Die 3 häufigsten Fehler bei der Lagerverwaltung
Ein Lager effizient zu führen, ist keine leichte Aufgabe. Von der Bestandsverwaltung bis zur Mitarbeiterschulung können viele Faktoren Ihren Betrieb beeinflussen. Ein einziger Fehler kann zu erheblichen Verzögerungen, höheren Kosten und sogar zu Sicherheitsrisiken führen. In diesem Artikel untersuchen wir einige der häufigsten Fehler bei der Lagerverwaltung und stellen Ihnen praktische Lösungen zu ihrer Vermeidung vor.
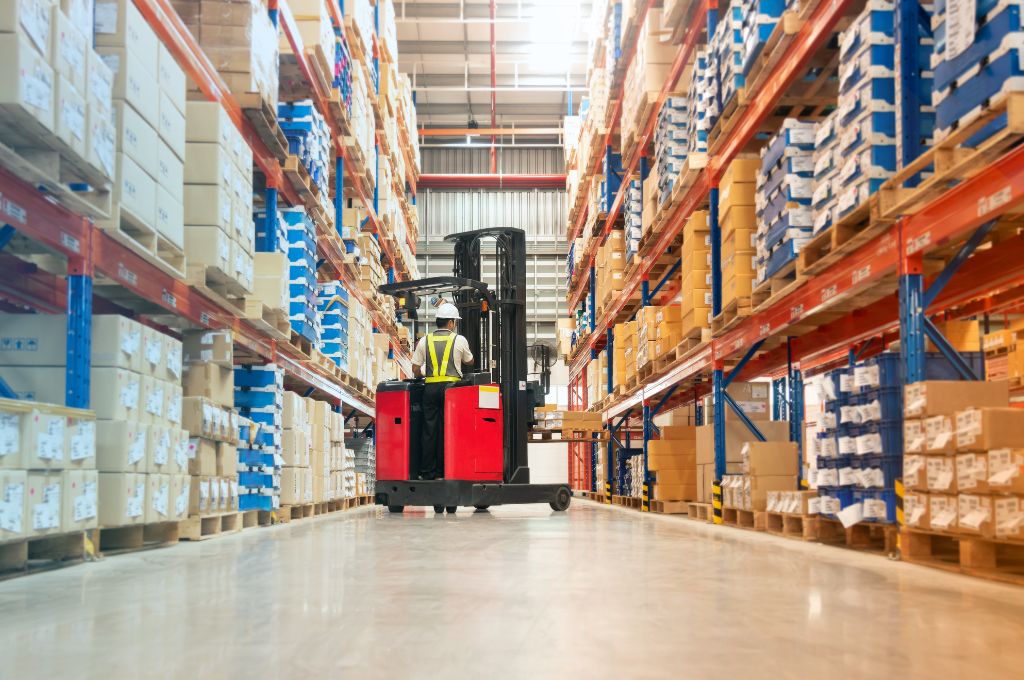
Was ist Lagerverwaltung?
Bei der Lagerverwaltung werden alle Aktivitäten in einem Lager überwacht und organisiert. Zu diesen Aktivitäten gehören der Wareneingang und die Auftragsannahme, die Lagerung von Beständen, die Verwaltung von Lagermengen, die Kommissionierung und Verpackung von Artikeln für den Versand sowie der effiziente Versand von Bestellungen. Das oberste Ziel der Lagerverwaltung ist es, reibungslose Abläufe im Lager zu gewährleisten.
Dieses Ziel ist jedoch manchmal schwer zu erreichen. Fehler passieren, und wenn sie passieren, können sie Ihren Betrieb verlangsamen und zu negativen Kundenerfahrungen mit Ihrem Unternehmen führen. Werfen wir einen Blick auf die häufigsten Fehler in der Lagerverwaltung und wie Sie sie in Ihrem Unternehmen verhindern können.
Fehler Nr. 1: Fehlverwaltung des Lagerbestands
Beginnen wir mit einem der häufigsten Fehler im Lagerwesen: der Fehlverwaltung des Lagerbestands. Dieser Fehler kann weitreichende Folgen für den Lagerbetrieb und die Effizienz des Lieferkettenmanagements haben.
Fehlverwaltung des Lagerbestands ist oft auf eine mangelnde Bestandsverfolgung zurückzuführen. Sie kann auch durch unsachgemäße Planung oder das Vertrauen auf veraltete Papierprozesse verursacht werden. Werfen wir einen Blick auf die negativen Auswirkungen der Fehlverwaltung des Lagerbestands:
- Zu viel oder zu wenig bestellen. Überbestände können ein großes Problem darstellen. Mehr Lagerbestände als nötig belegen wertvollen Lagerraum und binden Gelder, die an anderer Stelle im Unternehmen besser eingesetzt werden könnten. Darüber hinaus besteht bei zu lange gelagerten Produkten die Gefahr, dass sie veralten oder ablaufen, insbesondere in Branchen, in denen sich Trends schnell ändern oder Produkte eine begrenzte Haltbarkeit haben. Dies ist nicht nur eine Verschwendung von Ressourcen, sondern kann auch zu finanziellen Verlusten führen. Auf der anderen Seite kann es zu Fehlmengen kommen, wenn Sie nicht genug bestellen. Fehlende Lagerbestände können die Auftragsabwicklung zum Erliegen bringen. Die Folge? Verzögerungen, Lieferrückstände und unzufriedene Kunden. Das kann Ihrem Ruf schaden und zu Umsatzeinbußen und Vertrauensverlust bei den Kunden führen.
- Fehlende Echtzeitverfolgung. Es ist wichtig, die Lagerbestände ständig zu überwachen und zu aktualisieren, wenn Artikel in den Lagerraum gebracht oder aus diesem entnommen werden. Viele Lager nutzen jedoch keine Echtzeitverfolgung, da sie auf veraltete Methoden wie papierbasierte Erfassung setzen. Das kann zu ungenauen Bestandszählungen führen, wodurch die Wahrscheinlichkeit von Überbeständen oder Fehlmengen steigt.
- Ungenaue Prognosen. Wenn Sie nicht über genügend Daten verfügen, um die Nachfrage genau vorherzusagen, oder keine entsprechenden Tools nutzen, um dies effektiv zu tun, riskieren Sie Überbestände und Fehlmengen. Überbestände reduzieren nicht nur den verfügbaren Lagerraum, sondern binden auch Ihre Ressourcen. Fehlmengen führen zu entgangenen Verkäufen und enttäuschten Kunden. Keine der beiden Optionen ist gut.
- Zu seltene Bestandsaufnahmen. Bestandsaufnahmen, sprich das physische Zählen aller Artikel in Ihrem Lager, sind eine notwendige Praxis, um die Genauigkeit des Lagerbestands sicherzustellen. Zu seltene Bestandsaufnahmen können jedoch zu Diskrepanzen zwischen dem tatsächlichen Lagerbestand und den in Ihrem System erfassten Daten führen. Diese Diskrepanzen können Sie Geld kosten und zu nicht ausgeführten Bestellungen und Überbeständen führen.
- Manuelle Methoden. Wie bereits erwähnt, sind manuelle Methoden der Bestandsverwaltung, wie das Führen von Papieraufzeichnungen oder die Verwendung von Tabellenkalkulationen, anfällig für menschliche Fehler. Diese veralteten Methoden sind außerdem langsamer und weniger zuverlässig als automatisierte Systeme.
Bewährte Verfahren zur Vermeidung einer schlechten Bestandsverwaltung
Wie können Sie einer schlechten Bestandsverwaltung entgegenwirken? Implementieren Sie eine Lagerverwaltungslösung (WMS). Ein WMS (oder Warehouse Management Solution) automatisiert die Bestandsverfolgung und liefert Echtzeitdaten zu den Lagerbeständen. Dies reduziert das Risiko menschlicher Fehler und steigert die Gesamtproduktivität, indem es eine All-in-One-Lösung für die Lagerverwaltung bietet.
Die Durchführung regelmäßiger Audits ist eine weitere bewährte Methode. Bestandsaudits tragen dazu bei, die Bestandsgenauigkeit aufrechtzuerhalten und Unstimmigkeiten frühzeitig zu erkennen. So stellen Sie sicher, dass der tatsächliche Bestand mit den aufgezeichneten Beständen übereinstimmt und Überbestände und Fehlmengen vermieden werden. Durch den Einsatz von Barcode- und Lagerautomatisierungstools werden Fehler weiter reduziert und die Bestandsgenauigkeit erhöht. Regelmäßige Bestandsaufnahmen oder auch nur eine teilweise Zählung der wichtigsten Waren sind eine weitere effektive Möglichkeit, diese Probleme anzugehen.
Eine gute Planung ist ebenfalls von entscheidender Bedeutung. Eine genaue Bedarfsprognose und -planung sind für die Optimierung des Lagerbestands unerlässlich. Durch die Analyse historischer Verkaufsdaten, Markttrends und saisonaler Schwankungen können Sie die Kundennachfrage und den Lagerbedarf vorhersagen und die Lagerbestände entsprechend anpassen.
Fehler Nr. 2: Schlechtes Lagerlayout
Ein schlechtes Lagerlayout kann für die Lagerverwaltung schnell zum Albtraum werden. Schauen wir uns genauer an, warum.
- Geringere Produktivität. Das erste große Problem ist die geringere Produktivität. Wenn die Lagerfläche nicht optimiert ist, verbringen Ihre Mitarbeiter mehr Zeit damit, längere Kommissionierwege zurückzulegen, um Artikel zu finden und zu entnehmen. Diese Ineffizienz verlangsamt nicht nur die Auftragserfüllung, sondern erhöht auch die Arbeitskosten, da mehr Zeit für die Erledigung von Aufgaben benötigt wird, die schneller und einfacher sein sollten. Ein ineffizientes Layout kann einen eigentlich einfachen Prozess in eine zeitraubende Tortur verwandeln.
- Erhöhte Fehlerquoten. Eine weitere kritische Folge ist eine erhöhte Fehlerquote. In einem schlecht organisierten Lager folgt die Artikelaufbewahrung keiner Logik, was Ihre Mitarbeiter beim Kommissionieren verwirren kann. Verwirrung führt oft zu Fehlern wie der Kommissionierung der falschen Artikel oder falscher Mengen, was unweigerlich zu einer ungenauen Auftragserfüllung führt. Allerdings könnten nicht nur Ihre Mitarbeiter, sondern auch Ihre Kunden irritiert werden, wenn sie die falsche Bestellung erhalten. Diese Irritation führt schnell zu Unzufriedenheit und Misstrauen.
- Erhöhte Arbeitskosten. Erhöhte Arbeitskosten sind eng mit den durch ein schlechtes Layout verursachten Ineffizienzen verbunden. Wenn Mitarbeiter zusätzliche Zeit für die Suche und Kommissionierung von Artikeln aufwenden müssen, steigt der Gesamtarbeitsaufwand für die Auftragserfüllung. Das treibt die Betriebskosten in die Höhe, was an sich schon eine schlechte Nachricht ist, sich aber zusätzlich auf die Gesamteffizienz des Lagers auswirkt. Auch die Rentabilität ist davon betroffen. Anstatt sich auf produktivitätssteigernde Aufgaben zu konzentrieren, werden die Mitarbeiter durch die grundlegenden Ineffizienzen eines suboptimalen Layouts ausgebremst.
- Sicherheit. Dann ist da noch die Frage der Sicherheit. Sicherheitsrisiken sind ein oft übersehenes, aber kritisches Problem, das sich aus einer schlechten Lagerraumgestaltung ergibt. Unaufgeräumte oder schlecht organisierte Räume können zahlreiche Sicherheitsrisiken bergen, wie z. B. blockierte Gänge, schlecht gestapelte Artikel und unsichere Wege. Diese Gefahren erhöhen das Risiko von Unfällen und Verletzungen, die Ihren Betrieb stören und zu kostspieligen Schadensersatzansprüchen von Arbeitnehmern und potenziellen rechtlichen Problemen führen können.
Bewährte Verfahren zur Verbesserung des Lagerlayouts
Um diese Probleme zu bekämpfen, nehmen Sie sich die Zeit, um Ihren Lagerbereich zu organisieren. Durch diese Organisation werden Wegezeiten minimiert und Arbeitsabläufe optimiert.
Artikel mit hoher Nachfrage sollten an besser zugänglichen Lagerorten aufbewahrt werden, um die Kommissionierung, Einlagerung und Materialhandhabung zu beschleunigen. Nutzen Sie vertikale Lagerlösungen wie Regale und Paletten, um den Platz in Ihrem Lager zu maximieren. Dadurch bleibt die Bodenfläche frei und die Zugänglichkeit des Lagerbestands wird verbessert.
Ziehen Sie die Umsetzung der 80/20-Regel in Betracht, die auch als Pareto-Prinzip oder ABC-Lagerverwaltung bekannt ist. Bei der 80/20-Regel ermitteln Sie zunächst die 20 % der Artikel in Ihrem Bestand, die 80 % des Umsatzes generieren. Platzieren Sie diese Artikel dann an der am besten zugänglichen Stelle in Ihrem Lager, um Zeit und Aufwand zu sparen.
Schaffen Sie freie Wege für Gabelstapler und Mitarbeiter, die sich durch das Lager bewegen. Dadurch wird das Unfallrisiko verringert und die Arbeitsabläufe werden optimiert. Teilen Sie Ihr Lager in Zonen ein, indem Sie den Raum in bestimmte Bereiche unterteilen, die auf unterschiedlichen Funktionen basieren. Sie können beispielsweise separate Bereiche für den Wareneingang, die Lagerung, die Kommissionierung, die Verpackung und den Versand in Ihrem Lager einrichten. Dadurch werden Prozesse optimiert und Verwirrung vermieden.
Durch den Einsatz eines Lagerverwaltungssystems können Sie außerdem die Lagerorte in Echtzeit überwachen und wertvolle Erkenntnisse über die optimalsten Lagerlayouts auf der Grundlage des Warenflusses gewinnen. Ein WMS analysiert Daten zu Lagerbewegungen und Auftragserfüllung und identifiziert Muster zur Optimierung der Lagerung. Es verfolgt auch Bewegungen und schlägt Layoutanpassungen vor, um die Wegezeiten zu verkürzen und die Raumnutzung zu verbessern.
Es hat sich auch bewährt, das Lagerlayout regelmäßig zu überprüfen und anzupassen. Wenn sich die Anforderungen Ihres Unternehmens ändern, stellen diese regelmäßigen Bewertungen sicher, dass Ihre Einrichtung effizient bleibt. Durch die Anpassung an neue Produkte, saisonale Veränderungen und Schwankungen im Auftragsvolumen können Sie einen reibungslosen Ablauf in Ihrem Lager gewährleisten.
Fehler Nr. 3: Fehlende Schulungen
Unzureichende Schulungen gehören zu den häufigsten Fehlern, die den Lagerbetrieb beeinträchtigen können. Dies kann auf den Wunsch eines Unternehmens zurückzuführen sein, die Arbeitskosten gering zu halten. Häufig ist es jedoch auf eine hohe Mitarbeiterfluktuation zurückzuführen, da nur wenige Mitarbeiter zur Verfügung stehen, um neue Mitarbeiter zu schulen. Es kann auch die naive Annahme bestehen, dass neue Mitarbeiter ohne formelle Schulung allein am Arbeitsplatz alles lernen können. Was auch immer der Grund ist, mangelnde Schulungen führen zu Ineffizienzen, vermehrten menschlichen Fehlern und Sicherheitsmängeln.
Hier erfahren Sie, wie sich mangelnde Schulung negativ auf Ihr Unternehmen auswirken kann:
- Ineffiziente Betriebsabläufe. Wenn Mitarbeiter nicht richtig geschult sind, verstehen sie möglicherweise ihre Aufgaben nicht vollständig oder wissen nicht, wie sie Aufgaben effizient ausführen können. Dies führt zu Verzögerungen und Engpässen im Lagerbetrieb.
- Höhere Fehlerquoten. Unerfahrene Mitarbeiter machen eher Fehler bei der Bestandsverwaltung, der Kommissionierung und anderen kritischen Aufgaben. Infolgedessen hat Ihr Unternehmen mit ungenauen Lagerbeständen und einer fehlerhaften Auftragserfüllung zu kämpfen. Diese Fehler können zu unzufriedenen Kunden und zusätzlichen Kosten für die Fehlerbehebung führen.
- Sicherheitsrisiken. Ohne eine angemessene Schulung in Sicherheitsprotokollen steigt das Risiko von Unfällen und Verletzungen. Dies führt nicht nur zu Produktionsunterbrechungen, sondern kann auch zu höheren Kosten für Gesundheit und Sicherheit sowie zu einer höheren Unfallrate führen. Ungeschultes Personal kennt möglicherweise nicht die korrekten Verfahren für den Umgang mit Geräten oder Materialien. Durch unsichere Praktiken können Ihre Mitarbeiter verletzt werden und sogar Ihre Kunden einem Verletzungsrisiko ausgesetzt sein. Beispielsweise kann eine unsachgemäße Handhabung von Materialien zu beschädigten Waren führen, wodurch fehlerhafte oder unsichere Produkte an Kunden gelangen.
- Geringere Kundenzufriedenheit. Wenn Aufträge nicht korrekt oder pünktlich ausgeführt werden, kann dies das Vertrauen und die Loyalität der Kunden stark beeinträchtigen. Diese Fehler oder Verzögerungen können zu unzufriedenen Kunden und Geschäftsverlusten führen.
Bewährte Verfahren zur Umsetzung effektiver Schulungsprogramme
Um die oben genannten Probleme anzugehen, sollten Sie umfassende und effektive Schulungsprogramme ausarbeiten. Diese sind weit mehr als ein schönes „Vorzeigeobjekt“ und vielmehr ein wesentlicher Bestandteil einer effektiven Lagerverwaltung. Ein gründliches Einführungsprogramm sollte alle Aspekte des Lagerbetriebs abdecken, von der Bestandsverwaltung bis hin zu Sicherheitsverfahren. Auf diese Weise verstehen Ihre neuen Mitarbeiter vom ersten Tag an ihre Aufgaben und Verantwortlichkeiten.
Die Schulung sollte nicht nach der Einarbeitung enden. Führen Sie fortlaufende Schulungsprogramme durch, um die Mitarbeiter über die neuesten Technologien, Verfahren und bewährten Praktiken auf dem Laufenden zu halten.
Wenn möglich, sollten Mitarbeiter für mehrere Aufgaben im Lager ausgebildet werden. Cross-Training ist für die meisten Unternehmen eine kluge Entscheidung, da es Flexibilität bietet und dazu beiträgt, die Produktivität bei Personalmangel oder in Spitzenzeiten aufrechtzuerhalten. Außerdem sollten Sie Schulungen zu Gesundheit und Sicherheit priorisieren, damit alle Mitarbeiter die Sicherheitsprotokolle verstehen und einhalten, um das Unfallrisiko zu verringern.
Nutzen Sie verschiedene Schulungsformen, darunter Live-Sessions, Online-Schulungsmodule, Video-Tutorials und interaktive Simulationen. Diese Sorte von Schulungspräsentationen kann Ihre Schulung ansprechender und effektiver machen. Echtzeit-Feedback und -Bewertungen helfen dabei, Fortschritte zu verfolgen und verbesserungswürdige Bereiche zu identifizieren.
Durch Investitionen in umfassende und kontinuierliche Schulungsprogramme können Sie die Gesamtproduktivität verbessern, Fehler reduzieren und die Sicherheit erhöhen. Gut ausgebildetes Personal ist entscheidend für einen effizienten Lagerbetrieb und die Gewährleistung der Kundenzufriedenheit.
Abschließende Gedanken
Die Vermeidung gängiger Lagerfehler ist für einen reibungslosen und sicheren Betrieb von entscheidender Bedeutung. Durch den Fokus auf eine ordnungsgemäße Bestandsverwaltung, die Optimierung Ihres Lagerlayouts und die Sicherstellung einer gründlichen Mitarbeiterschulung können Sie die Produktivität erheblich steigern und Fehler reduzieren. Denken Sie daran, dass ein gut organisiertes und effizientes Lager Ihren Gewinn erhöht und gleichzeitig die Moral der Mitarbeiter und die Kundenzufriedenheit steigert.
Die Implementierung einer geeigneten Bestandsmanagementsoftware oder eines ERP-Systems (Enterprise Resource Planning) für die Fertigung kann zu den effizientesten Mitteln zur Verbesserung des Lagerverwaltungsprozesses gehören. Moderne Cloud-basierte Systeme sind kostengünstig und funktionsreich und bieten darüber hinaus eine fortschrittliche Bestandskontrolle, eine durchgängige Rückverfolgbarkeit und Skalierbarkeit.
Die wichtigsten Kernpunkte
- Eine ordnungsgemäße Bestandsverfolgung verhindert Überbestände und Fehlmengen, verbessert die Lagereffizienz und senkt die Produktions- und Lagerkosten.
- Ein gut durchdachtes Lagerlayout minimiert die Wegezeiten, senkt die Arbeitskosten und erhöht die Sicherheit.
- Kontinuierliche und gründliche Schulungen für das Personal minimieren Fehler, steigern die Produktivität und erhöhen die Sicherheit.
- Die Implementierung eines Lagerverwaltungssystems (WMS) unterstützt die Echtzeit-Bestandsverfolgung und die Layout-Optimierung.
- Durch regelmäßige Überprüfung und Anpassung der Lagerprozesse und -layouts können Sie Ineffizienzen beheben und sicherstellen, dass Sie sich schnell an veränderte Geschäftsanforderungen anpassen.
- Wenn Sie alle Mitarbeiter in Sicherheitsverfahren schulen, senken Sie das Unfallrisiko und schützen Ihre Mitarbeiter und Kunden.
Häufig gestellte Fragen
Die Lagerverwaltung umfasst die Überwachung und Organisation aller Aktivitäten in einem Lager, einschließlich der Annahme, Lagerung und des Versands von Lagerbeständen. Sie ist von entscheidender Bedeutung für die Aufrechterhaltung eines effizienten Betriebs, die Vermeidung von Verzögerungen, die Senkung von Kosten und die Gewährleistung der Kundenzufriedenheit.
Um das Lagerlayout zu verbessern, organisieren Sie die Fläche, um die Wegzeiten zu minimieren und die Arbeitsabläufe zu optimieren. Nutzen Sie vertikale Lagerung, setzen Sie die 80/20-Regel um, schaffen Sie hindernisfreie Wege und überprüfen und passen Sie das Layout regelmäßig an. Ein WMS kann durch die Analyse von Bestandsbewegungen ebenfalls zur Optimierung von Layouts beitragen.
Eine schlechte Bestandsverwaltung kann zu Überbeständen, Fehlmengen und ungenauen Prognosen führen. Diese Probleme können wertvollen Platz beanspruchen, Gelder binden, die Auftragserfüllung zum Stillstand bringen und zu finanziellen Verlusten führen, was letztlich zu Unzufriedenheit bei den Kunden führt.
Um die Skalierbarkeit in der Lagerverwaltung zu gewährleisten, sollten Sie in ein flexibles Lagerverwaltungssystem (WMS) investieren, das sich an Ihren wachsenden Lagerbestand und Ihre betrieblichen Anforderungen anpassen kann. Überprüfen Sie außerdem regelmäßig Ihre Prozesse und Ihr Lagerlayout, um dem gestiegenen Volumen und der Komplexität Rechnung zu tragen. Die Schulung von Mitarbeitern und die Einführung kontinuierlicher Verbesserungspraktiken können ebenfalls dazu beitragen, dass Ihre Lagerabläufe reibungslos skalieren, wenn Ihr Unternehmen wächst.
Ihnen könnte ebenfalls gefallen: Leitfaden für schlanke Lagerverwaltung für KMU