Plan Do Check Act – Die Umsetzung von PDCA in der Fertigung
Kontinuierliche Verbesserung ist ein wichtiger Aspekt der modernen Fertigungslandschaft. Eine der bekanntesten Methoden ist Plan-Do-Check-Act. In diesem Artikel werden die Grundsätze von PDCA, seine Vorteile und die optimale Vorgehensweise erläutert.
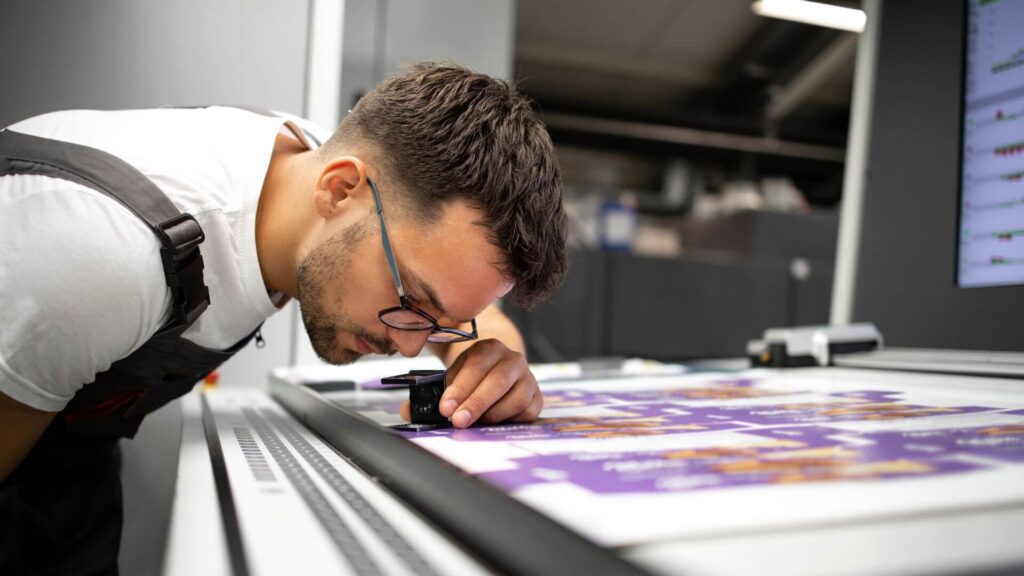
Was ist Plan-Do-Check-Act?
Plan-Do-Check-Act (zu Deutsch Planen, Tun, Prüfen, Handeln) oder PDCA ist eine vierstufige Methode zur Unternehmensführung, die auf die kontinuierliche Verbesserung des Geschäftsprozessmanagements abzielt. Manchmal auch als Plan-Do-Study-Act oder PDSA-Zyklus bezeichnet, handelt es sich um ein sich wiederholendes Modell, das einen disziplinierten, iterativen Ansatz zur Problemlösung fördert. Die vier Phasen – Plan, Do, Check, Act – bieten einen einfachen, aber effektiven Ansatz für das Veränderungsmanagement und stellen sicher, dass Ideen angemessen getestet werden, bevor sie vollständig umgesetzt werden.
PDCA geht auf Walter Shewhart zurück, einen Statistiker und Innovator im Bereich Qualitätsmanagement. Der Ökonom W. Edwards Deming machte das Modell jedoch erst richtig bekannt. Deming betonte die Bedeutung einer ständigen Interaktion zwischen Forschung, Design, Test und Produktion als Grundlage für eine kontinuierliche Verbesserung. Daher wird PDCA manchmal auch als „Deming-Zyklus“, „Deming-Rad“ oder „Shewhart-Zyklus“ bezeichnet.
Die Umsetzung des PDCA-Zyklus in der Fertigung hat mehrere Vorteile, darunter die systematische Herangehensweise an die Identifizierung und Lösung von Problemen, die verbesserte Kommunikation zwischen den Abteilungen und die Förderung einer strategischen Kultur der kontinuierlichen Verbesserung. In der sich schnell entwickelnden Fertigungsbranche hilft der PDCA-Zyklus Unternehmen, wettbewerbsfähig zu bleiben, indem er die Anpassungsfähigkeit an Veränderungen erhöht, die Effizienz verbessert und die Qualität der Produkte optimiert.
PDCA und andere Methoden zur kontinuierlichen Verbesserung
PDCA ist zwar ein bekanntes Modell zur Verbesserung von Geschäftsprozessen, doch es gibt auch andere Modelle zur kontinuierlichen Verbesserung (Continuous Improvement oder CI), die jeweils unterschiedliche Schwerpunkte und Werkzeuge haben. Hier sind vier solcher Modelle und wie sie sich von PDCA unterscheiden und mit ihm zusammenwirken:
- Kaizen ist ein japanisches CI-Modell, das die Einbeziehung aller Mitarbeiter des Unternehmens – vom Top-Management bis zu den Mitarbeitern in der Produktion – in den Fokus stellt, um sich auf kleine tägliche Qualitätsverbesserungen zu konzentrieren. Im Gegensatz zu den strukturierten Schritten in PDCA fördert Kaizen kleine Veränderungen, die im Laufe der Zeit zu großen Verbesserungen führen. Ähnlich wie PDCA ist auch Kaizen zyklisch. Es handelt sich jedoch eher um eine Denkweise oder einen Teil der Unternehmenskultur als um einen einzelnen Prozess.
- Lean Manufacturing oder schlanke Produktion ist eine fertigungsorientierte Methode, die darauf abzielt, Verschwendung in der Fertigung wie Zeitverschwendung, Ressourcenverschwendung, Verschwendung von Fähigkeiten usw. zu reduzieren und gleichzeitig die Produktivität zu steigern. Sie führt spezifische Tools wie die Wertstromanalyse ein, die dabei helfen, Verschwendung zu erkennen und zu beseitigen. Diese können gut in Verbindung mit PDCA eingesetzt werden, um spezifische Fertigungsprobleme zu erkennen und zu lösen.
- Six Sigma ist eine amerikanische Methode zur Prozessoptimierung, die in den 1980er Jahren bei Motorola entwickelt wurde und hauptsächlich auf Datenanalyse zur Qualitätsverbesserung basiert. Sie folgt einem bestimmten Ablauf, der als DMAIC (Define, Measure, Analyze, Improve, Control) bekannt ist und dazu dient, Fehler oder Engpässe in Systemprozessen zu ermitteln und zu beheben. Im Vergleich zu PDCA ist Six Sigma detaillierter und datengestützt. Die beiden Methoden können sich jedoch gegenseitig ergänzen.
- Die Ursachenanalyse ist ein Qualitätsmanagementprozess, der versucht, die Ursachen von Problemen zu finden, damit sie nicht erneut auftreten. Sie wird häufig in der Planungs- oder Überprüfungsphase des PDCA-Zyklus eingesetzt, wenn ein Problem gründlich untersucht werden muss, um herauszufinden, was schiefgelaufen ist.
Der PDCA-Prozess
Der Plan-Do-Check-Act-Zyklus schafft einen strukturierten Prozess, um Änderungen systematisch zu identifizieren und zu testen und anschließend erfolgreiche Strategien in größerem Umfang umzusetzen. Jede Phase baut auf der vorherigen auf, sodass sichergestellt ist, dass Verbesserungen auf soliden Daten und Praxistests basieren, was wiederum dazu beiträgt, Prozesse zu verfeinern und nachhaltige Produktivitätssteigerungen zu erzielen.
Lassen Sie uns die einzelnen Phasen etwas genauer betrachten.
Plan
In der Plan-Phase wird die Grundlage für mögliche Verbesserungen geschaffen. In dieser Phase identifizieren die Teams Problembereiche, die verbessert werden müssen, legen klare und konkrete Ziele fest, formulieren Hypothesen darüber, welche Änderungen zu besseren Ergebnissen führen könnten, und bestimmen die wichtigsten Leistungsindikatoren (KPIs), um die Ergebnisse des bevorstehenden PDCA-Zyklus zu messen.
In der Plan-Phase werden gründliche Recherchen und Datenerhebungen durchgeführt, um die aktuellen Prozesse zu verstehen und Ineffizienzen zu ermitteln. Anschließend werden Pläne für die Umsetzung von Lösungen entwickelt, die auf die identifizierten Probleme zugeschnitten sind, und mit Produktionskennzahlen versehen, die als Richtschnur für die nächsten Phasen dienen.
Schauen wir uns ein Beispiel an. Ein kleiner Hersteller stellt ein Problem fest: übermäßiger Materialabfall in seiner Produktionslinie. Das Team setzt sich das klare Ziel, den Abfall innerhalb von drei Monaten um 20 % zu reduzieren. Es werden Daten über den aktuellen Abfallaufkommen gesammelt, Ineffizienzen im Arbeitsablauf analysiert und die Hypothese aufgestellt, dass durch eine Anpassung der Schneidemaschinen-Einstellungen der Materialüberschuss minimiert werden könnte. Anschließend wird ein detaillierter Plan entwickelt, um diese neuen Einstellungen zu testen, einschließlich der Messung des Abfalls während des Versuchszeitraums.
Do
In der Do-Phase wird der Plan dann in einem kontrollierten, kleinen Maßstab umgesetzt, um die Wirksamkeit der vorgeschlagenen Änderungen zu testen. Diese experimentelle Phase ist entscheidend für die Risikominderung, da sie den Umfang der Umsetzung auf eine überschaubare Größe begrenzt und es so einfacher macht, die Ergebnisse zu beobachten und wertvolle Daten zu sammeln, ohne den gesamten Betrieb zu stören. Es handelt sich im Wesentlichen um einen Testlauf des Geplanten, der einen ersten Einblick in mögliche Verbesserungen bietet.
Um bei unserem Beispiel zu bleiben: Der Hersteller implementiert die neuen Einstellungen zunächst nur an einer seiner Schneidemaschinen. So können die Änderungen überwacht werden, ohne die gesamte Produktionslinie zu verändern, wodurch das Risiko minimiert wird. Während der Do-Phase verfolgt der Hersteller genau, wie viel Materialabfall die angepasste Maschine produziert, und beobachtet unvorhergesehene Probleme sowie zusätzliche Vorteile, die sich aus den neuen Einstellungen ergeben können.
Check
In der Check-Phase werden die Ergebnisse der Do-Phase im Detail analysiert. Dabei werden die gesammelten Daten aus der Testimplementierung mit den erwarteten Ergebnissen und den Ausgangswerten verglichen, um den Erfolg der Maßnahme zu bewerten. Die Check-Phase ist entscheidend, um die Wirksamkeit des Plans und die Auswirkungen der vorgenommenen Änderungen zu verstehen.
In dieser Phase können Unternehmen Unstimmigkeiten erkennen, Erkenntnisse sammeln und feststellen, ob die geplanten Verbesserungen realisiert wurden. Wenn weitere Änderungen für notwendig erachtet werden, wird der Zyklus oft wieder in die Plan-Phase zurückversetzt.
In unserem Beispiel analysiert das Team als Nächstes die im Rahmen des Pilotprojekts gesammelten Daten. Es stellt fest, dass die neuen Maschineneinstellungen den Materialabfall um 15 % reduziert haben – etwas weniger als das angestrebte Ziel, aber dennoch eine deutliche Verbesserung. Es hat sich jedoch auch ein unerwarteter Vorteil ergeben: Der Schneidevorgang an der getesteten Maschine ist jetzt 10 % schneller. Bei der Überprüfung dieser Ergebnisse stellt das Team fest, warum das Ziel nicht vollständig erreicht wurde, und kommt zu dem Schluss, dass die Verbesserung nicht weiter ausgenutzt werden kann.
Act
In der Act-Phase werden schließlich fundierte Entscheidungen auf der Grundlage der Erkenntnisse aus der Check-Phase getroffen. Wenn sich die Teständerungen als erfolgreich erweisen, konzentriert sich Act auf die Standardisierung der Verbesserungen und deren Umsetzung in größerem Umfang im gesamten Unternehmen.
Wenn die Ergebnisse nicht den Erwartungen entsprechen, dient die Act-Phase als Feedbackschleife, in der der ursprüngliche Plan auf der Grundlage der gewonnenen Erkenntnisse überarbeitet und verfeinert wird, um das Team auf den erneuten Eintritt in den PDCA-Zyklus vorzubereiten. Die Act-Phase stellt sicher, dass die Verbesserungen im Betrieb des Unternehmens verankert werden und der Zyklus der kontinuierlichen Verbesserung fortgesetzt wird.
In unserem Beispiel beschließt der Hersteller, die neuen Maschineneinstellungen aufgrund der erfolgreichen Reduzierung des Ausschusses und der gesteigerten Produktivität auf alle Schneidemaschinen zu übertragen. Er aktualisiert die Schulungsmaterialien für Maschinenbediener, um die neuen Einstellungen und Verfahren zu berücksichtigen, und plant regelmäßige Nachfassaktionen, um die breitere Umsetzung zu überwachen. Außerdem beschließt er, den PDCA-Zyklus vierteljährlich zu überprüfen, um weitere Verbesserungen zu ermitteln.
PDCA –bewährte Verfahren für Hersteller
Als Nächstes werfen wir einen Blick auf vier bewährte PDCA-Verfahren für Hersteller und Händler.
Fördern Sie funktionsübergreifende Teams
Unterschiedliche Perspektiven können zu innovativeren Lösungen führen und die Wahrscheinlichkeit erhöhen, dass potenzielle Probleme oder Verbesserungen erkannt werden. Binden Sie verschiedene Abteilungen wie Technik, Produktion, Lager, Qualitätskontrolle usw. in den PDCA-Zyklus ein. Dieser kooperative Ansatz bereichert den Planungs- und Problemlösungsprozess und erleichtert die Akzeptanz und Umsetzung im gesamten Unternehmen.
Definieren Sie Ziele und Kennzahlen klar
Klare und verständliche Ziele und konkrete Kennzahlen sind unerlässlich, um die Auswirkungen Ihrer Maßnahmen im PDCA-Zyklus zu messen und die Ausrichtung an Ihren übergeordneten Unternehmenszielen sicherzustellen.
Legen Sie zu Beginn der Planungsphase spezifische, messbare, erreichbare, relevante und zeitgebundene, sprich SMART-Ziele fest. Bestimmen Sie, welche KPIs Sie den Erfolg am effizientesten messen lassen, und verfolgen Sie diese KPIs während des gesamten PDCA-Zyklus, um den Fortschritt und die Wirksamkeit der umgesetzten Änderungen zu bewerten. Die konsequente Dokumentation der Ergebnisse ist ebenfalls unerlässlich.
Beziehen Sie Mitarbeiter ein und schulen Sie sie
Wenn Sie Teammitglieder auf allen Ebenen in den PDCA-Prozess einbinden und schulen, können sie zur Effizienz des Verbesserungszyklus beitragen. Wenn Mitarbeiter verstehen, wie ihre Handlungen die Unternehmensleistung beeinflussen können, sind sie eher bereit, Verantwortung für ihre Aufgaben zu übernehmen und sich aktiv an der Problemlösung und Prozessoptimierung zu beteiligen.
Tipps zur Mitarbeitermotivation:
- Entwickeln Sie Schulungsprogramme, die die Grundlagen des PDCA-Zyklus und seine Bedeutung für die Unternehmensziele erläutern.
- Verwenden Sie Beispiele aus der Praxis, um zu veranschaulichen, wie jede Phase des Zyklus funktioniert und welche Auswirkungen sie hat.
- Beziehen Sie die Mitarbeiter in jeden PDCA-Zyklus ein, indem Sie ihnen spezifische Rollen zuweisen, die auf ihren Fachkenntnissen und Interessen basieren.
Überprüfen und passen Sie den Zyklus regelmäßig an
Marktbedingungen, Technologien und interne Geschäftsabläufe entwickeln sich ständig weiter. Daher sollte auch der PDCA-Zyklus regelmäßig überprüft und angepasst werden, um seine Wirksamkeit zu erhalten.
Planen Sie regelmäßige Überprüfungen Ihrer PDCA-Prozesse ein, um deren Effektivität und Relevanz im aktuellen Geschäftsumfeld zu untersuchen. Aktualisieren Sie Ihre Ansätze und Strategien als Reaktion auf neue Erkenntnisse und Veränderungen in der Branche, um sicherzustellen, dass das PDCA-Modell weiterhin sinnvolle Verbesserungen bewirkt.
Wie kann Fertigungssoftware zu kontinuierlichen Verbesserungen beitragen?
Fertigungssoftware kann eine entscheidende Rolle bei der Förderung eines Umfelds der kontinuierlichen Verbesserung in industriellen Betrieben spielen. Durch die Integration einer einheitlichen Softwarelösung können Hersteller ihre Prozesse optimieren, die abteilungsübergreifende Kommunikation verbessern, Fehler reduzieren und einheitlichere Qualitätsstandards aufrechterhalten. Schauen wir uns einige Möglichkeiten an, wie Fertigungssoftware Ihre Bemühungen um kontinuierliche Verbesserung effektiv unterstützen kann.
Verbesserte Datenerfassung und -analyse
Fertigungssoftware automatisiert die Erfassung und Analyse wichtiger Daten aus verschiedenen Phasen des Produktionsprozesses. So erhalten Sie Live-Dashboards für Leistungskennzahlen und Echtzeitinformationen zu Produktionsengpässen und Wartungsbedarf. Durch den Zugriff auf genaue und aktuelle Daten können Unternehmen Verbesserungsbereiche identifizieren, potenzielle Probleme vorhersagen, bevor sie auftreten, und schneller bessere Entscheidungen treffen.
Rückverfolgbarkeit und Einhaltung von Vorschriften
Fertigungssoftware verbessert die Rückverfolgbarkeit erheblich und unterstützt die Einhaltung strenger behördlicher Auflagen. Durch die detaillierte Aufzeichnung des gesamten Fertigungsprozesses – von den Rohstoffen bis hin zu den fertigen Produkten – stellen MRP-Systeme sicher, dass jede Komponente in jeder Produktionsphase nachverfolgt werden kann. Diese Rückverfolgbarkeit ist entscheidend, um Fehlerquellen zu ermitteln, die Auswirkungen von Prozessänderungen zu überwachen und zu gewährleisten, dass alle Produkte den Qualitätsstandards entsprechen.
Standardisierung von Prozessen
Einer der Hauptvorteile einer gut implementierten Fertigungssoftware ist ihre Fähigkeit, die Abläufe in der gesamten Produktion zu standardisieren. Standardisierung ist entscheidend, um Schwankungen in der Produktqualität und der Produktionseffizienz zu beseitigen. Durch einheitliche Prozesse lassen sich Abweichungen leichter erkennen und korrigieren, was zu einer höheren Qualität und einer zuverlässigeren Produktion führt.
Erleichterung der Kommunikation
Eine effektive Kommunikation ist für kontinuierliche Verbesserungsprozesse von entscheidender Bedeutung. Fertigungssoftware verbessert die Kommunikation und das Personalmanagement, indem sie eine einheitliche Plattform für den Informationsaustausch zwischen verschiedenen Abteilungen bereitstellt. Aktualisierungen, Änderungen und Feedback können schnell und klar weitergegeben werden, sodass alle Teammitglieder auf dem gleichen Stand sind und umgehend auf neue Informationen oder Anpassungen im Produktionszyklus reagieren können.
Unterstützung proaktiver Wartung
Fertigungssoftware enthält Tools zur Überwachung der Leistung von Maschinen und Anlagen, die bei der Umsetzung proaktiver Wartungsstrategien helfen. Durch die Vorhersage von Wartungsbedarf, bevor es zu Ausfallzeiten kommt, können Hersteller einen reibungslosen Betrieb gewährleisten und Unterbrechungen vermeiden, die sich auf Produktivität und Qualität auswirken könnten. Dieser proaktive Ansatz ist ein wesentlicher Bestandteil der Check- und Act-Phasen des PDCA-Zyklus, in denen fortlaufende Anpassungen vorgenommen werden, um eine optimale Leistung zu gewährleisten.
Die wichtigsten Kernpunkte
- Der PDCA-Zyklus ist ein zyklischer, vierstufiger Ansatz zur kontinuierlichen Verbesserung, der Fertigungsunternehmen dabei unterstützt, Probleme systematisch anzugehen und zu lösen, um die Produktivität und Produktqualität zu steigern.
- Der Plan-Do-Check-Act-Zyklus ist wichtig für die Aufrechterhaltung der Wettbewerbsfähigkeit in der Fertigungsindustrie, indem er die Anpassungsfähigkeit und kontinuierliche Verbesserung von Prozessen fördert.
- Der PDCA-Zyklus besteht aus den folgenden Schritten: Planung zur Identifizierung und Bewertung von Problemen, Durchführung kleinerer Versuche mit potenziellen Lösungen, Überprüfung der Ergebnisse anhand der erwarteten Ergebnisse und Umsetzung erfolgreicher Änderungen in großem Umfang oder Verfeinerung des Plans und erneute Prüfung.
- Zu den bewährten Verfahren des PDCA-Zyklus für Hersteller gehören der Beginn mit kleinen, überschaubaren Projekten, die klare Definition von Zielen und Messgrößen, die Einbeziehung und Schulung von Mitarbeitern auf allen Ebenen sowie die regelmäßige Überprüfung und Anpassung des Zyklus an sich verändernde Marktbedingungen und interne betriebliche Veränderungen.
Häufig gestellte Fragen
Kleine Hersteller können die finanziellen Auswirkungen des PDCA-Zyklus bewerten, indem sie bestimmte Kennzahlen vor und nach den vorgenommenen Änderungen verfolgen. Wichtige Leistungsindikatoren wie Produktionskosten, Abfallreduzierung, Markteinführungszeit und Produktqualitätsmängel können analysiert werden, um Kosteneinsparungen und Umsatzsteigerungen zu ermitteln. Darüber hinaus können Vorher-Nachher-Analysen von Pilotprojekten ein klares Bild der finanziellen Vorteile vermitteln.
Zu den häufigsten Herausforderungen für kleine Hersteller gehören begrenzte Ressourcen für umfangreiche Tests und die mangelnde Bereitschaft, etablierte Prozesse zu ändern. Um diese Probleme zu überwinden, können Hersteller mit kleinen Pilotprojekten beginnen, um die Wirksamkeit des PDCA-Zyklus zu demonstrieren, ohne dass dafür im Vorfeld umfangreiche Ressourcen erforderlich sind. Durch Schulungen und eine klare Kommunikation über die Vorteile des PDCA-Zyklus können auch die Mitarbeiter eingebunden werden, um Widerstände gegen Veränderungen abzubauen.
Der PDCA-Zyklus kann in bestehende ERP-Systeme oder andere von kleinen Herstellern verwendete Technologielösungen integriert werden. Die meisten modernen Fertigungssoftwares unterstützen die Datenerfassung und -analyse, die für die Check-Phase des PDCA-Zyklus von entscheidender Bedeutung sind. Hersteller können diese Tools nutzen, um die Datenerfassung und -analyse zu automatisieren, PDCA-Aktivitäten mit anderen betrieblichen Prozessen abzustimmen und sicherzustellen, dass Verbesserungen auf genauen und aktuellen Daten basieren.
Ihnen könnte ebenfalls gefallen: Was ist Poka Yoke und wie kann es in der Fertigung eingesetzt werden?