BOM Management Guide for Growing Manufacturers
A bill of materials (BOM) is a document that defines the materials used in the production of a product. But BOM management is much more than just drawing up a list of items. Here is how to expertly manage your BOMs.
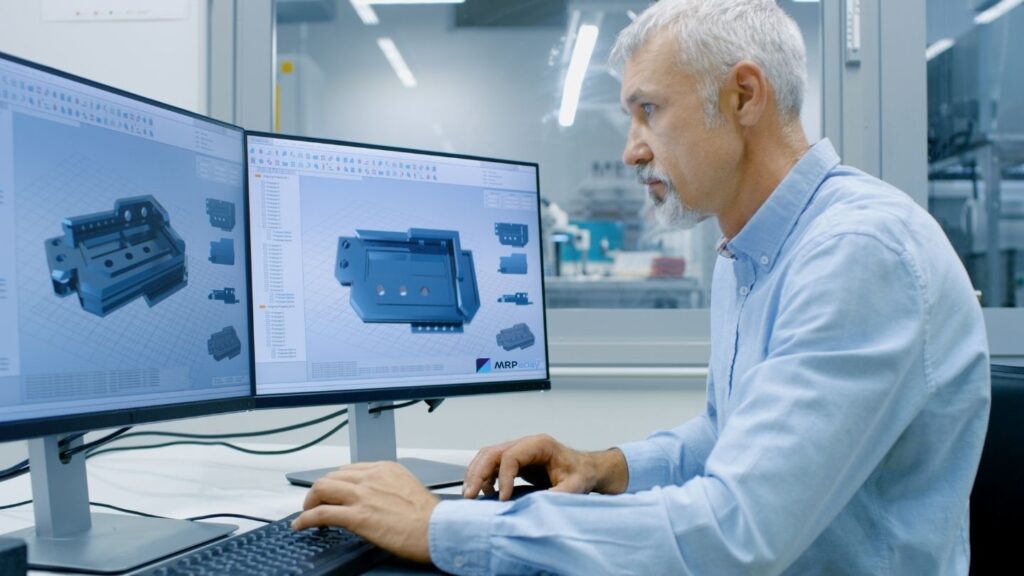
What is a bill of materials (BOM)?
A bill of materials (BOM) specifies the materials and components used to manufacture a product. It creates a base for production planning by ensuring alignment between inventory, procurement, and production.
BOMs are often coupled with production routings, creating a full “product recipe” by combining the ingredients with the manufacturing processes required to build the product.
What is BOM management?
Creating a bill of materials is just the first step in its life cycle. Properly managing your bills of materials is a process that lasts the whole lifetime of the product, making it an integral part of product lifecycle management or PLM. Managing a bill of materials includes:
1. Creating the BOM
An effective BOM starts with a comprehensive list of all the components required to build the product, including raw materials, sub-assemblies, and, if necessary, consumables. This includes assigning clear part numbers and descriptions to each item and defining quantities needed.
During the development of more complex products such as electronics or machinery, first the engineering BOM (EBOM) is created to define the product design. This serves as the foundation for the manufacturing BOM (MBOM), which specifies how the final product will be built on the shop floor. Effective BOM management also means seamlessly converting EBOMs into MBOMs.
2. Structuring the BOM
Proper BOM structure is necessary for clarity and efficiency when products reach a certain complexity. Depending on the product, the BOM can be structured as a single-level BOM, listing components directly related to the final product, or as a multi-level BOM, which includes sub-assemblies and their components.
3. Adding the routing
The production routing defines the sequence of operations required to turn the components into a finished product. It specifies the steps, tools, machines, and time needed for each stage of production. Adding a routing integrates the BOM further with the production floor and enables more precise capacity planning and production scheduling.
4. Integrating the BOM with inventory
Tying your bills of materials to your stock-keeping units (SKUs) within your production management system ensures that the materials and components going into a product are accurately tracked. When the materials and their quantities are precisely defined within the BOM, it can be used to calculate material requirements for upcoming orders or periods, compare the requirements with current inventory levels, and make the necessary purchases.
5. Enabling customizations
Configurable BOMs or matrix BOMs are used to handle variations in the product design. Unlike static BOMs, these dynamic formats allow for flexible combinations of raw materials, components, and sub-assemblies to meet specific customer requirements or market demands. This approach reduces the need to create entirely new BOMs for every new product variant, helping to streamline the customization process while preserving the integrity of the BOM structure.
6. Recording BOM updates
Managing BOM revisions ensures that updates—such as changes to materials or design optimizations—are documented and implemented without disruption. Recording each engineering change enables you to know which iteration you are currently on and helps you revert back to a previous version of the BOM when needed.
Benefits of effective BOM management
Effective BOM management leads to an array of advantages that help you save resources and increase efficiency. These benefits include:
1. Standardization and consistency
A properly defined bill of materials introduces standardization to the manufacturing process by ensuring that everyone is on the same page regarding what goes into the product. By defining a product’s components and its assembly process, you will ensure that the item will be made in the same way, with the same parts each time. An accurate BOM will also allow you to create precise work instructions that streamline workflows.
2. Less confusion between engineering and production
Effective BOM management ensures that the list of parts, materials, and instructions provided by engineering is clear and complete for manufacturing teams. By standardizing product data and aligning engineering BOMs with manufacturing BOMs, you’ll eliminate miscommunication and ensure that both teams are working with the same, up-to-date version of the product structure. Well-defined and detailed BOMs are especially important when outsourcing some processes to contract manufacturers.
3. Effective supply chain and materials management
Precisely documenting the components that go into a product, including their quantities, dimensions, and other characteristics, enables you to source the exact materials that match your requirements. Secondly, by integrating the BOM with inventory management and purchasing, you can keep track of your material inventory, quickly forecast material requirements for incoming orders or entire periods, and avoid stockouts and excess inventory.
4. Improved production planning and scheduling
After forecasting their material requirements for the period, companies can align purchases with production so that the necessary materials would reach the shop floor at the right time while also avoiding overstocking. Furthermore, production schedules can be made considering actual material lead times and cycle times defined in the production routing.
5. Better cost estimating and tracking
Effective BOM management lays the groundwork for estimating and tracking material and labor costs. When an order comes in, the BOM data can be used to estimate material and labor costs according to how many units were ordered. Later, as products are being manufactured, the workers can report material consumption and labor hours to calculate the actual production costs and compare them to the estimates. Accurate estimating along with knowing exactly where your money goes ensures appropriate pricing and profitability.
6. Better quality and reduced waste
Standardizing your products and processes with BOMs and routings ensures that they are manufactured consistently each time. This improves overall product quality and reduces material waste. Using the routing and cycle times as a basis for monitoring production efficiency also enables manufacturers to improve their processes.
7. Traceability
Proper BOM management ties products to specific parts, which is a prerequisite for lot tracking. Lot tracking is then used to keep a record of which material batches were used in specific products and which customers received these products. This enables companies to trace back the root causes of product defects and organize callbacks.
Common BOM management issues
Even if your bills of materials are simple, managing them and integrating them with inventory and the shop floor could bring complications. Here are the most common BOM management issues:
- Inaccurate or incomplete data. Missing or incorrect product information can disrupt production and lead to costly errors. Without an accurate BOM, manufacturers risk delays, over-ordering, or shortages in the supply chain.
- Overly complex BOMs. For simpler products, unnecessarily detailed or multi-level BOMs can slow down workflows and create confusion on the shop floor. Simplifying BOMs where possible helps streamline the product development process.
- Poor integration with inventory. When BOMs are not linked to inventory systems, manufacturers lack visibility into material consumption and stock levels, leading to procurement inefficiencies and supply chain bottlenecks.
- No version control. Without proper change management, teams may use outdated BOM versions, causing inconsistencies between engineering, procurement, and production.
- Manual BOM management processes. As linking various functions such as BOMs and inventory is very complicated in manual tools like Excel, it can result in inefficiencies, human errors, and limited collaboration.
All these common BOM management issues can sink your efficiency, cost you money, and lengthen your products’ time-to-market. One way to mitigate all this is to implement BOM management software,
Managing BOMs with manufacturing ERP
All the above issues can be solved and benefits accrued by implementing a capable system, such as a manufacturing ERP (enterprise resource planning) software to manage your bills of materials and your operation at large.
Manufacturing ERP software integrates BOM management with sales, inventory, procurement, production, and finances to automate hundreds of managerial and administrative processes, including inventory updates, revision control, order and cost tracking, etc. This ensures that all stakeholders have a real-time overview of current BOM versions, orders, production costs, material requirements, and so forth.
When dealing with complex products that consist of many subassemblies, or products with variations (e.g. in color or size), a robust manufacturing ERP system such as MRPeasy also provides you with the tools to manage multi-level and configurable BOMs.
With all this data centralized and easily accessible, communication between departments becomes lightning-fast and collaboration rises to a much higher standard. This streamlined exchange of information inevitably leads to more efficient shop floor and supply chain management.
Key takeaways
- A BOM specifies the materials, components, and quantities required to build a product. It acts as the backbone for production planning, ensuring alignment between design, inventory, and procurement processes.
- Managing a BOM involves its creation, structuring, integration with inventory, and revision over time. This process ensures accurate product data across the entire lifecycle, from product development to production and beyond.
- By linking BOMs to inventory systems, manufacturers can forecast material requirements, reduce overstocking and shortages, and gain better visibility into material costs. This integration helps optimize production workflows and supports efficient resource allocation.
- Configurable and matrix BOMs allow for flexible combinations of materials and components, supporting product variations without creating entirely new BOMs. This enhances efficiency and speeds up customization for diverse market demands.
- Manufacturing ERP systems, like MRPeasy, centralize BOM data, integrate it with procurement and production, and automate revision control. This enables real-time updates and collaboration across departments, reducing inefficiencies and improving supply chain management.
- Standardized BOMs ensure consistency in material usage, reducing waste and improving product quality. When paired with lot tracking, BOM management facilitates full traceability, helping manufacturers address defects and meet regulatory compliance efficiently.
Frequently asked questions (FAQ)
A BOM specifies the materials, components, and quantities required to manufacture a product, acting as a “parts list.” A routing, on the other hand, defines the sequence of operations, tools, and time needed to transform those materials into the finished product. While the BOM focuses on “what” is needed, the routing focuses on “how” the product is made.
BOM management software uses tools like configurable BOMs or matrix BOMs to handle product variations without requiring separate BOMs for each variant. By allowing dynamic selection of components based on predefined rules, it supports customization while maintaining consistency and reducing manual effort.
ERP systems link BOM data directly to inventory management, ensuring real-time tracking of stock levels and material requirements. This integration allows manufacturers to forecast demand, avoid shortages or overstocking, and automate material purchasing based on the BOM’s specifications.
You may also like: What Are Co-Products and How to Manage Them?