Seamless EDI Integration for MRPeasy Users: How Crossfire Streamlines Manufacturing Software and Third-Party Connections
Beyond connecting manufacturing with inventory and finances, app integration can simplify large parts of business management. In this case study, we explore Crossfire’s connection with the manufacturing ERP system MRPeasy.
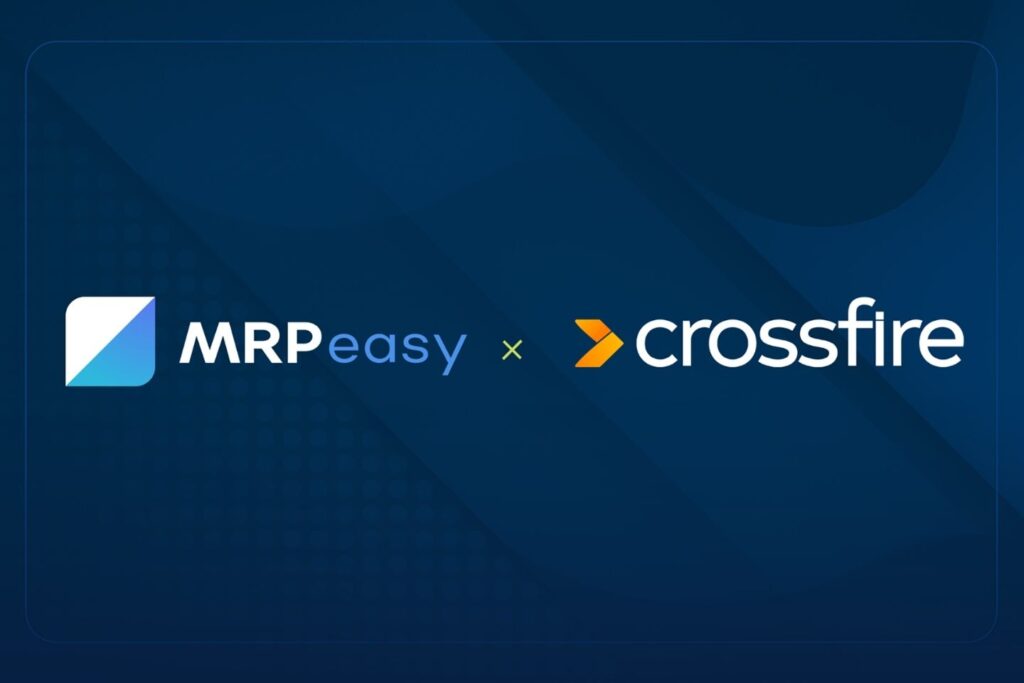
The growing need for EDI in manufacturing
A growing number of manufacturers and distributors are directly integrating their production and inventory systems with retailer, supplier, and 3PL (Third-Party Logistics) partners. Electronic Data Interchange (EDI) is becoming the new norm for automating these types of business connections. However, implementing and managing EDI connections in-house can be expensive, time-consuming, and incur considerable technical complexity. This is especially true for smaller companies with limited resources and liquidity to undertake operational innovation.
For companies using manufacturing software, integrating with external partners may require manual data entry, multiple system logins, and complying with retailer-specific protocols. Without sufficient automation, businesses risk inefficiencies and errors that can disrupt operations and slow down growth.
The challenge of manual data handling
Many manufacturing businesses, especially in the SME segment, still rely on manual processes to manage their orders, invoices, and shipping data. The trouble is that manual methods like entering purchase orders and updating inventory levels by hand, or copying and pasting data between systems, have potential downsides.
For example, data entry errors can lead to incorrect shipments or delayed payments, resulting in disgruntled suppliers and declining order fulfillment rates. Businesses may also struggle to keep up with retailer EDI requirements, which dictate how orders and invoices must be formatted or transmitted. Failing to comply can result in order cancellations or penalties and even lead to lost partnerships.
Additionally, 3PL providers and retailers increasingly require real-time updates on stock levels and shipments. Handling this information manually can lead to mismatches between inventory records, delayed deliveries, and increased operational costs. Businesses using manufacturing software for production planning stand to gain big from automated connections with external partners.
What is Crossfire?
Crossfire is an EDI & API integration service designed to take the complexity out of business-to-business (B2B) connectivity. Businesses using partnered manufacturing software like MRPeasy can use it to largely automate their connections with retailers, suppliers, and 3PLs without the need to manage complex technical integrations in-house or hire dedicated EDI staff.
Unlike traditional EDI solutions that require ongoing IT involvement, Crossfire provides an end-to-end integration service, handling setup, monitoring, and maintenance. Businesses can automate document exchanges—such as orders, invoices, and shipping notices—without worrying about compliance, mapping errors, or unexpected downtime.
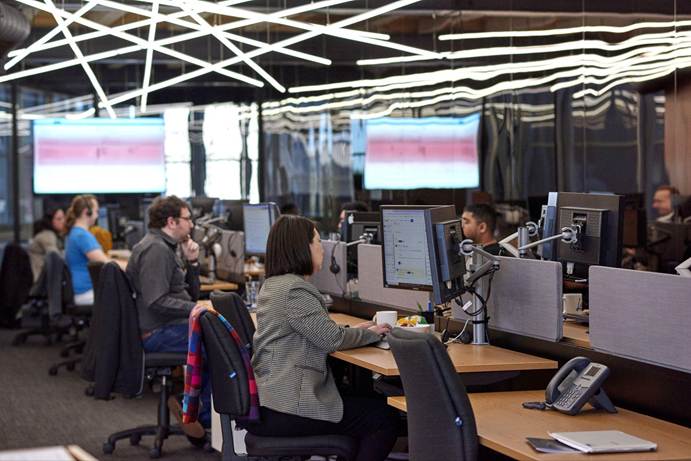
How Crossfire ensures EDI compliance
Crossfire’s fully managed service simplifies the integration process by managing all technical requirements on behalf of a business. The service includes customized setup, data transformation, and automated communication between the production software and a company’s external partners.
For manufacturers selling to large retailers, compliance is often a key concern. Many retailers impose strict EDI formatting rules, and failure to comply can easily lead to rejected orders or penalties. Crossfire handles all mapping and formatting requirements to ensure that every transaction meets the retailer’s standards. This means you no longer need to worry about EDI updates or evolving retailer requirements—Crossfire takes care of everything.
To ensure seamless operations, Crossfire provides:
- A fully-managed integration process that includes system setup, stakeholder coordination, and ongoing monitoring.
- Custom business logic and rules to match each company’s unique workflows, ensuring that data flows exactly as needed.
- Pre-built connections to thousands of global trading partners, enabling rapid deployment and scalability.
- Automatic compliance with EDI standards so businesses meet retailer and 3PL requirements without manual intervention.
Who benefits from Crossfire?
Manufacturers using MRPeasy gain a seamless, automated connection between their production software and external partners. Instead of constantly having to input order or shipping data and wrestle with bespoke requirements, these processes are largely automated, thus reducing operational overhead.
Crossfire is particularly beneficial for:
- Small and medium-sized manufacturers that need EDI compliance and want an affordable, hassle-free interface for achieving it.
- Suppliers and wholesalers working with retailers that require strict order and invoice formatting.
- Companies that integrate with 3PLs for ensuring real-time inventory updates and accurate shipping communication.
For companies experiencing rapid growth, Crossfire provides a scaling solution, ensuring smooth data flow as order volumes increase. Third party businesses also benefit as their requirements are met, allowing for trouble-free partnerships.
How do Crossfire and MRPeasy work together?
MRPeasy’s Crossfire integration automates key workflows between a company’s manufacturing system and its external partners. It eliminates manual data entry and ensures seamless data flow between systems, greatly reducing transactional issues.
Crossfire connects to MRPeasy via API and allows businesses to exchange purchase orders, invoices, shipping details, and inventory updates with their trading partners automatically. Once connected, MRPeasy users can leverage Crossfire’s extensive library of built-in connections to integrate with major retailers, logistics providers, and supply chain partners around the globe.
The integration process is handled entirely by Crossfire’s specialists, so a smooth transition is guaranteed with minimal disruption to business operations. Dedicated support teams from both software providers are available to provide ongoing assistance and ensure fast troubleshooting of any potential issues.
Real-world example of MRPeasy x Crossfire success
Companies that implement the Crossfire-MRPeasy integration can see significant efficiency gains quickly. For example, one Australian manufacturing company previously had a staff member spending three days per week on manual data entry. After integrating with Crossfire, this workload was completely eliminated, allowing the employee to focus on higher-value tasks. This ultimately led to the company securing a new high-value customer contract worth 30% of the company’s existing revenue.
Automation has an immediate impact on compliance and fulfillment speed for manufacturers working with large retailers. Companies that may have previously struggled with manually processing large order volumes now experience much faster order processing, fewer chargebacks, and improved customer satisfaction.
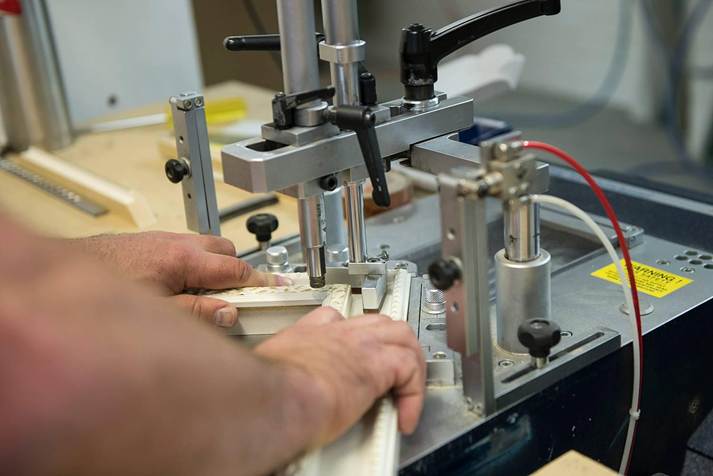
Integration directly impacts operational efficiency
For manufacturers using MRPeasy, integrating with Crossfire delivers tangible improvements in efficiency, accuracy, and scalability. By automating key workflows, Crossfire eliminates time-consuming manual tasks, reduces costly errors, and optimizes supply chain operations.
With Crossfire handling MRPeasy’s EDI and API integrations, manufacturers can ensure that their order processing, inventory management, and supplier communication run smoothly without constant oversight. Compliance with retailer and logistics requirements becomes effortless, allowing businesses to meet industry standards with less administrative burden.