Was ist ein Master Production Schedule? Mit Beispielen
Der Master Production Schedule (MPS) ist ein Produktionsplanungsinstrument, das Sie herausfinden lässt, wie viel von einem Produkt in den verschiedenen Perioden hergestellt werden muss. Dieser einfache Plan kann als Grundlage für die weitere Planung und Terminierung im gesamten Fertigungsbetrieb verwendet werden.
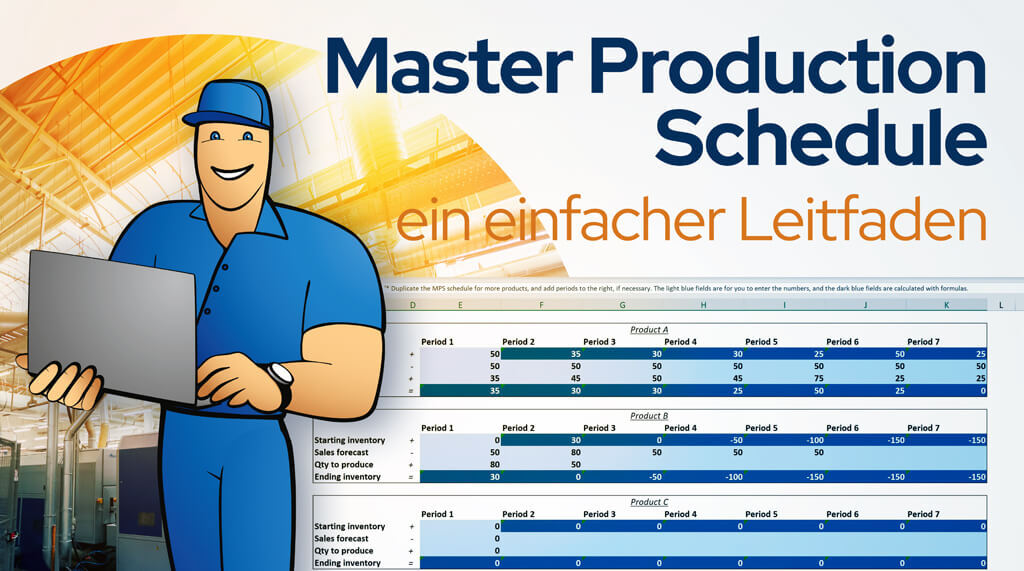
Was ist ein Master Production Schedule (MPS)?
Der Master Production Schedule (MPS) ist ein Instrument für die Produktionsplanung, das festlegt, welche Produkte in welcher Menge und zu welchem Zeitpunkt hergestellt werden müssen. Ein Master Production Schedule geht jedoch nicht im Detail auf die Produktionsvorgänge, die Reihenfolge, die den Aufgaben zugewiesenen Mitarbeiter usw. ein, sondern ist vielmehr wie ein Vertrag zwischen der Vertriebsabteilung und der Produktionsabteilung, der Angebot und Nachfrage ausgleicht, indem er die erforderlichen Mengen für die Produktion innerhalb bestimmter Zeitrahmen festlegt.
Der Master Production Schedule ist ein unverzichtbares Instrument in der Lagerfertigung, wo eine Nachfrageprognose die Produktionsplanung bestimmt. Da ein MPS häufig als Hauptantrieb für die Produktionstätigkeit verwendet wird, muss er genau und praktikabel sein, damit er sich positiv auf die Rentabilität eines Unternehmens auswirkt.
Die MPS kann auch in bestimmten Auftragsfertigungsumgebungen und bei gemischten Fertigungsverfahren eingesetzt werden, bei denen ein Unternehmen Standardprodukte herstellt. In diesem Fall werden die Absatzprognose und der Master Production Schedule meist dazu verwendet, den für die Produktion benötigten Bestand zu planen.
Ein standardmäßiger Master Production Schedule ist ein langfristiger Plan, der für jedes Produkt einzeln erstellt wird. Er wird mit einem Planungshorizont von einigen Monaten bis zu mehreren Jahren erstellt, mit einem minimalen Zeitfenster (kleinster angegebener Zeitrahmen) von 1 Woche.
Die Vorteile eines Master Production Schedule
Die Einführung eines MPS in einem Fertigungsunternehmen hat viele Vorteile:
- Er bietet eine solide Grundlage für die Erstellung, Verbesserung und Verfolgung der Absatzprognose.
- Er hilft dabei, die gewünschten Lagerbestände zu bestimmen und zu erreichen, wodurch Fehlmengen und Überbestände vermieden werden.
- Er ist ein Input für die Berechnung der Mengen an Teilen, Unterkomponenten oder Rohstoffen, die im Rahmen der nächsten Phase der Materialbedarfsplanung gekauft oder produziert werden müssen.
- Er lässt die Berechnung der benötigten Arbeitskräfte und Schichten viele Monate im Voraus zu.
- Er ermöglicht die Optimierung der installierten Kapazität und den Ausgleich der Auslastung der Anlage im Voraus, sodass Unternehmen Engpässe vermeiden können.
- Die Fertigungsabteilung kann den MPS nutzen, um die mit den Arbeitsplätzen verbundenen Produktions- und Wartungskosten abzuschätzen.
- Die Finanzabteilung des Unternehmens kann die erwarteten Einnahmen und Ausgaben aus dem MPS ableiten und eine Cashflow-Prognose erstellen. Neben anderen Vorteilen hilft dies bei der Erstellung von Investitionsplänen.
- Die Personalabteilung kann die Vorteile des MPS nutzen, um den Bedarf an Arbeitskräften vorauszusehen.
- Eine genaue MPS-Planung und -Ausführung kann den Kundenservice und die Kundenzufriedenheit erheblich verbessern, da so die Erfüllung von Aufträgen und die Aufrechterhaltung der erforderlichen Servicelevels sicherstellt werden.
- Der MPS definiert sichtbare, klare und messbare Ziele für den Geschäftsbetrieb und einen Plan, um diese zu erreichen.
Der MPS sollte den Geschäftsplan so genau wie möglich widerspiegeln. Dies erfordert eine ständige Aktualisierung durch alle Abteilungen des Unternehmens.
Wenn die Marketingabteilung beispielsweise eine Verkaufsförderungsaktion plant, muss sich der Anstieg der Nachfrage im MPS und in der Prognose widerspiegeln. Sollte das Verkaufsteam vom Verkauf einer Produktlinie zugunsten einer anderen abraten, müssen der MPS und die Prognose angepasst werden.
Wo sollte der MPS eingesetzt werden?
Obwohl Master Production Schedules am häufigsten mit Lagerfertigungsabläufen in Verbindung gebracht werden, können sie auch die Produktionsplanung in Auftragsfertigungs-, Auftragsmontage-, Serienproduktions- und kundenindividuellen Massenproduktionsumgebungen unterstützen. Hier ein kleiner Einblick, wo MPS am effektivsten eingesetzt werden kann:
1. Lagerfertigung. Bei Lagerfertigern, die Produkte auf der Grundlage von Bedarfsprognosen für den Lagerbestand herstellen, wird der MPS eingesetzt, um die Produktionspläne auf die erwartete Nachfrage abzustimmen. Durch Vorhersage der Menge der benötigten Produkte können Hersteller Überproduktionen oder Fehlbestände vermeiden, ihren Lagerbestand optimieren und Verschwendung reduzieren.
2. Auftragsfertigung. Auch in Auftragsfertigungssituationen, in denen Produkte nach Eingang eines Kundenauftrags hergestellt werden, kann der MPS nützlich sein. Es ermöglicht den Herstellern eine effiziente Kapazitäts- und Ressourcenplanung und stellt sicher, dass sie Aufträge innerhalb der zugesagten Vorlaufzeiten erfüllen können.
3. Auftragsmontate. Auftragsmonteure, die Produkte auf der Grundlage von Kundenbestellungen mit vorgefertigten Komponenten zusammenstellen, profitieren ebenfalls von einem MPS. Der Zeitplan hilft bei der Planung der Montagevorgänge und stellt sicher, dass die Komponenten bei Bedarf verfügbar sind und die Endprodukte rechtzeitig montiert werden.
4. Serienproduktion. In Umgebungen, in denen ähnliche Produkte in Gruppen oder Chargen hergestellt werden, hilft MPS bei der Bestimmung der optimalen Chargengröße und der Reihenfolge der Chargen, um die Effizienz zu maximieren und die Rüst- oder Umrüstzeiten zu minimieren.
5. Kundenindividuelle Massenproduktion. Bei der kundenindividuellen Massenproduktion (Mass customiztion) handelt es sich um eine Mischung aus Lager- und Auftragsfertigung, bei der Basisprodukte massenweise hergestellt und später entsprechend den Kundenanforderungen angepasst werden. Durch die Koordinierung der Produktion allgemeiner Komponenten mit Master Production Schedules und die anschließende Anpassung an spezifische Aufträge können Hersteller die Nachfrage effizienter bedienen.
Die Eingaben eines Master Production Schedule (MPS)
Die grundlegenden Inputs, die Sie für die Erstellung eines brauchbaren Master Production Schedules benötigen, sind die folgenden:
1. Anfangsbestand. Wie viele Einheiten der SKU sind bereits auf Lager?
2. Absatzprognose / Bedarfsplan. Wie viele Aufträge werden für diesen Zeitraum erwartet?
3. Aktueller Auftragsbestand. Wie viele Aufträge sind bereits für den Zeitraum geplant?
4. Zu produzierende Menge. Wie viele Einheiten müssen während des Zeitraums produziert werden, um Angebot und Nachfrage im Gleichgewicht zu halten?
Laden Sie eine kostenlose Vorlage für einen Master Production Schedule herunter.
Beispiel
Angenommen, Sie stellen Holzmöbel wie Stühle, Esstische und Couchtische her.
Zu Beginn des Zeitraums haben Sie 40 Stühle auf Lager. Ihre Verkaufsprognose besagt, dass Sie 200 Stühle verkaufen werden. Das bedeutet, dass Sie in diesem Zeitraum 160 Stühle produzieren müssen, um die Nachfrage zu decken.
Folglich wird Ihr Anfangsbestand in der nächsten Periode 0 sein. Da das Geschäft konstant läuft, werden weitere 200 Stuhlverkäufe prognostiziert. Das bedeutet, dass Sie nun innerhalb einer Periode 200 Stühle produzieren müssen, um die Nachfrage zu decken.

Master Production Schedule und Sicherheitsbestand
Wenn Sie das Modell der Just-in-Time-Fertigung nicht absolut perfektioniert haben, werden Sie immer eine bestimmte Menge an Einheiten als Reserve für den Fall einer unvorhersehbaren Nachfragespitze aufbewahren wollen. Aus diesem Grund können wir den Master Production Schedule mit einem Sicherheitsbestand ergänzen:
5. Sicherheitsbestand. Wie viele Einheiten möchten Sie auf Lager halten, falls es zu Nachfragespitzen kommt?
Im Master Production Schedule wird der Sicherheitsbestand als Teil des Endbestands der Periode ausgedrückt, der in die nächste Zeitperiode als Anfangsbestand übertragen wird.
Beispiel Fortsetzung.
Stellen Sie sich nun vor, dass Sie immer 40 Stühle als Sicherheitsbestand halten wollen, um das vorherige Beispiel fortzusetzen. Daher werden 160 Stühle nicht ausreichen, um die Nachfrage zu befriedigen und Ihren Sicherheitsbestand in der ersten Periode aufzufüllen. Das bedeutet, dass Sie insgesamt 200 Stühle produzieren müssen, um Ihre Kunden zufrieden zu stellen und den erforderlichen Puffer zu halten.

Erfahren Sie mehr über den Sicherheitsbestand und wie Sie ihn berechnen können.
Master Production Schedule und Grobkapazitätsplanung
Bei der Produktionsplanung müssen Sie immer berücksichtigen, wie viel genau Sie in einem bestimmten Zeitraum produzieren können. Wenn Sie Aufträge erhalten, die die Herstellung von tausend Stühlen in einem Monat erfordern, Sie aber nur die Mittel haben, 500 zu produzieren, werden Sie Ihre Kunden und Ihr Unternehmen enttäuschen. Deshalb sollten Sie immer ein Auge auf folgendes haben:
6. Produktionskapazität. Wie viele Produkte könnten Sie in diesem Zeitraum herstellen, vorausgesetzt, alles läuft reibungslos?
Die grobe Kapazitätsplanung ist ein wichtiges Instrument, das Sie neben dem Master Production Schedule einsetzen können. Um Ihre Produktionskapazität zu berechnen, müssen Sie die Durchlaufzeit Ihrer Produkte und die Gesamtproduktionsstunden in Ihrer Fertigung kennen.
Sobald Sie Ihren anfänglichen Master Production Schedule erstellt haben, können Sie seine Durchführbarkeit testen, indem Sie einen groben Kapazitätsplan auf der Grundlage des MPS erstellen. Wenn der Kapazitätsplan zeigt, dass Ihre Produktionskapazität nicht ausreicht, um das Produktionsniveau in einer der im MPS festgelegten Perioden zu erreichen, müssen Sie Wege finden, um die Kapazität zu erhöhen oder den MPS zu ändern.
Die Master Production Schedule und die Grobkapazitätsplanung sind ein wechselseitiger Prozess. Das bedeutet, dass jede Änderung in einem der beiden Bereiche eine Überprüfung des anderen erfordert.
Erfahren Sie mehr über Produktionskapazität und Grobkapazitätsplanung.
Zusätzliche Überlegungen zur MPS
Einfrieren des Master Production Schedule
Das Einfrieren des MPS bedeutet, dass die ersten paar Perioden eine bestimmte Zeit, z.B. eine oder zwei Wochen, gesperrt werden, bevor die Produktion gemäß dem Plan beginnt. Dies geschieht, um Änderungen in letzter Minute zu verhindern, die die Produktion verlangsamen und letztendlich Ihre Pläne zunichte machen könnten.
Zusicherbarer Bestand
Zusicherbarer Bestand ist die Anzahl der Einheiten, deren Auslieferung an Kunden (als feste Aufträge) Sie im aktuellen Zeitraum zusätzlich versprechen können. Sie wird gemäß dem Master Production Schedule berechnet. Dabei werden alle festen Aufträge und die geplanten Mengen über den MPS-Horizont hinweg berücksichtigt. Zusicherbarer Bestand spielt eine wichtige Rolle im Lieferkettenmanagement.
Chargenkriterien
Wenn Sie einen Master Production Schedule erstellen, sollten Sie immer Ihre Chargengrößen berücksichtigen, d.h. wie viele Produkte Sie in einem Lauf herstellen. Dies bestimmt die Stufe Ihrer Mengen. Wenn Sie z.B. in Chargen von 25 Produkten produzieren, kann Ihre zu produzierende Menge nicht 240 betragen, sondern muss 250 oder 225 betragen.
Maximaler Bestand
Das MPS ist ein hervorragendes Instrument für die Planung und die frühzeitige Vorbereitung auf Nachfrageschübe. Allerdings gibt es physische und praktische Grenzen für die Mengen, die Sie auf Lager halten können. Selbst wenn Sie über die Produktionskapazität verfügen, können Sie diese möglicherweise nicht nutzen, wenn Ihr Lager voll ist. Außerdem könnten ab einem bestimmten Lagerbestand möglicherweise zu viele Barmittel im Lager gebunden sein.
6 Tipps für die Verwaltung eines Master Production Schedules
Die Beherrschung des Master Production Schedule ist entscheidend für eine effiziente Produktionsplanung und optimierte Fertigungsprozesse. Hier sind sechs wichtige Tipps für die effektive Verwaltung eines MPS:
1. Bringen Sie Angebot und Nachfrage ins Gleichgewicht. Ein effektiver MPS stellt ein Gleichgewicht zwischen der Kundennachfrage und der Produktionskapazität her. Es ist zwar wichtig, Kundenaufträge pünktlich zu erfüllen, aber eine Überlastung Ihrer Produktionslinie kann zu erhöhten Kosten und Ineffizienz führen. Andererseits kann eine Unterauslastung der Kapazitäten zu Umsatzeinbußen und geringerer Rentabilität führen. Finden Sie das richtige Gleichgewicht auf der Grundlage Ihrer Geschäftsstrategie und der Marktbedingungen.
2. Richten Sie die MPS an den Unternehmenszielen aus. Ihr MPS sollte sich an Ihren allgemeinen Geschäftszielen orientieren. Wenn Ihr Ziel beispielsweise darin besteht, die Lagerhaltungskosten zu senken, sollte Ihr MPS so konzipiert sein, dass er just-in-time produziert, um die Nachfrage zu befriedigen. Wenn Ihr Ziel ein hoher Servicegrad ist, muss Ihr MPS möglicherweise einen Sicherheitsbestand umfassen oder auf schnelle Reaktionszeiten ausgerichtet sein.
3. Überprüfen und aktualisieren Sie regelmäßig. In der sich ständig verändernden Landschaft von Angebot und Nachfrage kann ein statischer MPS schnell veraltet sein. Überprüfen Sie Ihren MPS regelmäßig und passen Sie ihn auf der Grundlage von Echtzeit-Verkaufsdaten, Kundenbestellungen, Lagerbeständen und Lieferkettenbedingungen an, um seine Genauigkeit und Effektivität sicherzustellen. Als Faustregel gilt, dass ein MPS wöchentlich überprüft werden sollte.
4. Arbeiten Sie abteilungsübergreifend zusammen. Ein MPS wirkt sich auf mehrere Abteilungen in einem Unternehmen aus, von der Produktion über den Vertrieb bis hin zur Beschaffung. Stellen Sie sicher, dass alle relevanten Parteien an der Erstellung und Überprüfung beteiligt sind. Dieser kooperative Ansatz kann die Prognosegenauigkeit, die Ressourcenzuweisung und die allgemeine Effektivität des MPS verbessern.
5. Verwenden Sie geeignete Technologie. Setzen Sie ein ERP-System für die Fertigung ein, das einen Großteil des MPS- und Fertigungsplanungsprozesses automatisieren kann. Diese Systeme können Daten in Echtzeit bereitstellen und dazu beitragen, den Prozess zu rationalisieren, Fehler zu reduzieren und die Reaktionsfähigkeit auf Nachfrage- oder Angebotsänderungen zu verbessern.
6. Verfolgen Sie Kennzahlen und verbessern Sie sich kontinuierlich. Es gibt viele KPIs, die Sie im Auge behalten können, um die Genauigkeit und Nützlichkeit eines MPS zu beurteilen. Dazu gehören die Einhaltung und Erreichung von Zeitplänen, Lagerbestände, Kapazitätsauslastung, OTIF usw. Wenn Sie Ihre MPS-Leistung messen und mit historischen Daten vergleichen, können Sie erkennen, wann ein bestimmter Aspekt des Planungsprozesses verbessert werden muss. Vergessen Sie nicht, dass eine MPS kein Instrument ist, das Sie einmal einstellen und dann wieder vergessen. Er muss kontinuierlich verwaltet und angepasst werden, um die aktuellen Gegebenheiten widerzuspiegeln und eine optimale Produktionsleistung zu erzielen.
Master Production Schedule vs. Fertigungsressourcenplanung
Der Master Production Schedule ist einer der Ausgangspunkte für die Materialbedarfsplanung (Material Requirements Planning, MRP I) und die Fertigungsressourcenplanung (Manufacturing Resource Planning, MRP II). Zusätzlich zum MPS verwendet MRP jedoch Inputs wie Lagerbestände, Stücklisten, Arbeitspläne, Materialbedarf und -kosten, Finanzdaten, Personal- und Maschinenkapazitäten usw., um einen sehr detaillierten Plan für alle verschiedenen mit der Produktion verbundenen Ressourcen zu erstellen und Ihnen einen Echtzeit-Überblick über Ihr Unternehmen zu verschaffen, der das gesamte Betriebsmanagement und nicht nur die Produktionsplanung verbessert.
Im Gegensatz zur Erstellung eines Master Production Schedules ist die Planung der Fertigungsressourcen aufgrund ihrer Komplexität nicht manuell durchführbar. Heute gibt es viele verschiedene Softwareanbieter, die MRP-Systeme anbieten, aber viele von ihnen sind aus Buchhaltungs- oder Bestandsmanagementsoftware hervorgegangen und verfügen nur über begrenzte Möglichkeiten zur Planung von Fertigungsressourcen. Der Einsatz einer geeigneten MRP-Software wird jedoch immer wichtiger, wenn es darum geht, in der Fertigungsbranche wettbewerbsfähig zu bleiben.
MRPeasy ist eine der wenigen Cloud-basierten Lösungen, die sowohl die Funktionen der Produktionsplanung als auch der Produktionssteuerung in sich vereinen, d.h. das System unterstützt sowohl die MPS-basierte langfristige Planung als auch die kurzfristige Terminierung.
Master Scheduling Prozess innerhalb eines MRP-Systems
Sie können für die Erstellung eines einfachen Master Production Schedules zwar immer noch Excel verwenden, aber moderne MRP/ERP-Systeme für die Fertigung (oder zumindest solche mit MPS-Funktionalität) machen die Verwendung des Master Production Schedules als Grundlage für eine erweiterte Planung und Produktionssteuerung äußerst einfach. So verwendet ein MRP-System den Produktionsplan:
1. Automatisierte Dateneingabe. Die Dispositionssoftware füllt automatisch mehrere Eingaben auf der Grundlage der ihr vorliegenden Daten aus: feste Kundenaufträge, bereits eingeplante Fertigungsaufträge, Bestellungen und Anfangsbestand. Wenn sich einer dieser Werte ändert, wird der MPS automatisch aktualisiert. So erhalten die Teams in Vertrieb, Produktion und Beschaffung Echtzeitinformationen und können die notwendigen Maßnahmen ergreifen, z.B. den MPS ändern, die Kapazität erhöhen oder zusätzliche Materialien bestellen.
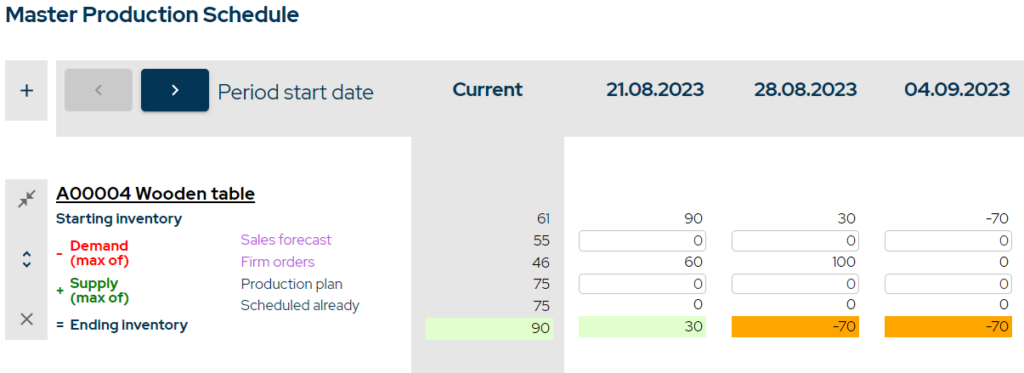
2. Bedarfsplanung. Das Vertriebsteam nutzt historische Daten und Trends, um die Nachfrage für die kommenden Perioden zu prognostizieren. Nachdem Sie die festen Kundenaufträge und die prognostizierte Nachfrage eingegeben haben, vergleicht das System diese mit den aktuellen Lagerbeständen, um die Mengen zu ermitteln, die für die Produktion in der jeweiligen Periode erforderlich sind. Dies ist der grundlegende Master Production Schedule.
Es ist wichtig zu beachten, dass die Nachfrageprognose nur so lange gültig ist, bis die festen Auftragsmengen die prognostizierte Nachfrage nicht übersteigen.
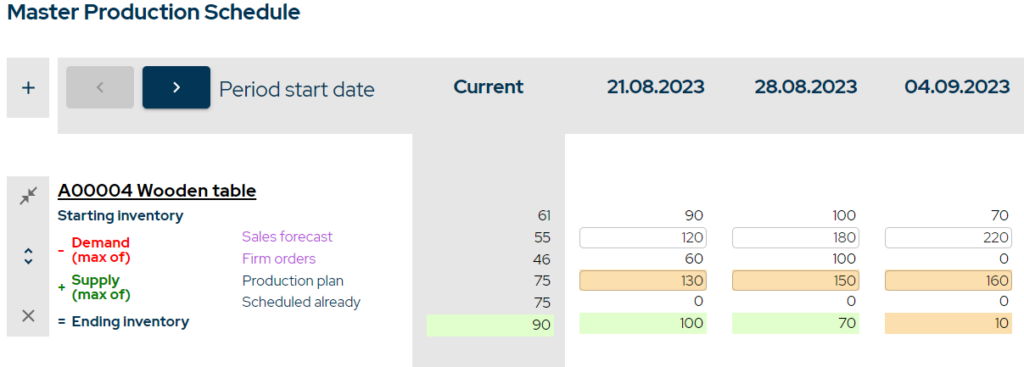
3. Kapazitätsplanung. Nachdem der grundlegende MPS erstellt wurde, kommt der Produktionsplaner ins Spiel. Das Dispositionssystem verwendet den MPS, um eine grobe Kapazitätsplanung (Rough Cut Capacity Planning, RCCP) durchzuführen. Dabei wird geprüft, ob die verfügbare Kapazität (in Form von Maschinen und Arbeitskräften) ausreicht, um den im MPS festgelegten Produktionsplan zu erfüllen. Wenn die verfügbare Kapazität nicht den Kapazitätsanforderungen entspricht, muss der Produktionsplaner den MPS anpassen oder die Produktionskapazität erhöhen, z.B. durch Hinzufügen einer Schicht.
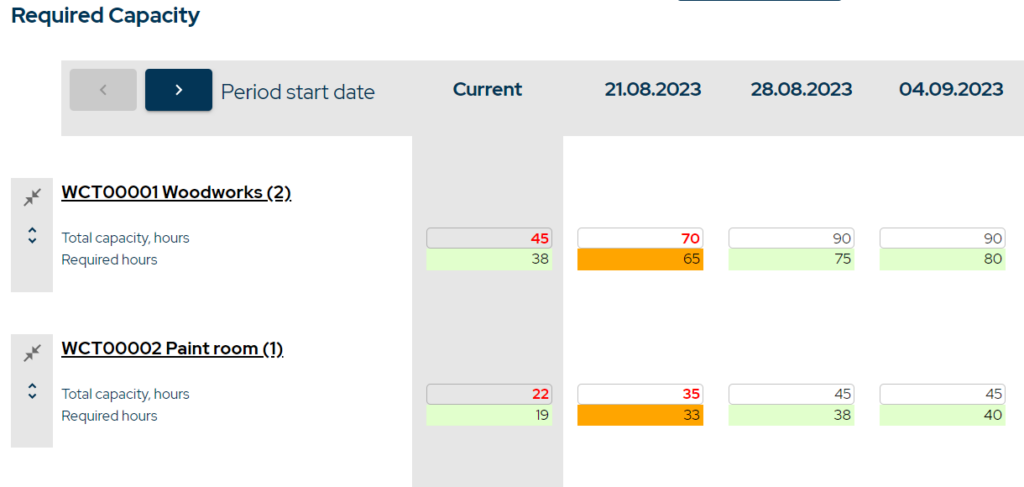
4. Beschaffungsplanung. Sobald der MPS erstellt ist, verwendet das System ihn als Input für die Berechnung des Materialbedarfs für jede Periode. Die Dispositionssoftware nimmt den Master Production Schedule und die Stückliste (BOM) für jedes Produkt sowie den aktuellen Rohmaterialbestand und berechnet die benötigten Mengen jedes Materials oder jeder Komponente und wann sie benötigt werden. Das Beschaffungsteam kann dann anhand dieses Plans sicherstellen, dass die erforderlichen Materialien rechtzeitig für die Produktion beschafft und die Lagerbestände optimiert werden.
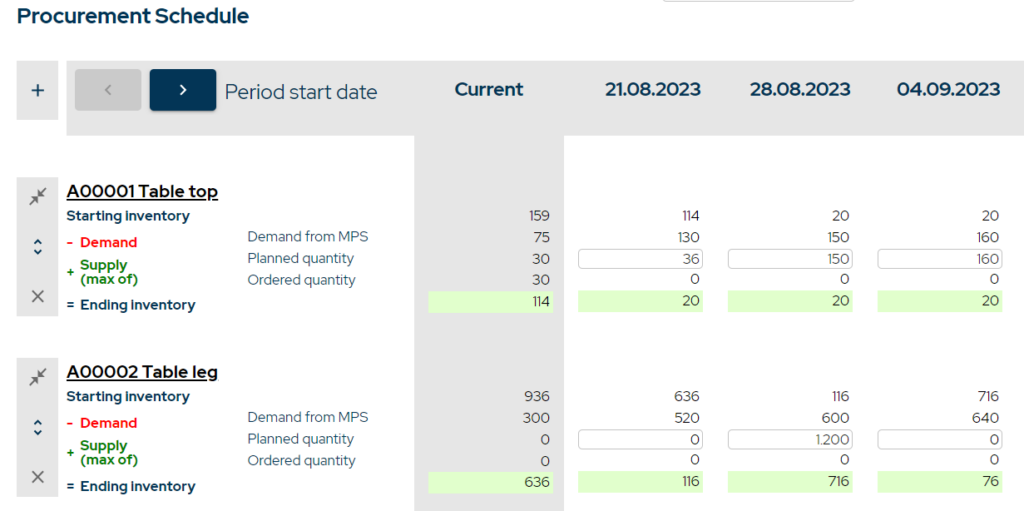
5. Produktionssteuerung. Ein MRP-System kann dazu verwendet werden, Kundenaufträge in Fertigungsaufträge umzuwandeln und diese automatisch entsprechend den verfügbaren Ressourcen oder dem Fälligkeitsdatum des Auftrags zu planen. Alternativ können Produktionsplaner manuell Fertigungsaufträge erstellen (die dann automatisch eingeplant werden), um die Produktion mit dem MPS abzustimmen.
6. Anpassungen in Echtzeit. Wie bereits erwähnt, können MRP/ERP-Systeme verwendet werden, um den MPS und die nachfolgenden Pläne in Echtzeit anzupassen, wenn sich die Bedingungen ändern, z. B. bei einem Nachfrageschub oder einer Verzögerung beim Eingang von Rohstoffen. Diese Flexibilität ermöglicht es Herstellern, schnell auf Veränderungen im Geschäftsumfeld zu reagieren, Risiken und potenzielle Verluste zu reduzieren und alle Beteiligten zu informieren und in den Prozess einzubeziehen. Es erleichtert auch die Analyse von Was-wäre-wenn-Szenarien, sodass Hersteller besser auf eine Vielzahl möglicher Situationen vorbereitet sind.
Durch die Integration des MPS in ein MRP-System können Hersteller ihren Produktionsplanungsprozess automatisieren und optimieren, die Effizienz steigern, die Kosten senken und ihre Fähigkeit, die Kundennachfrage zu erfüllen, verbessern.
Die wichtigsten Kernpunkte
- Der Master Production Schedule (MPS) ist ein Produktionsplanungsinstrument, das die Produktion mit der Nachfrage in Einklang bringt und Produkte, Mengen und Zeitpläne mit einem Planungshorizont von mehreren Monaten bis Jahren detailliert aufführt.
- Zu den Vorteilen des MPS gehören Bestandsoptimierung, Benchmarking der Prognosegenauigkeit, genaue Kapazitäts-, Arbeits- und Finanzplanung sowie eine potenziell höhere Kundenzufriedenheit.
- Obwohl der MPS meist mit der Lagerfertigung in Verbindung gebracht wird, kann er auch in der Auftragsfertigung und in gemischten Fertigungsumgebungen eingesetzt werden.
- Zu den wichtigsten Inputs des MPS gehören der aktuelle Bestand, die Nachfrageprognose, feste Kundenaufträge und Produktionsmengen. Darüber hinaus können Unternehmen Sicherheitsbestände und Produktionskapazitäten berücksichtigen.
- Zur richtigen Verwaltung von Master Production Schedules gehört es, Angebot und Nachfrage in Einklang zu bringen, die Pläne an den Unternehmenszielen auszurichten, den MPS regelmäßig zu aktualisieren, abteilungsübergreifend zusammenzuarbeiten, MPS-fähige ERP-Software zu verwenden und wichtige Kennzahlen zu verfolgen.
Häufig gestellte Fragen
Ein Master Production Schedule informiert Sie über die Menge jedes Produkts, die in jeder Periode hergestellt werden soll.
Ein Beispiel für einen Master Production Schedule wäre, dass ein Möbelhersteller 40 Stühle auf Lager hat. Die Absatzprognose besagt, dass in der Periode 200 Stühle verkauft werden. Das bedeutet, dass in dieser Periode 160 Stühle produziert werden müssen, um die Nachfrage zu decken.
Der Unterschied zwischen MRP und Master Production Schedule besteht darin, dass sich der MPS darauf konzentriert, wann und wie viel produziert werden soll, während MRP die Materialien und Ressourcen bestimmt, die zur Erfüllung des MPS erforderlich sind.
In der schlanken Produktion ist der Master Production Schedule ein rationalisierter Plan, der die Produktion auf der Grundlage der tatsächlichen Nachfrage steuert und gleichzeitig Verschwendung und Bestände minimiert.
Ihnen könnte ebenfalls gefallen: Was ist der Unterschied zwischen Produktionsplanung und Terminierung?