Building an ERP Implementation Team for Manufacturing
With MRP or ERP implementation, the key to a successful implementation relies on assembling the right team. With the right skills, attributes, and leadership, a fully optimized system can be built to fit any manufacturer’s needs.
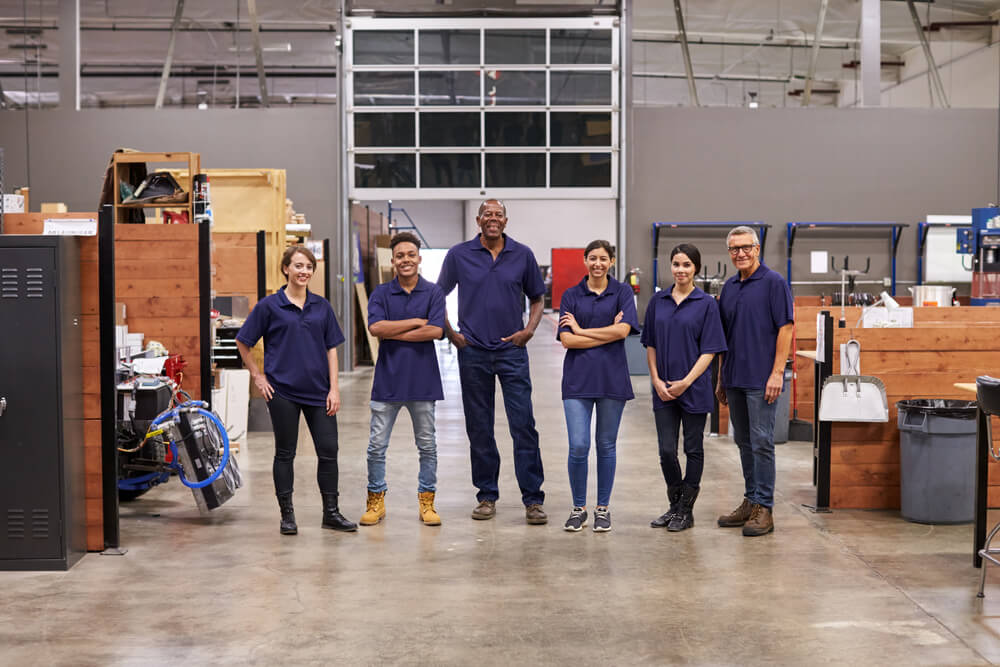
You can also listen to this article:
Intro
Any adoption of new software at the corporate level can cause headaches for a manufacturing company. Change is difficult to manage, there is lots of training to be done and new systems often have trouble adapting legacy knowledge into a new process-oriented framework.
As a result, no two implementations are alike. Implementing a new ERP has been compared to two different artists working on the same piece of music. Just as the sound and emphasis may come across differently depending on the artist, an ERP system using the same source code can result in very different experiences.
At the end of the day, the key to a successful manufacturing ERP implementation relies on assembling the right team. With the right mix of key players, there will still be a lot of hard work and many challenges, but it can be done much as a well-orchestrated performance of an artist’s music.
Why ERP Teams Fail
A study by the Project Management Institute found that 60% of projects fail. Sometimes the projects were doomed from the start, such as placing the purchasing decision in the wrong department or in inexperienced hands. Other times, a company’s organizational culture is to blame, with entrenched legacy management and outdated SOPs (Standard operating procedure). In these cases, it is not the software that fails. Rather it is the lack of understanding that projects such as an ERP implementation require strong and well-organized change management as well.
Common reasons for ERP implementation failure (and large software projects of any kind) include:
- Top-heavy management where the executives are the only group making decisions and shepherding the project.
- Lack of “as is” process mapping. It is difficult to know where to take the project of a company that doesn’t firmly grasp where their processes have placed them in the present time.
- Failure to identify clear business goals and objectives.
- Lack of communication or weak communication both internally and with the vendor/partner.
- Failing to plan for the organizational culture’s response to the system.
- Executive failure to understand the project scope.
- Cutting corners with training.
- Lack of experience coupled with a resistance to spending for outside consulting assistance.
You may also like ERP Implementation – How to Analyze Your Internal Processes.
Important Team Elements for Successful ERP Implementation
To get an ERP implementation on the right track, it is important to assemble a team that addresses all the above reasons for failure. This means building a broad, experienced team with clearly defined goals and the communication skills required to succeed. It also means that the team should be agile and adaptable and be provided with all the resources required for the job.
Important team elements include:
Team Composition
An ERP implementation team should be assembled based on competency and not status. This may mean including less senior members over those with more tenure and managing the issues that could result from that. It also means blending the right amount of technical skills as well as less technical, but task or project management-oriented to ensure all aspects of the project have someone who can accomplish tasks based on their skillset. Team members should also include the following:
- Executive Sponsor – An executive sponsor is critical because this person will both lend top-level authority to the project as well as acting as a bridge and buffer back to the executive group. This reduces the tendency for conflicting goals coming from multiple executives.
- Project Manager – Some companies have a specific person or persons in the role of project manager while smaller companies may have a key member who is good with projects. The important thing is to have someone in this role to manage the overall project costs, timeline, vendor interaction, and training schedules.
- Implementation Partner – Just as many companies leave out a project manager, others may try and use only internal skillsets to implement the system. But most platforms are represented by a third party or provide implementation consultation native from the software and platform provider itself. This is important because there is always a depth of system knowledge that an implementation provider can offer that would far exceed an internal team’s ability to understand at the beginning of deployment as everyone is undergoing a steep learning curve.
- Report Writer – Many companies undertake ERP implementation and consider reports as almost an afterthought. But any system will need to be customized to provide the right reports for proper insight into the data and analysis the system is providing. This role can be assigned to a dedicated team member, or in smaller companies may fall to a super-user. Responsibilities may include reconciling old reports to the new system’s capabilities, writing and developing new report structure and processes and exploring the way the new system can provide reporting not available in the old ERP.
- Core Team Members – Core team members are those from within the company who will be using the system daily to drive production. They may include manufacturing members from different production departments, IT staff members, finance and purchasing staff as well as HR, maintenance and inventory control. They provide insight into how and why things work the way they do, and they can offer process improvement SOPs that take advantage of platform functionality. They are also important as subject matter experts for their respective areas when customizing the system for production.
Team Knowledge and Skillsets
Having the right knowledge base and skillsets is critical to any implementation team. By building them across functional areas and making their benefits available to all team members, the entire team’s tasks can be made easier.
- IT – Few skillsets are as important as those of a manufacturer’s IT department. Regardless of the size of the company, IT is a critical part of operational infrastructure. While many team members will develop new SOPs and provide area-specific knowledge for the production processes, IT will be required to be involved in each step and area of implementation. If this skillset isn’t strong enough or large enough, it may be necessary to subcontract augmented IT services from an additional third-party supplier or from the implementation partner.
- Change Management – In any implementation there will need to be a strong emphasis on change management. The executive sponsor and perhaps HR may need to aggressively deal with trouble spots before they occur as many legacy staff is hesitant to surrender knowledge for fear of losing status or even their job. Effective change management would start with the team and branch out through regular and positive communication with employees in the company. Help from HR and from the executive sponsor and entire executive team can lay the groundwork for change early in the process.
- End Users – It is important for teams to utilize end users heavily. This means that the platform will need to be tested and retested as customization and functionality are added. It is here, in the hands of those in production that will use the system daily, that both errors and process optimization can occur. This means training heavily and keeping the end-users engaged to build familiarity with the system through repetition. End users can also communicate their needs both for core production processes that need to be addressed, but for suggesting process improvement.
Team Attributes
Working closely with an implementation partner or the new platform’s customer service, management should build a team where the implementation load is balanced between in-house staff, consultants and temporary labor (when required). Care should also be given to resource allocation and in making sure that all team members have proper access to information and system permissions to complete their tasks.
Teams work best with realistic timelines and when elements of the implementation are broken into stages. This gives all members time to internalize the new system and prepare for the next phase. Members of an implementation team should have certain individual characteristics that will help make a cohesive and effective team. Characteristics such as
- Upward Mobility – Upwardly mobile employees within the company are less attached to the status quo. They will adapt faster to change.
- Team Smart – Many people are personally smart. But often that does not translate into being an effective team member. By finding “team smart” employees, the focus will be on the goals of the team and not on ego.
- Personal Depth – Emotional intelligence in the workplace manifests itself as personal depth. This means that while the team member may not like or agree with decisions for implementation, they understand the what and why of the decisions made.
Conclusion
Implementing a new manufacturing ERP system will always be a challenge. But by assembling an implementation team with the right skills, attributes and leadership, those challenges can be managed to build a fully optimized and customized system to fit any manufacturer’s needs.