How to Communicate Effectively in a Manufacturing Company?
An exchange of information is necessary to trigger any kind of action and as such, communication is an essential part of any manufacturing business. Improving your communication process and practices can therefore have a significant effect on the efficiency of your business.
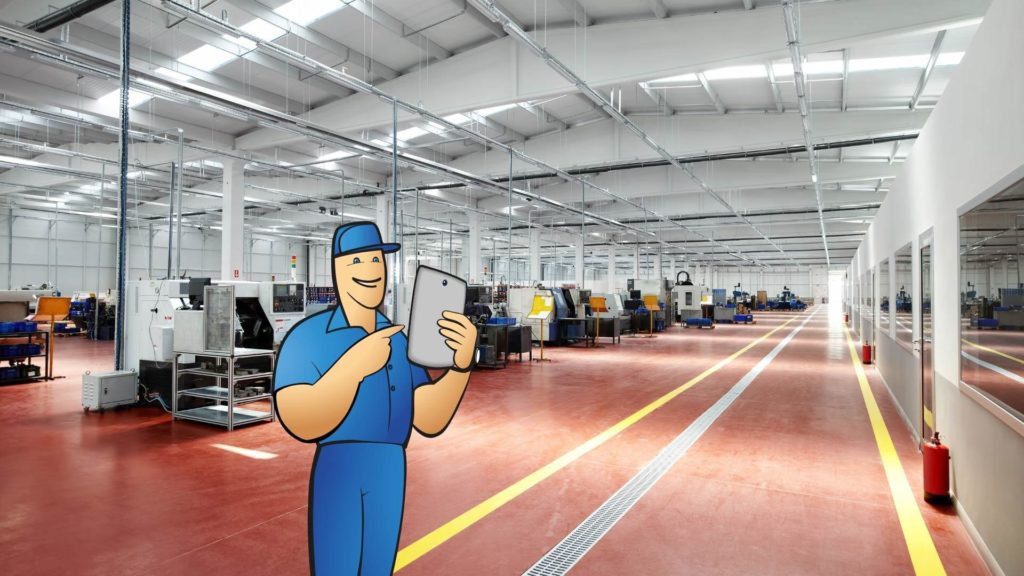
You can also listen to this article:
What is communication in manufacturing?
Manufacturing communication is the exchange of information pertaining to the manufacturing process between any two parties that are part of the supply chain of a manufactured product. This includes contacts with suppliers and customers as well as interactions between departments and employees within the manufacturing company.
Communication is inevitable. In any business, people have to exchange information to get anything done, e.g. by putting in an order or sending out a production schedule. But even though communication is the basis and lifeblood of any business, many manufacturing companies could do with improving their communication practices.
More effective exchange of information could lead to very real benefits, such as fewer workplace accidents, better production efficiency, higher product quality, and greater customer as well as employee satisfaction.
On the other hand, sub-par communication practices, especially those that rely on oral and paper-based methods, could result in poor working conditions, excessive waste, low product quality, late deliveries, and dissatisfied customers and employees
Why is communication important in manufacturing?
Effective communication in manufacturing is crucial for a variety of reasons:
- Workplace safety. Manufacturing environments can be high-risk settings, with potential dangers including heavy machinery, hazardous substances, and more. Clear communication can help to ensure safety procedures are understood and followed, preventing accidents and injury.
- Efficiency. Clear instructions and updates can significantly boost productivity by ensuring everyone knows what they’re supposed to be doing, when, and how. This can help to reduce downtime, eliminate wasted effort, and speed up the production process.
- Quality control. Manufacturing is often done according to precise specifications. Miscommunication or misunderstanding can lead to errors, resulting in waste and possibly harm to the company’s reputation. Clear communication helps ensure high-quality output.
- Teamwork. Manufacturing often involves collaboration across multiple departments, from design to production to distribution. Good communication can enhance teamwork and ensure that all departments are aligned with each other.
- Customer satisfaction. Good communication ensures that customer specifications and requirements are understood and met. It also helps in promptly addressing any concerns or complaints, thereby increasing customer satisfaction and loyalty.
- Supplier relationships. Communication with suppliers is also vital in manufacturing to ensure timely delivery of materials, negotiate contracts, and resolve any issues or disputes.
- Problem-solving. Problems are inevitable in any industry, and manufacturing is no exception. Effective communication helps in identifying, discussing, and solving these problems promptly and efficiently.
- Regulatory compliance. Clear communication helps ensure that all employees understand and comply with the industry regulations and standards, thus preventing legal issues and penalties.
Therefore, investing in good communication strategies and tools can have a substantial impact on a manufacturing company’s success.
How to improve communication in manufacturing?
There are several direct and indirect ways to improve communication in a manufacturing company. From encouraging social interactions to providing an infrastructure for the exchange of information, here are some approaches that help you build a more tightly connected business.
Provide training
Training related to safety as well as new technologies and machinery implemented in the facility is a must for all involved parties. But more training is not always better training. Training sessions should be clear, focused, and concise and the lessons learned should later be ingrained with the help of supplementary materials handed out to the employees, attached to the walls near the equipment, and added to instruction folders. An efficient way to improve the onboarding of new employees is to assign them a seasoned partner that could help them learn while also bringing them into the company culture.
Create common areas
Common areas in the facility such as a dining hall or a kitchen serve another purpose other than the obvious. These are the places where people whose work does not directly overlap meet and socialize. Various departments convene in these rooms to interact and discover new perspectives through discussions. Not only do common areas facilitate team spirit, they also act as incubators for fresh ideas that could lead to improvements.
Organize events
Teambuilding events are a great way to improve and strengthen relationships at the workplace. Giving employees a chance to interact outside of the work routine allows them to form deeper connections which can improve team spirit, communication at the workplace, and consequently, their work efficiency. But events can also be held with suppliers and customers for the exact same reason. Having more casual interactions with your suppliers and customers can strengthen your important relationships and often help you discover areas that could be improved and new ideas that could be implemented.
Meet regularly
Meeting regularly does not mean meeting whenever possible. There have been so many meetings that could just as well have been an email or a text message. But regular meetings should not be shunned. In fact, a weekly team meeting is still a great way to catch up, provide updates, and coordinate activities.
Use shop floor reporting
The most important production-related insights come from the shop floor and it is a manufacturing mortal sin not to gather this data. The basic things workers should report are labor or machine time (i.e. the time worked on an order/product), consumed materials, and finished products. These three types of reports allow you to give feedback to shop floor managers and workers as well as calculate production costs, overall equipment effectiveness (OEE), worker productivity, and many other important metrics that can help you improve the efficiency of your operation.
Create a communication infrastructure
The best thing you can do for maximum communication efficiency, however, is to build a logical and effective communication infrastructure that integrates your whole business and standardizes the communication process.
- Create communication SOPs. Define a chain of command, the people in charge of specific types of issues, which channels of communication to use with various levels of urgency, etc.
- Use visual cues and instruction print-outs. Mark different areas and different types of inventory, put up signs and safety placards, use tape to create movement corridors on the floors, put up instructions near machinery, etc. Good factory floor and warehouse organization always facilitates effective communication.
- Implement software. There are different types of software with various degrees of complexity that can significantly improve communication in the workplace. From simple messaging apps to cloud-based document-sharing platforms to full-fledged cloud-based ERP systems, having easily accessible real-time information about what is going on in the business gives you and your employees a chance to act with unseen efficiency.
Although SOPs and visual cues have been business communication staples for ages, software is also quickly becoming indispensable in the modern small manufacturing landscape.
Useful apps for improving communication in manufacturing
Software selection and implementation are always a pain. With so many available options, it is getting more and more difficult to find the needle in the haystack – software that fits your company. First, it is important to map out in detail what you need in the software. This allows you to determine which type of solution you need. Here are the basic types of software used for improving communication in manufacturing:
Email and messaging apps
Emails and messaging apps are a simple and effective way to communicate with your team. Email can be used to send documents, production schedules, meeting agendas, etc. Messaging apps, however, can be used to convey more urgent information such as last-minute changes or delays. These types of apps send notifications to the recipients’ smartphones so they can be alerted within seconds. Messaging apps are also good for casual team conversations and many of them also support voice and video calls.
Examples: Skype, Facebook Messenger
Collaborative apps
Collaboration apps take one step further from simple messaging and can also be used to share and edit documents, manage projects, create and track tasks, and much more. People can be assigned to teams that can use their private messaging channel for communication while general topics can be discussed in larger groups. These apps most often also have mobile support so that employees can receive notifications on their smartphones about new tasks or messages.
Examples: Slack, Google Workspace
Manufacturing ERP systems
MRP and ERP systems have become the foundational part of the operations of many manufacturing companies today. These systems are designed for real-time exchange of information related to every vital part of an organization: customer orders, inventory, production planning, material requirements, purchases, finances, team management, etc.
This type of software is typically a tightly-woven network of information, where a small input can reverberate or pull information throughout the system to produce, for example, production costs and lead times for new customer orders, production schedules with recently added manufacturing orders, statistics for important insights about your efficiencies, and much more. Some ERP/MRP systems also allow you to add attachments and notes to workstations and orders to convey extra information and instructions.
Users can also be assigned user rights so that the sales team can only access the CRM, the purchasing department can only see data related to procurement or inventory, shop floor workers can only access their personal production schedules and the reporting module, and so forth.
Having this accurate real-time information only a click away allows your employees to always be up-to-date regarding data pertaining to their jobs. Inventory planners can see the material requirements for a certain period, production planners can instantly create accurate schedules, and salespeople can compile quotes with accurate price and lead time estimations within minutes. In a nutshell, everything happening in the company can be tracked and reviewed within one simple system, making vital communication within the company as well as with customers and suppliers lightning-fast.
Key takeaways
- Manufacturing communication is the exchange of information pertaining to the manufacturing process between any two parties that are part of the supply chain of a manufactured product.
- More effective exchange of information could lead to very real benefits, such as fewer workplace accidents, better production efficiency, higher product quality, and greater customer as well as employee satisfaction.
- Sub-par communication practices could result in poor working conditions, excessive waste, low product quality, late deliveries, and dissatisfied customers and employees.
- Communication can be improved by providing an infrastructure for the exchange of information as well as by creating the conditions for social interactions in the workplace.
- Today, software is widely used to facilitate better communication both internally and externally.
You may also like: Change Management in Manufacturing – Implementing an ERP System