Common Reasons for Bad Material Resource Planning
Material Resource Planning is one of the important parts of modern MRP – a systematic approach to planning, scheduling and executing of manufacturing processes.
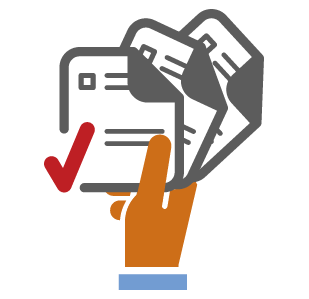
In Material Resource Planning, also known as Material Requirements Planning dependent demand items are components of finished products, such as parts, machinery, sub-assemblies, and raw materials. The quantity or amount of these components or inventory highly relies on the production level of the finished product.
Simply put, dependent demand inventory refers to raw materials as well as other supplies that are integral in the production of a company’s offerings. For example, a car company’s dependent demand inventory are materials such as steel, metal, paint, tires, and motor engine.
How does Material Resource Planning work?
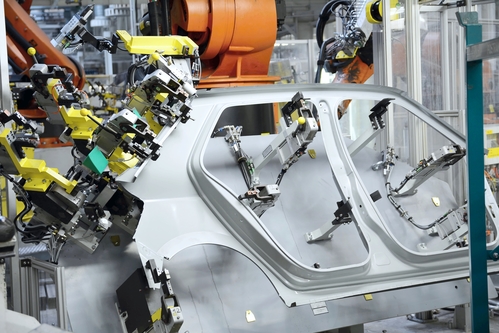
Material Resource Planning works its way backwards, as it comes from a solid production plan for final products. Planning draws requirements for raw materials and raw components. The first step of Material Resource Planning starts with implementing a schedule of raw materials and sub-assemblies – all of which are needed to
The final product needs to be completed within the predetermined schedule formulated during the planning stage of the manufacturing process. Essentially, Material Resource Planning addresses four questions commonly asked during the production stage:
- What materials are needed?
- How much raw materials are needed?
- When are raw materials and other components needed?
- For who are the finished products for?
Material Resource Planning simplifies the process of production by masterfully breaking down inventory requirements and criteria into periods of planning. The goal of this manufacturing management approach is to complete production activities in a timely manner while keeping inventory as well as costs to a minimum.
In manufacturing excessive material inventory levels are avoided by companies through extensive planning and careful design, elements such as capacity needs are controlled and production time is allocated accordingly too. However, when not implemented carefully, material planning delivers an opposite result, that which is a waste of time and money resources.
The risk of inaccurate information
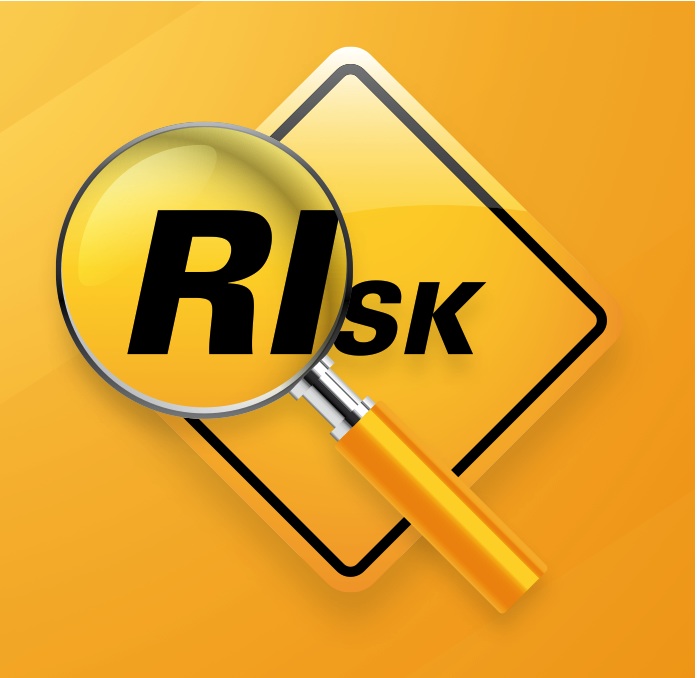
An example of material resource planning done wrongly is when inaccurate information is being entered into the system. The efficiency of effective production components planning highly relies on the quality of information that is typed into the system.
Key management personnel should ensure that all data placed on the system are both accurate and updated. Companies should always maintain a backup of the current list of the bill of materials, numbers, and inventory information to be able to fix the errors fast and without big loss to the manufacturing process.
Why is Material Resource Planning Critical to the Success of Manufacturing Companies?
As being an essential part of the MRP system, well-designed and properly implemented material resource planning is crucial to increasing profits and expanding the size and scope of any business.
You may also like 10 Things You Need to Know Before Buying Manufacturing Software
Shortages in inventory and disorganized scheduling can result in delays that may even be the cause of production halts and canceled orders from clients. If you want to avoid problems and make sure your shop floor runs smoothly and flawlessly, first the risk of wrong information has to be eliminated. When this is done a business owner can reap the following benefits from using the approach:
- Identify potential inventory shortages before they happen
- Generate work and purchase orders automatically
- Planned purchase of raw materials and components when needed. This frees up money by taking advantage of price slashes and significant discounts
- Optimizing manufacturing of product offerings by scheduling personnel and equipment
- Efficiently schedule work orders and deliveries to ensure timely delivery
Conclusion
By integrating Material Resource Planning into their system, companies strike a balance between the good things for a business and the ever-changing customer demands. With good material planning in place, competitive pressures can be easily dealt with.
Amidst reduced margins, leaner operations, and less production, the best way to ensure that the planning is done correctly is to look into the MRP software applications that are being offered on the market right now and pick the one that suits all your needs.