How to Calculate the Cost of Goods Manufactured (COGM)?
Knowing the cost of goods manufactured is vital for a good overview of production costs and how they relate to the bottom line. COGM also allows management to identify cash drains, adjust prices, and track the development of the business.
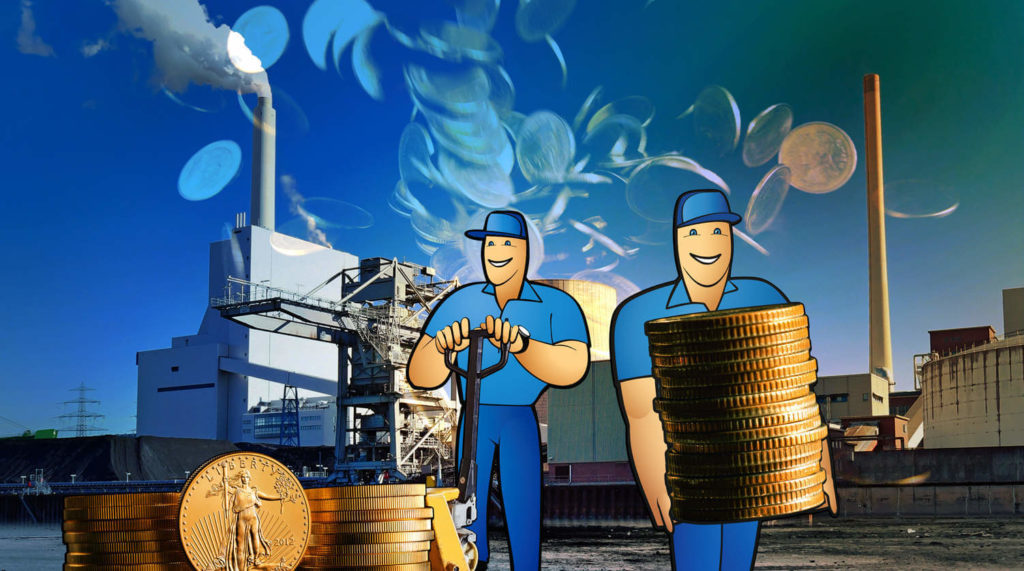
You can also listen to this article:
What is the cost of goods manufactured?
The cost of goods manufactured (COGM) is a financial metric that depicts the total expenses a manufacturing business incurs when producing finished goods. Situated on a company’s income statement, COGM adds up all costs associated with manufacturing finished products including both direct (raw materials and labor) and indirect costs (manufacturing overheads).
COGM does not include general business expenses like utilities or marketing fees – only those associated with the manufacturing process. Unlike the closely related key performance indicator, the total manufacturing cost (TMC), COGM excludes the cost of goods that were not finished at the end of a time period – these constitute the ending work in process (WIP) inventory.
Keeping an eye on COGM is important because it enables manufacturers to scope the expenses involved with producing goods, analyze the profitability of their operations, and also calculate the cost of goods sold (COGS) KPI. While accountants can approximate its value at the end of fiscal periods, modern inventory and manufacturing software calculates COGM in real-time, based on actual manufacturing data.
The cost of goods manufactured formula
Calculating the cost of goods manufactured entails adding together all direct and indirect costs associated with manufacturing, and also factoring in changes to the work in process (sometimes also referred to as work in progress), or WIP inventory. This means that finding COGM entails knowing the total manufacturing cost (TMC) of the manufacturing operation, as well as the WIP inventory values for the beginning and end of the accounting period.
The COGM formula is therefore:
Cost of goods manufactured = Beginning Work in process inventory + Total manufacturing cost – Ending Work in process inventory
Let us delve a bit deeper into the metrics that make up COGM: the total manufacturing cost and work in process inventory.
Total manufacturing cost
Total manufacturing cost, a.k.a total cost of production, is a KPI that expresses the total cost of manufacturing, e.g., all activities directly tied to the production of goods during a financial period. It’s very similar to the cost of goods manufactured except that it doesn’t factor in work in process.
Manufacturing costs fall into three main categories. These are:
- Cost of direct materials. These are the physical materials and components that the finished goods will be manufactured from. The direct material costs comprise the values of the beginning existing and procured raw materials for an accounting period, minus those that are unused by the end of the period.
- Direct labor costs. This means all labor expenses of people directly dealing with production activities. This includes the salaries, holidays, sick leave, etc., of the shop floor workers. Direct labor does not include the payroll costs of other staff of the company such as janitors, accountants, management, etc.
- Manufacturing overhead. Also known as factory overhead or indirect manufacturing costs, these are expenses not directly tied to creating the finished products that are still required for the production process. It comprises indirect materials used in production that aren’t necessarily part of the product (e.g. glue, sandpaper, lubricants, etc.), indirect labor costs such as the payroll of supervision, quality control, management, etc., not directly responsible for the production of goods but without whom production would not happen, premises and equipment depreciation, rent or property taxes, and insurance.
Total manufacturing cost = direct materials + direct labor + manufacturing overhead
Read more about Total manufacturing cost.
Work in process inventory
The other half of the COGM formula accounts for the work in process or WIP Inventory. WIP is a current asset in the company’s balance sheet and represents the total value of all materials, labor, and overhead of unfinished products.
WIP is usually calculated at the end of accounting periods. The beginning WIP is the value of all unfinished products that carried over from the previous accounting period. The ending WIP, on the other hand, comprises the remaining manufacturing costs after deducting the value of goods finished within the period.
Most manufacturers strive toward minimizing the ending WIP as it frees up capital, deflates the tax burden, and crucially, makes accounting much easier. If WIP is zero then TCM equals COGM. Manually finding the precise WIP value is also complicated because overhead margins, taxes, etc., need to be calculated per unfinished work orders. In practice, most modern manufacturers use MRP software with perpetual inventory systems that calculate WIP automatically and continuously.
Read more about Work in Process Inventory Accounting.
Example
Let us look at an example of the COGM calculation for a furniture manufacturer. The company has $5,000 worth of furniture in the making at the start of the fiscal quarter. This is the beginning WIP Inventory.
The raw materials inventory is valued at $8,000 and is replenished with another $5,000 worth of stock within the quarter. At the end of the period, $3,000 worth of stock remains as raw materials. Therefore, direct material cost is $8,000 + $5,000 – $3,000 = $10,000
The company employs eight shop floor workers – they constitute the direct labor. Let’s say their payroll comes in at $30,000.
The manufacturing overhead for the business comes in at $13,500, comprising of indirect labor costs for maintenance and warehouse ($9,000), additional materials such as glue and sandpaper ($800), rent ($3,000 per quarter), insurance ($200 per quarter), and an equipment depreciation of $500 per quarter.
The total manufacturing cost for the quarter is the sum of the three above cost articles: $10,000 + $30,000 + $13,500 = $53,500.
At the end of the quarter, $8,500 worth of furniture is still unfinished as calculated by the MRP system. This is the ending WIP Inventory.
The cost of goods manufactured is, therefore, $5,000 + 53,500 – $8,500 = $50,000.
Cost of goods manufactured VS total manufacturing cost VS cost of goods sold
As we have seen, the total manufacturing cost and cost of goods manufactured are very similar metrics. Their only real difference is that COGM sums up the part of a company’s production efforts that is marketable, i.e. finished goods, whereas TMC tallies up all manufacturing-related expenses, regardless of their status at the end of an accounting period.
Another closely related KPI crucial in manufacturing accounting is the cost of goods sold or COGS. Whereas COGM depicts the costs of producing all finished goods, COGS only takes into account the costs of producing goods that were sold within the same accounting period. This is important from an accounting point of view as it pinpoints the expense that a company needs to recover per sold product in order to break even.
Essentially, COGS is to finished goods inventory what COGM is to WIP inventory. The metric can be calculated by summing together the value of the beginning finished goods inventory, if any, and the cost of goods manufactured before deducting the value of the ending finished goods inventory, i.e., unsold merchandise at the end of the accounting period.
Continuing with the above example, if the company had $10,000 worth of finished goods in stock at the beginning and $5,000 worth of finished goods in stock at the end of the quarter, and COGM is $50,000, then the cost of goods sold would be $10,000 + $50,000 – $5,000 = $55,000. This can then be divided by the number of sold goods to arrive at cost per unit.
Read more about Calculating the Cost of Goods Sold in Manufacturing.
The importance of COGM
The cost of goods manufactured is an important KPI to track for several reasons. It’s not just a good way of getting a general overview of production costs and how they correspond to the profitability of the business; it also enables calculating the cost of goods sold, which is necessary for calculating gross margin and net income.
More than a financial metric, COGM is an essential management tool that provides valuable insights into the efficiency and effectiveness of a manufacturing company’s operations. Here are 6 reasons why tracking COGM is crucial for manufacturers:
- Understanding Manufacturing Costs: COGM helps manufacturers get a clear picture of the costs associated with producing their goods. By breaking down raw material, labor, and overhead costs, manufacturers can better understand where the bulk of their expenses lie.
- Profitability Analysis: By subtracting COGM from sales revenue, businesses can determine gross profit and assess the overall profitability of their manufacturing process.
- Price Determination: COGM plays a significant role in determining the price of a product. A clear understanding of it helps to ensure that the product pricing covers all the manufacturing costs and leaves a margin for profit.
- Cost Control: Continuously monitoring COGM enables identifying areas where costs may be rising and taking corrective action. This could involve negotiating better prices with suppliers, improving production efficiencies, or reducing waste.
- Inventory Management: COGM directly influences the value of finished goods inventory. By tracking COGM, companies can keep an eye on inventory levels and manage them more effectively, avoiding overstocking or stockouts.
- Performance Benchmarking: COGM can be used as a benchmark to compare performance over different periods or against industry standards or competitors. This can inform strategic decisions and guide improvements in the manufacturing process.
Read more about Important Manufacturing KPIs.
COGM in a manufacturing ERP
Calculating COGM is possible manually or using basic Excel templates. However, production software such as a capable manufacturing ERP system continuously tracks all manufacturing costs and inventory movements and calculates both COGM and COGS automatically. This means that a company need not wait until the end of accounting periods to find out these crucial financial metrics. It also means that approximate calculations are replaced by real, data-based numbers, increasing the accuracy of financial statements.
The perpetual inventory system provided by modern manufacturing software eliminates big chunks of arduous work from accounting while also reducing or negating data entry errors. In addition, more capable solutions have built-in integrations with financial software such as Xero or Quickbooks, enabling automation of financial data and hugely simplifying purchase and sales order management.

Key takeaways
- The cost of goods manufactured (COGM) is a financial metric that depicts the total expenses a manufacturing business incurs when producing finished goods.
- COGM does not include the manufacturing costs of goods that were left unfinished by the end of a financial period. These are, however, included in the total manufacturing cost (TMC) KPI instead.
- Calculating the cost of goods manufactured entails adding together the values of the beginning work in process (WIP) inventory and the total manufacturing cost, and deducting the value of the ending WIP inventory. If there is no WIP inventory left by the end of the period, TMC = COGM.
- Tracking COGM is important for better understanding and controlling manufacturing costs, setting profitable price levels, inventory management considerations, and benchmarking financial performance.
- Manufacturing software such as MRP systems include perpetual inventory systems which help businesses track their manufacturing costs and calculate various KPIs like COGM automatically.
Frequently asked questions
The cost of goods manufactured (COGM) can be calculated by adding together the value of the beginning work in process (WIP) inventory and the total manufacturing cost (direct material and labor costs plus manufacturing overhead costs) for the accounting period, and deducting the value of the ending WIP inventory, if any.
The difference between the cost of goods manufactured (COGM) and the cost of goods sold (COGS) is that whereas the former tallies up the total costs incurred with manufacturing all finished products for an accounting period, the latter only includes the costs of manufacturing those goods that the company also managed to sell within the same period.
The cost of goods manufactured is included in a company’s income statement, usually together with the beginning and ending finished goods inventories. It’s used also for calculating the cost of goods sold.
You may also like: How to Calculate the Selling Price of Your Products?