Was sind Produktionsausfälle? Wichtige Begriffe erklärt
Ungeplante Ausfälle sind mehr als nur Produktionsverluste – sie sind ein Wettlauf gegen die Zeit, um übermäßige Schäden für ein Unternehmen zu verhindern. In diesem Beitrag erkunden wir Produktionsausfälle, Möglichkeiten zu ihrer Minderung und der entscheidende Unterschied zwischen ungeplanten und geplanten Ausfällen.
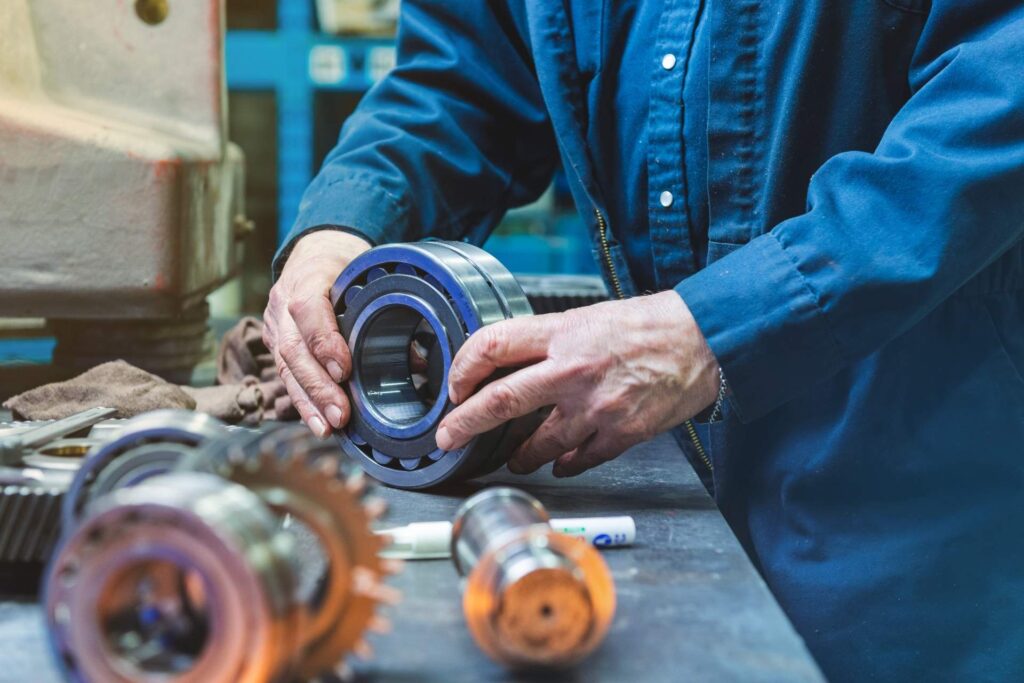
Was sind Produktionsausfälle?
Produktionsausfälle sind Zeiträume, in denen ein Fertigungsprozess unterbrochen und der normale Betriebsablauf gestört wird. Ausfälle können viele Ursachen haben, von Geräteausfällen oder Streiks der Mitarbeiter bis hin zu geplanten Wartungsarbeiten oder Unterbrechungen der Lieferkette. Unabhängig von der Ursache erschweren Ausfälle die Erreichung der Produktionsziele und gefährden somit die Kundenzufriedenheit und die Rentabilität.
Im Allgemeinen lassen sich zwei Arten von Ausfallzeiten unterscheiden: ungeplante und geplante Ausfallzeiten. Ungeplante Ausfallzeiten sind unerwartete und oft kostspielige Produktionsunterbrechungen, die durch Geräteausfälle oder andere unvorhergesehene Probleme verursacht werden. Geplante Ausfallzeiten hingegen sind eine proaktive und absichtliche Produktionsunterbrechung, die für Wartungsarbeiten oder Upgrades vorgesehen ist.
Sehen wir uns diese beiden Arten genauer an.
Ungeplante Ausfallzeiten sind das kostspielige Geräusch der Stille
Einfach ausgedrückt ist eine ungeplante Ausfallzeit ein unerwarteter oder ungeplanter Produktionsstopp, der den normalen Betrieb beeinträchtigt oder unterbricht. Für einen kleinen bis mittelgroßen Hersteller (in der Regel zwischen 10 und 200 Mitarbeitern) können die mit Ausfallzeiten verbundenen Kosten leicht lähmend werden und sich tief in die Bilanz eines Unternehmens einschneiden.
Die direkten Kosten ungeplanter Ausfallzeiten
Für einen kleinen Hersteller belaufen sich die durchschnittlichen Kosten für Produktionsausfälle auf 1.000 bis 3.000 US-Dollar pro Stunde. Bei mittelgroßen Unternehmen mit 50 bis 200 Mitarbeitern steigen diese Kosten auf 4.000 bis 10.000 US-Dollar.
Wenn man die potenziellen direkten Ausfallkosten des mittelgroßen Herstellers zugrunde legt, kann eine Ausfallzeit, die 20 bis 30 Mal pro Monat auftritt, einen beträchtlichen Teil des Gewinns in Höhe von 80.000 bis 300.000 US-Dollar kosten.
Neben den Kosten für die Maschinenreparatur sind aufgrund des Maschinenausfalls noch weitere Faktoren zu berücksichtigen. Notfallwartungen und -reparaturen kosten oft das Drei- bis Fünffache der geplanten Wartungskosten. Wenn die Teile nicht auf Lager sind, müssen die Kosten für den Expressversand von Ersatzteilen hinzugerechnet werden.
Dann kommen noch die Arbeitskosten hinzu. Jedes Mitglied des Produktionsteams, das herumsteht und nichts tut, verdient immer noch seinen Stundenlohn. Darüber hinaus muss die verlorene Produktionsleistung aufgeholt werden, was häufig zu Überstundenzuschlägen führt. Überstunden werden normalerweise mit dem 1,5-fachen des regulären Stundenlohns berechnet. Folglich sind die Arbeitskosten für jeden Artikel gestiegen.
Kurz gesagt können ungeplante Ausfallkosten zu einer enormen Rechnung führen, die sich auf die Stückkosten des Unternehmens auswirkt und zu einer niedrigeren OEE-Bewertung (Gesamtanlageneffektivität) beiträgt.
Indirekte Kosten ungeplanter Ausfallzeiten
Erstens kann es bei einem Neustart der Produktion zu Problemen bei der Qualitätskontrolle kommen. Reparaturen können die Ausrichtung und andere Messungen, die für eine präzise Steuerung verwendet werden, verändert haben. Dies bedeutet oft, dass die ersten hergestellten Teile oder verarbeiteten Produkte nicht den richtigen Spezifikationen entsprechen oder innerhalb akzeptabler Parameter liegen.
Also wandern sie auf den Müll.
Die Produktivität der Fertigung kann auch so stark beeinträchtigt werden, dass es zu Terminüberschreitungen und damit verbundenen Strafen kommen kann. Dies kann zu Unzufriedenheit bei den Kunden, Stornierungen von Aufträgen und sogar zum Verlust wichtiger Geschäftsverträge führen.
Ungeplante Geräteausfälle sind deshalb so kostspielig, weil die sofortige „Lösung“ in einer reaktiven Wartung besteht. Es handelt sich um eine reflexartige Reaktion auf ein Problem, das nicht hätte auftreten dürfen.
Nach jeder größeren ungeplanten Ausfallzeit sollte das Management eine Ursachenanalyse des Ausfalls durchführen. Eine ordnungsgemäße Ausfallzeitanalyse wird die Gründe dafür aufdecken, wie und warum es zu einem Geräteausfall kam. Alle Ergebnisse sollten dokumentiert werden, wobei den Ursachen besondere Aufmerksamkeit geschenkt und sie nachverfolgt werden sollten.
Tatsächlich sollte für jede Maschine eine fortlaufende Dokumentation vorhanden sein, die ihre Betriebs- und Leistungseffizienz verfolgt. Eine Ausfallzeitenhistorie jeder Maschine kann die Kennzahlen (Leistungskennzahlen) enthalten, die bestimmen, ob eine Maschine ersetzt werden sollte, anstatt ständig repariert zu werden.
Der eigentliche Schlüssel zur Vermeidung und Reduzierung von Ausfallzeiten ist ein proaktiver Ansatz bei der Gerätewartung. Dies reduziert die Anzahl unerwarteter Ausfallzeiten und fördert einen schlanken Fertigungsprozess.
Geplante Ausfallzeiten sind der Klang der betrieblichen Effizienz
Die Kehrseite der Maschinenwartung sind geplante Ausfallzeiten. Im Gegensatz zu ungeplanten und außerplanmäßigen Ausfallzeiten sind geplante Ausfallzeiten geplant und sogar budgetiert und Teil des normalen Fertigungsprozesses.
Es ist eine Tatsache, dass jede Fertigungsmaschine – oder prinzipiell alle Maschinen – irgendwann Verschleißerscheinungen aufweisen. Hier kommen geplante Ausfallzeiten und proaktive Wartung ins Spiel.
Es gibt zwei Hauptarten der proaktiven Wartung während Ausfallzeiten: vorbeugend und vorausschauend. Obwohl diese ähnliche Merkmale teilen, unterscheiden sie sich in bestimmten Aspekten.
Das Hauptziel ist jedoch, ungeplante Ausfallzeiten zu vermeiden und Fabriken und Verarbeitungsbetriebe mit optimaler Betriebseffizienz am Laufen zu halten. Dieses Ziel wird durch einen geplanten, gut durchdachten Wartungsplan erreicht.
Softwareprogramme, computergenerierte Planung und sogar KI (künstliche Intelligenz) spielen eine immer wichtigere Rolle im Wartungsmanagement.
Vorbeugende Wartung ist entscheidend, um Produktionsausfälle zu vermeiden
Beginnen wir mit einem kurzen Blick auf die Geschichte der Ausfallzeiten.
Vor den 1950er Jahren war die Instandhaltung in der Fertigung rein reaktiv und folgte dem einfachen Prinzip: „Was nicht kaputt ist, muss auch nicht repariert werden.“ Dieser Ansatz funktionierte, weil die Maschinen unkompliziert waren und die meisten Montagearbeiten von Hand ausgeführt wurden.
Die erste große Veränderung in der Branche fand 1901 statt, als Ransom Olds das Fließband einführte, bei dem Arbeiter an festen Stationen Autos zusammenbauten, die von Station zu Station geschoben wurden. Wie wir wissen, revolutionierte Henry Ford dieses Konzept 1913 mit seinem Fließbandsystem, das von Fleischverarbeitungsbetrieben inspiriert war. Arbeiter spezialisierten sich auf einzelne Aufgaben, was die Effizienz erheblich steigerte, obwohl die Wartung weiterhin reaktiv blieb.
Der Nachkriegsboom in der Fertigung in den 1950er Jahren führte schließlich zu einem Wandel in der Wartungsphilosophie. Mit der zunehmenden Komplexität der Produktionsmaschinen entstand die vorbeugende Wartung, um Geräteausfälle und ungeplante Ausfallzeiten zu reduzieren. Die Branche wechselte von „Repariere es nicht, wenn es nicht kaputt ist“ zu „Repariere es, bevor es kaputt geht“ und legte damit den Grundstein für moderne Wartungspraktiken.
Dies führte zum Konzept der vorbeugenden Wartung, manchmal auch als präventive Wartung bezeichnet.
Geplante Ausfallzeiten für vorbeugende Wartungsarbeiten wurden in den Produktionsplan aufgenommen. Tatsächlich integrierte MRP-Software die geplante Wartung bald direkt in die Gesamtplanentwicklung, einschließlich der Führung eines Bestandsverzeichnisses der vorrätig zu haltenden Teile.
Geplante Ausfallzeiten werden häufig für die Umrüstung und Aufrüstung von Geräten genutzt.
Ein wichtiger Bestandteil der vorbeugenden Wartung ist das Konzept der MTBF oder „Mean Time Between Failure“ (mittlere Betriebsdauer zwischen Ausfällen). Dieses Konzept wurde auf alle Arten von Ausrüstungsteilen angewendet, insbesondere auf solche, die Bewegung ermöglichten (Lager, Zahnräder und ähnliche Teile), und schließlich auf elektrische und elektronische Teile, die eine begrenzte Lebensdauer oder Lebenserwartung hatten.
Ein Hauptziel der vorbeugenden Wartung besteht also darin, diese Teile mit einem MTBF-Wert zu ersetzen, bevor sie kaputtgehen. Das bedeutet, dass Ersatz oder sogar die Generalüberholung ganzer Maschinen für Zeiten geplant wurden, in denen die Produktion nicht lief. Wochenenden, Feiertage und eine tägliche Wartungsschicht ermöglichten die Durchführung vorbeugender Wartungsarbeiten.
Das Ergebnis? Ungeplante Ausfallzeiten gingen deutlich zurück.
Viele vorbeugende Wartungsstrategien haben jedoch einen Haken. Teile werden ausgetauscht, bevor sie ausfallen … manchmal lange bevor sie ausfallen. Während das Warten auf den Ausfall eines Teils bedeutete, dass man jedes Gramm „Gut“ aus ihm herausholte, bedeuteten vorbeugende Reparaturen, dass man durch zu früh ausgemusterte Teile Geld verlor.
In den allermeisten Fällen wurde der Verlust durch den Austausch vor dem Ausfall jedoch dadurch mehr als ausgeglichen, dass keine Kosten für ungeplante Ausfallzeiten anfielen.
Ein Kompromiss, ja. Aber einer, der sich in der Regel lohnt.
Vorausschauende Wartung – Just-in-Time-Reparaturen und Ausfallzeiten verfolgen
Die vorausschauende Wartung, die in den 1990er und frühen 2000er Jahren entwickelt wurde, nutzt eine stärker datengesteuerte Methodik für die Planung von Wartungsreparaturen und reduziert so ungeplante Ausfallzeiten noch weiter. Sie nutzt vorausschauende Analysen, um unerwartete Maschinenstillstandzeiten zu vermeiden, und senkt die Kosten für Ausfallzeiten, indem sie eine effizientere Arbeitsweise ermöglicht.
Während vorbeugende Wartung im Grunde eine fundierte Vermutung war, nutzt die vorausschauende Wartung eine ganz neue Reihe von Parametern, Techniken und Technologien. Sie kann Ihre Fertigungsanlagen in Echtzeit oder so nah wie möglich daran überwachen.
Eine der Hauptursachen für Lagerprobleme bei beweglichen Teilen war und ist beispielsweise Wärme. Dasselbe gilt für elektrische und elektronische Komponenten. Eine wichtige Technologie, die ich in meiner 36-jährigen Karriere als Industriemechaniker häufig eingesetzt habe, ist die Wärmebildtechnik, auch Thermografie genannt.
FLIR ist eine Abkürzung für „Forward Looking Infrared“. Wenn Sie das Gerät auf ein Objekt richten, erfasst es die Wärme und erstellt ein farbcodiertes Bild auf einem Bildschirm. Die verschiedenen Farben geben die Temperatur des Objekts oder von Teilen davon an, die in der Regel mit der Umgebungstemperatur verglichen wird.
Wenn Sie die normale Betriebstemperatur des Bauteils kennen, können Sie sehen, ob es sich zu überhitzen beginnt, was auf einen bevorstehenden Ausfall hindeutet. Das Bauteil kann dann rechtzeitig für einen Austausch oder eine Reparatur eingeplant werden … eben gerade rechtzeitig oder „Just-in-Time“.
Fortgeschrittene vorausschauende Wartung im 21. Jahrhundert
Heute befinden wir uns im Zeitalter von Industrie 4.0+, und es steht eine ganze Reihe neuer Technologien für die vorausschauende Wartung zur Verfügung, um die Fertigungsabläufe zu verbessern. Spezialisierte Sensoren werden an Maschinenkomponenten angebracht, die rund um die Uhr als Wächter fungieren und bei potenziellen Problemen vor einem bevorstehenden Ausfall warnen.
Diese Sensoren sind oft mit dem Netzwerk oder der Wartungs-Cloud der Einrichtung verbunden und geben Daten über IoT-Verbindungen (Internet der Dinge) direkt in die Software zur Wartungsverfolgung und -planung ein. Jedes Gerät kann in Echtzeit verfolgt werden, wobei seine Leistung mit einer Reihe definierter Metriken und Betriebsparameter verglichen wird.
KI in Verbindung mit maschinellem Lernen ermöglicht eine intelligente Wartungsplanung und steuert ein Computer-Wartungsmanagementsystem oder CMMS.
Dadurch werden menschliche Fehler bei der vorausschauenden Wartung so gut wie ausgeschlossen. Wenn Wartungsteams in der Lage sind, vorausschauende Wartung durchzuführen, wird die Gesamtanlageneffektivität weiter verbessert. Und das bedeutet, dass die Ausfallzeiten aufgrund von Geräteausfällen, die zu Produktionsausfällen führen, minimiert werden.
Allerdings sind nicht alle unerwarteten Ausfallzeiten auf Geräteausfälle zurückzuführen.
Man kann nicht alle ungeplanten Ausfallzeiten herausfiltern
Aber Sie können sie reduzieren.
In meinen über 35 Jahren in der Fertigung habe ich jede erdenkliche Art von Produktionsausfall erlebt. Von kleineren Maschinenproblemen bis hin zu verheerenden Stillständen im gesamten Werk sind diese Störungen eine ständige Realität für Fertigungsunternehmen.
Hier sind einige weitere häufige Ursachen für Ausfallzeiten in der Fertigungsindustrie.
Rohstoffknappheit
Engpässe führen zu Produktionsstopps, erhöhen die Kosten durch Eilaufträge und beschädigen die Kundenbeziehungen durch Terminüberschreitungen. Diese Störungen ziehen sich durch die gesamte Lieferkette und stellen das Bestandsmanagement vor komplexe Herausforderungen, die sich auf den gesamten Betrieb auswirken.
Moderne Technologie bietet effektive Lösungen durch Echtzeit-Bestandsverfolgungssysteme und fortschrittliche Analysen für bessere Prognosen. Software für das Lieferkettenmanagement (SCM), die in ERP-Systeme (Enterprise Resource Planning) integriert ist, ermöglicht eine umfassende Bestandsüberwachung und -verwaltung.
Stücklisten-Software (BOM) stärkt die Bestandskontrolle durch automatisierte Nachbestellpunkte, RFID-Integration und präzise Materialberechnungen auf der Grundlage des Produktionsbedarfs.
Um Materialknappheit erfolgreich zu verhindern, müssen diese technologischen Hilfsmittel mit strategischer Planung kombiniert werden, einschließlich der Pflege mehrerer Lieferantenbeziehungen und der Entwicklung klarer Notfallpläne. Dieser integrierte Ansatz hilft Herstellern, eine gleichmäßige Produktion aufrechtzuerhalten und gleichzeitig das Risiko von Unterbrechungen zu minimieren.
Stromausfälle
Stromausfälle stellen ein ständiges Risiko für Produktionsanlagen dar. Sie können durch Ausfälle von Versorgungsunternehmen, elektrische Probleme oder Naturkatastrophen verursacht werden. Die Auswirkungen sind unmittelbar und schwerwiegend. Produktionslinien kommen zum Stillstand. Empfindliche Geräte können beschädigt werden. Produktionsziele und -fristen werden nicht eingehalten.
Hersteller benötigen einen mehrschichtigen Schutz vor diesen Risiken:
- Beginnen Sie mit einer robusten Infrastruktur.
- Installieren Sie Notstromaggregate und unterbrechungsfreie Stromversorgungen (USV).
- Führen Sie regelmäßige Lastbanktests durch, um die Zuverlässigkeit des Systems zu überprüfen.
- Entwickeln Sie klare Protokolle für Stromausfälle.
- Erwägen Sie redundante Stromleitungsverträge für zusätzlichen Schutz.
Moderne Überwachungssysteme bieten eine weitere wichtige Schutzschicht. Installieren Sie sowohl analoge als auch digitale softwaregesteuerte Überwachungstools. Diese verfolgen die Stromaufbereitung und das Lastmanagement. Sie können frühzeitig Warnungen ausgeben, bevor Probleme eskalieren. Hochleistungs-Industriebeleuchtungssysteme bieten zusätzliche Widerstandsfähigkeit.
Zusammen helfen diese Lösungen Herstellern, die Kontinuität auch bei Stromausfällen aufrechtzuerhalten.
Menschliches Versagen
Menschliches Versagen ist wahrscheinlich am schwierigsten zu minimieren und gefährdet täglich den Erfolg der Fertigung. Diese Fehler reichen von falscher Maschinenbedienung bis hin zu Wartungsversäumnissen. Sie können auch Fehler im Produktionsprozess umfassen. Die Auswirkungen sind erheblich. Bei Produktionslinien kommt es zu Verzögerungen oder Stillständen. Qualitätsprobleme und Verschwendung nehmen zu. Sicherheitsrisiken entstehen. Die Produktivität und Effizienz sinken insgesamt.
Hier sind einige Tipps, um menschliche Fehler zu minimieren:
- Entwickeln Sie klare und eindeutige Kommunikationssysteme, die den gesamten Arbeitsablauf stärken.
- Führen Sie umfassende Schulungsprogramme mit digitalen Arbeitsanweisungen ein. Digitale Schulungsplattformen tragen dazu bei, die Konsistenz in der Mitarbeiterschulung zu erhöhen.
- Installieren Sie bei Bedarf visuelle Hilfsmittel in mehreren Sprachen.
- Erstellen und pflegen Sie detaillierte Standardarbeitsanweisungen (SOPs).
- Strenge Maßnahmen zur Rechenschaftspflicht und regelmäßige Kompetenzbewertungen bieten weitere Schutzschichten.
Diese Tools und Prozesse helfen Herstellern, die Qualität zu erhalten und gleichzeitig ihre Belegschaft zu schützen.
Geplante vs. ungeplante Produktionsausfälle – Sie haben die Wahl
Ungeplante Produktionsausfälle treten als reaktive Wartungsarbeiten oder kostspielige Unterbrechungen auf. Geplante Ausfallzeiten dienen der Wartung der Ausrüstung und der Verbesserung von Prozessen. Sie ermöglichen eine gründliche Inspektion der Ausrüstung, wichtige Aktualisierungen und die Prozessoptimierung.
Regelmäßige Wartung verlängert die Lebensdauer der Maschinen und beugt zukünftigen Ausfällen vor. Sie erspart Ihnen stundenlange Ausfallzeiten, die sich negativ auf Ihr Betriebsergebnis auswirken. Ungeplante Ausfallzeiten hingegen stören die Produktionszeit und kosten Tausende pro Stunde.
Eine Software zur Planung von Fertigungsressourcen hilft dabei, geplante Ausfallzeiten für Wartungsarbeiten zu maximieren und gleichzeitig unerwartete Ausfälle zu verhindern. Dies steigert die Effizienz, senkt die Kosten und gewährleistet eine zuverlässige Produktion. Eine strategische Wartungsplanung führt zu höherer Produktivität, besserer Qualitätskontrolle und erheblichen langfristigen Einsparungen.
Die wichtigsten Kernpunkte
- Produktionsausfälle sind Störungen in Fertigungsprozessen, die durch Geräteausfälle, Wartungsprobleme, Probleme in der Lieferkette usw. verursacht werden können.
- Ungeplante Ausfallzeiten sind kostspielig und störend. Sie treten unerwartet auf und führen zu hohen Reparaturkosten, Produktivitätsverlusten und Terminüberschreitungen.
- Geplante Ausfallzeiten sind ein proaktiver Ansatz zur Effizienzsteigerung. Sie werden so geplant, dass Wartungsarbeiten und Upgrades möglich sind, wodurch das Risiko unerwarteter Produktionsunterbrechungen verringert wird.
- Vorbeugende Wartung reduziert ungeplante Ausfallzeiten. Durch den Austausch von Teilen und die Wartung von Geräten vor einem Ausfall wird die Lebensdauer der Maschinen verlängert und das Risiko von Störungen verringert.
- Die vorausschauende Wartung nutzt moderne datengesteuerte Technologien, um Reparaturen zu optimieren. Echtzeit-Überwachung und -Analysen helfen, Probleme frühzeitig zu erkennen und eine rechtzeitige und effiziente Wartung zu gewährleisten.
- Zu den Herausforderungen bei der Planung von Ausfallzeiten gehören Ressourcenknappheit und menschliches Versagen. Eine effektive Planung, eine angemessene Schulung und die Integration moderner technischer Lösungen sind entscheidend, um diese Hindernisse zu überwinden.
Häufig gestellte Fragen
Unter Produktionsausfall versteht man jeden Zeitraum, in dem die Fertigung unterbrochen ist. Dies kann durch ungeplante Ereignisse wie Geräteausfälle oder geplante Aktivitäten wie Wartungsarbeiten oder Upgrades verursacht werden. Ausfallzeiten wirken sich auf die Produktivität, die Kundenzufriedenheit und die Rentabilität aus und sind daher ein entscheidender Faktor für die Fertigungseffizienz.
Ja, die Ausfallzeit ist ein wichtiger Leistungsindikator (KPI) in der Fertigung. Sie wird häufig zur Messung der Gesamtanlageneffektivität und zur Bewertung der betrieblichen Effizienz verwendet. Die Überwachung von Ausfallzeiten hilft, Problembereiche zu identifizieren und Strategien zur Reduzierung von Störungen umzusetzen.
Um Produktionsausfälle zu berechnen, erfassen Sie die Gesamtdauer der Betriebsunterbrechungen während eines bestimmten Zeitraums. Teilen Sie diese durch die insgesamt verfügbare Produktionszeit und multiplizieren Sie sie dann mit 100, um sie als Prozentsatz auszudrücken. Diese Kennzahl hilft Herstellern, die Effizienz ihrer Prozesse zu bewerten und Verbesserungsmöglichkeiten zu identifizieren.
Ihnen könnte ebenfalls gefallen: Was ist veralteter Lagerbestand und wie können Sie ihn verhindern?