What Is Cost per Unit and How to Reduce It?
Understanding your cost per unit enables you to monitor production costs, set competitive prices for your products, and increase profitability.
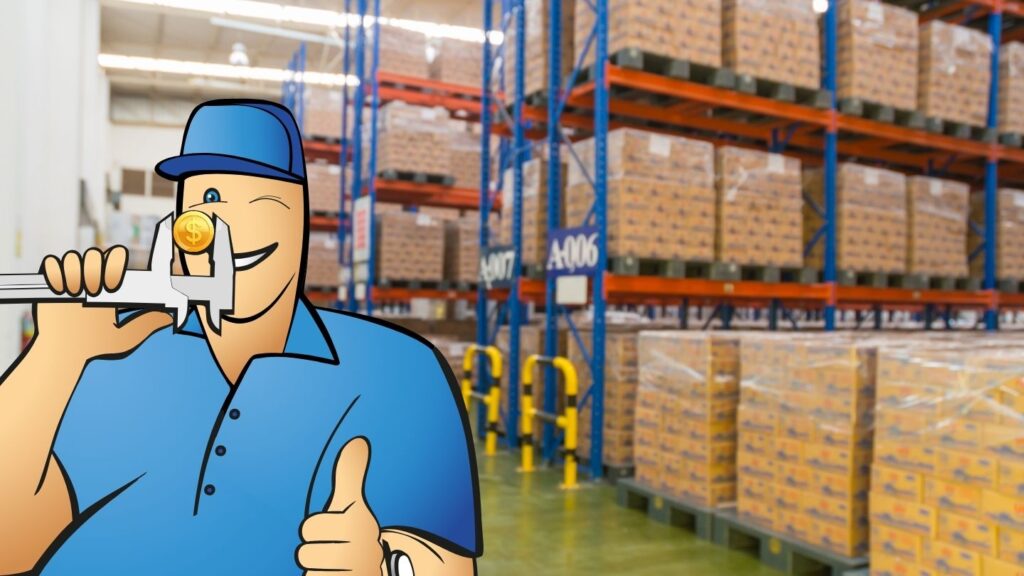
What is cost per unit?
Cost per unit refers to the total expense incurred to produce a single unit of a product. This metric is crucial for manufacturers to monitor costs, set competitive prices, and optimize production efficiency and profitability.
Cost per unit vs. price per unit
Cost per unit and price per unit are two key financial metrics that businesses use to manage profitability. While both relate to individual products, they serve different purposes—one reflects the expense of production, while the other determines revenue. I.e. while cost per unit reflects the cost incurred in producing the goods, price per unit is how much a customer pays for a unit.
Components of cost per unit
The cost per unit is determined by dividing the total production costs by the number of units produced. These production costs consist of two main components: total fixed costs and total variable costs. Understanding these components is critical for accurate unit calculation and effective cost management.
1. Total Fixed Costs
Fixed costs are expenses that do not change with the production volume. These costs remain constant whether a company produces 10 or 10,000 units. Examples include:
- Rent and insurance
- Equipment depreciation
- Salaries in case of fixed pay
Fixed costs are distributed across all units, meaning the average cost per unit decreases as production increases.
2. Total Variable Costs
Variable costs fluctuate based on the production volume. These include:
- Direct labor costs. Wages paid to workers directly involved in production.
- Material costs. Raw materials required for each unit.
- Ordering costs. Costs incurred by ordering materials, including shipping costs.
- Other variable expenses, like utilities.
As production increases, total variable costs rise, but the per-unit cost depends on the efficiency of resource use.
How to calculate the cost per unit?
As mentioned above, the cost per unit is calculated by dividing the total manufacturing cost, comprised of fixed costs and variable costs (e.g., raw materials, direct labor), by the total number of units produced:
Cost per Unit = Total Manufacturing Cost ÷ Total Units Produced
When a manufacturer produces multiple products, such as tables and chairs, calculating the cost per unit requires allocating fixed costs and accurately tracking variable costs for each product.
Calculation steps
- Identify fixed costs
Fixed costs, such as rent, utilities, and equipment depreciation, are shared among all products. These costs should be allocated based on production volume or machine hours. - Track variable costs for each product
Variable costs (e.g., material costs and labor) are specific to each product. For example, tables might require more wood, while chairs might need more labor. - Calculate total cost for each product
Combine the allocated fixed costs and variable costs for each product. - Divide total costs by units produced
For each product, divide its total cost by the number of units produced to get the cost per unit.
Example
Costs:
- Fixed costs:
- Factory rent, insurance, and depreciation: $10,000.
- Variable costs:
- Tables: Direct materials ($12,000), labor ($5,000)
- Chairs: Direct materials ($9,000), labor ($7,000)
Units produced:
- 500 tables.
- 1,000 chairs.
Step 1: Allocate fixed costs
Suppose the allocation is based on units produced:
- Tables: (500 ÷ 1,500) × $10,000 = $3,333.
- Chairs: (1,000 ÷ 1,500) × $10,000 = $6,667.
Step 2: Calculate total costs
- Tables: Fixed Costs ($3,333) + Variable Costs ($17,000) = $20,333.
- Chairs: Fixed Costs ($6,667) + Variable Costs ($16,000) = $22,667.
Step 3: Calculate Cost per Unit
- Tables: $20,333 ÷ 500 = $40.67 per table.
- Chairs: $22,667 ÷ 1,000 = $22.67 per chair.
Benefits of tracking the cost per unit
Tracking unit costs gives manufacturers crucial insights to improve profitability and maintain a competitive edge. Here are the key benefits:
Cost optimization
Analyzing the actual cost of production at a granular level reveals inefficiencies and changes, such as high labor expenses or increasing material costs. This provides you with the opportunity to negotiate with suppliers or identify areas for process improvement.
Streamlined operations
Tracking unit costs allows manufacturers to assess and optimize production processes, ensuring efficiency and minimizing waste. This could translate directly into a reduction in labor and material costs.
Improved pricing strategy
Understanding the cost per unit enables businesses to set a selling price that ensures a healthy gross profit. By accurately factoring in manufacturing overhead costs, material costs, and other components of the cost of goods sold, manufacturers can avoid underpricing or overpricing products.
Profitability analysis
By tracking unit costs, businesses can evaluate the profitability of their operations. Comparing the selling price per unit to the production cost per unit helps in identifying which products are profitable and which need adjustments.
Break-even point identification
Calculating the cost per unit aids in determining the break-even point. This is essential for forecasting sales targets and understanding when a business will start generating profit.
Informed decision-making
Monitoring unit costs empowers manufacturers to make informed decisions about production processes, pricing, and investments. This data helps identify cost-saving opportunities and informs strategies for achieving economies of scale.
How to reduce your cost per unit
Reducing your costs per unit is a key strategy to increase profit margins and remain competitive in the market. Here are some effective ways to achieve this:
1. Negotiate volume discounts
Purchasing materials in bulk can significantly lower costs. Suppliers often offer volume discounts for large orders, allowing businesses to reduce the cost of raw materials. However, this strategy must be balanced with proper inventory control to avoid overstocking.
2. Source more affordable materials
Evaluate your raw material suppliers and explore alternative sources that offer the same quality at a lower cost. Look for local suppliers to reduce shipping costs or consider alternative materials that maintain product integrity while being more cost-effective. However, ensure that any cost-saving measures do not compromise quality, as this could lead to higher production defect rates and increased product returns.
3. Streamline production processes
Evaluate your production workflow and look for inefficiencies that can be eliminated. Automating repetitive tasks, reducing bottlenecks, and improving order fulfillment processes can cut down labor and operational costs.
4. Reduce your defect rate
A high defect rate leads to increased direct labor costs, wasted materials, and additional expenses related to rework or product replacements. Implementing quality control measures at multiple stages of production can help catch defects early. Investing in better equipment, improving worker training, and refining manufacturing techniques can significantly lower defect rates. Lower defects mean fewer returns, better customer satisfaction, and reduced production waste—leading to a lower cost per unit.
5. Reduce material waste
Material waste can result from inefficient cutting, excess accumulation of raw materials, or poor planning. To streamline material use, manufacturers can optimize production layouts, use precision cutting tools, and find ways to repurpose leftover materials. Implementing real-time monitoring can help identify areas with excessive waste.
6. Improve supply chain efficiency
Collaborating with suppliers and logistics providers can help reduce shipping and material costs. Choose lower cost freight options if you can—although these usually come with longer lead times, proper planning can help you manage. For e-commerce businesses, improving packaging efficiency and negotiating better shipping rates can also reduce unit costs.
7. Increase production volume
Producing more units can spread fixed costs (like rent and equipment) over a larger output, reducing the cost per unit. However, this requires careful planning to ensure that demand supports increased production.
Managing your cost per unit with manufacturing ERP
Manufacturing ERP software helps businesses track and manage costs efficiently, ensuring that the cost per unit remains under control. By integrating different aspects of production, inventory, and financial management, ERP systems help manufacturers streamline operations and lower costs. Here’s how:
1. Real-time cost tracking
ERP software provides real-time visibility into unit costs in addition to material costs, labor expenses, and overhead costs, helping manufacturers monitor and adjust spending. This prevents cost overruns and allows for more accurate pricing decisions.
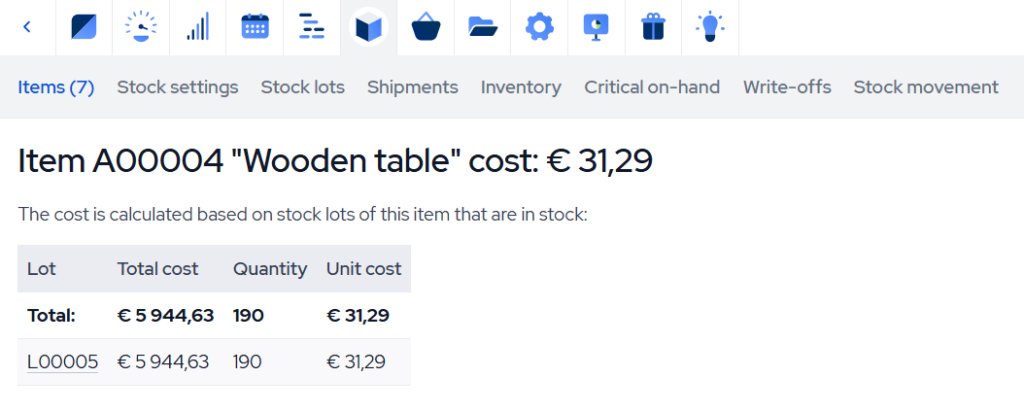
2. Optimized inventory management
Holding excess raw materials or finished goods leads to high warehousing and holding costs. ERP systems help businesses maintain the right inventory levels by tracking stock in real-time, reducing unnecessary storage expenses and minimizing material waste.
3. Efficient production planning
By optimizing production schedules, ERP software ensures that resources like labor and materials are used efficiently. This reduces machine downtime, eliminates bottlenecks, and improves workflow, leading to lower per-unit costs.
4. Automation of manual tasks
ERP software automates key processes such as order fulfillment, purchasing, and reporting, reducing reliance on manual labor. This helps minimize direct labor costs and ensures that operations run smoothly with fewer errors.
5. Supplier and procurement cost optimization
Manufacturers can leverage ERP tools to negotiate better volume discounts and compare supplier pricing. This helps secure the best deals for raw materials and shipping, ultimately lowering cost per unit.
6. Reduction of defects and waste
ERP systems support quality control by tracking defect rates and ensuring compliance with production standards. By reducing rework and material waste, manufacturers save costs and improve overall efficiency.
7. Data-driven decision-making
With access to financial statements and performance reports, manufacturers can analyze cost trends and make informed decisions to improve profitability. ERP software helps businesses quickly identify areas where costs can be cut without sacrificing quality.
Key takeaways
- Cost per unit refers to the expense of producing one unit of a product, while price per unit is the amount a customer pays. Businesses add a profit margin to the cost per unit to determine the selling price.
- The cost per unit consists of fixed costs (e.g., rent, equipment depreciation) and variable costs (e.g., raw materials, labor). Managing both effectively helps manufacturers lower costs and improve financial stability.
- Monitoring unit costs helps manufacturers optimize production, set the right pricing strategy, and analyze profit margins. It also enables better decision-making regarding product profitability and sales goals.
- Businesses can reduce their cost per unit by negotiating volume discounts, sourcing affordable materials, streamlining production, reducing defects and material waste, and improving supply chain efficiency.
- Manufacturing ERP software provides real-time cost tracking, improves inventory management, automates order fulfillment, and helps businesses optimize supplier negotiations to reduce costs and maximize efficiency.
- Regularly reviewing financial statements and cost trends helps businesses identify areas for improvement. By leveraging ERP systems and continuous process optimization, manufacturers can achieve long-term cost savings while maintaining product quality.
Frequently asked questions (FAQ)
When production increases, fixed costs (like rent and equipment depreciation) are spread over more units, lowering the cost per unit. However, if production decreases, fixed costs are allocated to fewer units, causing CPU to rise. Variable costs per unit remain stable unless bulk purchasing reduces material costs.
Cost per unit only accounts for production expenses and doesn’t include holding costs, shipping, marketing, and administrative expenses. To ensure profitability, businesses must calculate the total cost per product and add a profit margin before setting a price.
A high CPU can reduce profit margins or make pricing uncompetitive.
You may also like: What Is Job Costing and How to Get It Right?