Die 15 wichtigsten Lean-Manufacturing-Tools im Jahr 2025
Lean-Manufacturing-Tools lassen Sie Arbeitsbereiche organisieren und Probleme beheben, bevor sie Sie ausbremsen. Mit diesen Tools können Sie Kosten senken, die Qualitätskontrolle verbessern und Ihren Kunden genau das bieten, was sie wollen.
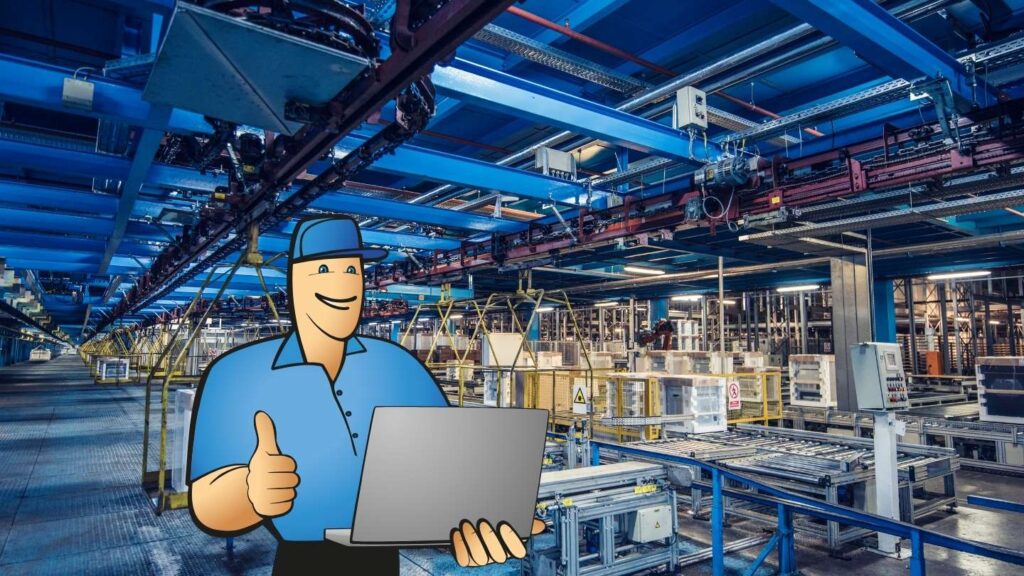
Was ist Lean Manufacturing?
Bei Lean Manufacturing oder der schlanken Produktion geht es darum, intelligenter und nicht härter zu arbeiten. Im Kern möchte sie Verschwendung reduzieren und sich nur auf das konzentrieren, was für Ihre Kunden einen Mehrwert schafft.
Die schlanke Produktion basiert auf fünf Grundprinzipien, die jeden Schritt des Prozesses leiten. Es beginnt mit der Definition des Wertes, sprich der Konzentration auf das, was den Kunden wirklich wichtig ist, und der Gewährleistung, dass jede Maßnahme zu ihrer Zufriedenheit führt. Als Nächstes erstellen die Hersteller eine Prozesskarte, indem sie jeden Produktionsschritt analysieren, um festzustellen, wo Ressourcen verschwendet werden. Sobald Ineffizienzen identifiziert wurden, besteht das Ziel darin, die Arbeitsabläufe so zu optimieren, dass alles reibungslos und ohne unnötige Unterbrechungen abläuft. Lean legt auch Wert auf die Einrichtung eines Pull-Systems, sodass nur das produziert wird, was benötigt wird, wenn es benötigt wird, anstatt Lagerbestände anzuhäufen.
Lean ermutigt Teams, ständig nach Verbesserungsmöglichkeiten zu suchen. Egal wie effizient ein Prozess wird, es gibt immer Raum für Verbesserungen.
Die Arten von Tools für die schlanke Produktion
Lean Manufacturing stützt sich auf eine Vielzahl von Tools, um Betriebsabläufe zu optimieren, Verschwendung zu beseitigen und die Produktivität zu verbessern. Diese Tools lassen sich in vier Hauptkategorien einteilen, von denen jede eine einzigartige Rolle bei der Erreichung der Ziele von Lean spielt.
1. Visuelle Hilfsmittel
Visuelle Hilfsmittel sind für die Schaffung von Klarheit in der schlanken Produktion unerlässlich. Sie vereinfachen komplexe Prozesse und erleichtern es Teams, Fortschritte zu verfolgen, Probleme zu erkennen und schnell zu reagieren. Zu den gängigen Beispielen gehören visuelle Tafeln, Kanban-Karten und andere Signalsysteme. Diese Hilfsmittel ermöglichen es den Mitarbeitern, den Status der Produktion auf einen Blick zu erkennen und Daten ohne langwierige Erklärungen zugänglich zu machen. Durch das Hervorheben von Abweichungen und die Bereitstellung umsetzbarer Erkenntnisse ermöglichen visuelle Hilfsmittel es den Teams, die Produktionsziele im Auge zu behalten und gleichzeitig eine Kultur der kontinuierlichen Verbesserung aufrechtzuerhalten.
2. Problemlösungstools
Problemlösungstools in der schlanken Produktion konzentrieren sich darauf, die Ursachen von Ineffizienzen zu identifizieren und sie systematisch zu beseitigen. Methoden wie die Ursachenanalyse und PDCA-Zyklen werden häufig eingesetzt, um Probleme zu analysieren und zugrunde liegende Probleme aufzudecken. Diese Problemlösungstechniken fördern eine proaktive Denkweise und ermutigen Teams, Herausforderungen frühzeitig anzugehen, Störungen zu minimieren und eine gleichbleibende Qualität im gesamten Betrieb sicherzustellen.
3. Prozessoptimierungstools
Prozessoptimierungstools in der schlanken Produktion konzentrieren sich auf die Verfeinerung von Arbeitsabläufen, um Ineffizienzen zu beseitigen und die Produktivität zu steigern. 5S organisiert und standardisiert beispielsweise Arbeitsbereiche und schafft so eine effiziente und visuell überschaubare Umgebung. In ähnlicher Weise fördert Kaizen die kontinuierliche Verbesserung, indem es kleine, schrittweise Veränderungen anregt, die im Laufe der Zeit zu erheblichen Gewinnen führen. Ein weiteres wichtiges Instrument, Just-in-Time (JIT), minimiert Verschwendung, indem nur das produziert wird, was benötigt wird, und zwar dann, wenn es benötigt wird, wodurch die Produktion eng an die Nachfrage angepasst wird. Diese Methoden optimieren nicht nur die Betriebsabläufe, sondern fördern auch eine Kultur der proaktiven Problemlösung und nachhaltigen Effizienz.
4. Software
Softwarelösungen für die schlanke Produktion bieten eine digitale Plattform für die Verwaltung und Verbesserung von Prozessen. Zu diesen Tools gehören ERP-Systeme für die Fertigung, Manufacturing Execution Systems (MES) und Lean-spezifische Software wie eKanban-Plattformen. Durch die Echtzeit-Datenanalyse, -Verfolgung und -Berichterstattung ermöglicht diese Software eine bessere Entscheidungsfindung und Ressourcenzuweisung. Automatisierung und vorausschauende Analysen verbessern die Produktionsplanung, die Bestandskontrolle und die Wartungsplanung. Die Integration von Software in Lean-Praktiken gewährleistet eine höhere Genauigkeit, Skalierbarkeit und Anpassungsfähigkeit, um den sich ändernden Anforderungen gerecht zu werden.
Die 15 wichtigsten Tools für die schlanke Produktion
Visuelle Hilfsmittel
1. Kanban
Kanban ist ein Lean-Planungssystem, das durch die Visualisierung von Aufgaben die Verwaltung von Arbeitsabläufen unterstützt und Überproduktion vermeidet. Dieses Tool verwendet Karten oder digitale Signale, um anzuzeigen, wann Bestände oder Aufgaben aufgefüllt oder zum nächsten Schritt weitergeleitet werden müssen. Auf diese Weise wird die Arbeit nur dann fortgesetzt, wenn eine Kundennachfrage besteht.
Für die Einrichtung eines Kanban-Systems muss eine visuelle Tafel mit Spalten erstellt werden, die verschiedene Phasen eines Prozesses darstellen, z. B. „Zu erledigen“, „In Bearbeitung“ und „Erledigt“. Jede Aufgabe oder jeder Lagerartikel wird durch eine Karte dargestellt, die sich im Laufe des Prozesses durch die Spalten bewegt. Dieses visuelle System hilft Teams, Engpässe schnell zu erkennen, Ressourcen zu verwalten und auf sich ändernde Anforderungen zu reagieren.
2. Andon
Andon ist ein Echtzeit-Warnsystem, das es Teams ermöglicht, Probleme sofort zu beheben. Ursprünglich von Toyota entwickelt, verwendet Andon visuelle Signale wie Lichter, Bildschirme oder Töne, um Mitarbeiter zu benachrichtigen, wenn im Produktionsprozess etwas schief geht. Beispielsweise kann ein Mitarbeiter an einer Andon-Schnur ziehen oder einen Knopf drücken, um einen Defekt oder eine Fehlfunktion der Ausrüstung zu melden.
Zur Implementierung eines Andon-Systems gehört die Einrichtung klarer Kommunikationsprotokolle und die Sicherstellung, dass alle Teammitglieder verstehen, wie sie das System effektiv nutzen können.
3. Wertstromanalyse (VSM)
Die Wertstromanalyse (Value Stream Mapping, VSM) ist ein visuelles Lean-Management-Tool, mit dem jeder Schritt in einem Prozess abgebildet wird, um Verschwendung in der gesamten Lieferkette zu identifizieren und zu beseitigen. Die ebenfalls von Toyota entwickelte VSM liefert ein klares Bild davon, wie der Wert durch einen Prozess fließt, und hebt die Zykluszeit und die Vorlaufzeiten in jedem Schritt hervor, um zu zeigen, wo Zeit, Ressourcen und Materialien verschwendet werden.
VSM ist ein wichtiger Bestandteil von Lean-Methoden, um Muda (das japanische Wort für „Verschwendung“ und ein zentrales Konzept im Toyota-Produktionssystem) zu ermitteln.
Erstellen Sie eine Wertstromanalyse, indem Sie Teammitglieder direkt einbeziehen. Stellen Sie jeden Schritt in der Reihenfolge dar und verwenden Sie Flussdiagramme, um zu visualisieren, wo Prozessverbesserungen die größte Wirkung erzielen können.
Problemlösungstools
Jede Herausforderung ist eine Chance, sich zu verbessern. Mithilfe von Lean-Problemlösungstools können Teams die tatsächlichen Ursachen hinter den Problemen aufdecken und dauerhafte Lösungen umsetzen. Mit diesen Werkzeugen können Hersteller Rückschläge in Fortschritt umwandeln und eine Kultur der kontinuierlichen Verbesserung schaffen.
4. Ursachenanalyse (Root Cause Analysis, RCA)
Die Ursachenanalyse (Root Cause Analysis, RCA) ist eine Methode, die dazu dient, die grundlegende Ursache eines Problems zu ermitteln und zu beseitigen, um ein erneutes Auftreten zu verhindern. Im Gegensatz zu schnellen Lösungen geht die RCA tiefer, um zu verstehen, warum ein Problem überhaupt erst aufgetreten ist. Die RCA wird oft zusammen mit Werkzeugen wie den „5 Whys“ eingesetzt, bei denen man wiederholt „Warum?“ fragt, bis man die Grundursache erreicht hat. Dieser Ansatz ermöglicht es Teams, das Problem an seiner Wurzel anzugehen, anstatt nur die Symptome zu behandeln.
Um eine RCA durchzuführen, identifizieren Sie das Problem und finden Sie alles über den Vorfall heraus, was Sie können. Verwenden Sie dann die „5 Whys“, um das Problem bis zu seinem Ursprung zurückzuverfolgen. Sobald die Grundursache gefunden ist, implementieren Sie eine Lösung, die direkt darauf eingeht, und überwachen Sie die Ergebnisse.
5. Plan-Do-Check-Act (PDCA)
Der auch als Deming-Zyklus bezeichnete Plan-Do-Check-Act (PDCA) ist ein Zyklus zur kontinuierlichen Verbesserung, der einen strukturierten Ansatz zur Problemlösung und Prozessverbesserung bietet. Die vier Schritte Plan, Do, Check und Act führen Teams durch das Testen von Änderungen, die Überprüfung der Ergebnisse und das Vornehmen von Anpassungen. PDCA fördert das Lernen durch kleine, schrittweise Änderungen.
PDCA beginnt mit dem Schritt Planen (Plan). Hier identifizieren Sie ein Problem und entwickeln einen Verbesserungsplan. Im Schritt Ausführen (Do) setzen Sie den Plan in kleinem Maßstab um. Der nächste Schritt ist das Überprüfen (Check), bei dem die Ergebnisse gemessen und mit den erwarteten Ergebnissen verglichen werden. Schließlich handeln (Act) Sie auf der Grundlage der Ergebnisse. Wenn die Änderung erfolgreich ist, setzen Sie sie flächendeckend um. Wenn nicht, überarbeiten Sie den Zyklus und wiederholen Sie ihn.
Tools und Methoden zur Prozessoptimierung
Die Optimierung von Arbeitsabläufen und die Beseitigung von Verschwendung stehen im Mittelpunkt der schlanken Produktion, und Prozessoptimierungstools machen dies möglich. Diese Tools konzentrieren sich auf die Verbesserung der Effizienz, die Reduzierung von Fehlern und die Maximierung der Produktivität durch die Verfeinerung der Arbeitsabläufe.
6. 5S
5S ist eines der grundlegendsten Lean-Tools, das in Japan als Teil des Toyota-Produktionssystems entwickelt wurde. Es handelt sich um eine einfache, aber wirkungsvolle Methode zur Schaffung eines organisierten, sauberen und effizienten Arbeitsplatzes mit klarem visuellem Management zur Unterstützung jedes einzelnen Schritts.
Die „5S“ stehen für fünf japanische Wörter, die sich mit Sortieren (Seiri), Ordnung schaffen (Seiton), Sauberkeit (Seiso), Standardisierung (Seiketsu) und Aufrechterhaltung (Shitsuke) übersetzen lassen. Jedes „S“ steht für einen Schritt beim Aufbau eines effizienten, ordentlichen Arbeitsbereichs, der sich leicht verwalten und pflegen lässt.
Beim ersten Schritt, dem Sortieren, geht es darum, Unordnung aus dem Arbeitsbereich zu entfernen. Als Nächstes bedeutet Ordnung schaffen, Werkzeuge und Materialien so anzuordnen, dass der Arbeitsablauf unterstützt wird. Beim Saubermachen wird der Bereich gründlich gereinigt, damit er sicher und effizient ist. Durch Standardisierung wird sichergestellt, dass alle die gleichen Schritte befolgen, um den Arbeitsbereich organisiert und sauber zu halten. Schließlich sorgt die Aufrechterhaltung dafür, dass das System durch regelmäßige Kontrollen und Verbesserungen auf Dauer erhalten bleibt.
Um 5S umzusetzen, beginnen Sie damit, das gesamte Team in den Sortier- und Organisationsprozess einzubeziehen. Dadurch entsteht ein geteiltes Gefühl der Eigenverantwortung und der Verantwortung für die Instandhaltung des Bereichs. Regelmäßige Audits können dazu beitragen, sicherzustellen, dass jeder Schritt von 5S weiterhin befolgt wird.
7. Kaizen
Kaizen (was auf Japanisch „kontinuierliche Verbesserung“ bedeutet) wurde als Teil des Fertigungsansatzes von Toyota entwickelt und ist ein Lean-Tool, das die Prozessverbesserung durch kleine Anpassungen in Echtzeit fördert. Die Idee ist einfach: Kleine Anpassungen im Laufe der Zeit führen zu großen Verbesserungen in Bezug auf Qualität, Produktivität und Effizienz.
Dieser Ansatz befasst sich mit Problemen wie Überbearbeitung und Verzögerungen in der Produktionslinie und treibt so kontinuierliche Verbesserungen voran. Die Effektivität von Kaizen kann anhand von Kennzahlen gemessen werden. Im Laufe der Zeit baut Kaizen ein proaktives Team auf, das sich für die Total Productive Maintenance (TPM) einsetzt, die darauf abzielt, Ausfälle zu minimieren.
Zur Umsetzung von Kaizen schaffen Unternehmen eine Umgebung, in der Teammitglieder auf allen Ebenen Verbesserungsvorschläge einbringen können. Dies kann alles Mögliche bedeuten, von der Anpassung des Layouts eines Arbeitsplatzes bis hin zur Suche nach einer schnelleren Möglichkeit, eine sich wiederholende Aufgabe zu erledigen.
Zu den besten Kaizen-Praktiken gehören regelmäßige Treffen, die oft als „Kaizen-Events“ oder „Blitz-Meetings“ bezeichnet werden, bei denen Mitarbeiter Verbesserungen vorschlagen und Probleme besprechen, die sich direkt auf ihre Arbeit auswirken. Im Laufe der Zeit baut Kaizen ein proaktives, engagiertes Team auf, das ständig nach Verbesserungsmöglichkeiten sucht.
8. Just-in-Time (JIT)
Just-in-Time (JIT) stammt aus dem Fertigungssystem von Toyota und reduziert die Überproduktion, indem nur das produziert wird, was benötigt wird, und zwar dann, wenn es benötigt wird. Dadurch minimiert JIT überschüssige Lagerbestände und senkt die Lagerkosten. Die Grundidee besteht darin, Materialien und Produkte nur bei Bedarf durch den Produktionsprozess zu „ziehen“, anstatt große Mengen an Lagerbeständen in das Lager zu „schieben“.
Um JIT umzusetzen, müssen Unternehmen eng mit Lieferanten zusammenarbeiten, um zuverlässige und pünktliche Lieferungen zu gewährleisten. Die Produktionsplanung ist bei JIT von entscheidender Bedeutung. Zeitpläne und Arbeitsabläufe müssen eng mit den Bedarfsprognosen abgestimmt werden.
Sie können JIT mit Kanban kombinieren, da sich diese beiden Instrumente ergänzen. JIT reduziert überschüssige Lagerbestände, indem nur nach Bedarf produziert wird, während Kanban visuell signalisiert, wann neue Artikel hergestellt oder bewegt werden sollten. Zusammen sorgen sie dafür, dass die Produktion auf die Nachfrage reagiert und Verschwendung vermieden wird.
9. Poka Yoke (Fehlervermeidung)
Poka Yoke, oder „Fehlervermeidung“, verhindert große Verluste, indem Fehler vermieden werden, bevor sie passieren. Poka Yoke wurde von Shigeo Shingo bei Toyota entwickelt (Sie sehen hier vielleicht einen Trend) und zielt darauf ab, Prozesse zu entwerfen, die Fehler entweder verhindern oder sofort offensichtlich machen. Dieses Lean-Prinzip geht das Problem menschlicher Fehler bei sich wiederholenden Arbeiten wie der Fertigung an. Wenn es umgesetzt wird, eliminiert es kostspielige Nacharbeiten und reduziert die Wahrscheinlichkeit, dass Fehler den Kunden erreichen.
Poka Yoke führt Sicherheitsvorkehrungen ein, die den Mitarbeitern helfen, häufige Fehler zu vermeiden. Ein Beispiel für Poka Yoke ist das Hinzufügen von farbcodierten Verbindungen, die nur in einer Richtung passen. Poka Yoke befähigt Teams, zuverlässiger zu arbeiten, indem es die Fehlervermeidung direkt in den Prozess einbaut.
10. Statistische Prozesskontrolle (SPC)
Die statistische Prozesslenkung (SPC) ist eine datengesteuerte Methode zur Überwachung und Steuerung von Schwankungen in Fertigungsprozessen. Durch die Analyse von Leistungskennzahlen hilft SPC Teams, Trends zu erkennen, potenzielle Probleme frühzeitig zu bemerken und eine gleichbleibende Qualität zu gewährleisten. Tools wie Regelkarten erleichtern die Visualisierung von Daten und halten Prozesse innerhalb der gewünschten Grenzen.
11. Total Productive Maintenance (TPM)
Total Productive Maintenance (TPM) konzentriert sich auf die Maximierung der Anlageneffizienz durch Minimierung von Ausfallzeiten. Durch die Einbeziehung der Bediener in die routinemäßige Wartung und die Schaffung eines proaktiven Ansatzes trägt TPM zur Zuverlässigkeit der Maschine bei. Diese Methode verbessert nicht nur die Produktivität, sondern verlängert auch die Lebensdauer der Anlagen.
Softwarelösungen für die schlanke Produktion
Mit der Weiterentwicklung der schlanken Produktion ist die Technologie zu einem wesentlichen Partner bei der Steigerung der Effizienz und der Vermeidung von Verschwendung geworden. Softwarelösungen erwecken die Prinzipien von Lean zum Leben, indem sie Prozesse automatisieren und wichtige Arbeitsabläufe integrieren.
12. MES (Manufacturing Execution System)
Ein Manufacturing Execution System (MES) hilft Herstellern, die Kontrolle zu behalten, indem es die Produktion in Echtzeit verwaltet. Diese Software verfolgt und koordiniert die Aktivitäten in der Fertigung, wodurch die Prozesse während ihres Ablaufs besser sichtbar werden. MES sorgt für einen reibungslosen Betriebsablauf, indem es die Leistung der Geräte, einschließlich der Gesamtanlageneffektivität (GAE), überwacht, die Produktivität der Mitarbeiter verfolgt und Aufgaben plant. Es hilft auch bei der Verwaltung von Materialien, damit diese bei Bedarf verfügbar sind.
Einer der größten Vorteile eines MES ist seine Fähigkeit, potenzielle Engpässe oder Probleme frühzeitig zu erkennen. So können Teams Anpassungen vornehmen, bevor Probleme eskalieren. Durch die Integration von Daten aus der gesamten Produktionshalle hilft MES den Herstellern, agil und reaktionsschnell zu bleiben.
13. QMS (Qualitätsmanagementsoftware)
Qualitätsmanagementsoftware (QMS) ist der Schlüssel zur Aufrechterhaltung einer gleichbleibenden Qualität und Konformität in allen Fertigungsprozessen. Sie automatisiert Aufgaben wie die Fehlerverfolgung, die Inspektionsplanung und das Dokumentationsmanagement. QMS hilft, Abfall und Nacharbeit zu reduzieren, indem Probleme identifiziert werden, sodass Sie sie lösen können, bevor sie sich auf die Produktion auswirken.
QMS unterstützt auch die Einhaltung von Vorschriften, indem es die gesamte qualitätsbezogene Dokumentation organisiert und auf dem neuesten Stand hält. Dies ist besonders wichtig in Branchen wie der Automobilindustrie, der Luft- und Raumfahrt und dem Gesundheitswesen, in denen Standards zu 100% eingehalten werden müssen.
Projektmanagement-Software
Projektmanagement-Software vereinfacht die Organisation und Durchführung von Fertigungsprojekten, indem sie Informationen zentralisiert und Tools für eine effektive Planung, Überwachung und Kommunikation bereitstellt. Neben der Aufschlüsselung von Projekten in Aufgaben können Teams mit dieser Software auch Termine festlegen und Ressourcen zuweisen. Mit integrierten Funktionen wie Gantt-Diagrammen sorgt die Projektmanagement-Software dafür, dass Projekte im Zeitplan bleiben.
14. MRP I (Materialbedarfsplanung)
Materialbedarfsplanung (MRP I) hilft bei der Optimierung der Bestands- und Produktionssteuerung, um die Kundennachfrage zu decken. Durch die Analyse von Bedarfsprognosen stellt MRP I sicher, dass die richtigen Materialien zur richtigen Zeit verfügbar sind. So werden Engpässe oder Überbestände vermieden.
MRP I optimiert auch die Beschaffung durch die Automatisierung von Nachbestellpunkten und die Planung von Materiallieferungen. Es ist ein unverzichtbares Werkzeug für Unternehmen, die Effizienz und Flexibilität in ihren Abläufen in Einklang bringen wollen.
15. ERP (Enterprise Resource Planning) oder MRPII
Ein ERP für die Fertigung, auch Manufacturing Resource Planning oder MRP II genannt, integriert alle Aspekte eines Unternehmens in einem einzigen, zusammenhängenden System. Dies umfasst die Bereiche Produktion, Lager und Finanzen. ERP bietet Herstellern einen umfassenden Überblick über ihre Betriebsabläufe, um die Entscheidungsfindung und die abteilungsübergreifende Koordination zu erleichtern. Mit ERP können Hersteller Prozesse automatisieren und Echtzeit-Einblicke in die Leistung gewinnen.
Die wichtigsten Kernpunkte
- Bei Lean Manufacturing oder der schlanken Produktion liegt der Schwerpunkt auf der Vermeidung von Verschwendung und der Priorisierung von Maßnahmen, die den Kunden einen Mehrwert bieten und gleichzeitig die Effizienz steigern.
- Tools wie Kanban und Andon machen Arbeitsabläufe transparent und ermöglichen es Teams, Fortschritte zu verfolgen und Probleme umgehend zu beheben.
- Methoden wie die Ursachenanalyse (Root Cause Analysis, RCA) und der PDCA-Zyklus helfen dabei, Ineffizienzen aufzudecken und Lösungen zu implementieren, die die Ursachen von Problemen angehen.
- Strategien wie 5S und Kaizen sorgen für effiziente Arbeitsbereiche und kontinuierliche Prozessverbesserungen und fördern so eine nachhaltige Produktivität.
- Tools wie MES und ERP integrieren Prozesse und bieten Echtzeit-Einblicke, sodass Unternehmen sich schnell anpassen und Verschwendung reduzieren können.
- Der Schwerpunkt auf kontinuierlicher Verbesserung und Teambeteiligung ist der Schlüssel zum langfristigen Erfolg in der schlanken Produktion.
Häufig gestellte Fragen
Kleine Unternehmen können mit der Einführung einfacher, kostengünstiger Tools wie 5S und Kaizen beginnen, um Arbeitsbereiche zu organisieren und schrittweise Verbesserungen zu fördern. Moderne ERP-Systeme für die Fertigung sind auch für Unternehmen mit minimalem Budget verfügbar.
Die Aufrechterhaltung von Lean-Verbesserungen erfordert regelmäßige Schulungen, das Engagement der Führungskräfte und regelmäßige Audits, um sicherzustellen, dass Praktiken wie 5S und Kaizen wirksam bleiben. Die Förderung einer Kultur der kontinuierlichen Verbesserung und die Einbeziehung der Mitarbeiter in die Überwachung und Verfeinerung von Prozessen tragen dazu bei, den Fortschritt aufrechtzuerhalten.
Die Zeit bis zur Erzielung von Ergebnissen hängt vom Umfang der Umsetzung und der Komplexität der Prozesse ab. Während einige Änderungen, wie die Einführung von 5S, sofortige Verbesserungen bewirken können, kann es bei größeren Initiativen wie JIT oder Wertstromanalyse Wochen oder Monate dauern, bis sich eine signifikante Wirkung zeigt. Beständigkeit und Engagement sind der Schlüssel zum langfristigen Erfolg.
Ihnen könnte ebenfalls gefallen: Wie können Sie die Vorlaufzeiten in Ihrer Lieferkette reduzieren?