Best MRP Software for Small Manufacturers – Top 7 Solutions for 2025
Effective material requirements planning is unavoidable for any manufacturing company or distributor. But doing it manually or using antiquated methods isn’t. Here’s a look at seven powerful MRP solutions that small to medium manufacturers should consider when choosing production software.
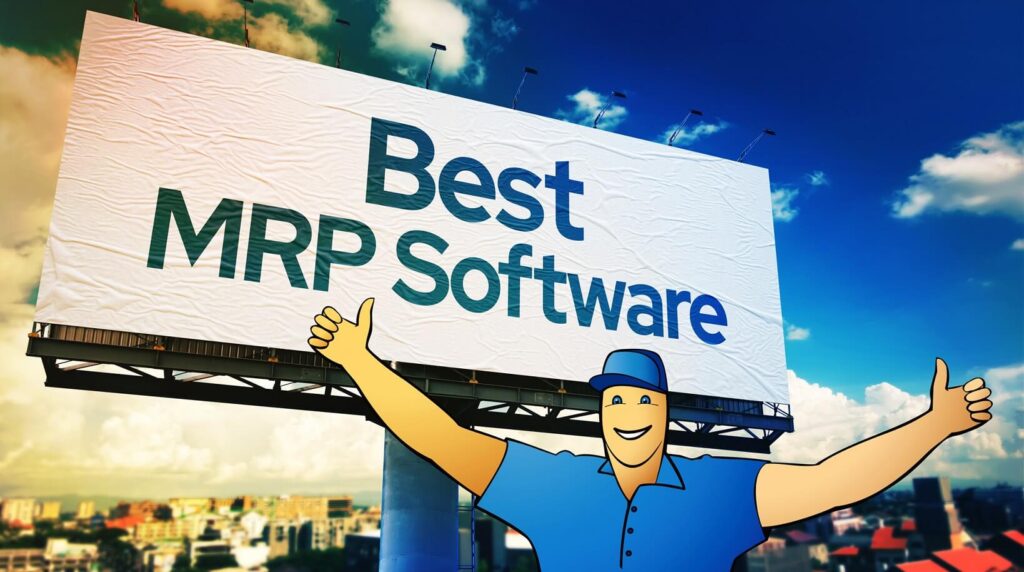
What is MRP software?
MRP software is a sophisticated software system designed to unify manufacturing-centric business processes into a single cohesive system. By integrating work order management, production scheduling, bill of materials functionality, inventory traceability, shop floor control, etc., MRP systems act as a single source of truth for manufacturing operations, automating and streamlining large parts of production planning activities.
Manufacturers and distributors use MRP software to plan and schedule production activities, book inventory into work orders, optimize shop floors, manage purchases and customer orders, and more. MRP software is not reserved for only complex manufacturing setups—many modern solutions are highly flexible and can scale to meet diverse needs. Manufacturing software can be inherently useful for businesses that add any kind of value to a product or item, from simply re-packaging or bundling items to assembling complex machinery.
What does MRP stand for?
MRP stands for material requirements planning. It’s a production planning method developed in the mid-20th century for calculating and estimating products’ material demand. MRPs are designed to answer two basic questions: what goods are required, and how many of them do we need?
Modern MRP systems rely on an updated version of MRP called MRP II, which stands for manufacturing resource planning. MRP II builds on the original concept, enhancing its capabilities and adding advanced functionalities. This makes modern MRP software capable of high-end automation, integrated production management, intelligent inventory control, and much more.
MRP systems vs ERP systems
ERPs or enterprise resource planning systems are comprehensive software solutions that unify the entire business into a single digital ecosystem. MRP systems are distinct from ERP software in two main ways:
- At their core, MRP systems are built to manage and automate manufacturing-based business processes like production planning and scheduling, inventory management, manufacturing execution (MES), etc. Conversely, ERPs typically include modules absent in most MRP software, such as HR and team management, project management, sales pipeline tracking, and other back-office functionalities.
- ERPs come tailored for different purposes, from running multinational corporations or managing car parks to streamlining supply chain management or organizing retail operations. MRPs can also vary in their functionality, but they are fundamentally tied to managing manufacturing processes.
Nevertheless, many MRP software providers market themselves as ERPs or manufacturing ERP systems. This is because they include added functionalities, most commonly CRM (customer relationship management) and accounting modules, either natively or through built-in support for third-party apps.
What to look for in an MRP system
While certain functionalities are baked into any MRP system, their implementation, integration, and extended functionalities can vary widely from software to software. Here is a rundown of the most important aspects to consider when selecting MRP software for your small manufacturing business:
- Production planning and scheduling. Effective MRP systems excel in automating production planning and scheduling, optimizing resource allocation, and managing shop floor operations. They allow real-time adjustments to accommodate changes in supply or demand and help minimize downtime, maximize productivity, and spot efficiency drains. Well-designed MRPs include intuitive tools for simplifying complex scheduling processes.
- Inventory management. A robust inventory management module ensures that materials are accurately tracked and can be dynamically booked into production jobs. Look for systems that provide real-time inventory visibility, automated stock replenishment alerts, and a procurement module. Accurate inventory control is among the most important aspects of fulfilling orders on time and in full.
- Third-party integrations. Seamless integration with accounting software, e-commerce platforms, shipping solutions, etc., can significantly expand MRPs’ usability. Built-in integrations effectively create an ERP environment for a more rounded business management suite while retaining high-end manufacturing capabilities. Whether syncing with a dedicated CRM or automating processes with a fulfillment partner, integrations eliminate manual data entry and help further streamline workflows.
- Ease of use. Any software solution is only as effective as its user interface. User-friendly interfaces and straightforward setups are essential for usability, ensuring faster adoption and minimal training time. An intuitive UI should offer dynamic levels of functionality, catering to both tech-savvy users and those new to digital manufacturing tools. Most MRPs inevitably require some time to adjust, but a learning curve that is too steep often leads to frustration and underutilization of features.
- Scalability. The right MRP software should be able to grow alongside your business needs. Whether you’re operating a single production line or scaling up to multiple locations, your software should accommodate the level of complexity without requiring a complete overhaul or costly downtime to accommodate change. Scalable systems are far more cost-effective in the long run and ensure continuity with evolving requirements.
- Return on investment. Finally, a well-implemented MRP system should offer measurable improvements in efficiency, cost control, and output quality. Evaluate how the system can streamline operations, reduce lead times, enhance customer satisfaction, etc. Look for solutions that provide transparent pricing and avoid hidden fees, to ensure you get the best value for your investment.
Best MRP software for small manufacturers and distributors
Here are seven manufacturing systems to shortlist for 2025 and beyond.
1. MRPeasy
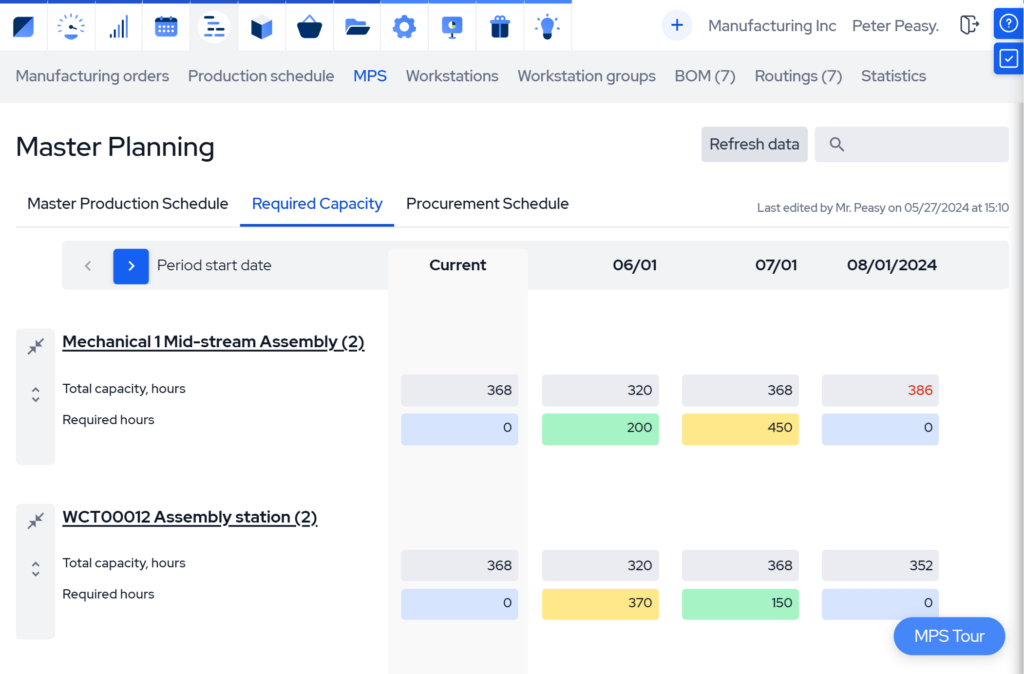
MRPeasy is a powerful cloud-based MRP/ERP system specifically designed for small and growing manufacturers (up to 200 employees). It combines robust manufacturing planning and inventory management capabilities with three traits that small companies value most – a great price-to-performance ratio, ease of use, and scalability.
MRPeasy gives users a high level of control over the entire production process from start to finish. Businesses can manage suppliers and purchases, track inventory and orders throughout the production cycle, control shop floor operations, conduct quality control, dynamically edit production calendars, track KPIs on production dashboards, etc. More advanced features like parallel execution, multi-level bills of materials, master production scheduling, subcontracting, and many more are also available.
MRPeasy provides intuitive access to manufacturing features like one-click production cost and lead time estimating, pre-filled purchase order generation, and advanced routing control. Extended functionalities include capable sales and order management, a B2B customer portal, warehouse management with barcoding, a returns system, financial reporting, and much more. Built-in integrations for third-party software like Shopify, WooCommerce, Shipstation, Quickbooks, Xero, Zapier, and many others are also included.
All in all, MRPeasy is a feature-rich and versatile MRP system specifically designed to cater to small manufacturers and distributors. It’s suitable for a wide range of business types and setups, from make-to-stock producers to discrete manufacturers and e-commerce distributors. The software comes in four editions – Starter, Professional, Enterprise, and Ultimate. Prices are attractive and incur no hidden fees, starting from $49/user for the Starter edition. Pricing remains highly competitive as businesses scale, with the price beyond the first ten users fixed at $79/10 users for all editions.
What customers say
MRPeasy’s users praise the software for its great balance between ease of use and high-end functionality. The level of manufacturing control, inventory optimization, and production tracking that it enables goes well beyond its price range. It’s also reported to be easy to implement and versatile enough to suit various use cases. Users also appreciate that the software is always up-to-date and virtually bugs-free. MRPeasy’s highly responsive support team also gets consistently positive feedback.
2. JobBoss²
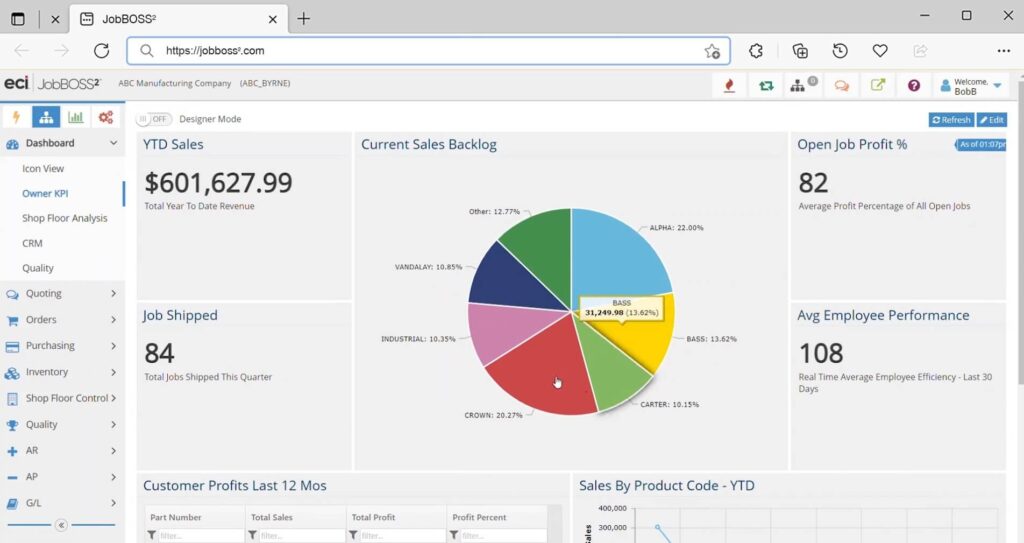
JobBoss² is a manufacturing system dedicated to job shops and shop management. It excels in managing made-to-order production environments where flexibility, detailed job costing, and real-time production tracking are important. With features that streamline quoting, scheduling, and advanced shop floor control, JobBoss² is a good option for small to medium-sized manufacturers working with custom workflows or short-run jobs.
The system’s key strengths lie in its detailed job costing and quoting tools, robust scheduling, and shop floor control that help optimize resource allocation and provide real-time visibility into job statuses. Its advanced reporting tools simplify inspection and compliance, providing paper trails of shop floor operations.
The platform is configurable and can accommodate various production setups. JobBoss² is somewhat less suited for smaller and simpler operations because its versatility in accommodating custom workflows can sometimes feel cumbersome. That said, its structured layout and intuitive interface generally enhance user-friendliness.
JobBoss² is priced at a medium tier, with custom quotes being the standard pricing approach. While this pricing model offers flexibility, it can make cost estimation challenging for prospective customers.
What customers say
JobBOSS² has garnered positive feedback for its comprehensive shop management functionalities, particularly in job costing and quoting. It also receives praise for its capable reporting system, which enhances compliance and simplifies documentation for inspections and audits. Users also appreciate JobBOSS²’s user-friendly interface and general ease of setting up. The pricing is perceived by some as being on the higher side, especially for smaller businesses, with calls for greater transparency regarding costs. Finally, some users have reported the system’s inventory control to be somewhat lacking compared to alternatives.
3. SYSPRO
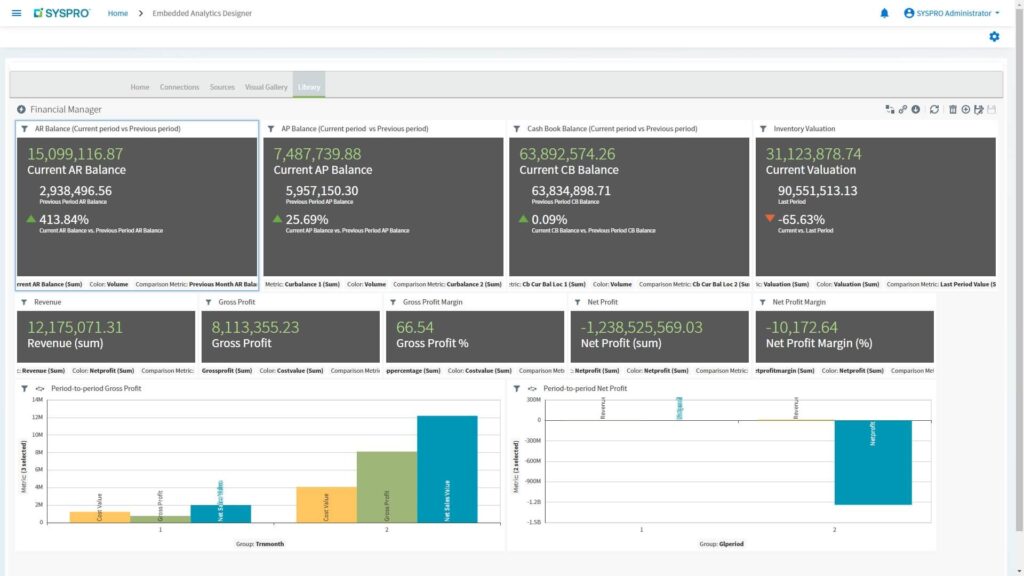
SYSPRO is a comprehensive MRP/ERP solution that supports a range of manufacturing environments, emphasizing engineer-to-order (ETO) workflows. Its flexible and modular interface is designed to allow easy management of custom-driven processes. SYSPRO has good project and quality management tools, and touts advanced scheduling and detailed costing features, making it a solid choice for custom manufacturing.
SYSPRO’s standout ETO feature lies in the software’s ability to integrate engineering and production data seamlessly. This allows businesses to manage customer-specific designs and track engineering changes on the fly, ensuring the updates are accurately reflected in production schedules and cost estimations.
SYSPRO also includes other features well suited for ETO workflows. Examples include advanced bill of materials management for handling multi-level and custom configurations, project-based resource and material planning, and precise cost tracking for highly customized orders. It also offers customizable quality and inspection management systems.
SYSPRO is reasonably priced for its functionality, with prices starting at around $200 per user per month. Expenses may mount, however, as its modular pricing can rack up the running cost for some advanced features.
What customers say
Syspro is highly regarded for its ease of navigation and modular flexibility, integrations with third-party apps, and plentiful customization options. Users further appreciate the software’s ability to handle complex workflows. The system’s inventory management and real-time data tracking features also receive positive feedback.
Downsides include challenges with complexity during the initial implementation phase, the lack of certain functionalities like dedicated warehouse management or equipment maintenance, and a somewhat congested quoting system. Also, while the modular approach is a strength, some businesses find it challenging to determine which modules best suit their needs, potentially leading to unnecessary costs.
4. Katana Cloud Inventory
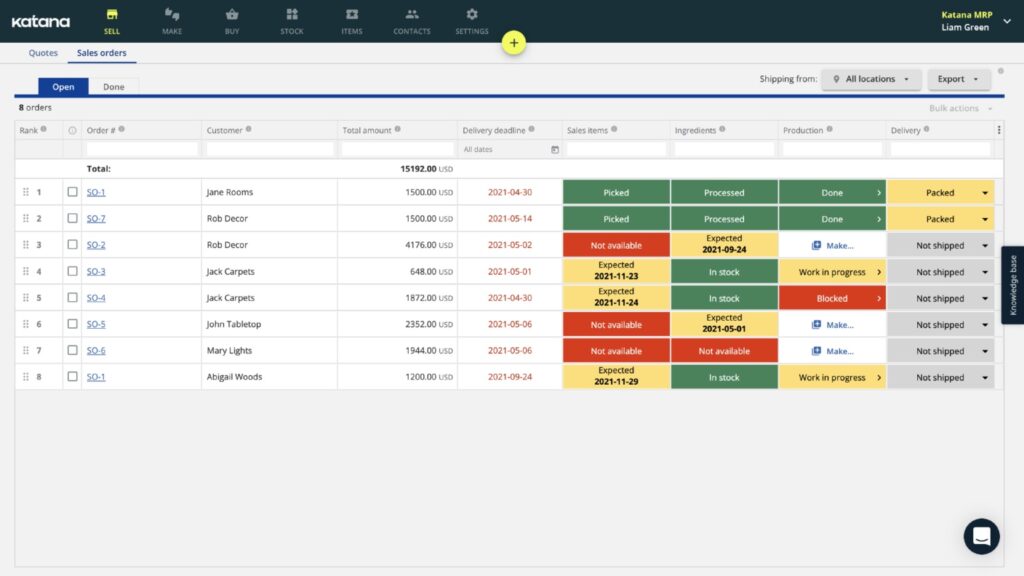
Katana is a cloud-based inventory and production management software with a focus on providing essential and easy-to-use tools for smaller inventories and manufacturing workflows. In essence, it’s a stock management and traceability solution that also enables companies with simpler production setups to manage their workflows and production schedules.
Being mostly oriented on increasing stock control and stock visibility, Katana is somewhat limited as an MRP solution. It lacks many advanced production planning and workflow management functionalities of other solutions. For example, there is limited functionality for managing sub-assemblies and no co-product management, tiered pricing, custom fields, etc. Still, the system handles essential workflow automation well and provides an easy-to-follow interface for doing so.
This makes Katana a good fit for small distributors with straightforward inventories and manufacturers with simpler production setups. Its built-in integrations also make it a viable option for many e-commerce businesses, even though the level of automation it provides can be limited in some cases. Having put a lot of development effort into the user interface, Katana is also generally easy to implement.
The software’s user-friendly interface comes with the notable caveat of being relatively limited in its customizability. But for those the interface suits, it does so well. Katana’s prices start at $199 per month for the Starter plan and reach $799 per month for the Professional edition, which adds more advanced functionalities and API (application programming interface) access.
What customers say
Katana Cloud Inventory receives positive feedback for its ease of use and implementation and overall intuitive interface. The system is also reported to provide simple and effective inventory control, traceability, and essential production management tools. On the other hand, customer satisfaction has fallen due to users reporting frequent bugs with certain features and slowdowns when using the system. Katana’s recent price hikes have also met with negative feedback, as users report that certain functionalities that were previously included in the subscription have been locked behind a paywall.
5. SAP Business One
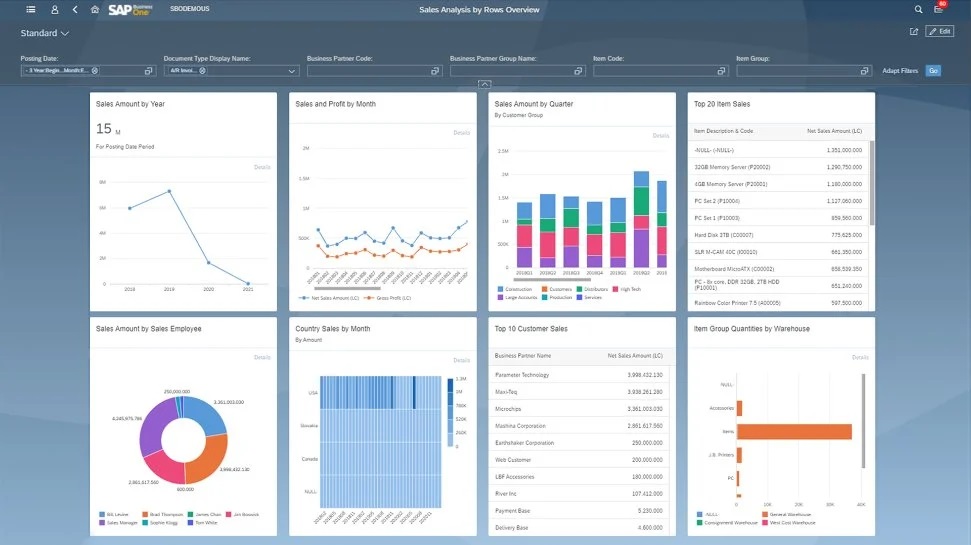
For companies that want to trade cloud-based convenience for the extra security of on-premise software, Business One is a choice worth considering. Business One is an SME-focused manufacturing ERP system provided by tech giant SAP. While Business One also has a cloud-based service, its on-premise deployment option sets it apart as a strong choice for companies prioritizing data security and control.
SAP Business One provides comprehensive tools for managing production planning, scheduling, and material requirements. Its inventory management capabilities ensure real-time stock visibility, and the addition of financial management tools like integrated accounting, budgeting, and cost analysis make it a viable all-in-one solution for businesses looking to consolidate operations. This is further enhanced by the software’s integration capabilities with other SAP solutions, making it a scalable choice for businesses planning future expansion.
Business One is suitable for manufacturers with more complex workflows, offering support for customizations and advanced tools like multi-level bills of materials, batch and serial tracking, detailed reporting, etc. Very small or simpler operations should weigh their options well before choosing Business One as the cost of implementing can reach orders of magnitude higher than alternatives. The on-premise option also entails higher running costs than cloud solutions.
What customers say
SAP Business One receives positive feedback for its comprehensive set of functionalities, particularly its strong financial management and inventory control tools. Users also value the platform’s ability to manage complex workflows, accommodate customizations, and integrate with other SAP products for expanded capabilities.
However, businesses also note significant challenges with the software, particularly during the implementation phase. Many report that the initial configuration can be highly complex, requiring specialized expertise and substantial time investment. Implementation costs are often described as astronomical, with businesses sometimes struggling to justify the expense, especially if they don’t fully utilize the software’s extensive features. Some users also point to a steep learning curve.
6. Odoo
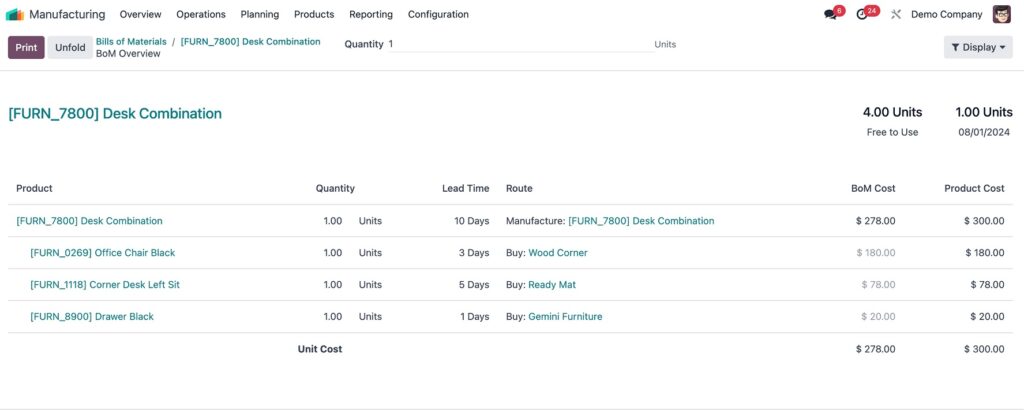
Odoo is a cloud-based ERP solution that offers a highly modular approach, making it a versatile choice for manufacturers with extended requirements for flexibility in business management. With an open-source architecture that allows for extensive customization and a wide range of modules covering inventory, production, POS, CRM, e-commerce, etc., Odoo enables businesses to tailor the system to diverse operational requirements.
Odoo’s standout feature enables businesses to implement only the necessary modules, reducing unnecessary complexity and costs. With over 30 official apps and thousands of third-party modules, it covers everything from production planning and inventory management to advanced sales, accounting, and marketing tools. For example, manufacturers looking to expand into retail or e-commerce can utilize Odoo’s POS and e-commerce integrations.
While Odoo provides essential manufacturing features like basic production planning, inventory tracking, and BOM management, its depth in manufacturing functionalities is relatively limited compared to more dedicated MRP systems. For instance, features like dynamic production scheduling, detailed routing, and a shop floor management system are less developed or lacking, which may hinder businesses with complex manufacturing setups. For simpler workflows or businesses focusing on integration with sales and distribution, however, Odoo remains a viable option.
Allowing businesses to pay only for the apps they use, Odoo’s modularity is a cost-effective approach. However, the affordability can be offset by high implementation costs, as configuring and setting it up to suit a business’s unique productivity mix often requires third-party support or consulting services. This, combined with the extra effort of acquainting yourself with Odoo’s ecosystem, can make implementation time-consuming and costly for SMEs with limited resources.
What customers say
Customers praise Odoo for its flexibility, affordability, and breadth of features, particularly its integration capabilities for e-commerce, POS, and shipping. The platform’s modularity is often highlighted as a major strength, allowing businesses to scale and adapt as needed. However, users frequently note challenges during the initial setup phase, citing a steep learning curve and the need for extensive customizations. Some users also report certain modules to have overcomplicated workflows and a lack of sophistication in some manufacturing functionalities.
7. Rootstock
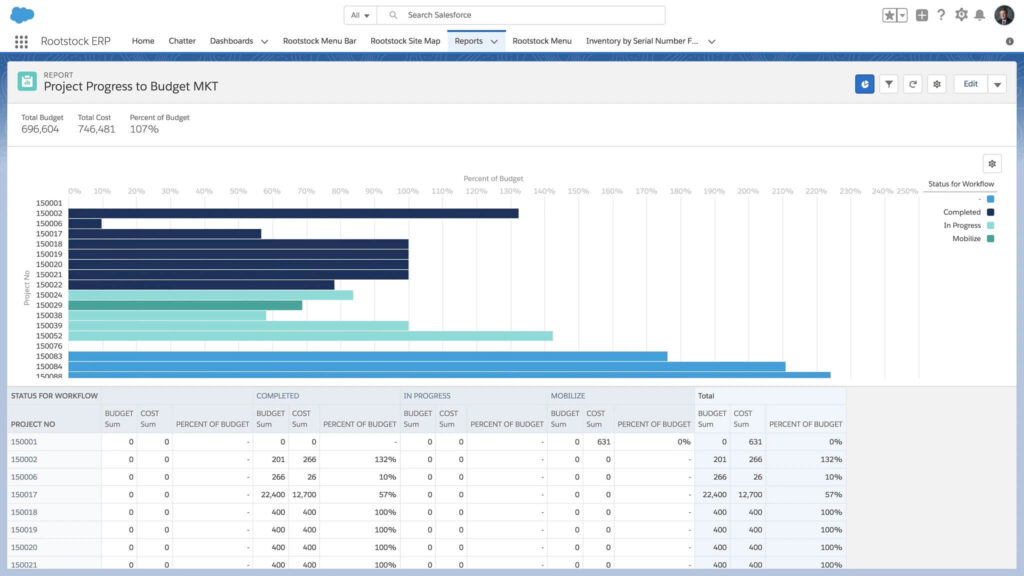
Rootstock is a cloud-based MRP solution designed for manufacturers, distributors, and supply chain businesses. Built on the Salesforce platform, its deep integration with Salesforce’s CRM and operational processes makes it a good choice for manufacturers requiring a more customer-focused approach.
Rootstock’s key strength lies in its ability to handle complex manufacturing and supply chain operations. It offers effective tools for production planning, inventory management, BOM management, and advanced project tracking. The Salesforce integration means businesses can unify customer interactions with production processes, providing good visibility of order statuses and project timelines. Demand forecasting, capacity planning, and real-time inventory tracking are also featured.
Rootstock’s project management tools also excel at handling custom manufacturing workflows. Businesses can manage customer-specific designs, track engineering changes, and link production schedules directly to sales orders. This makes Rootstock a viable option for businesses with customer-driven workflows requiring high customization levels and precision.
Rootstock’s pricing reflects its enterprise-level functionality and Salesforce integration, often making it a higher-cost option compared to standalone MRP systems. What’s more, the implementation process can be complex, requiring significant time and resources to configure the system to align with specific business needs. Additionally, businesses unfamiliar with Salesforce face a steeper learning curve, adding to the time and cost of adoption.
What customers say
Customers frequently praise Rootstock for its flexibility, scalability, and customization. The system’s native Salesforce integration and ability to handle complex manufacturing processes also garner praise. On the downside, some users note challenges with implementation and keeping customizations up to date. Other negatives mentioned include sluggish performance at times, limited estimating functionality, and difficult-to-navigate finances.
Tips on choosing the right MRP solution
Selecting the right MRP software is a crucial step for small manufacturers and distributors. The right choice will streamline operations, boost profitability, and have you up and running comparatively fast. The wrong choice could cost valuable time and money without offering measurable gains.
Look for a system that offers robust core functionalities like production planning, inventory management, and work order tracking in an easy-to-use interface. Scalability is equally important – your software should be able to grow with your business without requiring complete overhauls. A cloud-based solution generally ensures better accessibility and real-time updates while reducing running costs. Analyze your requirements and the software’s price point, and test the software thoroughly before committing fully to implementation.
Beyond features, the system’s ease of implementation, stability, and support responsiveness should also be considered. Well-designed software should provide ways of integrating easily with your preferred accounting, e-commerce, and shipping platforms to enhance its functionality and save time on manual tasks. Finally, transparent pricing and the absence of hidden fees are vital factors that help get the maximum value for your investment without unwelcome surprises.
You might also like: Top 10 Mistakes Small Manufacturers Make with ERP Software