What Is Dead Stock and How to Avoid It?
Dead stock consists of inventory items that your business cannot use according to their original purpose. There are many different types of dead stock and various ways to either eliminate it or avoid it in the first place.
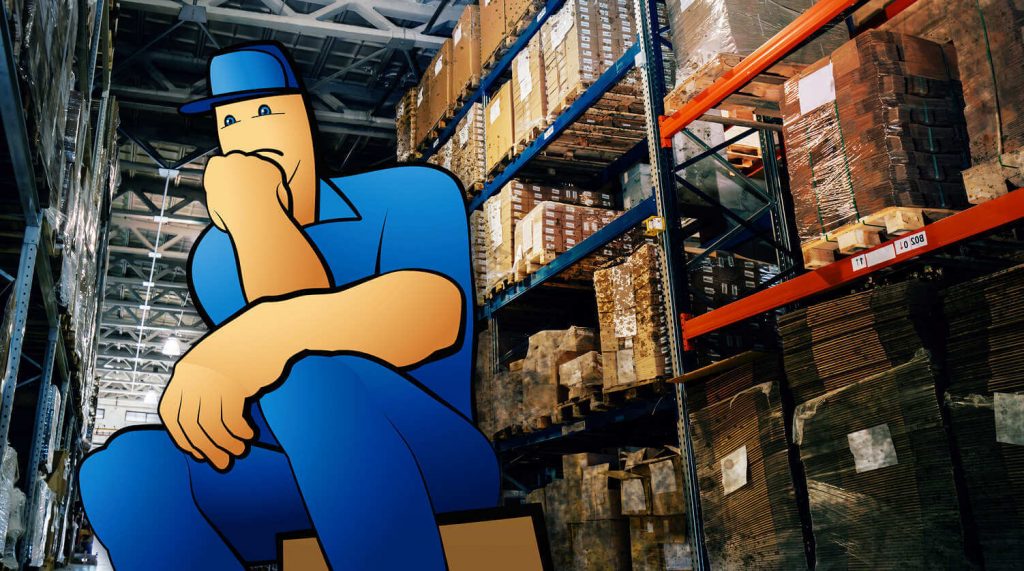
You can also listen to this article:
What is Dead Stock?
Dead stock is the products or materials in your inventory that have lost their function to your business and will most likely not be used according to their original purpose.
There are various causes for accumulating dead stock. These may range from engineering changes and improper storage conditions to inefficient inventory management practices and poor sales.
Holding on to dead stock is never a good idea as it is a waste of money and storage space. That is why small businesses need to take appropriate measures to eliminate it, or better yet, to avoid it in the first place.
Dead Stock vs. deadstock
In addition to the term “dead stock” which can be applied to any business environment where inventory is held, there is also “deadstock”. Deadstock is mostly related to the garment retail industry and means products that have been discontinued, such as vintage items. As opposed to dead stock, deadstock items are usually very high in value.
“Deadstock” is sometimes also used in the sense of the machinery used in a farm, as opposed to “livestock”.
Types of Dead Stock
There are several types of dead stock that a company may experience. Each of those can be traced to different circumstances and may require a different approach for managing them.
1. Obsolete inventory
Obsolete inventory is goods that have not been used or sold for a long period of time due to a lack of demand. Inventory can become obsolete in many ways. For example, new trends or models might replace old ones as they often do in the garment and electronics industries. When a holiday season ends, a company might end up with loads of unsold holiday-themed stock. A manufacturing company might decide to use different materials or components in a product, leaving the replaced goods collecting dust on the stockroom shelves. Or poor sales caused by ineffective marketing might prompt a company to ditch a product line completely.
2. Damaged goods
Damaged goods are materials or products that have become unusable due to careless inventory handling, manufacturing mishaps, or poor conditions in the warehouse. For example, a pallet with an unbalanced load might fall off a forklift, faulty machinery might render some materials unusable, or a leak could ruin a batch of goods that need to be kept dry.
3. Expired goods
The sector most susceptible to the expiration of goods is the food industry. However, there are also other industries where manufacturers and distributors need to keep tabs on expiration dates, including sectors such as pharmaceuticals and chemicals. Rigid regulations in industries that deal with expiring goods require companies to carefully track the expiry dates of their inventory, which can be done by using lot tracking software.
4. Defective goods
Defective goods are items that have not suffered explicit damage in your facility but are faulty in some way. These defects can sometimes be traced back to the supplier, but they can also occur due to engineering or design errors in your own facility.
5. Forgotten inventory
Sub-par inventory management practices may lead to inventory being stocked away and forgotten. For example, if inventory is not properly accounted for, a company might order extra stock without knowing that there are usable goods still somewhere in the stockroom. Forgotten inventory can often still be used, but in some cases, it can also become expired or obsolete.
Negative effects of Dead Stock
Dead stock can harm your company in many ways. Here are some of the most important negative aspects of holding dead stock.
Cash flow problems and reduced profits
First and foremost, dead stock incurs losses on your balance sheet. When you have paid good money for products or materials and have to write them off in the end, it can have a major impact on your profits depending on the quantity of dead stock.
Hidden costs
Accumulating and holding dead stock also incurs costs other than the direct losses due to write-offs. Unusable inventory means missed sales opportunities and even if you manage to sell the goods back to the supplier or to off-price resellers to minimize your losses, you will never cover the full price you could have asked for your products on the market. Other hidden costs incurred with dead stock is what you pay your employees for handling the unusable inventory, and what you pay for storing and transporting it.
Waste of inventory space
Inventory takes up space and storing dead stock makes it dead space. Instead of using your warehouse or stockroom efficiently, you will be wasting room on inventory that brings in nothing of value. As mentioned before, this also means paying for storage and labor. Clearing out your dead stock leaves more resources to be allocated to more valuable goods.
What to do with Dead Stock?
If you find out that you are holding dead stock, there are some measures that you can take to put it to use and minimize losses.
1. Sell it off. One company’s dead stock could be another company’s usable inventory. Try selling your dead stock back to your suppliers or to other companies that may need it.
2. Recycle the materials. In some cases, you can use dead stock materials for something else. However, if you cannot utilize them in your facility or sell them off, take your dead stock to a recycling company to get at least something back.
3. Donate it. If some of your goods are no good for you anymore, they might still be useful for someone else. Donating your dead stock to a charity could improve your company image and make you eligible for a tax write-off.
4. Bundle it. If you are selling your products directly to consumers, you can bundle/kit obsolete inventory together with merchandise that sells. By using product kitting, you can still make some money off your dead stock.
5. Throw it away. If nothing else works, the only way to avoid further losses is to eliminate dead stock from your inventory.
How to avoid Dead Stock?
Regardless of what you manufacture or sell, there are some universal steps you can take to make sure that dead stock would not become a problem for your business. These are:
1. Review your ordering practices
A surefire way to ensure there is minimum risk of accumulating dead stock is to keep inventory minimized. You can do this by implementing just-in-time inventory practices or order smaller quantities more frequently. Whichever method you use, good communication with your suppliers is essential.
2. Use accurate forecasting
Accurate forecasting is a must for distributors and make-to-stock manufacturers to ensure optimal inventory levels and avoid dead stock. Forecasting works by pulling in data from all areas of the business in order to identify demand trends and give you insights about when to order more stock. To create accurate forecasts, it is recommended to use software that collects large amounts of data from across your operation, such as an ERP/MRP system.
3. Inspect incoming goods
Inspecting incoming goods gives you the chance to detect any non-conformance early on and request a refund or a new shipment from your suppliers. If you do not find out that the materials or products are defective until they are already on the production floor or, worse yet, in the hands of a customer, it is difficult to prove to your suppliers that the problem was on their end.
4. Use inventory control techniques
Proven inventory control techniques such as ABC analysis, safety stock, reorder point, First-in-First-out, etc. are essential tools in most inventory environments. These methods provide a concrete framework for inventory organization, replenishment, and consumption, giving you the power to stay on top of your inventory operations at all time.
ABC analysis categorizes your inventory items by their consumption value or frequency, allowing you to better allocate resources or physically organize your stockroom.
Safety stock is a mathematical approach to holding buffer stock. It provides you with the optimal levels of extra stock you should hold at all times.
Reorder point is a mathematical approach to determining inventory levels at which you should replenish your stock. When an SKU’s quantity drops to the level of the reorder point, it is time to order/manufacture more. Reorder point is best used along with safety stock.
First-in-First-out (FIFO) is an inventory consumption technique. By following it, you will consume stock lots by the order they were taken into inventory. This is a great method for managing goods that have an expiration date.
5. Track your inventory with ERP/MRP software
ERP/MRP systems with built-in inventory management software and purchasing modules have quickly become a must in manufacturing and distributing businesses. Companies using spreadsheets or multiple different standalone systems for inventory management, order processing, production planning, scheduling, and accounting are realizing that old tools and methods are getting in the way of growth. Using a single software for everything allows companies to develop highly effective communication practices, create accurate schedules, and minimize as well as easily track their inventory, including expiry date tracking.
6. Take care of your employees and facilities
A lot depends on the shape of your employees and your facility. Training your employees to follow proper safety and inventory management procedures is an important prerequisite for the previous steps to work. Apart from teaching new employees the protocols, older members of staff need refresher training sessions as well. Finding a balance between discipline and unreasonable expectations is necessary to prevent your employees from hurting themselves or damaging goods or equipment. The same goes for proper conditions (lighting, cleanliness, equipment installation and maintenance, etc.) and appropriate warehouse organization.
7. Invest in marketing
When you are not visible to your target audience, you risk low demand for your products, which in turn creates the risk of your inventory becoming dead stock. Getting clients by word-of-mouth is great, but using different media to spread the word can significantly increase sales and improve your inventory turnover rate as well as your cash flow. The key is to be present in environments where your target audience is active, such as events, print and online publications, internet forums, social media sites, etc.
Read more about Manufacturing Branding – Marketing ABC for Small Manufacturers.
Key takeaways
- The term “dead stock” refers to products or materials in your inventory that have lost their function to your business and will most likely not be used according to their original purpose.
- There are several different types of dead stock, each of them having their origins in different inefficiencies in your facility.
- Obsolete inventory is goods that have not been used or sold for a long period of time due to a lack of demand.
- Damaged goods are materials or products that have become unusable due to careless inventory handling, manufacturing mishaps, or poor conditions in the warehouse.
- Expired goods are items that have aged past their latest permitted date of usage.
- Defective goods are items that have not suffered explicit damage in your facility but are faulty in some way.
- Forgotten inventory is goods that have been received into stock and then left there unused due to poor inventory management practices.
- When you have accumulated dead stock, you can either eliminate it as trash, or try to salvage some money by selling it off, donating it, recycling it, or bundling it with other goods.
- The accumulation of dead stock can be avoided by reviewing your ordering practices, producing accurate forecasts, inspecting incoming goods, using inventory control techniques and an ERP/MRP software, by training your employees and keeping your facility in good condition, and by putting more emphasis on your marketing efforts.
You may also like: What Is Traceability in Manufacturing and How to Achieve It?