What Is Co-Packing or Contract Packing?
Co-packing means having a specialized packing company package your manufactured goods into their final selling form. Using a co-packer helps small manufacturers focus on their core competencies, save money on packaging equipment, labor, and logistics, and sell their products in higher-quality packaging.
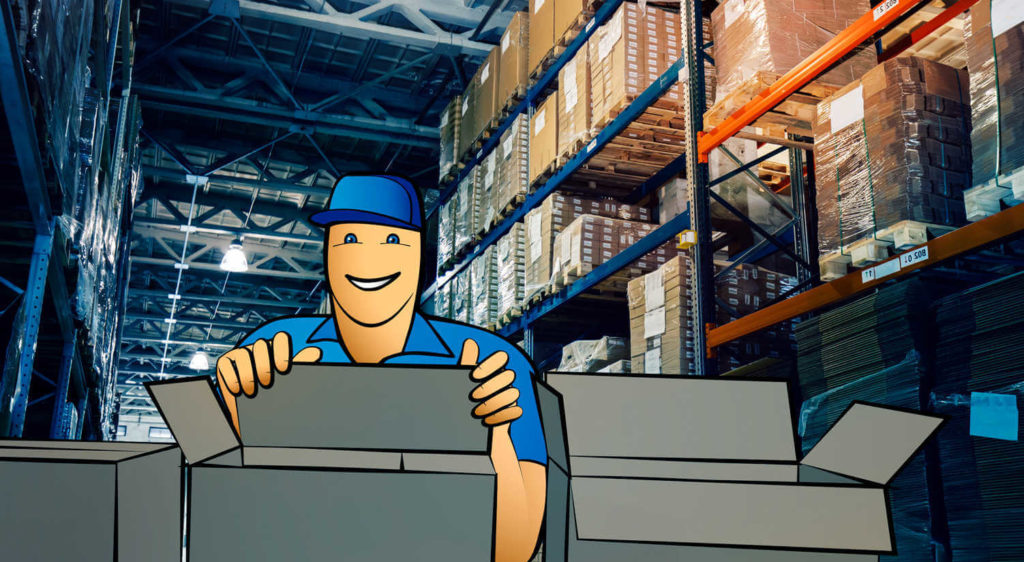
You can also listen to this article:
What is Co-Packing?
Co-packing or contract packing is a subcontracting model in the manufacturing industry wherein the manufacturer of a product outsources the final packaging of the goods to a contract packer. In the food and beverage industry, the term is often used interchangeably with contract manufacturing, meaning that brands use other manufacturers to produce or process, AND package their goods.
Co-packing can be utilized in almost any industry, but it is more prevalent in sectors such as food and beverage, health and beauty, medical and pharma, and chemical. Sometimes manufacturers package their own goods and then send them over to a contract packer for secondary packaging to create bundles or point-of-sale displays. Other times, co-packers design the packaging, produce it, and pack the products. Co-packing companies sometimes also deal with the final logistics of the packaged products.
Benefits of Co-Packing
By using co-packing, manufacturers can focus on their core competencies, i.e. the production of the goods, and have the packaging done by a company that specializes in that field. This way, the manufacturer’s costs are reduced as no packaging equipment and materials have to be procured and no salaries for packaging staff need to be paid. In addition, there is no need to accommodate the equipment and packaging staff in the manufacturer’s facility, which means there is no need for a larger space with higher rent and overhead costs.
Logistics costs could also be reduced with contract packing as the goods are moved less between facilities and warehouses during the packaging and distribution process. Plus, the specialized environment can almost every time achieve a higher quality packaging, which is essential for catching the customers’ eyes.
When to use a Contract Packer?
Outsourcing your packaging should be considered if it would be less costly and more efficient to use a contract packer, or if your company’s expertise or capacity is not enough to fulfill current packaging needs.
For example, you might not have the necessary packaging equipment nor the capital to invest in it.
You might need to create special packaging for a promotion and do not have the expertise for it.
You might be entering a new market area with bulk shipping and local packing turning out to be more cost-effective.
You might not have the capacity to respond to a spike in demand or you might be downsizing your packaging capacity.
However, if the need is not clear and you are reluctant to give away any control over your supply chain, it would not be feasible to turn to a co-packer. Rather, you should try and find solutions in-house, be it hiring a packaging specialist or increasing your capacity.
The decision of whether or not to use a contract packer should be done on a nearly case-by-case basis, by considering the specific needs and capabilities of your company. Some companies also opt for a mix of the two approaches: using in-house resources to package their homogenous core product line and outsourcing the limited or special edition packaging.
How to choose a Co-Packer?
Let’s say you have done your research and have decided to subcontract a co-packer in order to simplify your business process and save money. The next step would be to find a suitable contract packing company. But what are the aspects that you should consider when looking for one?
Here are some of the considerations you should take when choosing a contract packer:
- Location. Is the co-packer close enough to you that the transportation costs would not eat away what you win by outsourcing? On the other hand, is the co-packer close enough to your target market?
- Reputation and quality. Are they well-established and known experts in the field? Do they have the certificates required according to your industry standards?
- Price. Do their prices allow your company to be more competitive? Does outsourcing packaging free up extra cash that you could use elsewhere?
- Capacity and Minimum Order Quantity. If your orders are large, do they have the capacity to package your products in the quantities you need? Or if you’re still starting in the business, are they willing to take on orders as small as yours?
- Communication. How is the communication with the company? How quickly do they respond to emails? Do they pick up the phone without fault? Do they notify you any time something changes?
The best you can do as a manufacturer about to hire a contract packer is to investigate your prospective companies thoroughly. Visit their facilities, converse with their employees, and talk to their customers about their experience to make sure you are getting a reliable partner.
How to manage Co-Packing?
With some ERP/MRP systems, it is possible to manage outsourced services and operations that you order from a contract manufacturer or co-packer. The most feasible way to approach this would be to use either:
- separate bills of materials for bulk goods (produced by the manufacturer) and single units (packaged by the co-packer), OR
- a multi-level BOM wherein the operations taking place in your own facility would constitute separate levels from the packaging operations.
Either way, you can use the ERP system’s subcontracting feature to raise purchase orders and send them directly to the co-packer, with the system scheduling the operations according to the cycle time set.
You can also set up the packaged products as procured goods and use regular purchase orders to put in a request to the co-packer. In this case, you would create a shipment of the bulk finished goods to the contract packer to consume the unpackaged goods from inventory – and later receive the packaged goods back to inventory.
Key takeaways
- Co-packing or contract packing is a subcontracting model in the manufacturing industry wherein the manufacturer of a product outsources the final packaging of the goods to a contract packer.
- In the food and beverage industry, the term is often used interchangeably with contract manufacturing, meaning that brands use other manufacturers to produce or process, AND package their goods.
- By using a co-packer, manufacturers can focus on the actual manufacturing, save money on packaging equipment, staff, and logistics, as well as achieve higher quality packaging for their products.
- You could consider hiring a co-packer if you lack capital for your own packaging line, if you lack expertise for creating the packaging you want, if you are at full capacity, or just if using a co-packer could prove to be more cost-effective.
- Co-packing can be effectively managed with the help of an ERP/MRP system with subcontracting functionality.
You may also like: What Is Distributed Manufacturing?