Was ist die Produktionskapazität und wie berechnen Sie sie?
Die Produktionskapazität ist eine wichtige Kennzahl für jeden Hersteller, der seine Produktion plant. Wenn Sie sie kennen, können Sie Ihren Kunden genauere Vorlaufzeiten bieten und den Cashflow besser prognostizieren. In diesem Beitrag gehen wir darauf ein, was die Produktionskapazität ist und wie Sie sie berechnen können.
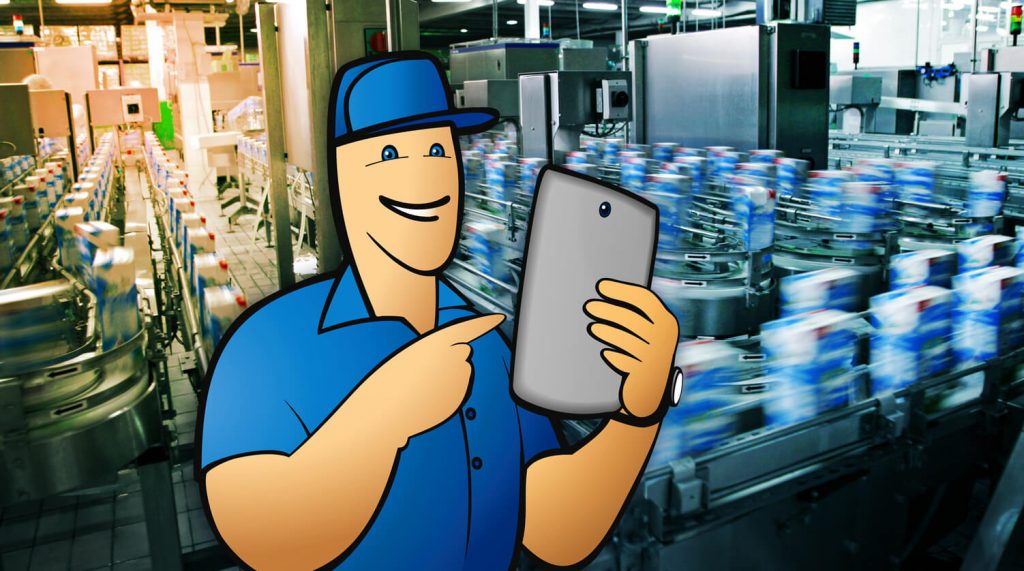
Was ist die Produktionskapazität?
Die Produktionskapazität ist der maximale Output einer Produktionsanlage, gemessen in Fertigprodukten innerhalb eines bestimmten Zeitraums. Sie zeigt den potenziellen Output, sprich die theoretische Obergrenze der Waren, die mit den vorhandenen Maschinen, Arbeitskräften und Ressourcen produziert werden können.
Die Produktionskapazität so genau wie möglich zu kennen, ist aus einer Reihe von Gründen wichtig:
- Von Herstellern wird erwartet, dass sie genaue Vorlaufzeiten angeben können. Wer sich mit groben Schätzungen zufrieden gibt, wird auf lange Sicht weniger zufriedene Kunden haben.
- Ein genauer Einblick in die Produktionskapazitäten ermöglicht eine insgesamt fundiertere Produktionssteuerung, die die Entscheidungsfindung vereinfacht und die Ungewissheit hinsichtlich der Erfüllung der Kundennachfrage mindert.
- Der Vergleich der Produktionskapazität mit der tatsächlichen Kapazität für vergangene Zeiträume ermöglicht die Messung der Kapazitätsauslastung, was nützlich ist, um die Effizienz von Fertigungsprozessen zu messen und ein Gleichgewicht zwischen Betriebsrate und Kosten pro Einheit zu finden.
- Eine verlässliche Produktionskapazitätskennzahl ist ein guter Indikator für die Leistung und dient beispielsweise dazu, die Mitarbeiter zu motivieren oder Produktionsziele zu erstellen und zu erreichen.
Es gibt verschiedene Möglichkeiten, die Produktionskapazität zu berechnen. In diesem Beitrag stellen wir Ihnen die grundlegenden Methoden vor, mit denen Sie die Produktionskapazität anhand der tatsächlichen Produktion annähern und die Produktionskapazitäten für einen oder mehrere Artikel anhand von Maschinenstunden und Durchlaufzeiten berechnen können. Wir gehen auch darauf ein, wie Produktionsplanungssoftware diesen Prozess weitgehend automatisieren und eine genaue, datenbasierte Kapazitätsplanung ermöglichen kann.
Wie berechnen Sie die Produktionskapazität?
Es gibt verschiedene Möglichkeiten, die Produktionskapazität zu ermitteln. Sehen wir uns zunächst die manuellen Berechnungsmethoden an.
Ermittlung des tatsächlichen Outputs
Die Ermittlung des tatsächlichen Outputs für eine vergangene Periode ist so einfach wie das Zählen der Anzahl der Fertigwaren für einen gewünschten Zeitraum wie eine Stunde, einen Tag, eine Woche usw. Die Ergebnisse für verschiedene Zeiträume können dann summiert und durch die Anzahl der Zeiträume geteilt werden, um die durchschnittliche Produktionskapazität für längere Zeiträume zu ermitteln.
Das ist zwar eine zuverlässige Methode, um die tatsächliche Produktion zu schätzen, aber sie gibt die Produktionskapazität nicht genau wieder. Sie berücksichtigt nur die nachgewiesene Kapazität und lässt Änderungen an Arbeitsplätzen, Arbeitsstunden, Qualifikationen der Arbeitskräfte, Angebotsschwankungen usw. unberücksichtigt. Das bedeutet, dass es keine Garantie dafür gibt, dass die tatsächliche Produktion in einem kommenden Zeitraum mit dem historischen Produktionswert übereinstimmt. Dennoch bietet die Methode eine Grundlage, die für eine Annäherung an die Produktionskapazitäten für stabile Lagerfertigungs-Workflows, die einen einfachen Produktmix mit sehr zuverlässiger Nachfrage produzieren, nützlich sein kann.
Manuelle Berechnung der Produktionskapazität
Die Berechnung der Produktionskapazität ist ein wenig komplizierter. Sie erfordert zwei Schlüsselkennzahlen – die Maschinenstundenkapazität und die Durchlaufzeit.
- Die Maschinenstundenkapazität bezieht sich auf die Gesamtzeit, die die verfügbaren Arbeitskräfte an den verfügbaren Maschinen arbeiten können, um ein Produkt herzustellen. Diese Kennzahl wird für jedes einzelne Produkt oder jeden einzelnen Prozess separat berechnet, indem die Anzahl der verfügbaren Maschinen mit den Stunden multipliziert wird, in denen die Mitarbeiter sie nutzen können.
Maschinenstundenkapazität = Anzahl der nutzbaren Maschinen x Anzahl der Arbeitsstunden
- Die Durchlaufzeit ist die gemessene Gesamtzeit, die ein Produkt für die Verarbeitung in einer Fertigungslinie benötigt. Mit anderen Worten, es handelt sich um den Teil der Gesamtproduktionszeit eines Produkts – die Gesamtzeit, die benötigt wird, um einen eingehenden Auftrag in ein fertiges Produkt umzuwandeln – der für die Bearbeitung eines Produkts aufgewendet wird. Wenn die Produktionskapazität pro einzelnem Herstellungsprozess gemessen wird, würde man dies als Zykluszeit bezeichnen. Die Zykluszeit ist die Zeit, die eine Arbeitsstation benötigt, um einen Schritt im Arbeitsablauf eines Produkts abzuschließen.
Die Division der oben genannten Metriken ermöglicht die Berechnung der grundlegenden Produktionskapazität für ein einzelnes Produkt:
Produktionskapazität für ein einzelnes Produkt = Maschinenstundenkapazität / Durchlaufzeit
Wenn zum Beispiel ein Getränkehersteller 5 Konservenmaschinen zur Verfügung hat und die Mitarbeiter in 8-Stunden-Schichten arbeiten, beträgt die Maschinenstundenkapazität für die Konservenfabrik 5h x 8h = 40h. Es dauert 6 Sekunden, um eine Getränkedose zu verarbeiten. Mit diesem Wissen können wir die Produktionskapazität für den Konservierungsprozess berechnen. Um die Berechnung zu vereinfachen, normalisieren wir beides auf Minuten: 40 Stunden sind 2.400 Minuten, und 6 Sekunden sind 0,1 Minuten. Die Produktionskapazität für den Konservierungsprozess ist also 2400 Minuten geteilt durch 0,1 Minuten pro Dose, was 24.000 Dosen pro 8-Stunden-Schicht für alle 5 Konservenmaschinen ergibt.
Produktionskapazität für mehrere Artikel
Die obige Berechnung liefert die Produktionskapazität für eine Art von Produkt oder einen einzelnen Prozess. Die meisten Betriebe stellen jedoch mehr als ein Produkt her. Um die Produktionskapazität für mehrere Produkte zu ermitteln, wird die Auftragsgröße für jedes Produkt mit seiner Durchlaufzeit multipliziert. Die Ergebnisse werden dann für die verschiedenen Produkte addiert und durch die verfügbare Maschinenstundenkapazität des Werks geteilt:
Produktionskapazität für mehrere Produkte = ((Menge von Produkt A x Durchsatz von Produkt A) + (Menge von Produkt B x Durchsatz von Produkt B)) / Maschinenstundenkapazität
Nehmen wir an, dass unsere Getränkekonservenfabrik zwei Aufträge erfüllen muss – 12.000 Dosen Limonade und 8.000 Dosen Bier – und setzen das obige Beispiel fort. Die Durchlaufzeit für die Herstellung von Limonade beträgt 6 Sekunden und für Bier 9 Sekunden. Ohne Berücksichtigung von Umrüstzeiten und anderen Einschränkungen würde die Produktionskapazität für die Arbeitslast in Minuten (12.000 x 0,1) + (8.000 x 0,15) = 1.200 + 1.200 = 2.400 Minuten oder 40 Maschinenstunden betragen. Wir wissen bereits, dass die Maschinenstundenkapazität der Konservenfabrik 2.400 Minuten pro Woche beträgt. Mit anderen Worten, die Fabrik kann unter idealen Umständen mit der installierten Kapazität beide Aufträge in einer Arbeitswoche erfüllen.
Ermittlung der Kapazitätsauslastungsrate
Sobald sowohl die Produktionskapazität als auch die tatsächliche Produktion gemessen sind, kann eine weitere wichtige Kennzahl für die Produktion berechnet werden – die Kapazitätsauslastungsrate. Diese Kennzahl zeigt, wie stark die eingerichtete Produktionskapazität eines Unternehmens ausgelastet ist, oder anders ausgedrückt, wie viel Prozent der maximalen Kapazität der Fertigungsprozess ausnutzt.
Die Kapazitätsauslastungsrate wird berechnet, indem die tatsächliche Kapazität durch die Produktionskapazität dividiert und das Ergebnis mit 100 multipliziert wird, um einen Prozentsatz zu erhalten.
Kapazitätsauslastung = (tatsächliches Produktionsniveau / Produktionskapazität) x 100%
Der Kapazitätsauslastungsgrad eignet sich hervorragend zur Beurteilung der betrieblichen Effizienz der Produktionsanlage sowie der Kosten und der Preisgestaltung der Produkte. Im Allgemeinen wird eine Kapazitätsauslastung von etwa 85% als optimal angesehen – eine höhere Auslastung kann zu geringeren Erträgen führen, da die Arbeitsplätze schneller abnutzen oder nicht in der Lage sind, auf plötzliche Nachfragespitzen zu reagieren. Im Allgemeinen gilt jedoch: Je höher die Kapazitätsauslastung, desto niedriger die Kosten pro Einheit und desto größer die Gewinnspanne.
Überlegungen zur Planung der Produktionskapazität
Um eine realistischere Vorstellung von den verfügbaren Kapazitäten zu erhalten, die mehr Einschränkungen und externe Effekte berücksichtigt, und insbesondere bei der Herstellung eines Gütermixes ist ein umfassenderer Ansatz für die Planung der Produktionskapazität erforderlich.
Je mehr Einschränkungen berücksichtigt werden können, desto genauer ist die Kennzahl der Produktionskapazität, was eine präzisere Produktionsplanung und -steuerung ermöglicht. Beispiele für Einschränkungen sind Umrüst- und Stillstandzeiten, Urlaubs- und Ferienzeiten der Mitarbeiter, Platz- und Transportprobleme sowie alle anderen Engpässe, die sich auf die Produktion auswirken.
Um einen realistischen Überblick über die Kapazität zu erhalten, muss die Produktion in die Abfolge der Arbeitsgänge, die Verfügbarkeit von Arbeitsplätzen, die Rüstzeiten, die Materialverfügbarkeit, die Vorlaufzeiten der Lieferanten sowie alle anderen Details, die den Zeitplan beeinflussen können, aufgeschlüsselt werden. Dabei ist zu bedenken, dass ein typisches Werk gleichzeitig mehrere Instanzen dieser Produktionsprozesse für eine Reihe verschiedener Produkte abwickeln muss.
Darüber hinaus ist es auch wichtig, die Effizienz der Produktionslinie zu berücksichtigen. Eine Möglichkeit hierfür ist die Messung der Gesamtanlageneffektivität (Overall Equipment Effectiveness oder OEE), die Fehlerraten, Leistungsverluste usw. berücksichtigt. Es gibt jedoch noch viele andere Methoden.
Produktionskapazität und Software zur Kapazitätsplanung
Kurz gesagt wäre es äußerst schwierig, all die oben genannten Punkte manuell zu berücksichtigen. Aus diesem Grund wurden MRP-Systeme und Kapazitätsplanungssoftware entwickelt. Diese Softwarelösungen sind in der Lage, alle verfügbaren Informationen und Einschränkungen zu berücksichtigen und zu nutzen, um Produktionskapazitäten automatisch zu berechnen und realistische Pläne auf der Grundlage realer Produktionsdaten zu erstellen. Während eine manuelle Berechnung zur Klärung kurzfristiger Pläne ausreichen mag, ermöglicht diese Art von Software auch eine genaue langfristige Kapazitätsplanung.
Fertigungssoftware ermöglicht die Definition von Arbeitsplätzen und deren Einteilung in Gruppen, wobei die individuelle Produktivität jedes einzelnen Arbeitsplatzes sowie Arbeitszeiten, Feiertage und geplante Stillstandzeiten berücksichtigt werden. Mit einem klaren Überblick über und Zugriff auf alle Arbeitspläne und aufeinanderfolgenden Prozesse, eingehende Aufträge und Materialverfügbarkeit, Engpässe und Planungskonflikte oder Doppelbuchungen lassen sich im Handumdrehen entschärfen.
All dies führt zu einer höheren Genauigkeit bei der Planung und Kostenkontrolle, zu mehr Flexibilität bei der Berücksichtigung von saisonalen Schwankungen und anderen Nachfrageschwankungen, zu weitaus genaueren Statistiken und Trends sowie zu einer insgesamt höheren langfristigen Effizienz und Vorhersagbarkeit.
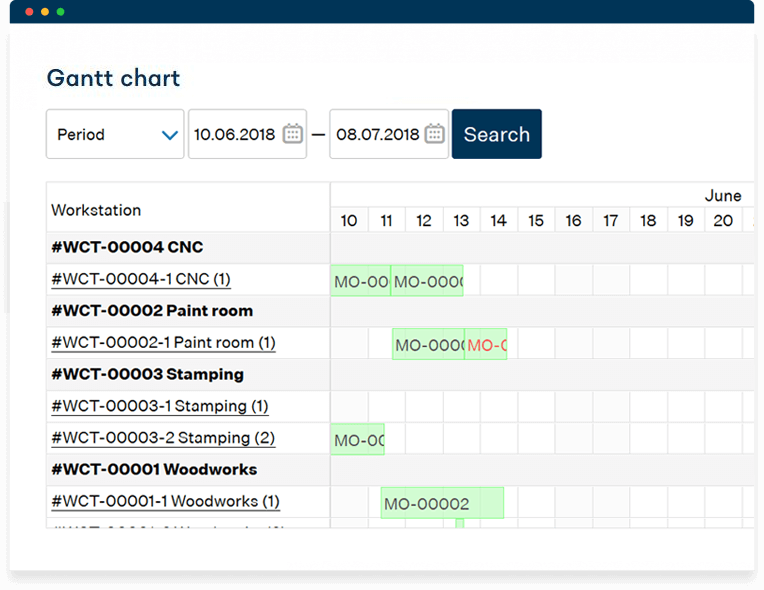
Wie lässt sich die Produktionskapazität erhöhen?
Es überrascht nicht, dass die Produktionskapazität einfach durch eine Erhöhung der Anzahl der Maschinen und zusätzliche Arbeitsschichten gesteigert werden kann. Dies ist jedoch mit zusätzlichen Kosten und Risiken verbunden, da neue Investoren gewonnen werden müssen oder eine kurz- oder langfristige Finanzierung in Betracht gezogen werden muss.
Eine valide Alternative zu den oben genannten Möglichkeiten ist die Erhöhung der Produktionskapazität durch die Nutzung vorhandener Ressourcen. Dies ist ein plausibler Ansatz für fast jedes produzierende Unternehmen, außer für solche, die bereits auf Hochtouren laufen.
Im Folgenden finden Sie einige Empfehlungen, wie Sie die Produktionskapazität erhöhen können, ohne die Produktionsfläche erweitern zu müssen.
- Optimieren Sie Ihre Fertigungsmethodik. Nutzen Sie z.B. die Prinzipien der schlanken Produktion, um Verschwendung zu beseitigen, die Engpasstheorie (Theory of Constraints, TOC), um Engpässe zu finden und zu verbessern, den Single Minute Exchange of Die (SMED), um die Umrüstzeiten zu verkürzen, usw.
- Verbessern Sie Ihre Geschäftsprozesse und planen Sie besser. Beginnen Sie zum Beispiel mit Just-in-Time (JIT), um die Produktion zu optimieren und die Gemeinkosten zu senken, beauftragen Sie einen Subunternehmer mit einer Unterbaugruppe, verbessern Sie die Kontrolle über die Lieferkette, indem Sie die Kapazitäten der Zulieferer bewerten usw.
- Führen Sie Fertigungssoftware ein. Der wahrscheinlich kostengünstigste Weg, die Produktionskapazität zu erhöhen und Ihr Werk langfristig zu optimieren, ist die Einführung einer leistungsfähigen Produktions- und Bestandsmanagementsoftware, wie z.B. ein ERP-System für die Fertigung. Die anfängliche Implementierung erfordert zwar Investitionen, aber moderne Cloud-basierte Lösungen sind zunehmend erschwinglich, ohne dass die Funktionalität darunter leidet.
Als kurzfristige Lösung können Sie die Produktionskapazität zur Bewältigung eines plötzlichen Nachfrageschubs durch folgende Maßnahmen erhöhen:
- Hinzufügen oder Verlängern von Schichten oder durch Überstunden der Mitarbeiter. Dies ist plausibel, wenn es sich um manuelle Arbeiten handelt oder wenn die Maschinen nicht bereits voll ausgelastet sind.
- Auslagerung der Produktion. Wenn Ihr Maschinenpark bereits voll ausgelastet ist und eine Kapazitätserhöhung nicht verkraften kann, kann die Auslagerung eines Teils der Arbeit ein kostengünstiges Mittel sein, um einen plötzlichen Anstieg der Nachfrage zu bewältigen.
Die wichtigsten Schlüsselpunkte
- Die Produktionskapazität ist der maximal mögliche Output eines Produktionsbetriebs, gemessen in Produktionseinheiten pro Periode.
- Die Kenntnis Ihrer Produktionskapazität ermöglicht eine bessere Planung und Terminierung der Produktion, die Angabe genauerer Vorlaufzeiten, die Berechnung der Kapazitätsauslastung, die Messung der betrieblichen Effizienz und andere Vorteile.
- Die Produktionskapazität kann anhand des durchschnittlichen Outputs vergangener Zeiträume ermittelt werden, der manuell mit Hilfe der Maschinenstundenkapazität und der Durchlaufzeit oder mit Hilfe von Software zur Planung der Produktionskapazität berechnet wird.
- Die Produktionskapazität kann langfristig durch die Anwendung von Prinzipien der schlanken Produktion, die Einführung besserer Geschäftsprozesse und die Automatisierung des Produktionsmanagements über Software oder vorübergehend durch zusätzliche Schichten oder die Auslagerung der Produktion erhöht werden.
- Der Einsatz eines ERP/MRP-Systems für das Kapazitätsmanagement ermöglicht es Unternehmen, ihre Produktion genauer und effizienter zu planen und dank besserer Datenanalysen und Erkenntnisse bessere Entscheidungen zu treffen.
Häufig gestellte Fragen
Eine einfache Möglichkeit, die Produktionskapazität zu ermitteln, ist die Multiplikation der Anzahl der verfügbaren Arbeitsplatzkapazitäten mit der verfügbaren Zeit in einer Arbeitsschicht. Wenn eine Maschine beispielsweise eine Kapazität von 10 Einheiten in einer Stunde hat und die Arbeitsschicht 8 Stunden dauert, beträgt die Produktionskapazität der Maschine 80 Einheiten pro Schicht.
Es gibt mehrere Möglichkeiten, die Produktionskapazität zu berechnen. Die einfachste Methode besteht darin, die tatsächliche Produktion von Einheiten für vergangene Zeiträume zu messen und auf dieser Grundlage eine durchschnittliche Produktionskapazität zu bestätigen. Eine fortschrittlichere Methode besteht darin, die Maschinenstundenkapazität der Anlage zu berechnen und diese durch die Durchlaufzeit eines Produkts zu dividieren. Die präziseste Methode ist jedoch der Einsatz einer Kapazitätsplanungssoftware, die Fertigungseinschränkungen und Arbeitspläne berücksichtigt und die Kapazität auf der Grundlage realer Fertigungsdaten berechnet.
Eine hohe Produktionskapazität bedeutet einfach, dass der Fertigungsbetrieb theoretisch in der Lage ist, eine große Anzahl von Produkten in einer bestimmten Zeit zu produzieren. Wenn die Produktionskapazität durch die tatsächlich gemessene Produktion geteilt und mit 100 multipliziert wird, ergibt sich eine Kapazitätsauslastung, die es ermöglicht, die Effizienz der Anlage im Vergleich zu ihrer maximalen potenziellen Kapazität zu messen.
Lesen Sie mehr über Kapazitätsplanung in ERPs für die Fertigung.