Materialplanung – Definition, Tools und Tipps
Bei der Materialplanung geht es darum herauszufinden, was in welchen Mengen benötigt wird, um Waren innerhalb eines bestimmten Zeitrahmens zu produzieren und die rechtzeitige Lieferung dieser Materialien sicherzustellen. Eine genaue Materialplanung kann erheblich zur Effizienz und Rentabilität eines Unternehmens beitragen.
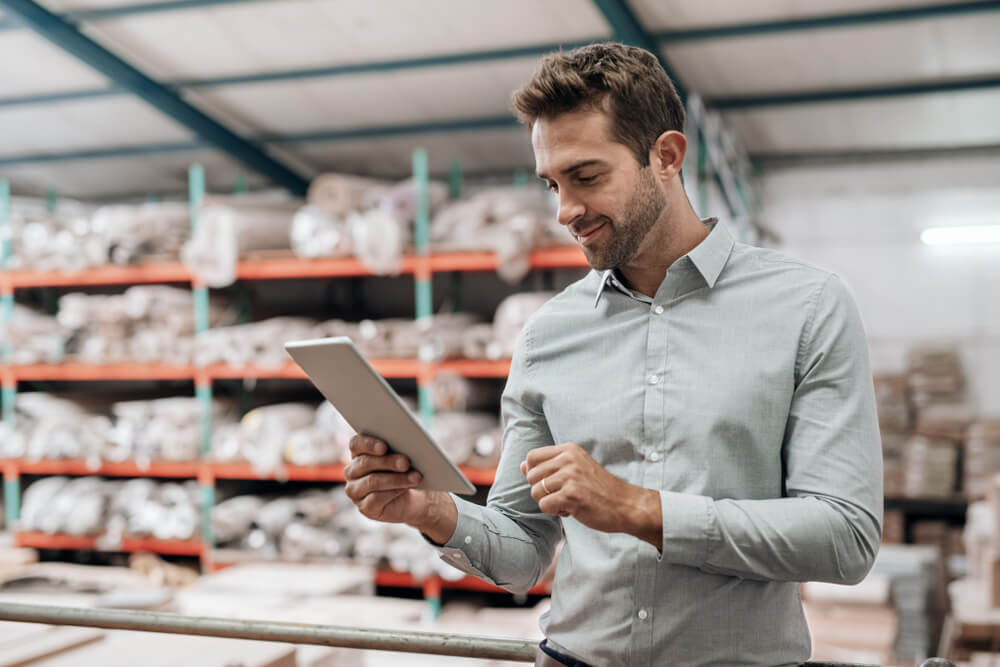
Was ist Materialplanung?
Die Materialplanung ist ein Prozess in der Fertigung, bei dem es darum geht, die in der Produktion benötigten Materialien und Mengen zu bestimmen und ihren Fluss zu steuern, um eine rechtzeitige Auftragserfüllung zu gewährleisten. Als solcher ist sie ein Teilprozess des Supply Chain Management.
Zu den Hauptaufgaben von Materialplanern gehören:
- Analyse von Bedarfsprognosen
- Berechnung des Materialbedarfs
- Erstellung von RFQs und Kaufaufträgen
- Sicherstellung, dass die Materialien den Spezifikationen, Qualitätsstandards und Budgetvorgaben entsprechen
- Erstellung von Beschaffungsplänen und Zeitplänen
In kleinen Unternehmen ist die Materialplanung jedoch ein Bereich, der sich häufig mit dem Bestandsmanagement, dem Einkauf, dem Supply Chain Management und sogar der Produktionsplanung überschneidet. Deshalb kann in kleinen Fertigungsunternehmen die Person, die für die Materialplanung zuständig ist, auch für alles andere verantwortlich sein, von der Material- und Komponentenbeschaffung bis hin zur Produktionssteuerung.
Warum ist die Materialplanung wichtig?
Eine exakte und kontinuierliche Materialplanung ist für jeden Hersteller von entscheidender Bedeutung. Ohne sie riskieren Sie höhere Lagerkosten, unzufriedene Kunden, Engpässe im Lagerbestand und weniger pünktliche Lieferungen. Wenn Rohmaterialien oder Komponenten verspätet eintreffen, kann Ihr Produktionsplan aus dem Ruder laufen, was sich wahrscheinlich in geringeren Gewinnen niederschlägt.
Eine effektive Materialplanung hilft Ihnen jedoch bei der Produktionsplanung, der Bestandskontrolle und in anderen Bereichen wie der Angebotserstellung, den Arbeitsaufträgen, den Stücklisten und der Werkstattverwaltung. Mit einer zuverlässigen Materialplanung können Hersteller Verbesserungen bei der Kundenzufriedenheit, der Gesamteffizienz und dem Endergebnis ihres Unternehmens erwarten.
Vorteile einer genauen Materialplanung
Eine genaue Materialplanung kann eine Reihe von Vorteilen bieten, darunter:
- Kosteneinsparungen. Durch eine genaue Planung des Materialbedarfs können Unternehmen eine Über- oder Unterbevorratung vermeiden, die zu unnötigen Kosten oder Geschäftseinbußen führen kann. Eine genaue Materialplanung kann Unternehmen auch dabei helfen, bessere Preise mit Lieferanten auszuhandeln, da sie einen Einblick in die langfristige Nachfrage ermöglicht.
- Bessere Effizienz der Lieferkette. Eine genaue Materialplanung kann den Warenfluss in der gesamten Lieferkette rationalisieren, die Vorlaufzeiten verkürzen und den Bestand auf einem optimalen Niveau halten. Dies kann Unternehmen helfen, Verschwendung zu reduzieren, Lieferzeiten zu verkürzen und die Kundennachfrage besser zu erfüllen.
- Besseres Bestandsmanagement. Mit einer präzisen Materialplanung können Unternehmen ihre Lagerbestände optimieren, sodass weniger kostspielige Lagerhaltung erforderlich ist und das Risiko von Fehlbeständen minimiert wird.
- Bessere Kundenzufriedenheit. Eine genaue Materialplanung kann dazu beitragen, dass Fertigwaren verfügbar sind, wenn die Kunden sie benötigen, und so das Risiko von Verzögerungen oder Lieferrückständen verringern. Dies kann dazu beitragen, die Kundenzufriedenheit und die Kundenbindung zu verbessern.
- Verbesserte Prognosen. Genaue Umsatzprognosen sind zwar für eine genaue Materialplanung erforderlich, aber eine genaue Materialplanung kann auch dazu beitragen, die Zusammenarbeit zwischen den Abteilungen zu verbessern, die Vorlaufzeiten zu verkürzen und die Lagerbestände zu optimieren, was alles zur Verfeinerung der Prognosen beitragen kann.
Zusammenfassend lässt sich sagen, dass eine genaue Materialplanung Unternehmen dabei helfen kann, die Kosten zu senken, die Effizienz in der gesamten Lieferkette zu verbessern und die Kundenanforderungen besser zu erfüllen.
Die 7 grundlegenden Schritte der Materialplanung
Der Materialplanungsprozess umfasst mehrere wichtige Schritte:
- Bedarf prognostizieren. Der erste Schritt besteht darin, die Nachfrage nach Fertigprodukten auf der Grundlage von historischen Daten, Markttrends und anderen relevanten Faktoren zu prognostizieren.
- Die benötigten Materialien bestimmen. Auf der Grundlage der Bedarfsprognose bestimmt das Materialplanungsteam die Arten und Mengen von Rohstoffen, Komponenten und anderen Inputs, die zur Herstellung der Produkte benötigt werden.
- Einen Beschaffungsplan erstellen. Das Materialplanungsteam arbeitet mit dem Einkaufsteam zusammen, um einen Beschaffungsplan zu erstellen, der Faktoren wie den aktuellen Bestand, Vorlaufzeiten, Sicherheitsbestände und Mindestbestellmengen berücksichtigt.
- Bestellungen erstellen. Das Team erstellt Bestellungen für die benötigten Materialien und gibt dabei die Mengen und Liefertermine an.
- Die Materiallieferung verfolgen. Das Materialplanungsteam verfolgt die Lieferung der bestellten Materialien, um sicherzustellen, dass sie pünktlich und in der richtigen Menge eintreffen.
- Die Pläne bei Bedarf anpassen. Das Materialplanungsteam muss unter Umständen den Produktionsplan und die Bestellungen aufgrund von Änderungen der Nachfrage, Verzögerungen bei der Materiallieferung oder anderen Faktoren, die die Lieferkette beeinflussen, anpassen.
- Die Leistung bewerten. Nach Abschluss des Produktionszyklus bewertet das Materialplanungsteam seine Leistung anhand des Plans, ermittelt verbesserungswürdige Bereiche und nimmt bei Bedarf Anpassungen am Materialplanungsprozess vor. Darüber hinaus sollten Sie die Leistung Ihrer Lieferanten verfolgen und bewerten.
Durch einen gut definierten und strukturierten Materialplanungsprozess können Unternehmen ihren Lieferkettenfluss optimieren und Verschwendung und Ineffizienzen minimieren.
Tools und Techniken der Materialplanung
Bestellpunkt
Der Bestellpunkt wird verwendet, um zu bestimmen, wann eine bestimmte Lagereinheit neu bestellt werden muss. Es handelt sich dabei um den Lagerbestand, bei dem eine Bestellung aufgegeben werden sollte, um den Bestand aufzufüllen, damit der Bestand nicht unter ein kritisches Niveau fällt.
Durch die Festlegung von Meldebeständen für ihre Materialien können Unternehmen sicherstellen, dass sie über genügend Bestände verfügen, um die Kundennachfrage zu befriedigen, ohne unnötige Kosten für überschüssige Bestände in Kauf nehmen zu müssen. Der Bestellpunkt ist eine wichtige Komponente von Bestandsverwaltungssystemen und wird häufig in Kombination mit anderen Instrumenten wie der optimalen Bestellmenge und dem Sicherheitsbestand verwendet, um die Lagerbestände zu optimieren und die Kosten zu minimieren.
Lesen Sie mehr über den Bestellpunkt und wie man ihn berechnet.
Kanban
Kanban ist eine Nachschubtechnik, bei der visuelle Hinweise wie z.B. Signcards verwendet werden, um die Produktion oder eine neue Materialbestellung auszulösen. Das Ziel des Kanban-Systems ist es, einen reibungslosen und effizienten Materialfluss durch den Produktionsprozess zu schaffen und gleichzeitig überschüssige Bestände zu vermeiden und den Abfall zu minimieren.
In einem Kanban-System hat jede Produktionsstufe einen bestimmten Lagerbestand, der durch eine Kanban-Karte oder ein anderes visuelles Signal überwacht wird. Wenn der Lagerbestand unter einen bestimmten Punkt fällt, wird das Kanban-Signal an die vorherige Stufe gesendet, um anzuzeigen, dass mehr Material benötigt wird. Dies löst den Nachschub von Materialien aus, entweder durch interne Produktion oder externe Beschaffung.
Just-in-time
Just-in-Time (JIT) ist ein Fertigungs- und Materialplanungssystem, das so konzipiert ist, dass Materialien und Produkte genau zum richtigen Zeitpunkt für ihre Verwendung produziert oder beschafft werden. Das Just-in-Time-System stützt sich auf Echtzeit-Nachfragesignale wie Kunden- oder Fertigungsaufträge, um die Produktion oder Beschaffung von Materialien auszulösen. Anstatt große Mengen an Materialien zu kaufen und auf Lager zu halten, beschaffen JIT-Materialplanungssysteme nur das, was zu einem bestimmten Zeitpunkt benötigt wird. Dadurch verringert sich die Menge der Bestände, die ein Unternehmen vorhalten muss, was wiederum die Kosten für die Lagerung und Verwaltung überschüssiger Bestände reduziert.
Materialbedarfsplanung
Materialbedarfsplanung oder Material Requirements Planning (MRP I) ist der Vorläufer der modernen MRP- und ERP-Systeme. MRP I war das erste weit verbreitete computergestützte Produktionsplanungssystem und hatte praktisch nur die Funktion der Materialplanung. Das MRP-Verfahren verwendet Eingaben wie den Produktionsplan, die Bestandsstatusdatei und die Stückliste, um die Mengen an Materialien, Komponenten oder Unterbaugruppen zu berechnen, die benötigt werden, um die erwarteten Kundenaufträge innerhalb eines bestimmten Zeitraums zu erfüllen.
Es gibt zwar spezialisierte Softwaresysteme für die Materialbedarfsplanung, aber diese grundlegenden Funktionen lassen sich auch in Tabellenkalkulationen einrichten, indem Sie einen Excel-Experten beauftragen oder online verfügbare Vorlagen verwenden. Wenn Sie fortschrittlichere Funktionen für die Verwaltung Ihres Fertigungsbetriebs benötigen, sollten Sie sich mit MRP I befassen.
Lesen Sie mehr über Materialbedarfsplanung.
Software für Manufacturing Ressources Planning
Manufacturing Resource Planning (MRP II) oder ERP-Software für die Fertigung ermöglicht es Ihnen, neben der Materialplanung auch andere Fertigungsprozesse zu verwalten und das gesamte Unternehmen in ein einziges System zu integrieren. Neben der Materialbedarfsplanung umfasst diese Art von MRP-System Funktionen, die die Vertriebs- und Auftragsverwaltung, die Bestandsverwaltung, die Beschaffung, die Produktionsplanung und die Terminierung unterstützen und rationalisieren und damit ein umfassendes Betriebsmanagementsystem für Hersteller darstellen.
Moderne Cloud-basierte MRP-Software bietet Herstellern einen Echtzeit-Überblick über ihre Produktionsprozesse, Lagerbestände, Einkaufs- und Kundenbestellungsstatus usw. Mit MRP-Software können Sie den Lagerbedarf berechnen, Meldepunkte und Sicherheitsbestände festlegen, um Fehlbestände zu vermeiden, selbst wenn die Nachfrage größer ist als erwartet, und Benachrichtigungen erhalten, wenn der Bestand unter ein bestimmtes Niveau fällt. So entsteht ein Bestandskontrollsystem, mit dem Sie Fehl- und Überbestände vermeiden können.
Wenn der MRP-Software ein Buchhaltungsmodul hinzugefügt wird, kann sie auch als ERP-System (Enterprise Resource Planning) für die Fertigung betrachtet werden.
Einige MRP/ERP-Systeme enthalten auch Rückwärtsterminierungsfunktionen, mit denen Sie das Just-in-Time-Modell umsetzen können. Bei der Just-in-Time-Fertigung und -Bestandsverwaltung wird die Produktion in letzter Minute geplant, d.h. die Fertigwaren werden gerade rechtzeitig zum gewünschten Liefertermin produziert. Das bedeutet auch, dass die Materialien gerade rechtzeitig bestellt werden, damit sie in der Produktion verwendet werden können. Auf diese Weise wird der Lagerbestand auf ein absolutes Minimum reduziert, wodurch die Lagerhaltungskosten minimiert werden.
Lesen Sie mehr über die Vorteile von MRP in unserem Blogbeitrag über die Vor- und Nachteile des Einsatzes eines MRP-Systems.
5 Tipps, um die Materialplanung effektiver zu gestalten
1. Ihre Lagerbestände müssen genau sein
Sie kennen das Sprichwort seit der Einführung der Computerprogrammierung: “Garbage in, Garbage out“. Wenn Ihre Lagerbestände nicht korrekt sind, können Sie sich nicht auf die Daten verlassen, die Ihr System für Sie generiert. Mit anderen Worten: Wenn Ihre Bestandsmengen nicht korrekt sind, wird Ihr Dispositionssystem um diese ungenauen Mengen herum planen.
Stellen Sie außerdem sicher, dass die Qualitätskontrolle den gesamten Bestand in Ihrem System genehmigt hat. Wenn dies nicht der Fall ist, wird Ihr nutzbarer Bestand geringer sein, als Sie angenommen haben, und Ihre Materialplanung wird durch fehlerhafte Daten verzerrt und beeinträchtigt.
Die Bedeutung präziser Daten ist zwar bekannt, doch überraschenderweise achten viele Hersteller nicht auf die Genauigkeit der eingegebenen Daten, sodass sie den Rest ihrer Materialplanung gefährden. Diese Bemühungen sollten sich auf alle Kalender, Ressourcen, Bestände und Kapazitäten konzentrieren. Wenn Sie die Zahlen überprüfen und regelmäßige Überprüfungen einplanen, können Sie sicherstellen, dass die von Ihnen verwendeten Daten auf dem neuesten Stand sind.
2. Ordnungsgemäße Prognosen sollten eine Priorität sein
MRP-Systeme verwenden in der Regel entweder Ihre offenen oder Ihre prognostizierten Verkäufe, um Ihren Materialbedarf zu berechnen. Wenn Sie Ihre Prognose erstellen, kann diese auf erwarteten oder auf Produktionszahlen basieren. Wie auch immer Sie sich entscheiden, das System wird die Informationen verwenden, um Ihren Materialbedarf zu ermitteln.
Wenn Sie die prognostizierten Verkäufe in Verbindung mit einem Produktionsplan und nicht mit den offenen Verkäufen verwenden, können Sie Ihren Materialbedarf weiter in die Zukunft verschieben als die Zeitspanne, die für Ihre aktuellen Kundenaufträge gilt. Außerdem haben Sie so den Vorteil, dass Sie Ihre Produktion und Ihren Personalbedarf weit in die Zukunft planen können.
Die von Ihnen erstellte Prognose muss nicht in Stein gemeißelt sein (und sollte es auch nicht sein!). Sie müssen eine gewisse Flexibilität haben, um Änderungen vornehmen zu können, wenn sich die Bedingungen ändern. Viele Hersteller haben das ganze Jahr über mit Schwankungen zu kämpfen. Diese Nachfrageschwankungen können auf Jahreszeiten, Feiertage, Veranstaltungen oder Trends zurückzuführen sein. Wenn Sie vermeiden wollen, dass Produktionsüberschüsse vergeudet werden oder die Nachfrage nicht gedeckt werden kann, müssen Sie genaue Prognosen zu einer Priorität machen.
Gute MRP- und ERP-Lösungen für die Fertigung können Ihnen helfen, die Materialplanung und -prognose zu verbessern. Ihr System wird mit historischen Verkaufsdaten ausgestattet sein, die Ihnen unschätzbare Einblicke in Ihren zukünftigen Bedarf geben sollten.
3. Berücksichtigen Sie Vorlaufzeiten bei der Materialplanung
Sie brauchen in Ihrem System genaue Daten für Verkaufs- und Kaufaufträge. Im Idealfall informiert Sie Ihr MRP-System darüber, wann Sie Ihre Materialien für die Produktion benötigen. Ein Beispiel: Wann müssen Sie die Bestellung freigeben, damit Sie die zwanzig Edelstahlbleche für die Herstellung der Konstruktion bis zum Stichtag haben?
Es ist wichtig zu wissen, wie lange es in der Regel dauert, bis die Materialien ab dem Zeitpunkt der Bestellung eintreffen und wie lange es dauert, bis das fertige Produkt fertiggestellt ist. Um die Sache noch genauer zu machen, können Sie die Zeit einrechnen, die Ihre Mitarbeiter Ihrer Qualitätskontrolle benötigen, um das Material zu prüfen und für die Produktion oder den Versand freizugeben.
Viele der heutigen MRP- und ERP-Systeme verfügen über eine Reihe von Feldern, in die Sie diese Informationen eingeben können, und empfehlen Ihnen auf dieser Grundlage, wann Sie die Bestellung aufgeben und mit der Produktion beginnen sollten.
4. Prüfen Sie Ihre Lieferanten regelmäßig
Neben der Beachtung der Vorlaufzeiten sollten Sie auch die Transaktionen nach Lieferanten oder Artikelnummern überprüfen. Durch diese Überprüfungen können Sie die geplanten Lieferzeiten mit den tatsächlichen Lieferzeiten vergleichen. Sie können sehen, wie Ihr Unternehmen für Ihre Kunden arbeitet, und Sie können die Informationen nutzen, um Anpassungen vorzunehmen.
Noch ein Wort zu den Lieferanten: Es kann bequem sein, immer wieder dieselben Lieferanten zu beauftragen, da Sie auf diese Weise gleichbleibende Qualität und Preise erhalten. Wenn Sie eine Beziehung zu ihnen aufbauen, entsteht ein Gefühl des Vertrauens, das sowohl Sie als auch den Lieferanten beruhigt, vor allem wenn es um große Aufträge geht.
Denken Sie nur daran, dass Sie den Komfortfaktor nicht überbewerten sollten. Führen Sie regelmäßig Audits durch und überprüfen Sie die historischen Transaktionen zwischen den Anbietern. Sehen Sie sich an, wie sich die erwartete Vorlaufzeit im Vergleich zur tatsächlichen Vorlaufzeit verhält. Diese Informationen können von unschätzbarem Wert sein, wenn es darum geht, Ihren Materialplanungsprozess zu verbessern.
5. Verstehen Sie Ihre Kapazität
Es reicht nicht aus, einen Produktionsplan zu erstellen, der aus einer genauen Materialplanung, der Verfügbarkeit von Mitarbeitern und der prognostizierten Nachfrage abgeleitet wurde. Sie müssen auch die verschiedenen Produktionsgrenzen Ihrer Arbeitsplätze und den Ihnen zur Verfügung stehenden Platz berücksichtigen.
Achten Sie darauf, dass Sie die Produktionskapazitäten und den Platz in die Produktionsgleichung einbeziehen, sonst könnten Sie am Ende mit verspäteten Lieferungen oder mit mehr Beständen dastehen, als Sie lagern oder versenden können.
Wenn Sie diese Tipps beherzigen, sollte Ihre Materialplanung effektiver werden, da Sie und Ihr MRP-System genaue und zuverlässige Informationen sammeln, die zu rechtzeitigen Lieferungen und einem klareren Bild Ihres Bestands führen.
Key takeaways
- Die Materialplanung ist ein Prozess in der Fertigung, bei dem es darum geht, die in der Produktion benötigten Materialien und Mengen zu bestimmen und ihren Fluss zu steuern, um eine rechtzeitige Auftragserfüllung zu gewährleisten.
- Eine genaue Materialplanung kann eine Reihe von Vorteilen mit sich bringen, wie z.B. Kosteneinsparungen, verbesserte Effizienz der Lieferkette, rationalisierte Bestände, verbesserte Kundenzufriedenheit und verbesserte Prognosen.
- Die Materialplanung erfolgt am besten innerhalb einer Material Requirements Planning- (MRP I) oder Manufacturing Ressources Planning- (MRP II) Software.
Häufig gestellte Fragen
Es gibt mehrere Techniken und Werkzeuge, die bei der Materialplanung effektiv eingesetzt werden können, darunter Bestellpunkt, Kanban, Just-in-Time, Materialbedarfsplanung und Software für die Fertigungsressourcenplanung.
Die Faktoren, die die Materialplanung beeinflussen, sind Bedarfsprognosen, Produktionspläne, Bestandsanforderungen, Auftragsgrößen, Materialpreise usw.
Eine ERP- oder MRP-Software für die Fertigung ist ein Fertigungsmanagementsystem, das effektiv zur Verwaltung der Materialplanung sowie vieler anderer Geschäftsprozesse eingesetzt werden kann. Diese Systeme enthalten in der Regel Funktionen, die die Materialplanung unterstützen, z.B. Materialbedarfsplanung, Bestandsverwaltung, Einkauf, Produktionsplanung und Lieferantenmanagement.
Das könnte Sie auch interessieren: Materialmanagement – Beste Verfahren für kleine Hersteller