Was ist der ROI eines MRP-Systems und wie kalkulieren Sie ihn?
Wenn es um die Einführung eines MRP-Systems geht, halten viele kleine Herstellungsunternehmen das für zu teuer für sie. Um sie zu beruhigen, haben wir einen kurzen Leitfaden zur Kalkulation der Kapitalrendite eines MRP-Systems erstellt.
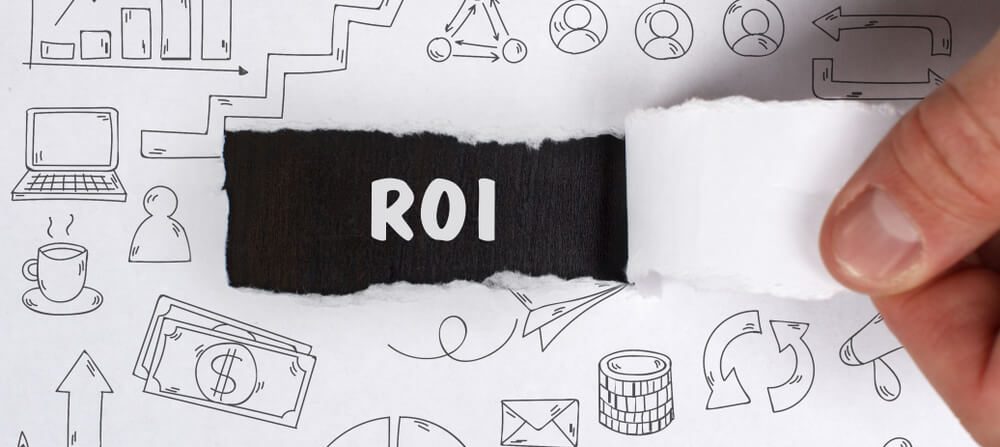
Warum ist es wichtig, vor einer Investition den ROI zu schätzen?
Viele Kleinunternehmen schieben die Entscheidung ständig auf, ob sie in ein MRP-System investieren sollen oder nicht, da sie sich schwer tun, die Kapitalrendite zu schätzen. Es herrscht der weitverbreitete Irrglaube vor, dass der ROI in Bezug auf Investitionen in digitale Lösungen nicht kalkuliert werden kann, doch das stimmt nicht. Ein weiterer häufiger Fehler ist die Annahme, dass positive Ergebnisse garantiert sind, unabhängig davon, welche digitale Lösung letztlich eingeführt wird. Tatsächlich besteht jedoch ein hohes Risiko, in die falschen Funktionen, zu viel oder zu wenig zu investieren, was zu einer extrem langwierigen Kapitalrendite oder gar zu verringerter Produktivität führen kann.
Bereits in den 70ern und 80ern, in den Spitzenzeiten der Automatisierung vieler Produktionsprozesse, wurden bereits ähnliche Trends beobachtet, dass nicht alle Investitionen zu positiven Ergebnissen führten. In vielen Fällen lag der Produktivitätsanstieg weit unter dem Erwartungswert. Dr. Armand Feigenbaum, ein amerikanischer Qualitätskontrollexperte, beschrieb dieses Phänomen in einem Interview mit Industry Week und sagte: „Nach 10 oder 15 Jahren der Automatisierung und Computerisierung – haben wir wenn überhaupt die ‘Hidden Factory’ noch größer gemacht.”
Die Hidden Factory ist ein von Feigenbaum geprägter Begriff und bezeichnet die Tätigkeiten in einem Herstellungsprozess, die Qualität und Effizienz eine betrieblichen Tätigkeit senken. Demnach ist es entscheidend, vor einer Investitionsentscheidung die potenziellen Vorteile gründlich zu untersuchen.
Wie können Sie den ROI eines MRP-Systems kalkulieren?
Wie können Sie die Auswirkungen eines MRPs auf die Produktivität und EBITA (Ergebnis vor Zinsen, Steuern und Firmenwertabschreibung) kalkulieren? Betrachten wir das zunächst aus einem anderen Winkel. Weder ein MRP-System noch irgendeine andere digitale Lösung kann einen direkten Einfluss auf die Rentabilität oder Produktivität haben, ohne dass ein Unternehmen gleichzeitig Änderungen an seinen Prozessen vornimmt.
Höhere Produktivität lässt sich erreichen, indem Produktionsprozesse optimiert und die ‚Hidden Factory‘ reduziert werden, wobei das MRP-System eine wichtige Rolle einnimmt, die für die Prozessoptimierung nötigen Bedingungen zu schaffen. In diesem Artikel finden Sie einen simplen und effektiven 8-Schritte-Prozess, mit dem Sie die Gewinne schätzen können, die Ihnen die Einführung eines MRP-Systems bringen kann.
Bevor Sie loslegen, sollten Sie Kennzahlen einrichten, mit denen Sie die Performance Ihres Unternehmens überwachen können. Rentabel zu werden wird oft als eine dieser Kennzahlen verwendet, was nicht notwendigerweise falsch ist. Bedenken Sie jedoch, dass Gewinn = Preis – Kosten ist. Der Verkaufspreis wird zu einem hohen Grad beeinflusst vom Wettbewerb und der Bereitschaft des Kunden, für ein bestimmtes Produkt zu bezahlen, während die Kosten unter direkter Kontrolle des Unternehmens sind. |
Es gibt drei universelle Kennzahlen, die unabhängig von Größe oder Branche für alle Unternehmen gelten:
- Kosten. Falls der Wettbewerb härter wird und Sie sich gezwungen sehen, beim allgemeinen Preiswettbewerb auf dem Markt mitzumachen, können Sie durch Senkung Ihrer Kosten Ihren Gewinn aufrechterhalten.
- Fehlerquote. Fehler erzeugen die ‚Hidden Factory‘, die Ihre Ressourcen aufzehrt und die Produktivität verringert.
- Leadzeit. Die Leadzeit ist meiner Meinung nach die am meisten unterschätzte Kennzahl, da sie sich auf beide Komponenten auswirkt, Gewinn – Preis und Kosten. Je länger Ihre Produkte in der Produktion sind, desto mehr nicht-wertschöpferische Aufgaben fallen an und desto höher sind die Kosten. Gleichzeitig verringern kürzere Leadzeiten nicht nur die Kosten, sondern schaffen auch einen Wettbewerbsvorteil, wodurch Sie die Gelegenheit erhalten, den Preis zu erhöhen.
Der Grundgedanke hinter der Kalkulation des ROI eines MRPs ist zu schätzen, wie gut das MRP notwendige Optimierungen durch Steigerung von Effektivität und Effizienz von Prozessen ermöglichen kann. Die Effektivität misst, wie viele Aktivitäten nötig sind, um das Endergebnis zu erreichen. Diese notwendigen Aktivitäten heißen wertschöpfende Aktivitäten. Die Effizienz misst, wie gut die Aufgabe ausgeführt wird.
8-Schritte-Prozess zur Kalkulation des ROI eines MRPs
Schritt 1: Bilden Sie Ihre aktuellen Prozesse ab
Um Optimierungen vorzunehmen, müssen Sie Ihre aktuellen Prozesse rundum verstehen. Sehr häufig wissen Manager nicht genau, wie die erforderlichen wertschöpfenden Schritte lauten, um ein Produkt von seinen Rohstoffen in einen fertigen Artikel umzuwandeln. Gleichzeitig wissen sie auch nicht um die nicht-wertschöpfenden Aufgaben Bescheid, die dazwischen verborgen liegen. Ein Mapping-Prozess kann helfen, die nicht-wertschöpfenden Aufgaben oder Verschwendung zu finden.
Schritt 2: Identifizieren Sie die nicht-wertschöpfenden Aufgaben und Ineffizienzen in Ihrem Prozess.
Laut der Lean Operational Excellence Strategie lässt sich jede ausgeführte Aufgabe in eine von drei Kategorien einteilen: wertschöpfende Arbeit, nicht-wertschöpfende Arbeit und pure Verschwendung oder Muda.
Damit eine Aufgabe als wertschöpfend bezeichnet werden kann, muss sie drei Kriterien erfüllen: Zunächst muss die Aufgabe Mehrwert für den Kunden schaffen (oder der Kunde muss bereit sein, für sie zu zahlen). Zweitens verändert die Aufgabe die Form oder Funktion des Produkts. Drittens muss die Aufgabe beim ersten Versuch richtig ausgeführt werden. Ihr Ziel lautet demnach, nicht-wertschöpfende Aktivitäten und Verschwendung zu finden und aus dem Prozess zu entfernen.
Einige nicht-wertschöpfende Aufgaben sind jedoch erforderlich, um die Ausführung von wertschöpfenden Aufgaben zu unterstützen. Diese unterstützenden Aufgaben werden oft als Hilfsaufgaben bezeichnet. Sehen Sie sich die Möglichkeiten an, wie Sie diese Hilfsaufgaben ausführen können, sodass sie sich nur minimal auf die Performance und Zykluszeiten der wertschöpfenden Aufgaben auswirken. Ein bekanntes Beispiel stammt von Toyota, wo der Wechsel von Gussformen bis zu 3,5 Stunden dauerte. Mit der Zeit schafften es Toyotas Techniker, diese Wechselzeit auf gerade einmal 3 Minuten zu senken.
Hier ist eine kurze Einführung, wie Sie den Einfluss von Hilfsaufgaben auf die Effektivität des Betriebs verringern können.
Alle Aufgaben, die während der Durchführung einer Tätigkeit ausgeführt werden, lassen sich in ‚interne Aufgaben‘ und ‚externe Aufgaben‘ aufteilen. Eine ‚interne Aufgabe‘ kann nur ausgeführt werden, wenn eine Maschine oder ein automatisierter Prozess gestoppt wurde. Eine ‚externe Aufgabe‘ hingegen kann ausgeführt werden, wenn die Maschine oder der automatisierte Prozess gleichzeitig läuft.
Denken Sie beispielsweise an eine maschinelle Arbeitsstation eines Auftragsfertigers, bei der Teile mit einer CNC-Maschine bearbeitet werden. Um die Tätigkeit komplett auszuführen, muss der Maschinenführer eine Reihe an Aufgaben abschließen, wie etwa: Das fertige Teil aus der Maschine nehmen, es ablegen und etikettieren, eine neue Aufgabe und das nächste zu fertigende Teil finden, es in die CNC-Maschine legen, eine Stanzform für das nächste Teil einbauen und die Fertigung abschließen.
Sowohl die Entfernung des fertigen Teils und die Beladung des neuen sind eindeutig ‚interne Aufgaben‘, weil sie sich nur ausführen lassen, wenn die Maschine gestoppt ist. Alle anderen Aufgaben – das Teil ablegen und etikettieren, eine neue Aufgabe und das nächste zu fertigende Teil finden und dessen Stanzform einbauen – könnten aktuell auch ‚interne Aufgaben sein‘, wobei sich viele von ihnen auch dann ausführen lassen, wenn die Maschine läuft. Das bedeutet, dass sich einige, wenn nicht sogar die meisten der ‚internen Aufgaben‘ von heute in ‚externe Aufgaben‘ umwandeln lassen. Ihr Ziel lautet, Möglichkeiten zu finden, wie Sie so viele ‚interne Aufgaben‘ wie möglich zu ‚externen Aufgaben‘ machen können.
Schritt 3: Ermitteln Sie den aktuellen Zustand Ihrer Leistungskennzahlen.
Oben haben wir die Kennzahlen auf Unternehmensebene diskutiert – Kosten, Leadzeit und Fehlerquote. An der Arbeitsstation oder auf Tätigkeitenebene lassen sich folgende geeignete Kennzahlen einsetzen: Zykluszeit, Gesamtanlageneffektivität (OEE) und die Fehlerquote. Wenn Sie diese Zahlen vor Ihrer Prozessänderung nicht korrekt erfassen, verlieren Sie die Möglichkeit, das Ergebnis der Änderungen zu bewerten.
Schritt 4. Erstellen Sie ein Konzept des Soll-Prozesses.
Bilden Sie die erste Version Ihres neuen Soll-Prozesses ab, bei dem sämtliche (oder zumindest die meiste) Verschwendung ausgemerzt und so viele ‚interne Aufgaben‘ wie möglich zu ‚externen Aufgaben‘ gemacht wurden.
Schritt 5: Analysieren Sie, welche Voraussetzungen erfüllt sein müssen, um den Soll-Prozess einzuführen.
Einige Voraussetzungen lassen sich durch Änderungen innerhalb der Organisation erreichen. Wenn Sie beispielsweise den Aufbau Ihrer Fabrik ändern, könnte es möglich sein, Transportzeiten und den Energiebedarf, Teile von Arbeitsstation zu Arbeitsstation zu bringen, zu verringern.
Einige Voraussetzungen lassen sich durch Technologie schaffen. Um beispielsweise zu fertigende Teile schneller aus dem Bestand an unfertigen Erzeugnissen zu finden, ist ein MRP erforderlich, das den Standort von Teilen im Lager verfolgen kann. Um die Etikettierung von Teilen zu beschleunigen, brauchen Sie eine MRP-Lösung, die Barcodes drucken kann, wenn eine Tätigkeit als abgeschlossen gemeldet wird, sowie einen Etikettendrucker. Um das Reporting zu beschleunigen, brauchen Sie möglicherweise ein MRP, das Barcodes auf Arbeitsaufträge drucken kann, wodurch der Maschinenführer nur den Barcode scannen muss, um eine Tätigkeit zu melden.
Schließen Sie die Analyse für alle Tätigkeiten in Ihrem Prozess ab. Stellen Sie anschließend die Liste mit Lösungen und den für sie benötigten Funktionen auf, die für die Schaffung der Basis der Prozessoptimierung nötig sind.
Schritt 6: Bewerten Sie verfügbare Lösungen und zu welchem Grad sie die erforderlichen Voraussetzungen schaffen können.
Bei der Bewertung von Lösungen, die bei der Schaffung der nötigen Voraussetzungen helfen könnten, wählen Sie diejenigen aus, die den höchsten Einfluss auf die Prozessoptimierung haben.
Schritt 7: Finalisieren Sie den Soll-Prozess
Erstellen Sie mit dem Wissen, welche Prozesse zu welchem Grad optimiert werden können, und unter Berücksichtigung der Funktionen Ihres ausgewählten MRPs eine finale Version Ihrer Soll-Prozess-Karte. Berechnen Sie dann die neue Durchsatzrate.
Schritt 8: Kalkulieren Sie den Effekt und den ROI.
Angenommen, Ihr aktueller Durchsatz beträgt 500 Teile pro Monat und Ihre gesamten Fertigungsgemeinkosten (Abschreibung auf Anlagen, Gehälter und Löhne für Fabrikpersonal und Energiekosten für die Betreibung der Anlagen) betragen 100.000$, was 200$ pro Teil entspricht. Nach der Einführung einer MRP-Lösung und der Anwendung der erforderlichen Prozessänderungen beträgt Ihr Durchsatz 650 Teile pro Monat.
Um unser Beispiel nicht unnötig kompliziert zu machen, nehmen wir an, dass die Prozessänderungen sich nicht auf die Gemeinkosten auswirken. In diesem Fall verringert sich die Gemeinkostenkomponente der Produkte von 200$ pro Produkt auf 153,85$ pro Produkt. Das entspricht 650 x 46,15$ = 29.997$ an eingesparten Kosten pro Monat durch verringerte Gemeinkosten, wenn Sie Ihren erwarteten Durchsatz erreichen. Außerdem steigern Sie Ihren Gewinn durch Umsatzwachstum.
Kalkulieren Sie auf ähnliche Weise alle Vorteile, die Sie erreichen, einschließlich der Verringerung von Kosten in Bezug auf weniger Fehler. Für unser Beispiel können Sie sich die folgende Tabelle ansehen – die Gesamtergebnisse zeigen eine Kapazitätserhöhung von 30%, eine Umsatzsteigerung von 30% und 54% Gewinnsteigerung.
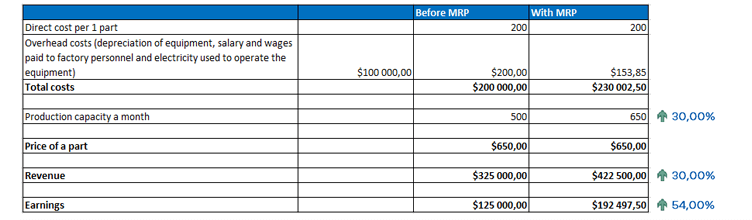
Berechnen Sie jetzt die erforderliche Gesamtinvestition für die Einführung des MRPs, die Prozessänderungen und die Ausbildung von Mitarbeitern. Kalkulieren Sie die monatliche Abschreibung für ein hergestelltes Produkt. Wenn Sie ein MRP mit monatlichem Zahlungstarif wählen, sollte das eine recht simple Kalkulation sein.
Betrachten wir uns ein Beispiel, bei dem die gesamten Projektkosten, einschließlich die Beschaffung von neuen Geräten und MRP-Software sowie die Anstellungskosten des Projektmanagers für das Einführungsprojekt und die Kosten für vorübergehende Produktionsausfälle zur Anwendung von Änderungen, 75.000$ betragen. In diesem Fall läge die optimistische Kapitalrendite der MRP-Lösung bei gerade einmal knapp über einem Monat. Da die Gewöhnung an neue Verfahren und neue Software eine Lernkurve erfordert, läge ein realistisches Ergebnis bei optimistischer Sichtweise für den ersten Monat normalerweise zwischen 70% und 85%.
Welche Vorteile liefert der oben beschriebene Prozess?
Wenn Sie die 8 Schritte dieses Prozesses befolgen, erhalten Sie Fakten, um Entscheidungen zu treffen, welche Eigenschaften Ihres Soll-Prozesses eine MRP-Lösung brauchen. Sie bekommen ebenfalls einen Plan, mit dem Sie eine Lösung wählen können, die zu Ihren Anforderungen passt. Sie können datengetriebene Entscheidungen treffen, basierend darauf, welche Prozessänderungen es in Anbetracht Ihrer aktuell verfügbaren Optionen wert sind gemacht zu werden. Sie können Änderungen priorisieren, die eine höhere erwartete Rendite bringen.
Als Bonus entdecken Sie innerhalb des Prozesses „leichte Beute“, sprich Änderungen, die Sie sehr leicht und schnell erreichen können, oftmals sogar ohne investieren zu müssen.
Die wichtigsten Kernpunkte
- Viele Herstellungsunternehmen haben damit zu kämpfen, den ROI eines ERP- oder MRP-Systems zu schätzen.
- Der ROI lässt sich für alle Lösungen berechnen, einschließlich digitaler.
- Die positiven Ergebnisse einer Einführung hängen jedoch von der Fähigkeit eines Unternehmens ab, seine Prozesse ändern zu können.
- MRP-Systeme spielen eine entscheidende Rolle bei der Schaffung der Bedingungen für die Prozessoptimierung.
- Die drei grundlegenden Kennzahlen, die in jedem Unternehmen überwacht werden sollten, sind: Gewinn, Fehler und Leadzeit. Bei richtiger Einführung kann ein MRP-System bei allen dreien für Verbesserungen sorgen.
1. Bilden Sie Ihre aktuellen Prozesse abBei der Kalkulation des ROI eines MRP-Systems fallen acht Schritte an:
2. Identifizieren Sie nicht-wertschöpfende Aufgaben und Ineffizienzen
3. Erfassen Sie den aktuellen Zustand Ihrer Leistungskennzahlen
4. Erstellen Sie ein Konzept Ihres Soll-Prozesses
5. Analysieren Sie, welche Voraussetzungen erfüllt sein müssen, um den Soll-Prozess einzuführen
6. Bewerten Sie verfügbare Optionen und deren Fähigkeit, die nötigen Voraussetzungen zu schaffen
7. Finalisieren Sie den Soll-Prozess
8. Kalkulieren Sie den Effekt und den ROI- Normalerweise beträgt der ROI eines MRP-Systems im ersten Monat zwischen 70% und 85%.
- Dieser Prozess der ROI-Schätzung hilft Ihnen bei der Prüfung Ihrer Prozesse und gibt Ihnen eine Vorstellung darüber, welche Software-Lösung Sie brauchen.
- Er offenbart außerdem „leichte Beute“ – sprich Prozessänderungen, die Sie leicht und ohne zusätzliche Investitionen erreichen können.
This guest article was written by Edward Laur, CEO of consulting company Laur & Partners.