Configurable BOM (CBOM) – Simplifying the Production of Customizable Items
Configurable BOMs enable companies to easily plan the manufacture of products with variations. Here is how they work and how they help.
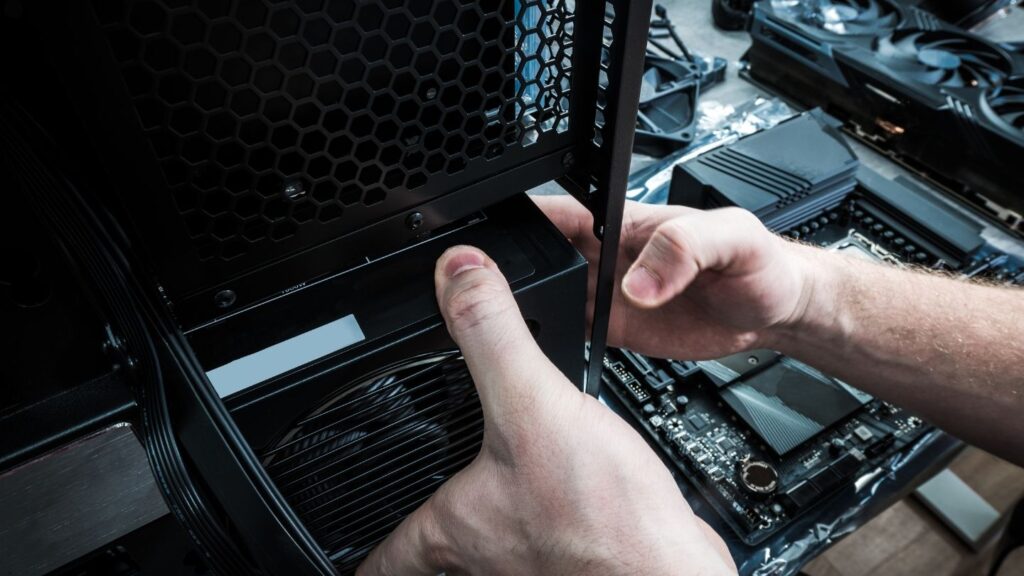
What is a configurable BOM (CBOM)?
A configurable bill of materials (also called a matrix BOM or a BOM with parameters) is a production planning tool that allows manufacturers to customize products to meet the requirements of individual customers. It enables manufacturers to create different product versions by choosing various options or configurations, e.g., for different colors, sizes, materials, or performance.
Configurable BOMs drastically simplify production planning and the management of product variations by eliminating the need for separate BOMs for each variant.
For example, a laptop manufacturer can use a core BOM with some components that are uniform in all variants of the model like the chassis, keyboard, and the screen, but provide options such as:
- 8 GB or 16 GB RAM
- 2.5 GHz or 3.5 GHz processor
- 256 GB or 512 GB solid-state drive
Providing these three choices already means that the laptop model has eight different possible configurations. With a configurable BOM, the laptop manufacturer doesn’t need to create separate bills of materials for each configuration. Instead, there would be a single BOM where these parameters could be changed to generate a manufacturing order with the correct configuration automatically.
Benefits of configurable BOMs
Configurable BOMs can significantly improve your production planning and management efficiency. Here’s how:
Less data entry
Instead of creating a separate BOM for each product variant, a configurable BOM allows you to enter data once for all possible configurations, reducing the amount of manual data input.
Reduced errors
With fewer BOMs to manage and the ability to handle multiple product variations within a single framework, there’s less chance of miscommunication or selecting the wrong BOM, leading to more accurate production planning and fewer errors.
Easier BOM updates
When components change, or new options are added, you only need to update the configurable BOM once, and it will automatically apply to all related product configurations. This simplifies BOM management and ensures all versions are up to date.
Reduced costs
Using configurable BOMs reduces your administrative workload, minimizes the need for extensive manual updates, and lowers the likelihood of costly production errors. This translates into noticeably reduced costs.
Improved analytics
With all product configurations managed within a single BOM, it becomes easier to analyze trends and track performance across different product variants. For example, if a specific product variant is ordered frequently, you can decide whether to include it in your standard product catalog.
Faster sales process
Using configurable BOMs also streamlines the sales process. With quick configuration, your sales team can provide quotes faster and reduce errors in pricing or component selection. By tying the BOMs to your online store, you can enable customers to configure their own products, which are then automatically converted into accurate purchase orders or manufacturing orders.
Satisfied customers
Customers love customizing their products. Configurable BOMs allow manufacturers to offer a wide range of customization options without complicating the customer journey or the production planning process. In addition, customers are often willing to pay more for more personalized goods.
Managing configurable BOMs in spreadsheets
Managing configurable BOMs in spreadsheets involves creating a master sheet that lists the core product components and possible configurations. You can manage various options by using drop-down menus, formulas, and filters. The steps include:
- Create a table with columns for core components, configurable options, quantities, and prices.
- Set up drop-down menus for options like size, color, or material to easily select configurations.
- Use formulas to automatically calculate total costs, quantities, or other data based on the selected configuration.
- Track each unique combination in separate rows or sheets.
While spreadsheets can handle basic configurations, managing complex products with many variations can quickly become unwieldy and error-prone.
Managing configurable BOMs in MRP software
MRP software is a better alternative to managing configurable BOMs as it automates a large part of the process, providing scalability and real-time updates, and reducing errors. In addition, an MRP system integrates your BOMs with your inventory, sales, production planning and scheduling, procurement, and finances, making it much easier to manage your whole operation. Here’s a step-by-step guide on how to set up a configurable BOM in MRPeasy:
1. Enable the matrix BOM feature
First, ensure that the Matrix BOM feature is enabled in your MRPeasy account. This feature is available in the Professional plan and can be activated under Settings → System Settings → Professional Functions → Matrix BOM.
You can also enable various advanced settings such as auto-creation of variants, different identification settings, and variable selling prices for different variants.
2. Configure the parameters
When the matrix BOM functionality is enabled, parameters and relations become available in your stock settings. Start by defining the different parameters and their values, which are usually based on key attributes such as size, color, or material.
3. Set up relations
If a parameter’s value changes the materials or components used in the production of the item, you need to also define the relations that tie each value to a corresponding stock item. For example, the value “small box” could be tied to item #A-01 small carton 10x10x10, the value “medium box” to #A-02 medium carton 20x20x20, etc.
If some parameter modifies the quantities of raw materials, then extra columns appear in the BOM for entering the corresponding quantity for every parameter value.
4. Add parameters to the item
Open the item details and select the configurable parameters that apply to this item.
5. Select the allowed variations
After configuring the parameters, the subsection Variations appears on the item details page. There, you can select the combinations that are made available to customers.
6. Add the BOM to the item
First, add all the universal parts common to all item variations. Then, add the relations that connect parameter value selections with specific parts. Lastly, if some parameters modify quantities of parts or materials, fill in all the quantity columns appropriately.
6. Create the routing
Lastly in the BOM creation process, specify the sequence of the actual manufacturing process as usual. The routing will be shared among all variations of the product.
7. Test the configurable BOM
Once your configurable BOM is set up, test it by creating a mock order and selecting different configurations. MRPeasy will generate the correct BOM for the specific variant chosen, allowing you to ensure that the right components and quantities are used.
8. Use multi-level configurable BOMs for complex products
A robust MRP system with both product configuration and multi-level BOM functionality allows you to simplify the management of products with hundreds of configurable subassemblies. If your product consists of configurable subassemblies that consist of other configurable subassemblies, it is a recipe for disaster when managed in spreadsheets. MRP software like MRPeasy reduces the administrative load related to these products substantially.
Watch this short demo video about how configurable BOMs work in MRPeasy:
Configurable BOM best practices
Although configurable BOMs have the power to enormously simplify your processes, make sure to follow these best practices to get the best result.
Use integrated software
Use MRP or ERP software to manage configurable BOMs rather than spreadsheets or a standalone product configurator. Integrated software automates the process, links directly to inventory and production, and reduces manual errors, making handling complex configurations and large numbers of product variations easier.
Don’t enable configurations where not needed
Only offer configurations where they add value to the customer or the product. Unnecessary options can complicate production, lead to higher costs, and confuse both the manufacturing team and customers. Focus on offering meaningful variations that meet market demand. Make sure to standardize as much of your core product as possible!
Think the configurations through
Plan configurations carefully by considering the entire production process. Ensure that all possible combinations are feasible from a manufacturing and performance perspective and avoid incompatible options. For example, a computer manufacturer should avoid pairing a high-performance processor with insufficient cooling or a low-capacity battery.
Regularly review configurations
Periodically audit and update the available configurations to ensure they reflect current market trends, material availability, and technological advancements. Remove obsolete options and introduce new ones to keep your product portfolio and BOMs relevant and efficient.
Keep costs under control
Monitor how different configurations affect costs. Some customizations can significantly increase expenses related to materials or labor, so be mindful of how each configuration impacts the overall production budget. Aim to balance customer choice with cost-effective production.
Simplify the customer-facing side
When offering configurable products to customers, present choices in a clear, user-friendly way. Too many options can overwhelm customers, so focus on the most important selections that align with customer needs and your production capabilities. In addition, integrate your configurable-BOM-enabled MRP software with your e-commerce platform to link customer orders directly to production planning.
Key takeaways
- A configurable BOM (CBOM) allows manufacturers to efficiently handle product variations without needing separate BOMs for each variant.
- Instead of managing multiple BOMs for different versions, you input core data once and simply adjust configurations, saving time and reducing the potential for errors.
- Automating configurations with CBOMs reduces administrative workload, cutting down on manual processes and lowering costs associated with production mistakes.
- Configurable BOMs streamline sales by allowing quick product configuration and pricing, enabling faster quotes and improving customer satisfaction.
- Updating a configurable BOM automatically applies changes across all product variants, ensuring that all configurations are up-to-date with minimal effort.
- Managing CBOMs with integrated MRP software enables seamless coordination between inventory, production, and sales, further improving efficiency and scalability.
Frequently asked questions
Focus on configurations that align with customer demand and product functionality. Conduct market research and consult with sales and production teams to identify which options are popular and feasible to produce. Avoid offering configurations that add complexity without improving the customer experience or product performance.
Periodically audit BOMs by analyzing sales data and production efficiency to identify outdated configurations or components. Incorporate feedback from customers and your production team to adjust options based on market trends and available materials, ensuring the configurable BOM evolves with both customer needs and operational capabilities.
When integrated with an e-commerce platform, a configurable BOM allows customers to customize products directly online, with their selections automatically sent to your MRP software. This improves the customer experience by offering real-time customization while streamlining order processing and production planning.
You may also like: What Is Configure, Price, Quote (CPQ)?