What Are Co-Products and How to Track Them?
Co-products are secondary products created during a manufacturing process. Tracking these goods enables companies to significantly reduce waste, manage costs, and increase profitability.
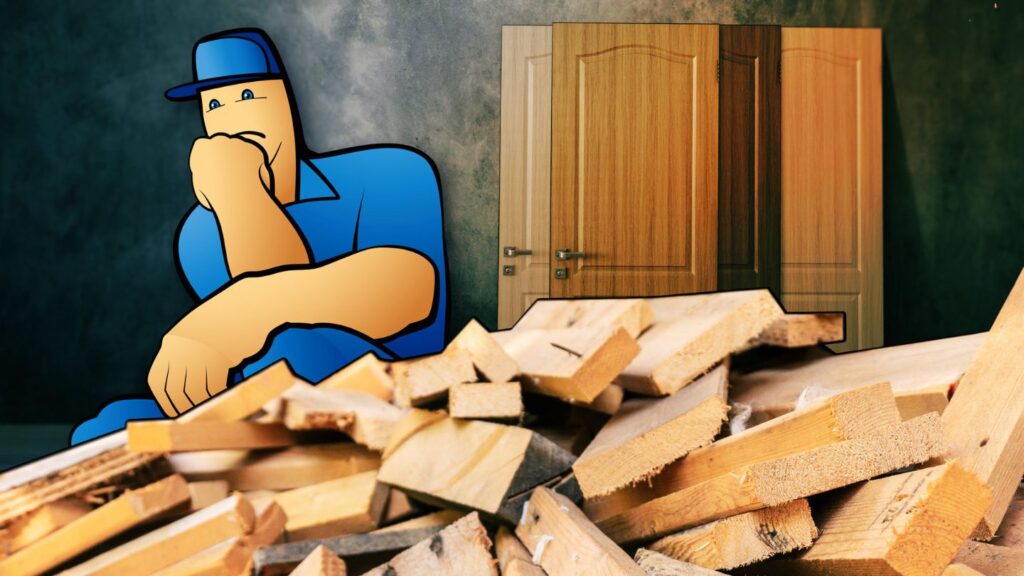
You can also listen to this article:
What are co-products?
Co-products are secondary products generated during the manufacturing process alongside the main product. Co-products have significant value and are often planned for and managed as integral parts of the production process. This is what sets them apart from the larger category of ‘by-products’ which also includes waste and less valuable secondary products.
Co-products are therefore desirable by-products that have market demand. This can include recyclable items such as rejected products or scrap.
Examples of co-products
Co-products are commonly produced in the food and beverage sector, chemical processing, mining, and woodworking, among others.
Here are 10 examples of co-products created during a production process:
- Molasses from sugar production
- Whey from cheese production
- Leather, bone meal, and gelatin from meat processing
- Bran and germ from flour milling
- Buttermilk from butter production
- Wood chips and sawdust from lumber production
- Slag from ore smelting
- Kerosene and petrochemicals from petroleum refining
- Cellulose and lignin from paper manufacturing
- Grape pomace and grape seed oil from winemaking
However, as there are no zero-waste production processes, every manufacturing sector has the potential to create secondary products that can be sold, reused, recycled, or repurposed.
Benefits of tracking co-products
If your manufacturing process creates valuable by-products, you should commit resources to tracking them to ensure they are properly accounted for and exploited. Here are the reasons why co-products should be tracked alongside your raw materials, WIP, and main products:
- More accurate cost management. Properly allocating costs among main and secondary products helps understand the true cost of production, enabling precise pricing strategies and better financial decisions.
- Reduced waste. Tracking secondary products ensures that all raw materials are fully utilized, minimizing waste and promoting sustainable manufacturing practices.
- Efficient inventory management. Keeping track of both main and co-products provides an accurate overview of your inventory levels, enabling you to prevent shortages and excess inventory.
- Regulatory compliance. Integrating the tracking of secondary products with lot tracking enables you to achieve traceability in co-products along with primary products. In addition, monitoring these goods also ensures adherence to environmental and safety regulations.
- Improved production planning and control. Having a comprehensive view of all products being manufactured allows for better production scheduling, decision-making, and resource allocation.
- New revenue streams. Identifying potential markets for co-products creates additional sources of revenue, diversifying income and spreading business risk.
As you can see, managing and tracking co-products enables you to maximize your resource utilization and profitability.
How to track co-products manually?
Tracking the production of co-products manually involves highly disciplined record-keeping. Here is a step-by-step guide to ensuring all your co-products are properly accounted for.
- Create detailed production logs
With each production run, record the quantities of raw materials used, primary products manufactured, and co-products created.
- Track your co-product inventory
Include co-products in your inventory records and update the records after each production run or other transaction involving your co-products.
- Ensure traceability
As with finished goods inventory, record the raw material lots that were used in the creation of the co-products. This enables you to trace back any quality issues.
- Allocate costs
Ensure that each co-products share of your total manufacturing costs are accounted for. To do this, first, you should derive what is the internal value (cost) of these compared to the primary product.
For example, imagine that a production run produces a primary product and one co-product. Through analysis you find that the cost per unit of the primary product is 4 times greater than that of the secondary product, approximately $40 and $10, respectively.
Next, you should calculate a cost allocation percentage by dividing the cost per unit of the particular product by the sum of the unit costs of all products created during the production run.
Product cost allocation rate = (CPU of product) / (Sum of all CPUs)
The cost percentage of the primary product is therefore:
Primary product = $40 / ($10 + $40) = 40 / 50 = 0.8 = 80%
The cost percentage of the co-product is:
Co-product = $10 / ($10 + $40) = 10 / 50 = 0.2 = 20%
Once this exercise is completed, next time when you have a production run, you can easily calculate actual costs of all products after totaling up production costs. For example:
Total production cost: | Direct materials + Direct labor + Overhead = | $ 1000 |
Cost of 24 main products: | 24 x 80% x $1000 / (24 x 80% + 4 x 20%) = | $ 960 |
Cost of 4 co-products: | 4 x 20% x $1000 / (24 x 80% + 4 x 20%) = | $ 40 |
Cost of 1 main product: | $960 / 24 = | $ 40 |
Cost of 1 co-product: | $40 / 4 = | $ 10 |
This approach enables consistent cost allocation between primary and co-products regardless of the number of co-products, variable input costs, and variable produced quantities.
- Physically count your co-product inventory
Include co-product inventory in your regular stocktakes to discover any discrepancies between quantities recorded in the production logs and actual inventory levels.
Tracking co-products with MRP software
Co-product tracking can be largely automated with MRP software that includes co-products in the bill of materials functionality.
In MRPeasy, this functionality can be enabled at Settings -> System settings -> Professional functions -> Co-product BOM.
This functionality enables you to define additional products created as a result of manufacturing a product. After defining the co-products, workers can report the quantities of secondary products, side products, rejected products, or scrap created during a production run.
After a production report is entered, the co-products are added to stock and production costs are automatically allocated. When the lot tracking functionality is enabled, the software also automatically maintains a record of the materials used in producing a specific batch of a co-product to ensure traceability.
In addition, MRP software integrates all vital functions of a manufacturing operation, providing manufacturers with a real-time overview of their business. This enables companies to know their inventory levels, expertly plan production activities and purchases, provide clients with quick and accurate quotes, control costs, and deliver on time.
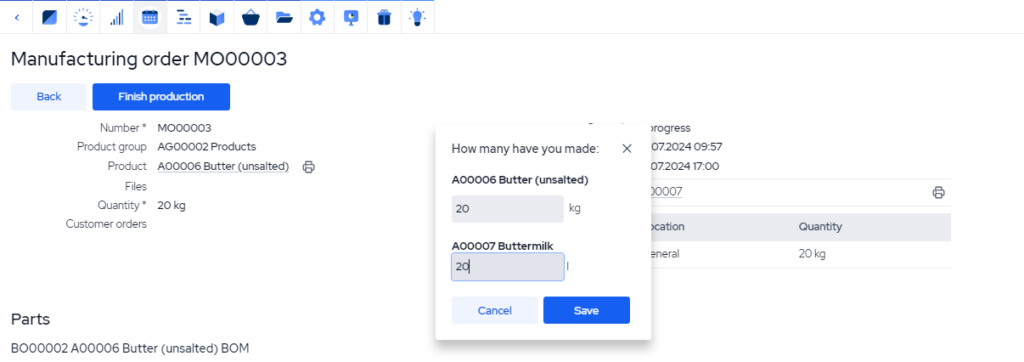
Key takeaways
- Co-products are valuable secondary products generated during the manufacturing process alongside the main product. They differ from by-products as they have significant market value and are planned for and managed as integral parts of production.
- Common industries producing co-products include food and beverage, chemical processing, mining, and woodworking. Examples include molasses from sugar production, whey from cheese production, and wood chips from lumber production.
- Tracking co-products ensures more accurate cost management, reduced waste, efficient inventory management, regulatory compliance, improved production planning, and new revenue streams by identifying potential markets for co-products.
- Manual tracking involves detailed production logs, updating inventory records, ensuring traceability, and accurate cost allocation. Regular physical inventory counts help reconcile recorded data with actual inventory levels.
- MRP software like MRPeasy can automate co-product tracking by including them in the bill of materials, allowing workers to report quantities produced.
Frequently asked questions
To determine the internal value of co-products, you can start by analyzing the market prices and production costs associated with each product. Consulting with a financial analyst or using cost accounting software can help simplify and accurately allocate these costs.
Look for MRP software that includes co-product BOM functionality, inventory management, lot tracking, and production reporting. Integration capabilities with your existing systems and user-friendly interfaces are also essential for smooth adoption and efficiency.
Additional examples include biodiesel production, which generates glycerin as a co-product, and brewing, which produces spent grain used for animal feed. These industries leverage co-products to enhance profitability and promote sustainable practices.
You may also like: How to Manage Product Variants in Manufacturing?