionality, you can create products that are composed of subassemblies. If you need to keep track of decoupling inventory, you can treat WIP that has completed certain stages of the production process as subassemblies that are used in the final product.
For example, a plain wooden table can be a subassembly for making a painted wooden table.
When a customer orders a painted wooden table and a manufacturing order is created, the system automatically checks if the necessary subassembly (the plain wooden table) is already in stock. If not, the manufacturing order includes the production of the required subassembly. As with other products, the subassemblies can also be assigned safety stocks and reorder points so that a defined number of decoupling inventory would always be in stock. It is also possible to have the subassembly product group named “Decoupling inventory” and have it categorized as WIP for accounting purposes.
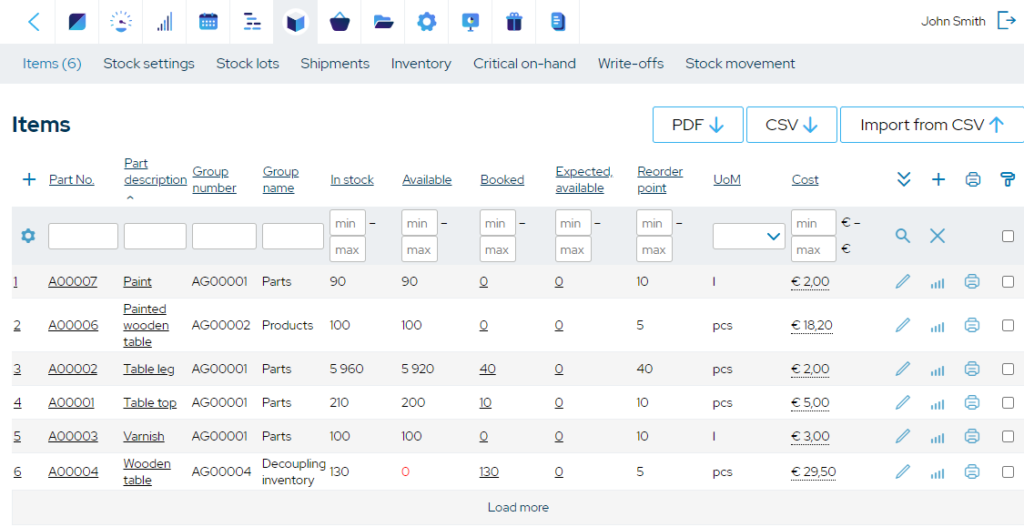
Key takeaways
- Decoupling inventory is the buffer stock kept to
supplement strategic stages of the manufacturing process to counter disruptions
in the company’s internal supply chain. - It means stocking up on specific subassemblies
and WIP, as well as raw materials and parts needed to complete the products, at
the decoupling points in order to shorten lead times or to prevent stoppages in
one area from spreading over to the whole operation. - Decoupling points are the points between
different workstations where inventory is decoupled, e.g. a furniture
manufacturer could decouple between assembly and painting. This way, there is
always assembled furniture ready to be painted and shipped out. - Decoupling inventory is often confused with
safety stock and pipeline inventory. While decoupled inventory means
subassemblies and WIP stocked at decoupling points, safety stock refers to raw
materials and finished goods that act as a buffer when suppliers are
unavailable or when demand is greater than usual. Pipeline inventory is the
flow of materials that is continuously in transit, arriving at regular
intervals to mitigate long supplier lead times. - Decoupling inventory can be easily managed in an
ERP/MRP system that supports multi-level BOMs.
You may also like: What Is Vendor-Managed Inventory (VMI) and How to Use It?